Automotive engine manufacturers who are looking to reduce emissions and maximize efficiency, have been utilizing innovative methods and materials to decrease engine weight.
One technique for reducing weight is to replace the heavy cast-iron cylinder liners, which are used in aluminum cylinder blocks, with lighter-weight materials that are thermally efficient and wear resistant.
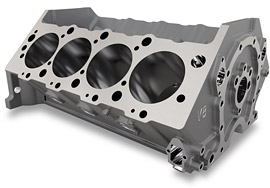
Image Credit: Zygo Corporation
Thermal Barrier Coatings
A number of manufacturers are turning to Thermal Barrier Coatings (TBC) instead of utilizing heavy cylinder liners. These are a ceramic or composite material applied as a spray to the carefully-prepared walls of the cylinder bores of an aluminum block, and then honed to a final finish with exacting specifications.
Precise measurements of a number of surfaces are needed throughout the prep and coating processes - this is in order to ensure that the TBC performs as designed. First, the cylinder walls undergo a mechanical activation process that prepares the surface so that the TBC will properly adhere and allow the sprayed coating to be finished correctly.
A splatter morphology occurs during coating, resulting in possible inconsistencies in the coating, which must be characterized reliably both before and after final finishing. Lastly, the post-spray honing step brings the coating to a very smooth finish and creates a specific cross-hatch pattern, which together with the texture of the spray coating, ensures proper lubricity.
Metrology Requirements
A versatile metrology system is required for measuring the cylinder walls at each step of the process. It should be able to measure surfaces ranging from extremely smooth to very rough, including the grooves scored into the surface during the mechanical activation process.
ZYGO's 3D optical surface profilers are perfect for this task, as they can measure a wide range of surface textures and reflectivities quickly and precisely. While several manufacturers sell optical profilers, only ZYGO optical profilers have a unique and differentiating version of coherence scanning interferometry (CSI) technology.
ZYGO CSI can deliver sub-nanometer precision at all magnifications, and measures a wider scope of surfaces more precisely and faster than other commercially-available technologies. ZYGO optical profilers are field-proven and robust, consistently supplying repeatable and reliable measurements in a production environment.
Metrology at Each Step of the Thermal Barrier Coating Process
Mechanical Activation
The cylinder walls are scored for the mechanical activation step of the process, as this dictates the amount of TBC that will be applied, the depth and spacing of the scoring must be strictly controlled.
The TBC may flake off if the scored depth is too shallow, if it is too deep, the honing process could remove the peaks of the TBC, making it less effective. ZYGO's 3D optical profilers with CSI technology can measure structures higher than 250 µm quickly and repeatably.
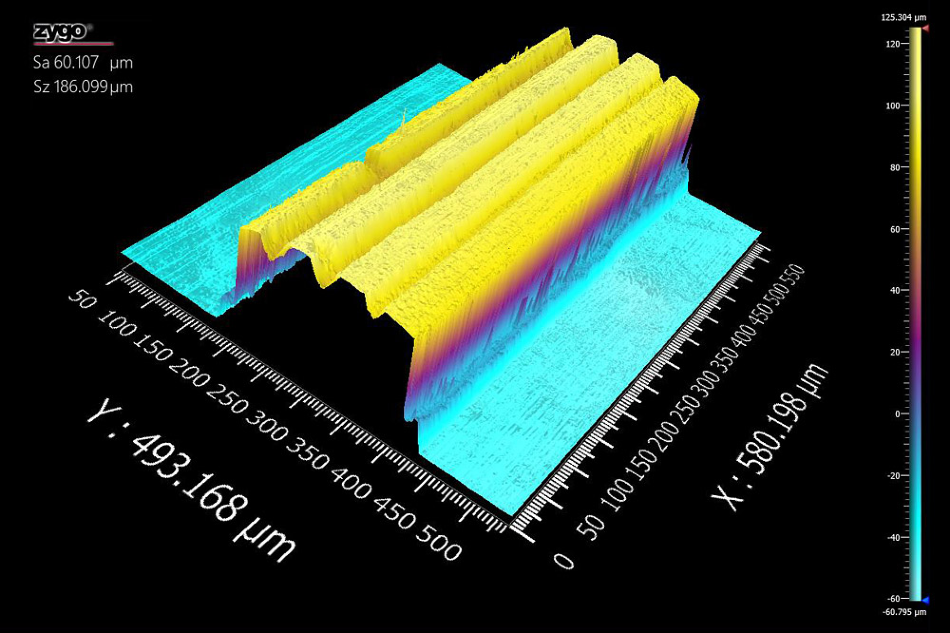
Image Credit: Zygo Corporation
Thermal Spray Application
Manufacturers must assess how the pores have developed after TBC application. The variety of pore sizes, ranging from to 50 µm2 to over 1 mm2, will help to establish the lubricity retention of the sprayed surface.
ZYGO optical profilers can measure these pre-hone coatings, even though they usually have low reflectivity and are very rough, thanks to ZYGO CSI technology and advanced data processing algorithms.
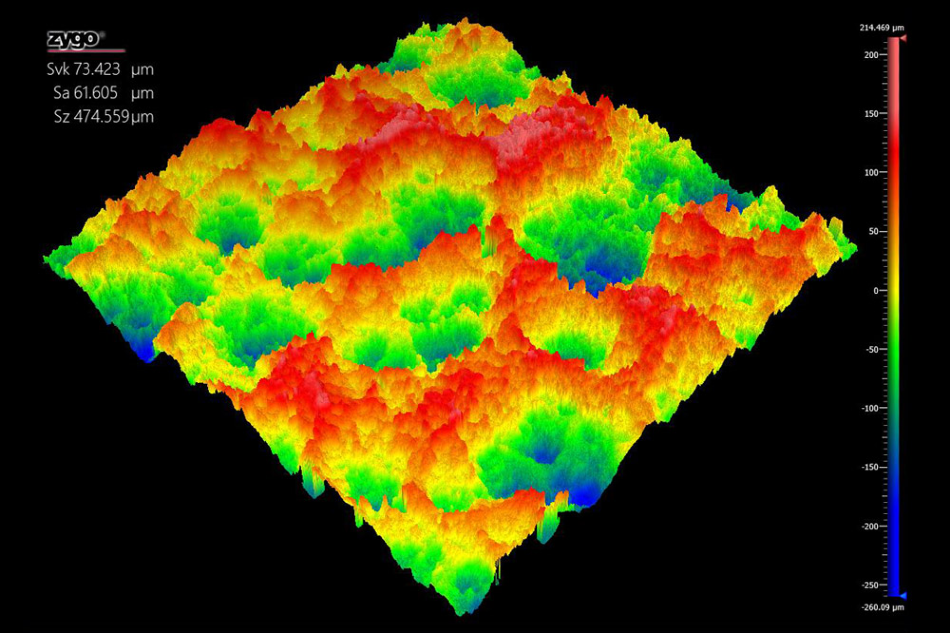
Image Credit: Zygo Corporation
Post Spray Finishing
The post-spray finishing step brings the coating to a very smooth finish and provides a cross-hatch pattern, which helps to give the surface proper lubricity retention characteristics.
It is vital to assess the finished surface texture of the cylinder at this step, checking the proper crosshatch depth and pattern, in addition to the final porosity (pore density, pore volume by area, and change of pore size by cylinder depth).
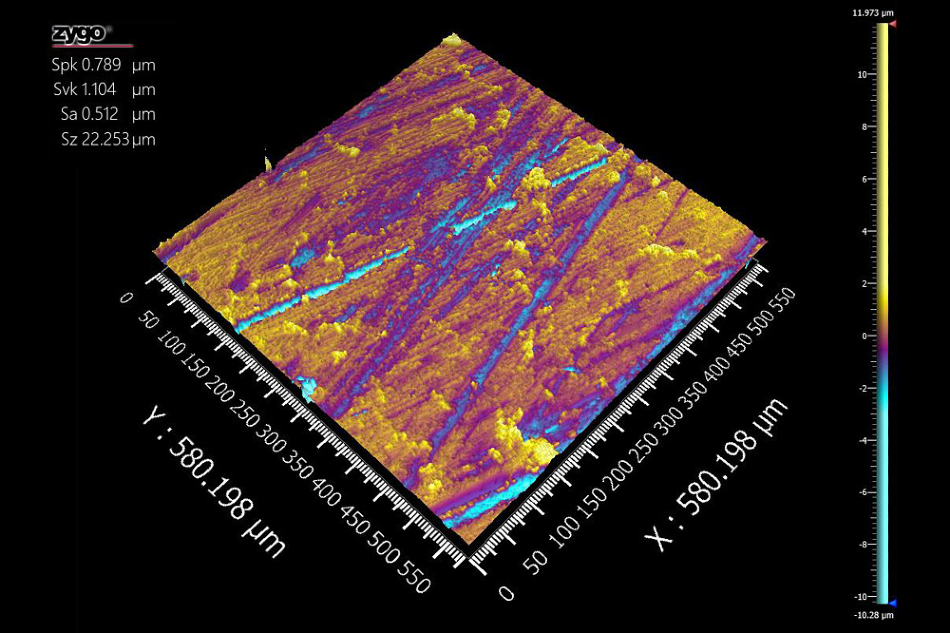
This information has been sourced, reviewed and adapted from materials provided by Zygo Corporation.
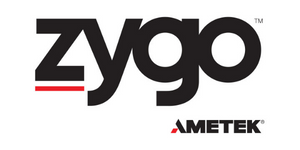
For more information on this source, please visit Zygo Corporation.