All decisions on the chemical, physical and mechanical properties of metal alloys are very much dependant on the role that the medical device will be taking on and the setting in which it will be operating.
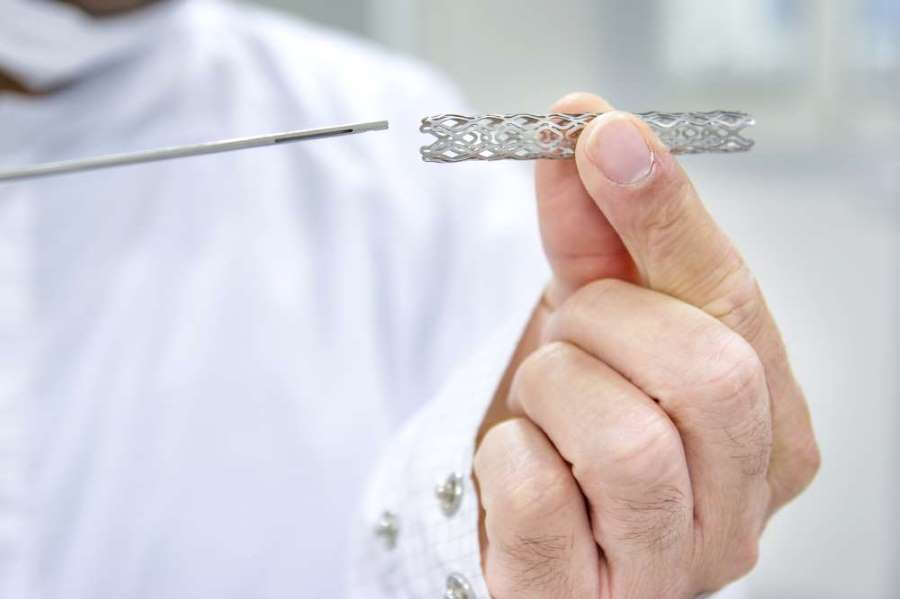
Image Credit: Ulbrich Stainless Steels & Special Metals.
What are the Properties to Consider When Deciding on a Certain Metal Alloy for a Medical Device?
The end-use application in question will dictate any and all decisions around choosing an appropriate alloy, as well as determining its size, shape and amount of material required.
Medical manufacturers and buyers may also consider other properties such as the alloy’s electrical properties, atomic properties, environmental properties or magnetic properties. They may also need to think about manufacturing properties such as castability or machinability, radiological properties, or the material’s thermal properties.
When identifying an alloy for a medical application, uniform and correct chemical properties must be agreed upon near the beginning of the metal selection process. Carefully choosing the correct chemical makeup of an alloy means that metal suppliers and precision re-rollers are able to obtain the accurate, good quality raw material.
Ulbrich’s engineers, experienced sales professionals, and product managers will generally work alongside one another to communicate the best approach to material selection.
At Ulbrich Specialty Wire Products in Westminster, South Carolina (where the majority of medical device customers obtain a precision flat and round wire), metallurgical and medical manufacturing experts will assist customers in selecting and procuring the correct material with the correct properties, based on their individual application requirements.
For medical braid wire applications, the most frequently required mechanical properties are high strength and dimensional control. Additionally, surface smoothness, dimensional control, and elongation are of considerable importance for Mandrel applications.
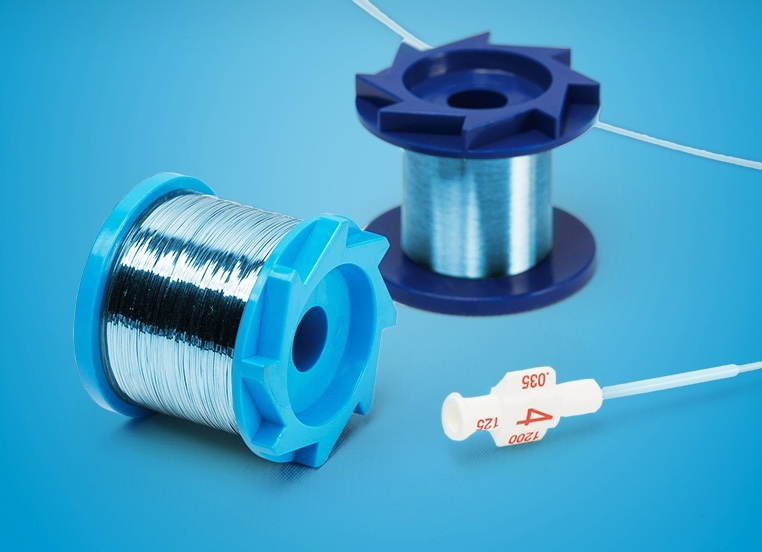
Image Credit: Ulbrich Stainless Steels & Special Metals.
The medical device industry makes heavy use of the specialty metal nitinol – a shape-memory alloy. This is large because of its oxide layers and mechanical properties. Biocompatibility, that is, the human body’s capacity to acclimate to contact with metal such as titanium, is also a key factor that medical manufacturers will generally consider.
One such example is that of titanium rods applied in oral surgeries. These bind to human flesh, meaning that these titanium rods are effectively and permanently set in place. Within this application, the rods’ biocompatibility is vitally important to avoid corrosion, rejection or infection.
Titanium is highly biocompatible, and for that reason it is commonly used in medical manufacturing like dental implants, allowing patients to heal quickly, often using their jaw and/or teeth as if nothing had happened within a relatively short period of time.
A large number of medical manufacturers utilize a spring temper round, flat or custom shaped wire for their particular application. Depending on the required or desirable characteristics based on the manufacturing process or end-use, it may be most appropriate to use annealed, full-hard, half-hard, or quarter-hard wire. All of these can be provided by wire manufacturers on request.
The harder the temper is, the more rigid the resulting structure will be. The torque response of the device, also known as ‘torquability’ may be important within certain applications.
For example, in the manufacture of catheters, the device’s maneuverability is of paramount importance, meaning that the torquability of the material used is a key requirement.
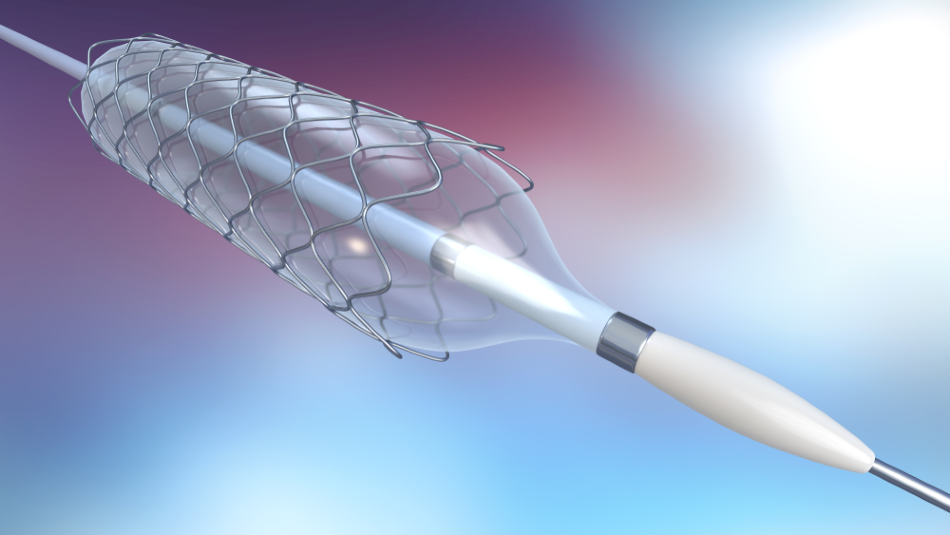
Image Credit: Ulbrich Stainless Steels & Special Metals.
As catheters are medical devices that may be introduced into the body to perform surgical procedures or treat diseases, their mechanical properties play a significant role in the selection of metal for their manufacture.
Medical device customers should also decide whether braid-enforced or coiled-enforced catheters are the best choices for their application.
Many customers are now choosing to use nitinol for coiled catheters in especially sensitive surgeries or other applications where accuracy is of utmost importance, such as cardiovascular or neural surgeries.
What are Some of the Different Methods for Ensuring Material Quality for Medical Wire and What do They Accomplish?
Considerable focus should be placed on the methods used for ensuring the quality of stainless steel and specialist metals for the medical wire. This should not only concern an organization’s quality assurance team, but it should also be the main priority of a medical rolling mill, and customers should expect this as standard.
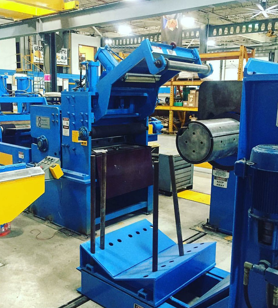
Image Credit: Ulbrich Stainless Steels & Special Metals.
As the metal moves through the mill, continuous dimensional data collection (SPC data) should be collected. This improves consistency in performance for both the device and the manufacturing process itself.
It is also worth bearing in mind that working alongside metal manufacturers who have metallurgists on staff offers an advantage, as these experts will have a specific understanding of how metal is shaped and sized at the mathematical, minuscule level.
Quality control such as this guarantees that defects are less likely, in turn ensuring that the device, application, or production process benefits from time and energy savings while reducing scrap, waste, and failure.
Most significantly, collecting dimensional data ensures that materials are all within the required specifications and that they meet all relevant manufacturing and regulatory requirements.
Another key factor in either improving (or reducing) the performance of materials within medical applications is that of surface cleanliness. Methods to ensure cleanliness must be stringent and continually improved, as this can effectively mean life or death for a patient. As a result, all precision strip, round wire, and flat wire should be as particulate-free as possible.
All staff at Ulbrich, from quality control coordinators to machine operators and helpers, inspect each work order with robust attention to detail. Communication and collaboration within the team are at the core of guaranteeing quality throughout the whole supply chain.
When picking a materials partner, it is important to be sure that they maintain the same level of quality control at all levels of the organization. Compliance with ISO certifications is a good baseline, but to meet the stringent material requirements of medical device customers, utmost care and special precautions must not just be standardized in the process, they must be engrained in the organization’s culture.
Personal Protective Equipment (PPE) is just one part of ensuring that material is free of contaminants. Custom guards, barriers, and other types of contaminant prevention should be fitted on machinery at all stages of production in order to protect metal in progress – and machine operators themselves - from being compromised.
This attention to detail is crucial in ensuring that the final material has been manufactured to a level of cleanliness and attention to performance/quality appropriate for a medical manufacturer.
Purchasing material from reputable vendors and qualified sources is vitally important. The material’s chemical makeup must be meticulously examined and inclusion rates should be as low as possible - non-existent in an ideal world.
Medical device customers should select an alloy and a supplier that provides materials with undeviating, consistent mechanical properties, ensuring that those properties are appropriate for processing medical wire.
Both production methods and manufacturing sources are equally important in supply chains within the high-tech medical device industry.
Finally, avoiding tangles during production is essential, so tedious spooling methods must be used. Because round wire can be as thin as 0.00075 ” for nitinol and other stainless alloys, tangling can cause enormous problems within medical device production.
In order to avoid this, Ulbrich carefully wraps wire on spools, always bearing the next operation in mind, and asking for ongoing feedback on the spooling so that this can be continually improved.
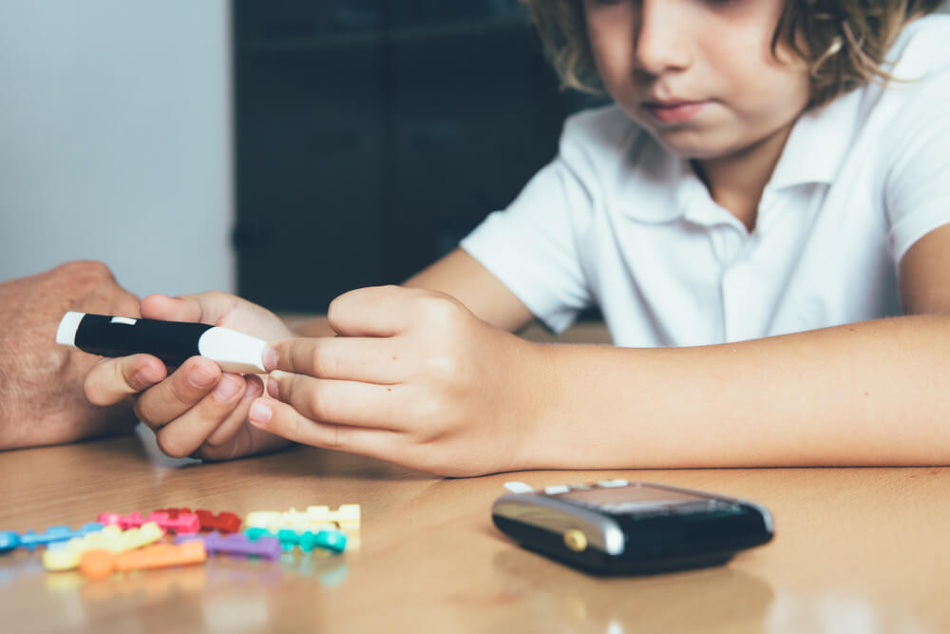
Image Credit: Ulbrich Stainless Steels & Special Metals.
What Environmental or Contextual Factors are Medical Devices Subjected to that Affect Material Selection?
The questions of whether the device can be implanted in the body, and if it is, how long it will be in the body for, are key considerations for medical devices and as such, biocompatibility and the material’s response to blood are important factors. Depending on the application, MRI compatibility may also be required.
How Important are the Corrosion Resistant Properties of Stainless Steel or Special Metal Wire for Medical Manufacturing?
The corrosion resistance properties of stainless steel or special metals are also important within medical applications. 304V stainless steel wire has been vacuum arc remelted, meaning that it has more consistent chemistry with minimal contaminants and voids.
304V is a robust, flexible material that can easily be welded or soldered, and 304V stainless steel wire is utilized within a wide range of medical applications because of its comparatively low cost next to other materials which may reach the minimum standards for corrosion resistance.
What are Some Common Materials We See Medical Manufacturers Turning to?
Bi-metals are becoming increasingly popular and more widely used. Various metals and special alloys like the developmental project-based alloy, MP35N, open up new, high-performance possibilities for surgeons.
Recently, other bi-metals such as nitinol with a platinum core (cladded) or a nitinol with a tantalum core have garnered more attention in the medical device marketplace.
For example, heavy metals like tantalum, platinum, and tungsten are highly visible under a fluoroscope during cardiovascular surgery, enabling surgeons to view more clearly where they are working within the human body.
Despite these advances, 304V stainless steel wire remains the most commonly used material in the majority of medical applications, because the alloy is a safe and productive material while meeting the minimum standards for corrosion resistance.
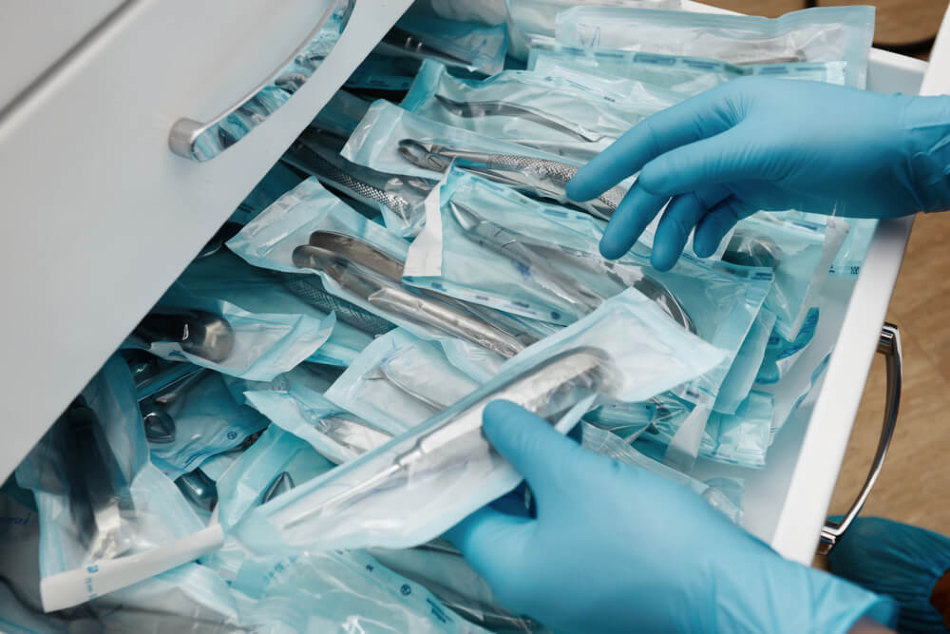
Image Credit: Ulbrich Stainless Steels & Special Metals.
What is Critical to the Production and Performance of Surgical Instruments?
Stainless steel alloys such as austenitic, martensitic, and precipitation hardening grades are commonly used within surgical instruments, as these are designed to perform very specific, critical tasks.
As such, alloys that are utilized to manufacture medical instruments must be produced to withstand the demands of daily use in healthcare environments, with considerable attention paid to quality and detail.
From cutting to stapling and pricking, the high demands of medical devices and surgical instruments necessitate the use of precision manufactured alloys that meet the precise specifications of the application in question.
Ulbrich is a driving force in medical instrument innovation through precision alloys.
Doctors and other workers in the medical field can restore and preserve the health of sick people, thanks to the aid of precision alloys and special metals. Ulbrich takes great pride in the fact that their work plays a part in the health of millions of people, regardless of the size of that impact.
As an organization, Ulbrich holds itself, its machinery, and its processes to the highest standards because precision alloys used within innovative surgical (and increasingly robotic) instruments have the ability to change lives.
Surgical Instruments Made with Precision Alloys are Simply Better
Differing incision tools and surgical instruments necessitate the use of a diverse array of alloys and alloy characteristics. Selecting the most appropriate materials and then having them manufactured to rigorous physical, chemical, and mechanical specifications guarantees that the resulting component or product delivers higher rates of consistency with less waste and lower rates of failure.
Ulbrich has a proven track record of providing alloys and bi-metals to the medical industry. Strategic sourcing methods, a vast inventory of alloys and considerable annealing and rolling capabilities allow Ulbrich a distinct competitive advantage that is passed on to customers.
Whether a medical device requires something non-magnetic and resistant to corrosion (like austenitic alloys) or for an alloy to be heat-treated to a higher hardness (like PH grade alloys), Ulbrich can accommodate these needs.
Surgical Instruments Manufactured with Precision Alloys Include:
- Surgical draws
- Sheers
- Cardiovascular clamps
- Scissors
- Strip square
- Stapler springs and staples
- Catheters
- Surgical robotic instruments
- Tissue grabbers
- Lances
- Needles
- Surgical grills and grinders
- Surgical staplers/anvils
Precision Alloys Employed in Surgical Instruments Include the Following, Among Others:
Stainless steel grades:
- 304 stainless steel
- 304V stainless steel
- 304LV stainless steel
- 304LVM stainless steel
- 316 stainless steel
- 316L stainless steel
Special Metals:
- Titanium
- Phosphor bronze
- Nitinol
- Aluminum
- MP35N
- Molybdenum
- Beryllium copper
- Copper
- Tungsten
- L605 and many other ‘bi-metals’ (combinations of cladded wire which may include silver or platinum).
Others specialty alloys include:
- 17-4PH® stainless steel UNS S17400
- 17-7PH® stainless steel UNS S17400
- 305 stainless steel UNS 30500
- 410 stainless steel UNS S41000
- 420 stainless steel UNS S42000
- 420 high carbon stainless steel UNS S42000
- 420 LC stainless steel strip UNS S42000
- 440A stainless steel UNS S44002
Ulbrich are continually exploring and searching for ways to innovate and improve upon existing medical devices.
Alongside state-of-the-art capabilities in annealing, rolling and slitting, Ulbrich is constantly assessing, researching, and analyzing the mechanical and chemical properties of alloys in order to maximize their performance potential.
Partnering with Ulbrich ensures the best in personnel, process, and product as well as a team that genuinely cares about making each project and medical device as effective and successful as possible.
Acknowledgments
Produced from materials originally authored by Weston Ulbrich from Ulbrich.
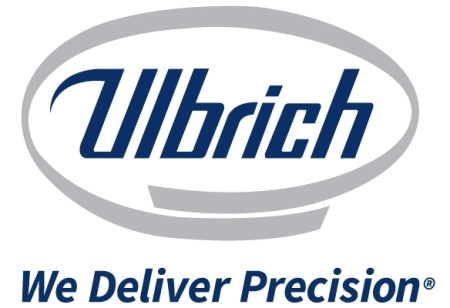
This information has been sourced, reviewed and adapted from materials provided by Ulbrich Stainless Steels & Special Metals, Inc.
For more information on this source, please visit Ulbrich Stainless Steels & Special Metals, Inc.