Designers and manufacturers of stainless steel and nickel alloy products are often required to make compromises between the properties needed for manufacturing and those needed for the product’s end use.
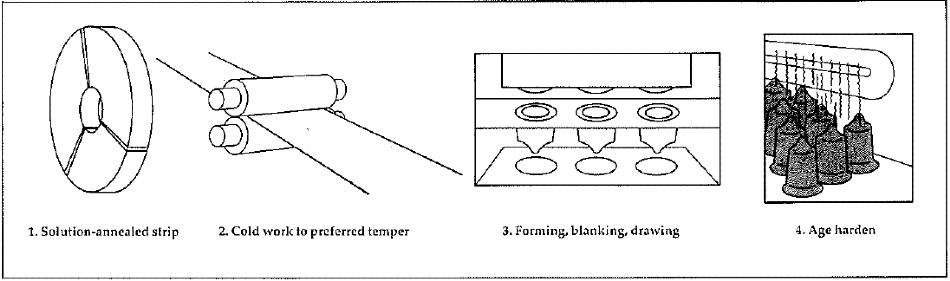
Image Credit: Ulbrich Stainless Steels & Special Metals.
When these compromises start to negatively impact on performance or cost, precipitation-hardening (PH) alloys can provide a helpful solution.
Many strip and wire components must be extensively drawn or formed during the manufacturing process, as well as being required to exhibit high strength and toughness when in service.
PH alloys are similar to other stainless steel and nickel-based alloys, with one main difference: They contain small additions of copper, phosphorus, aluminum or titanium.
When a part that is made of a PH alloy has been formed, it is then given an age-hardening treatment. During this treatment, these extra elements precipitate as hard intermetallic compounds, increasing strength and hardness.
Four main operations are required to create precipitation-hardenable parts.
The process starts with solution annealed strip (1), which is cold worked to the required temper (2). Next, the part is formed, blanked, and drawn (3). The last step (4) is the age hardening of formed parts that have the desired hardness and strength.
Despite their more complicated metallurgy, PH alloys are not necessarily more expensive than non-age-hardenable alloys. Performance may even be significantly higher than these alloys, without any negative cost implications.
Corrosion resistance is decreased (or possibly increased) during the aging cycle, but this is only by a small amount.
This article looks at PH stainless steel and nickel alloys in more detail, providing numerous application examples.
The Difference Between Annealed and Tempered Precipitation-Hardening Stainless Steels
PH stainless steels come in two main conditions – annealed (condition A) or tempered (condition C). The annealed alloys possess Rockwell hardnesses in the approximate range of B75 to C20. These are relatively soft and formable and, after forming, it is possible to age-harden parts to Rockwell C35 to C49.
Tempered alloys are passed through a rolling mill to add an element of cold work, usually 60%. The alloys can then be heat treated to extremely high hardness levels with Rockwell 50C not being uncommon. Additionally, yield strengths are usually in the 1200 to 1790 MPa (175 to 260 ksi) range.
Condition C is the starting point for high strength parts, but forming must be simple and minimal, with substantial radii.
Most users require more options however. Condition A could well be too soft as a starting point to heat treat the part to the desired strength; while condition C may be too hard for forming. In these cases, a precision reroll mill may be able to help.
Tailoring PH Alloys to the Task
Rerollers are specialist producers who maintain stocks of cold- and hot-rolled stainless steel and nickel alloy strip in huge quantities. They are able to custom roll it to a required gauge and temper, heat treating the material between passes to neutralize the effects of work hardening.
In controlling the amount of cold working applied, rerollers are able to achieve an intermediate temper that fits between conditions A and C, depending on the requirements of the customer.
Rerollers begin by rolling a specific area reduction into the material, aiming to achieve a temper that may be the maximum for forming. This is because if it were any harder, it would be challenging to form or fabricate.
They then age-harden a section of the wire or strip according to a cycle advised by standard specifications and measurements. Rerollers are able to ascertain the best cold-worked temper for forming and calculate the yield or tensile strength that will be created in the aging cycle.
The heat treatment can be as straightforward as 90 minutes at 565 °C (1050 °F), as can be seen in the example of Armco’s PH 15-7Mo stainless steel. With different alloys, treatment can entail several stages of heating, holding and cooling, with cycles that could even be 16 to 20 hours in duration.
The choice of aging cycle is largely based on whether the alloy is austenitic, semi-austenitic or martensitic. The part’s end use and the form of heat treatment available dictates which of these alloys would be the most appropriate.
Austenitic PH Alloys
The austenitic stainless steel grades of PH alloys are employed in applications that require moderate corrosion resistance, good fabricability and high strength. The most common of these is Allegheny Ludlum Corp’s Alloy A286.
Alloy A286 is an iron-nickel-chromium alloy with age-hardening elements of phosphorus and aluminum. This alloy has exceptional strength and good corrosion resistance at temperatures up to 700 °C (1300 °F).
Austenitic stainless steel grades necessitate high aging temperatures of around 700 °C (1300 °F). This high heat treatment decreases their corrosion resistance somewhat, but their oxidation resistance continues to be very good.
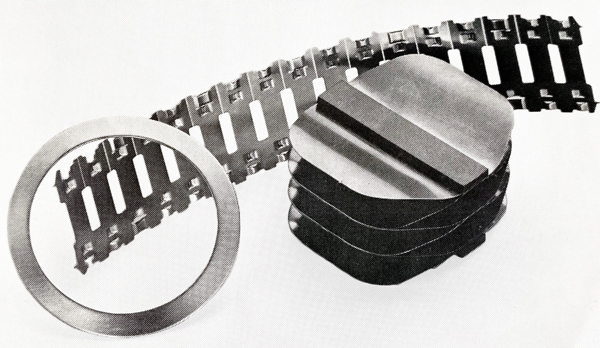
Image Credit: Ulbrich Stainless Steels & Special Metals.
Martensitic PH Alloys
The solenoid and large washer shown in the image above are both made from Armco’s 17-7 PH martensitic stainless steel. This grade is a good example of very high chromium-content PH alloys, which have superb oxidation resistance.
It can be heat treated at comparatively low temperatures, while demonstrating high strength and other useful mechanical properties when working in elevated-temperature service.
Martensitic grades display dimensional stability during age hardening (contracting around 0.0005in./in.), meaning they are highly suited for formed parts that need to meet strict tolerance specifications.
The 17-7 PH washer is used in oil field and aircraft applications. It has a 63.5 mm (2.5 in.) outside diameter and, while this is a simple shape, it does pose some difficulty in forming due to its large open middle section. In application, it needs both spring properties and the ability to hold a perfectly round shape.
After forming, a precipitation-hardening treatment increases its strength to 1380 MPa (200 ksi).
The solenoid spring is a welded assembly with a brownish color that is a result of being heat treated for several hours in an open air furnace, at temperatures of up to 900 °C (1650 °F). This heat treatment gives the solenoid particular spring properties without compromising the very small welds which connect the network of spring leaves.
Semi-Austenitic PH Alloys
Semi-austenitic PH alloys are metallurgically more complex than the other stainless steels described within this article. They are austenitic while in the annealed condition and must be converted into martensite so that they can age harden.
A normal cycle may consist of heating to high temperatures such as 995 °C (1750 °F); cooling to -75 °C (-100 °F) to cause the transformation to martensite; holding for between three and eight hours, then precipitation-hardening between 450 and 565 °C (840 and 1050 °F) for 60 to 90 minutes before air cooling.
The greatest availability of strip and sheet products is found in grades AM-350 (Allegheny Ludlum) and PH 15-7Mo (Armco). Grade AM-350 is somewhat similar to both 15-7 PH and 17-7 PH, but it possesses a slightly improved high-temperature capability. 15-7 PH is very similar to the martensitic 17-7 PH alloy, but it has a low molybdenum content which provides higher strength levels in the age hardening process.
Nickel Alloys
Among the range of nickel-chromium alloys, Inco’s Monel K-500 is the alloy of choice for various high-strength parts deployed in demanding environments. This alloy can be age-hardened to yield strengths up to 1030 MPa (150 ksi) and 20% elongation, with ductility improving as strength levels reduce.
Inco’s Monel K-500 maintains ductility and strength over a broad range of temperatures, from -250 to 650 °C (-425 to 1200 °F).
In the same image above, the long blanked strip is made from Inco’s Inconel 718. It functions consistently over the same temperature range as Monel K-500. Inconel 718 can also be welded in the fully aged condition, and it possesses good oxidation resistance up to 970 °C (1780 °F). Yield strengths with this alloy are up to 1170 MPa (170 ksi), while elongation is 17%.
In application, this part must continue to be very rigid in a high-temperature atmosphere, while retaining enough ductility to adjust to the subtle movement of adjoining parts. When the part has been blanked, 18 hours of precipitation-hardening then brings its strength up to 1380 MPa (200 ksi).
When to Ask for the Help of an Experienced Metallurgist or Development Partner
With all the compositions discussed above, specific heat treatments are best selected using standard industry specifications such as ASTM or AMS, or by using manufacturers’ data.
When heat treating plays a substantial role in engineering the part, it may be worth engaging the services of an outside heat treater, experienced with corrosion-resistant alloys or aircraft.
Designers may be hesitant about exploring specific topics around metallurgy, but using precipitation-hardening alloys is not as complex as other alternatives. Producers and distributors of these alloys are generally more than happy to assist in the process of selecting an appropriate alloy for any application.
Acknowledgments
Produced from materials originally authored by Ron Brucker from Ulbrich.
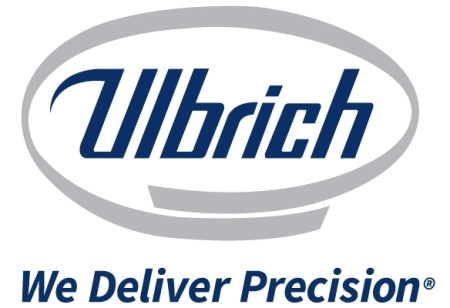
This information has been sourced, reviewed and adapted from materials provided by Ulbrich Stainless Steels & Special Metals, Inc.
For more information on this source, please visit Ulbrich Stainless Steels & Special Metals, Inc.