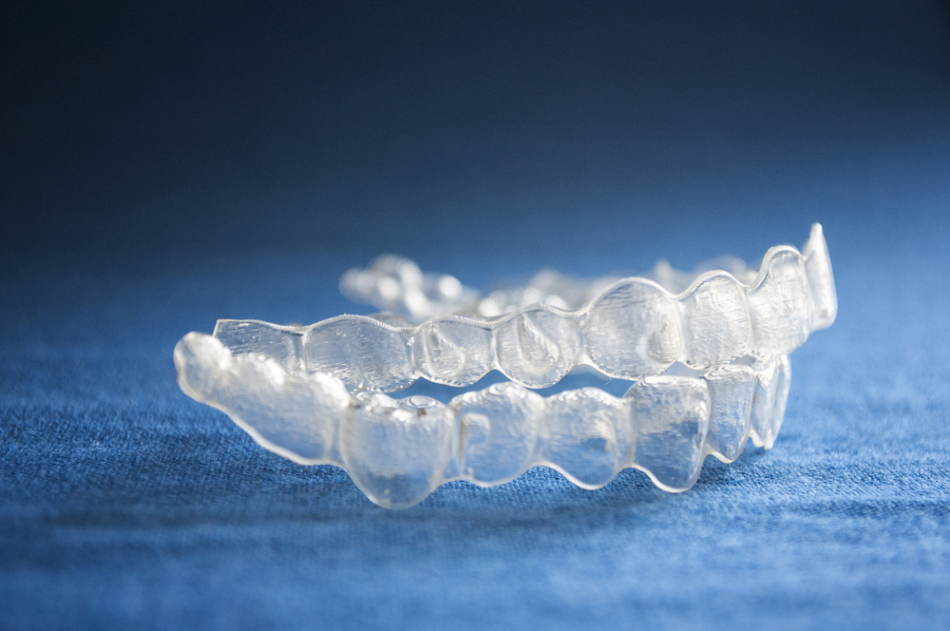
Image Credit: Lorena Tempera/Shutterstock.com
An award-winning additive manufacturing company, Spectroplast AG, has revolutionized the industrial market of 3D-printed products by developing the world's first high-precision silicone 3D printing technology.
The new technology meets a longstanding demand for a cost- and time-effective rapid prototyping and mass production of highly customizable silicone products, previously not accessible with conventional 3D printing technology.
Industrial-scale 3D printing using silicone brings functional high-precision silicone parts and products to the mass market through a wide range of industries, such as automotive, aerospace, consumer goods, healthcare, and food manufacturing. Components with tailored shapes and mechanical properties can be produced on a large scale using additive manufacturing of silicone.
First introduced more than 30 years ago, additive manufacturing was initially developed as a rapid prototyping method where a solid 3D object was built up in thin layers. Each layer corresponds to a slice (or a cross-section) of the object's digitally created model, allowing the design and manufacture of complex objects in a fraction of the time it would usually take, with a zero-waste material.
The intense development of a variety of additive processes for 3D manufacturing, commonly known as 3D printing, led to vastly improved accuracy and significant cost reductions with manufacturing hardware (3D printers) and building materials.
For more information on 3D printing technology, click here.
Material science innovations broadened the range of printable materials, meaning that designers and manufacturers are no longer limited to printing with rigid materials such as plastics, ceramics, and metals.
Silicone 3D Printing Technology as an Answer to a Growing Demand on the Market
One of the most recent advancements in additive manufacturing was the development of a new technology that enables the use of silicone as a 3D printing material.
Silicone (or polysiloxane) is a synthetic elastomer with excellent thermal stability (working temperature range -80 °C to 200 °C) and tear resistance. It was commercialized in the late 1940s and is biocompatible (easy to sterilize) and food-safe. Its surface is highly hydrophobic (repels water and surface contaminants) and is ideal for forming a tight seal.
The growing demand for silicone components is stimulated by their chemical and mechanical properties that are ideal for a broad range of applications.
However, some of its properties pose a real technological challenge as silicone's very high viscosity makes it difficult to extrude accurately. As an elastomer (or synthetic rubber), and unlike thermoplastics, silicone cannot be processed by melting and solidification.
To overcome the challenges associated with silicone 3D printing technology, Spectroplast calls on its substantial expertise in areas such as silicone material research, engineering, and additive manufacturing applications.
Spectroplast is a spin-off company from the Swiss Federal Institute of Technology in Zurich (ETH Zurich), where the company's co-founders, Manuel Schaffner and Petar Stefanov, spent several years developing silicone materials suitable for 3D printing applications. Launching Spectroplast allowed them to translate their research into a commercial opportunity.
3D printing of soft medical implants from silicone
Additive Manufacturing of Silicone Allows Cost, Time and Waste Reduction
Silicone components and parts are traditionally mass-fabricated by injection molding or casting. Both processes require prefabricated molds for each separate design, which slows down the whole production cycle and makes the small-scale manufacturing expensive and unsustainable. Additive manufacturing avoids the use of molds, reducing cost and time.
At the core of Spectroplast's cutting-edge silicone 3D printing technology is a well-established process called stereolithography (SLA). This method employs a printing vat filled with a liquid ultraviolet (UV)-curable silicone compound specially formulated by the company.
A spreader applies a thin and uniform layer of the liquid silicone onto the printer platform and a focused UV-light beam traces a slice of the 3D object to be printed. The UV-light solidifies the liquid silicone and joins the layer below.
For each subsequent layer, the printing platform sinks into the vat by a distance equal to the thickness of a single layer. This can be down to a few tens of microns. A fresh coat of liquid silicone is then spread on top of the solid structure.
The position of the light beam is also controlled on a micron scale. The printing steps are repeated until the 3D object is formed and the finished part arises out of the liquid.
Wide Range of Silicone Materials Suitable for 3D Printing Applications
Spectroplast's 3D printing technology offers customers industry-standard UV-curable silicones or a wide range of proprietary silicone materials, which hare often developed in collaboration with customers to meet their specific requirements.
The custom range of silicones covers a wide range of Shore hardness, between A0 and A80 (roughly corresponding to materials as soft as chewing gum or human skin, and as hard as a car tire or walking boot sole) and is expanding continuously.
The ability to cover a wide range of material properties together with the exquisite manufacturing precision and the unrestricted level of complexity of the final product can revolutionize silicone manufacturing and move the focus from mass production to mass customization. With its unique technology, Spectroplast can target a broad range of industries that require customized solutions. Applications include:
- Soft robotics
- Vibration damping
- Silicone valves and gaskets for the automotive and aerospace industry
- Non-stick cookware for the food industry
Tailored Medical Implants Become Reality with Silicone 3D Printing Technology
Silicone is a biocompatible material that is safe to use in medical devices and implants. The additive manufacturing of silicone life-enhancing products and medical implants opens up a whole new market to Spectroplast's technology. This includes anatomically relevant medical models (for surgical training), customized hearing-aids and dental implants, and bespoke silicone heart valve implants.
Manuel Schaffner, CEO of Spectroplast AG stated: "The replacement valves currently used are circular and cannot exactly match the shape of the aorta, which is different for each patient."
The rigid geometric shape of the traditional valve implants makes it challenging for the surgeons to ensure a tight seal between the implant and the cardiac tissue. By contrast, the patient-specific silicone heart valve implant gets around this problem, and it only takes one and a half hours to manufacture this type of valve using silicone 3D printing technology.
There is already a 7-10% gap in the silicone products market that conventional manufacturing methods cannot address due to technical challenges or costs. This is where the additive manufacturing of silicone products can truly impact our technological future.
Sources and Further Reading
Disclaimer: The views expressed here are those of the author expressed in their private capacity and do not necessarily represent the views of AZoM.com Limited T/A AZoNetwork the owner and operator of this website. This disclaimer forms part of the Terms and conditions of use of this website.