The birth of steel goes back 4000 years when bronze weapons were discarded in favor of iron ones due to their advantages in terms of strength. Steel was subsequently used for tens of centuries without people fully understanding its advantages over other materials.
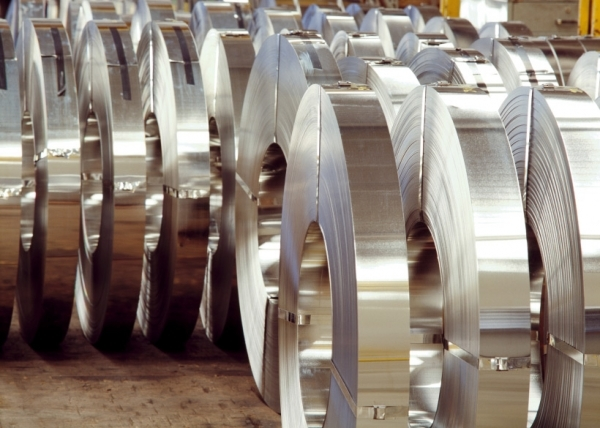
Image Credit: Ulbrich Stainless Steels & Special Metals.
The increasingly commercialized production of steel in the late 19th and early 20th centuries also led to innovation. Henry Bessemer’s 1856 discoveries resulted in a technique whereby the introduction of oxygen into molten iron reduced the carbon content of steel.
The US Steel Corporation was founded in 1901 as many of these innovations and discoveries occurred.
In 1904, French scientist Leon Gillet’s experiments led to a combination of alloys that resulted in stainless steel. Harry Brearley recorded this process in 1913 and patented the first martensitic after noting the corrosion resistance of the alloys.
Initially labeled ‘rustless steel,’ the polished surface and incredible strength properties of stainless steel saw it become an increasingly important tool in transportation and medicine.
Stainless steel can be put to any number of uses in the home, and it has many applications and specific uses in markets as diverse as aerospace and medical. But what is stainless steel?
Stainless steel = iron + chromium (>10.5%) + other materials
This is the very basic equation of a stainless steel alloy, but different grades of stainless steel will be comprised of various different elements. These grades and the elements therein mean they can be used in a wider range of markets due to their varied properties and capabilities.
Currently, over 250 different stainless steel alloys can be produced, but the majority of production is from a group of just 10.
Why is Stainless Steel So Popular in Manufacturing?
Stainless steel has a number of competitive advantages in comparison to other materials. It has higher oxidation and heat resistance than other metals and also possesses higher strength at room and high temperatures than alternative options. It is also more resistant to corrosion.
The low maintenance nature and attractive appearance of stainless steel along with its unique properties make it a strong choice for use in any number of functions.
Chromium is the main reason why stainless steel is resistant to corrosion. Iron is the base metal in most stainless steels and will oxidize (rust) over time when in contact with oxygen.
The chromium oxide layer added to iron is what differentiates it from other types of steel. Corrosion resistance is increased and rust is minimized due to the creation of a thin layer of oxidized chromium.
A higher percentage of chromium leads to increased resistance to corrosion.
Different alloying options and the varied metallurgy of individual alloys provide various groupings of stainless steel types which are further broken down into different grades.
The 5 main groupings of stainless steel are:
- Precipitation hardening (PH Grades) stainless steel
- Austenitic (300 Series) stainless steel
- Duplex
- Martensitic (400 series) stainless steel
- Ferritic (400 series) stainless steel
The chemistry of each grade can be altered by the addition of different elements. The factors of that grade will also change, which in turn affects the potential uses of the material. Formability versus weldability is a good example of this.
Which Stainless Steel Grade is Best for Formability?
Greater formability is found in an alloy that has a grade with increased levels of manganese, copper and nickel. 305 stainless steel wire is a prime example of this. It can be used in various applications including:
- Manufacturing of medical parts
- Deep drawn parts
- Surgical parts
- Bellows
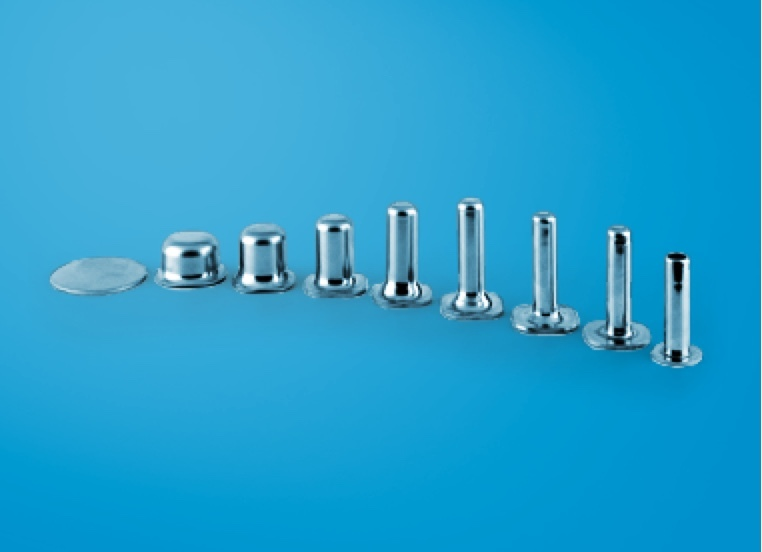
Image Credit: Ulbrich Stainless Steels & Special Metals.
Which Steel Grade is Best for Weldability?
Increased titanium or niobium content leads to alloys with greater degrees of weldability. An example is 316L stainless steel, which can be used in applications including:
- Marine applications
- Textile industry parts
- Chemical screens
- Oil refineries
- Flexible metal hose
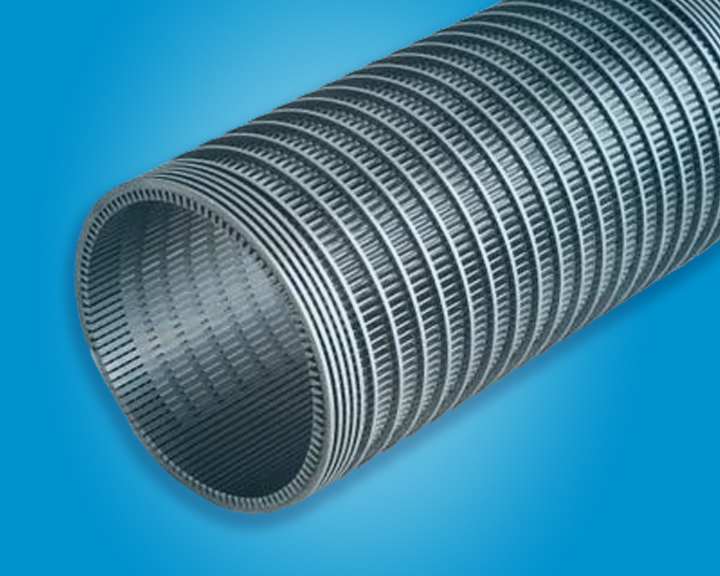
Image Credit: Ulbrich Stainless Steels & Special Metals.
Which Stainless Steel Grade Provides Increased Strength?
Increased strength is a factor manufacturers often desire during part making. This can be achieved by the addition of nitrogen, carbon, and/or vanadium to the alloy. Compared to other options, 440 stainless steel has a higher carbon content making it one of the stronger alloys available. Typical applications include:
- Surgical instruments
- Cutlery
- Firearms
- Scissors
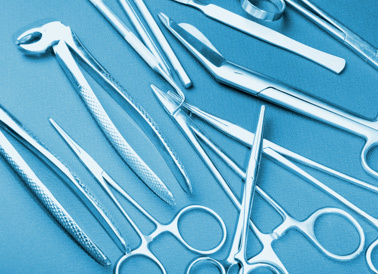
Image Credit: Ulbrich Stainless Steels & Special Metals.
Which Steel Alloy has Greater Oxidation Resistance?
Part manufacturers may seek oxidation resistance in an alloy. This is achieved by increasing the silicon and/or aluminum content.
The higher silicon content of 321 stainless steel and its heightened resistance to oxidation leads to its use in the manufacture of the following:
- Exhaust stacks and manifolds
- Tubing
- Jet engine parts
- Aircraft collector rings
- Fasteners
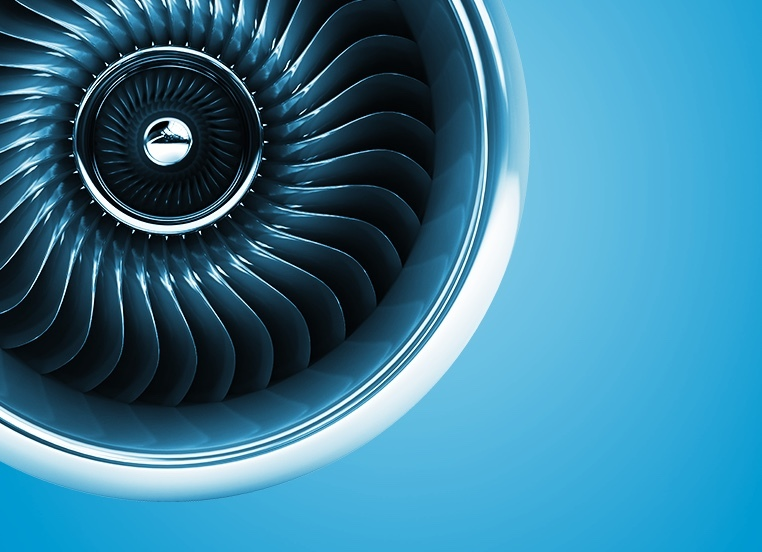
Image Credit: Ulbrich Stainless Steels & Special Metals.
What are the Benefits of Cold Rolled Stainless Steel?
Cold rolling stainless steel means thicknesses as small as 0.00039 inches can be attained, which has been a benefit to the medical and transportation industries.
Precision characteristics in cold rolling mean the strength and physical properties of an alloy can be increased. The flexibility and characteristics of stainless steel mean it will remain a valuable tool in maintaining advances in technology.
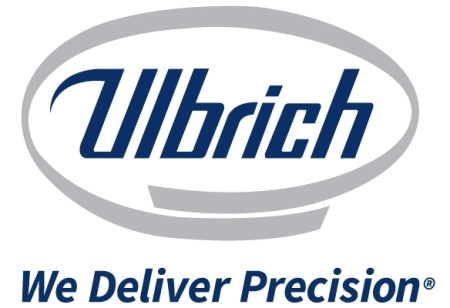
This information has been sourced, reviewed and adapted from materials provided by Ulbrich Stainless Steels & Special Metals, Inc.
For more information on this source, please visit Ulbrich Stainless Steels & Special Metals, Inc.