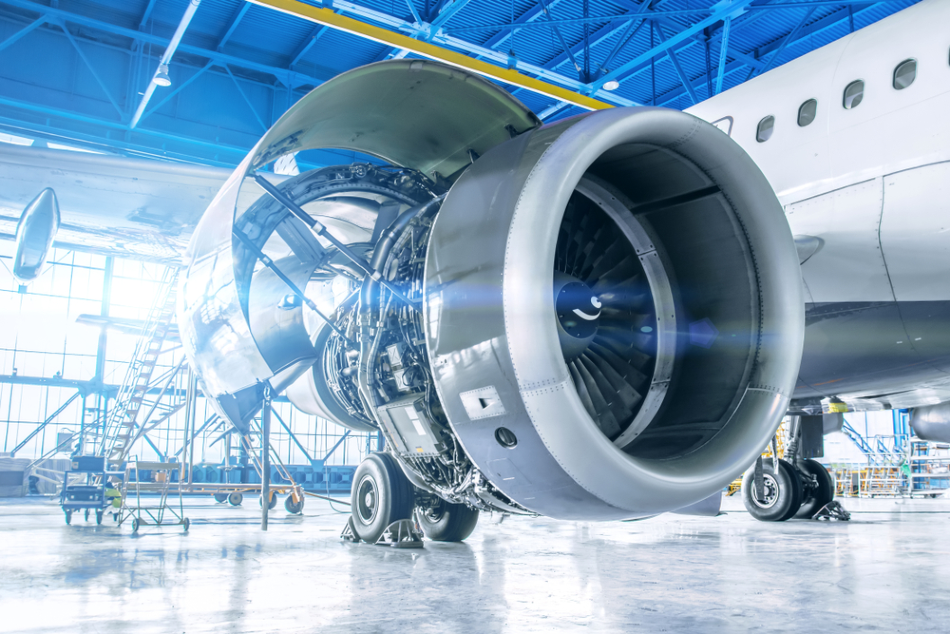
Image Credit: aapsky/Shutterstock.com
The Graphene Flagship project, funded by the European Commission with a total budget of €1 billion over 10 years (2013-2023), is investigating graphene, to enhance the aviation industry.
What is the Graphene Flagship Project?
Graphene, a two-dimensional atomic crystal constructed of carbon atoms arranged in a hexagonal lattice, is the strongest and lightest material known so far (Kostarelos & Novoselov, 2014).
Acknowledging its versatility, the EU Commission initiated the Graphene Flagship project (Graphene Flagship, 2020) as the first technology flagship to endorse graphene from laboratories to numerous industries.
The initiative coordinates over 145 academic and industrial research groups in 21 countries, and runs in two phases:
- 30 months under the 7th Framework Program with a total European Commission funding of €54 million
- The remaining months under the Horizon 2020 Program.
The Graphene Flagship Project and the Aviation Industry
The aviation industry is continuously looking into reducing the maintenance time or delay time on the ground while still keeping safety in the priority.
In 2018, global maintenance, repair and overhaul was valued at $69 billion, representing 9% of airline operational costs. This is expected to reach $103 billion by 2028 (IATA, 2019).
In freezing conditions, de-icing becomes a challenging and essential safety aspect as frozen contaminants jam control surfaces, preventing them from functioning normally. De-icing fluid costs between 1,000-10,000 Euros for smaller to larger private planes (Private Fly, 2020). The time, facilities, vehicles and personnel needed for de-icing quickly adds enormous amounts to already high operating costs.
Graphene-Based Thermoelectric Ice Protection Systems
One of the newest Spearhead projects, GICE (2020-2023), funded by the Graphene Flagship and backed by Airbus, is aiming to develop graphene-based thermoelectric ice protection systems to keep aircraft parts ice-free without affecting aerodynamic properties.
The key industrial partner Sonaca, which is the components supplier for Airbus, will collaborate to commercialize the graphene-based ice protection systems to the technology readiness level six. Successful completion of this project will provide an innovative de-icing system that is economically and environmentally beneficial for the aviation industry.
The current widely used de-icing system requires airport staff to spray the aircraft with either ethylene glycol or propylene glycol mixed with water until the contaminants are completely removed (Government of Canada, 2010).
Graphene Is.... Aeronautics
Video Credit: Graphene Flagship/YouTube.com
Other currently investigated materials to replace this system are carbon black, carbon rovings or carbon nanotubes (Graphene-info, 2019). However, the popularity of graphene as an electrically conductive material has initiated the exploration in this sector.
A reliable and inexpensive graphene-based ice protection system is in the development stage by many researchers (Vertuccio, De Santis, Pantani, Lafdi, & Guadagno, 2019) (Karim, et al., 2018). The GICE project aims to further commercialize using an electrical current to convert into heat and melt the ice.
A History of Aircraft Materials
In 1903, the Wright brothers flew the first motor-operated airplane made out of aluminum, wood and steel. Since then, aircraft materials have come a long way (Thomas, 2019). Aircraft constructed of heavier materials such as metals were designed to withstand the load of passengers and goods. Aluminum or aluminum alloy was essentially preferred due to its lightweight properties, designed for fuel-efficient technology.
In the mid-1930s, all-metal design principles were introduced, making it the primary material for the aviation industry, though the problems of corrosion and metal fatigue were discovered (Berends, Burg, & Raaij, 2011).
During World War Two, the shortage of metals stimulated the use of plastics in some of the replaceable parts, as they showed a proven ability to withstand chemically harsh environments.
Click here for more information on material processing and manufacturing.
Lighter and more fuel-efficient plastics became popular as electrical insulators and some mechanical components.
High-speed aviation required high strength and thermal resistance, leading the way to advanced carbon-carbon composites, titanium-aluminum alloys, and titanium alloys reinforced with ceramic fibers.
The aviation industry began to investigate various fiber-reinforced resin matrices that use resins. These included polyester, vinyl ester and epoxy reinforced with fibers such as glass and carbon.
The modern Airbus A350 is thought to contain 52% carbon-fiber-reinforced polymer (CFRP) (Marsh, 2007). Carbon composite materials consist of only 60% of the density of traditional aluminum, saving 20% weight and reducing fuel consumption.
Although using carbon composite is popular among Airbus and Boeing, the functional advantage of graphene in this industry is widely recognized and is the current focus of the aviation industry.
Graphene Materials in the Aviation Industry
Graphene can be chemically modified, making it applicable to a wide range of applications. Under the Graphene Flagship project, the world's first model aircraft 'Prospero' with graphene-skinned wings was tested and flown successfully at the Farnborough International Air Show in the UK in early 2016 (University of Central Lancashire, 2016).
This joint venture between The University of Manchester, the University of Central Lancashire and several SMEs, including Haydale Composite Solutions, reveals a new opportunity in investigating the effects of graphene material in drag reduction, thermal management and potential lightning strike protection.
Another fascinating initiative of Graphene Flagship in cooperation with the European Space Agency (ESA) has evaluated the use of graphene material in space applications (Graphene Flagship, 2019). In 2017, the consortium successfully tested graphene to enhance the efficiency of heat exchangers in gravity-free conditions to manage the temperature difference. The electrical and thermal conductivity of graphene material induces a faster flow of electrons than silicon, improving the heat transfer between the electronic units.
The Future of Graphene in the Aviation Sector
The inclusion of graphene material in the aviation industry has demonstrated the improvement of the mechanical properties while saving significant amounts of fuel, reducing maintenance time, and decreasing greenhouse gas emissions.
The Graphene Flagship Project has widely covered the rectifiable aspects of the industry in which graphene could be incorporated. So far, technological development has proved that graphene will play a huge role in making the aviation industry safer, more environmentally friendly and economically attractive in decades to come.
References and Further Reading
Aviation benefits beyond borders. (n.d). New materials and structural weight saving. [Online] Aviation benefits beyond borders. Available at: https://aviationbenefits.org/case-studies/new-materials-and-structural-weight-saving/ (Accessed on 03 May 2020).
Berends, H., Burg, E. v., & Raaij, E. M. (2011). Contacts and Contracts: Cross-Level Network Dynamics in the Development of an Aircraft Material. Organization Science, 22(4), 940-960. https://doi.org/10.1287/orsc.1100.0578
Government of Canada. (2010). Chapter 3 - Deicing/Anti-icing Fluids. [Online] Government of Canada. Available at: https://www.tc.gc.ca/eng/civilaviation/publications/tp10643-chapter3-summary-207.htm (Accessed on 03 May 2020).
Graphene Flagship. (2019). Airbus-Backed European Project Could Produce Safer Aircrafts. [Online] Graphene Flagship. Available at: https://graphene-flagship.eu/ (Accessed on 03 May 2020).
Graphene Flagship. (2019). Graphene goes to space. [Online] Graphene Flagship. Available at: https://graphene-flagship.eu/ (Accessed on 03 May 2020).
Graphene Flagship. (2020). Graphene Flagship. [Online] Graphene Flagship. Available at: http://graphene-flagship.eu/ (Accessed on 03 May 2020).
Graphene-info. (2019). Graphene Flagship launches Airbus-Backed Project for graphene-based thermoelectric ice protection systems. [Online] Graphene-info. Available at: https://www.graphene-info.com/graphene-flagship-launches-airbus-backed-project-graphene-based-thermoelectric (Accessed on 05 May 2020).
IATA. (2019). Airline Maintenance Cost Executive Commentary Edition 2019. [Online] IATA. Available at: https://www.iata.org/ (Accessed on 05 May 2020).
Karim, N., Zhang , M., Afroj , S., Koncherry, V., Potluri , P., & Novoselov, K. S. (2018). Graphene-based surface heater for de-icing applications. RSC advances, 8, 16815-16823. https://doi.org/10.1039/C8RA02567C
Kostarelos, K., & Novoselov, K. S. (2014). Graphene devices for life. Nature Nanotechnology. https://doi.org/10.1038/nnano.2014.224
Marsh, G. (2007). Airbus takes on Boeing with reinforced plastic A350 XWB. Reinforced Plastics. https://doi.org/10.1016/S0034-3617(07)70383-1
Plane Finder. (2017, 08 10). How Graphene could Revolutionise the Future of Aviation. [Online] Plane Finder. Available at: https://planefinder.net/about/news/graphene-revolutionise-aviation/ (Accessed on 05 May 2020).
Private Fly. (2020). De-icing for private jets. [Online] Private Fly. Available at: https://www.privatefly.com/privatejet-services/de-icing-private-jets.html (Accessed on 05 May 2020).
Thomas. (2019). A Brief History of Aircraft Materials. [Online] Thomas. Available at: https://www.thomasnet.com/insights/a-brief-history-of-aircraft-materials/ (Accessed on 05 May 2020).
University of Central Lancashire. (2016). World’s first flight of graphene-skinned aircraft to take place at Farnborough Air Show. [Online] University of Central Lancashire. Available at: https://www.uclan.ac.uk/news/graphene-skinned-aircraft-farnborough-show.php (Accessed on 05 May 2020).
Vertuccio, L., De Santis, F., Pantani, R., Lafdi, K., & Guadagno, L. (2019). Effective de-icing skin using graphene-based flexible heater. Composites Part B: Engineering, 162. https://doi.org/10.1016/j.compositesb.2019.01.045
Disclaimer: The views expressed here are those of the author expressed in their private capacity and do not necessarily represent the views of AZoM.com Limited T/A AZoNetwork the owner and operator of this website. This disclaimer forms part of the Terms and conditions of use of this website.