Stainless steel, including austenitic stainless steel, is strong, durable, and resistant to corrosion, making it a popular choice for a wide range of applications.
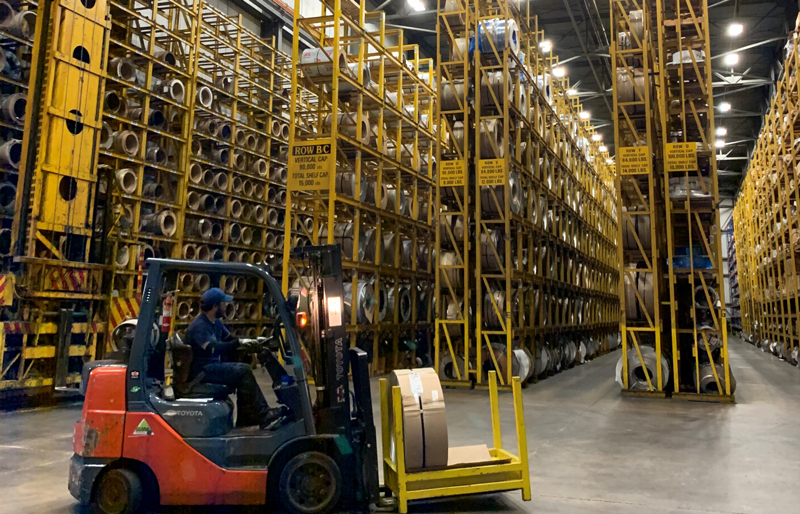
Image Credit: Ulbrich Stainless Steels & Special Metals.
It is environmentally friendly, aesthetically pleasing, and easy to produce, maintain, and clean. This combination of factors makes stainless steel the first choice for components in the architecture, automobiles, and many other areas.
Stainless steel is a broad term that refers to iron-based alloys containing chromium. In fact, there are over 100 grades of steel and numerous types of stainless steel.
Commonly, the percentage of chromium, molybdenum, nickel, and other alloying elements is the key factor in differentiating between types of stainless steel. Each grade has its own advantages and disadvantages which dictate its use.
Grades of stainless steel are grouped within five main categories: austenitic, precipitation-hardened (PH), ferritic, martensitic and duplex. This article focuses on austenitic stainless steel and looks at how it compares to some of the other grades.
Austenitic Stainless Steel
The term austenite refers to face-centered cubic (FCC) iron or steel alloys that share this type of structure. It was named after the Englishman Sir William Chandler Roberts-Austen, who was well known for his exploration into the physical properties of metals.
Austenitic stainless steel is the most commonly used type of stainless steel, due in no small part to its excellent resistance to corrosion and heat. It is used in a wide range of industries including the aerospace, automotive, medical and industrial sectors.
While it is known for its unparalleled strength and formability, austenitic stainless steel cannot be hardened by heat treatment.
Medical Applications
Medical uses of austenitic stainless steel are varied but commonly include hypodermic needles, surgical anvils, needle caps or guards, or drawn staple gun components.
Automotive Applications
Automotive manufacturing applications of austenitic stainless steel include orifices, fuel rails, and deep drawn automotive parts. Austenitic grades are popular in automotive applications due to their versatility and formability.
Industrial and Consumer Applications
Industrial and consumer applications tend to focus on cold-worked austenitic stainless steel strip material. These often include power generation parts, razor blade components, cutters, and springs.
Aerospace Applications
There are a number of aerospace applications for austenitic stainless steel strip that require precision cold processing; these commonly include helicopter and military applications, landing gears, and jet engine components.
While all steels contain an amount of carbon, they are generally differentiated by whether they are low or high carbon. The key difference between ‘carbon steel’ and stainless steel is in the amount of alloy content: stainless steels have at least 10.5% chromium content, while carbon steels must contain less than that amount to receive the carbon steel classification.
Levels of carbon vary within the stainless steel families, as well as within austenitic stainless steel variants. Straight grades of stainless steel strip and foil or stainless steel wire — or at least what would be deemed to be high carbon in this category - must contain a maximum of 0.08% carbon, while low carbon grades must contain a minimum of 0.03% carbon.
Lower carbon stainless steel grades possess substantially improved welding capabilities, a characteristic often referred to as ‘weldability’. If manufacturing requirements involve welding the metal, then 304L stainless steel would be a more appropriate choice than its 304 stainless steel counterpart.
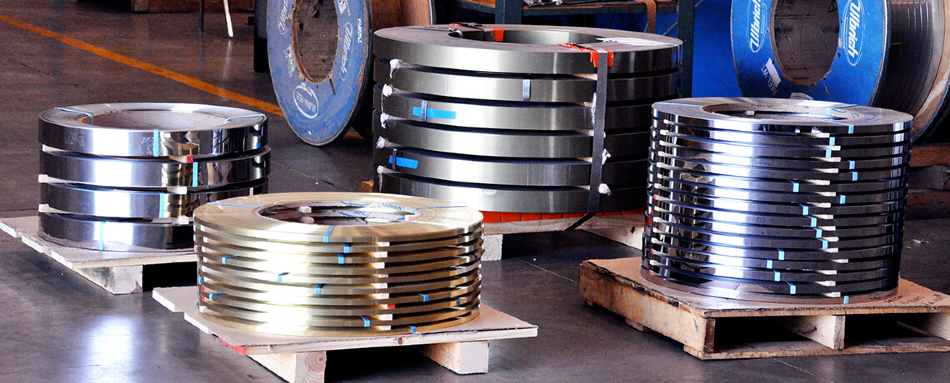
Image Credit: Ulbrich Stainless Steels & Special Metals.
What Makes a Stainless Steel Austenitic?
Steel becomes ‘austenite’ by nature when nickel or nitrogen is added to it. It is the chemical composition that dictates the exact grade of stainless steel, while the austenite crystalline structure in the material itself is a central characteristic.
In the annealed condition it is important to note that Austenitic stainless steel is usually characterized as non-magnetic, however cold rolling austenitic steel, or reducing its thickness and increasing its hardness, introduces a certain amount of magnetism to the material
Austenitic stainless steel is highly regarded for its formability, making it well suited for fabrication. Its resistance to corrosion also makes it a popular choice where this is a consideration within an application.
Chemical Composition
Austenitic stainless steel comprises a minimum of 10.5% chromium and 8 to 12% nickel, as well as nitrogen and a range of other elements in solution. It is chromium that gives the steel its considerable corrosion resistance, while nitrogen acts as a stiffening agent.
Austenite Crystalline Structure
Stainless steel that presents an austenite crystalline structure, as well as the face-centered-cubic lattice structure, remains present throughout both hot and cold temperatures. Magnesium, nickel, and nitrogen are the stabilizing elements of the austenite structure.
What are the Characteristics of an Austenitic Stainless Steel?
Austenitic stainless steel has a number of beneficial attributes which make it a material that is highly in demand. This category of stainless steel makes up around three-quarters of the global stainless steel market; a market which was valued at $93.69 billion in 2018 and is projected to show a CAGR of 5.2% by the year 2025.
These attributes include:
Strength at Temperature
Austenitic stainless steel can endure extreme temperatures. Depending upon the grade, these can be up to around 1900 °F. Some grades, however, do start to exhibit softening, deforming or loss of strength at 800 °F.
Cold Workability
As mentioned previously, austenitic stainless steels can’t be hardened using heat treatment and only cold working or reduction are able to enhance the strength of austenitic. Cold working in this context refers to shaping metal without heating it.
Additionally, austenitic stainless steels can be annealed before quickly cooling or ‘quenching’ the metal to return it to its initial state. Cold rolled stainless steel offers a range of benefits including, most notably, enhanced surface finish. This is a useful trait, as steel with an improved surface finish will possess higher hardness, making it stronger and more resistant to crack propagation.
Low Thermal Conductivity
Heat does not travel quickly through austenitic stainless steel. On the other hand, ferritic stainless steel possesses a higher thermal conductivity.
Formability
Austenitic stainless steel is extremely formable, meaning it is a versatile material that is suitable for an array of applications.
While cold working austenitic stainless steel increases its strength, it also decreases its ductility. Austenitic stainless steel possesses a higher susceptibility to stress corrosion cracking than ferritic.
Austenitic stainless steel is typically not magnetic, while ferritic stainless steel is generally magnetic. Where, for example, some refrigerators are magnetic while others are not, this is simply because they are made of differing types of stainless steel.
There are exceptions to the above, however, and specific processes or temperatures can cause the stainless steel’s crystal structure to rearrange, giving the material magnetic properties.
Applications for Austenitic Stainless Steel
With so many possible uses and applications for austenitic stainless steel, it is no surprise that it makes up such a large segment of the total global market share. These stainless steels are split into two series — the 200 series and the 300 series.
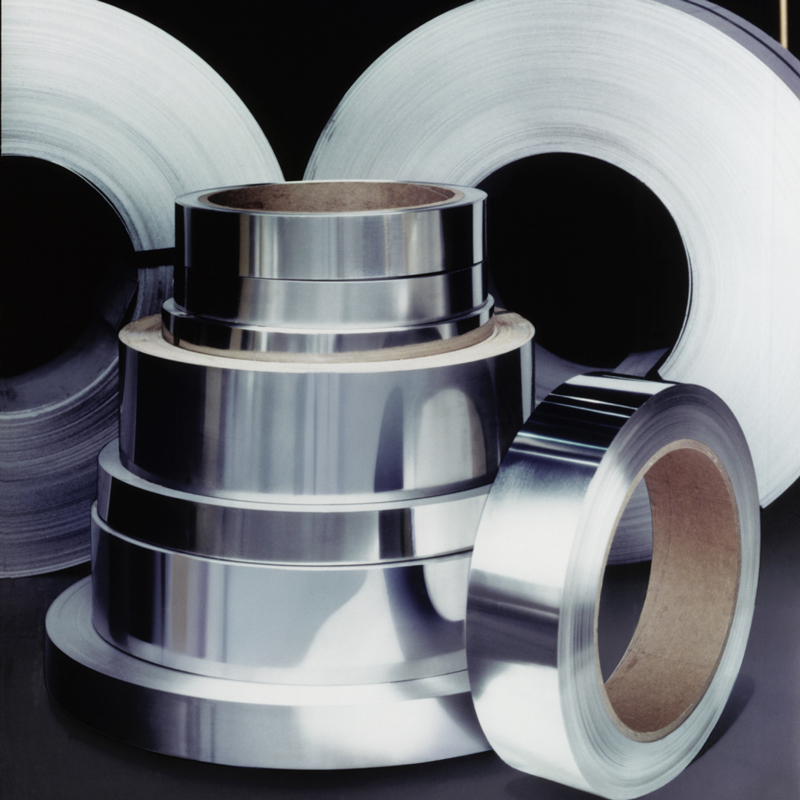
Image Credit: Ulbrich Stainless Steels & Special Metals.
The 300 series is nickel-based and incorporates the most commonly used, standard austenitic stainless steel - grade 304 stainless steel. This series usually contains 18% chromium and 8% nickel, which is the minimum percentage of nickel needed to transform ferritic stainless steel into austenitic when that amount of chromium is also present.
In contrast, the 200 series is low in nickel and high in nitrogen (or manganese) meaning that it offers a less expensive substitute to the 300 series. The following list outlines a number of applications for austenitic stainless steel, by series:
300 Series
- Mining and chemical equipment
- Pharmaceutical equipment
- Tanks
- Components for catalytic converters
- Food and beverage equipment
- Aerospace tubing
- Storage containers
- Sinks
- Compensators
- Afterburners
- Cutlery
- Furnaces
200 Series
- Cookware and cutlery
- Home water tanks
- Dishwashers
- Indoor architecture
- Automobile parts
- Washing machines
Ulbrich offers 33 austenitic stainless steel grades, with options available in strip and/or wire to accommodate a wide range of applications and purposes. This broad selection of alloys, coupled with an on-site engineering team means that Ulbrich is well placed to develop projects from trial through to production.
Ulbrich’s teams are able to determine the most ideal grade of austenitic for a project, and depending on the project’s specifications and manufacturing requirements, which form factor will be most appropriate.
The company has metallurgy and tooling teams that are industry experts in both strip and wire, offering unmatched, precision cold rolling. Efficient working relationships with melt mill partners make meeting unique and challenging requirements easier.
Customers commonly make trial orders for prototypes, allowing materials to be sampled, and this coupled with Ulbrich’s industry knowledge makes determining whether a project requires austenitic, ferritic, martensitic, duplex, or PH stainless steel - and at which grade – quick and straightforward.
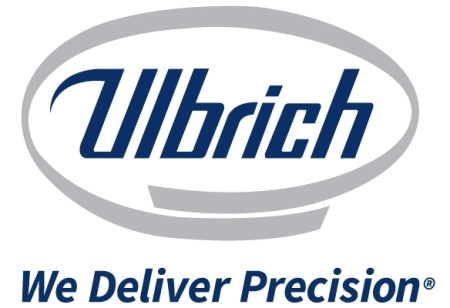
This information has been sourced, reviewed and adapted from materials provided by Ulbrich Stainless Steels & Special Metals, Inc.
For more information on this source, please visit Ulbrich Stainless Steels & Special Metals, Inc.