Successful insulation is not just about adding layers around heat sources. It needs to closely fit the dimensions of the components to reduce heat loss and make usage easier. When deciding the makeup of an insulation blanket, users need to know more about the materials that go inside.
Firwin Corporation’s team have wide-ranging knowledge regarding insulation materials and they have the ability to carefully match equipment with custom insulation covers and liners, produced from materials best matched for a user’s specific application. They offer a large selection of insulation materials for customers to choose from, guaranteeing an insulation solution that fits specific equipment and the particular needs of a facility.
Areas for Consideration
Selecting the correct material for insulation covers is vital, and not every material is suited for every application. Five areas that would affect the choice of a material are shown below:
1. Maximum Temperature Range
Possibly one of the most essential areas to consider in insulation materials is the temperature range. Insulation materials need to meet or exceed the high end of standard operating temperatures and should account for possible high-temperature extremes. Inadequate insulation can be expensive and unsafe.
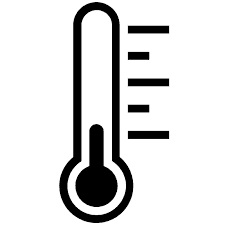
Image Credit: Firwin Corporation
2. Protection from the Elements
A user needs to evaluate the equipment’s exposure to elements, for example, water, debris, chemicals, and UV radiation. Selection of materials for insulation covers needs to include consideration of which materials can tolerate these environmental factors without degrading.
Some protective elements could be added to insulation materials, but others have the potential to cause stiffness or negatively influence ease of use. All materials at Firwin have their own property set, but a selection are superior at handling extreme environments in comparison to others. Depending on the equipment’s exposure, one type of material might be more appropriate as insulation compared to others.
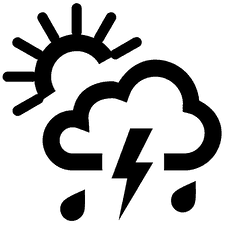
Image Credit: Firwin Corporation
3. Safety and Regulatory Requirements
It is essential to consistently check the manufacturer’s certifications for facility equipment, particularly with regards to safety. Certain industries also have more comprehensive UL and safety standard requirements in comparison to others.
Firwin ensures that insulation covers are produced with high-quality materials and the business is ISO 9001-certified. They have a team of engineers and technicians who work hard to meet or exceed all safety and regulatory requirements. Some safety requirements, such as fire retardancy, will influence which materials they select for insulation on the basis of the material properties.
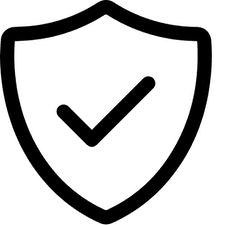
Image Credit: Firwin Corporation
4. Space
The type and quantity of insulation that can be added to a given system is limited by space. Thin and flexible materials are recommended for use near tight system configurations and controls. However, there are less restrictions on material type in areas with more space.
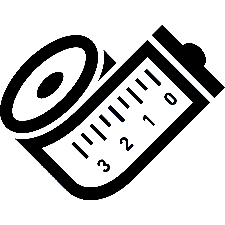
Image Credit: Firwin Corporation
5. Touch Temperature
The maximum temperature factor specifies the amount of heat a user’s insulation covers are able to safely handle, whereas the “touch” temperature factor specifies the handling temperature on the outside of the cover.
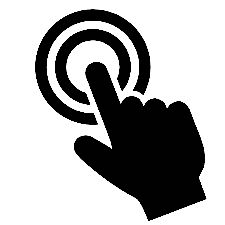
Image Credit: Firwin Corporation
Certain insulation materials have the ability to only decrease ambient heat in environments that just need lower, but not safe to touch, temperatures. Other insulation materials can comprehensively dampen heat in applications where the covers need to be handled throughout the day.
While small or limited environments might demand thinner material and/or somewhat higher temperatures, a consistent priority for the manufacturing team is a safe contact rating.
When considering a suitable exterior temperature for insulation materials, it is essential not to forget that fabric is safer at high temperatures in comparison metal. Fabric does not conduct heat as well as metal can, so it needs to surpass 203 °F (95 °C) before becoming dangerous to handle (UL 2200).
Insulation Materials
Video Credit: Firwin Corporation
Regularly Used Insulation Materials
It is helpful to know what insulation materials are available when designing an insulation. Some regularly used materials/fabrics for commercial and industrial insulation covers include:
Aerogel
This first-rate material is superior in performance than both wool and fiberglass. A cover of Aerogel that is 0.5-inches thick has the ability to perform just as successfully as a 1.5-inch thick cover of fiberglass. Due to this, facility managers frequently utilize this material in tight-fit environments.
Aerogel is extremely lightweight, making it perfect for use near fragile or light components. However, the material is costly, and has a maximum temperature limit of 1100 °F (593 °C).
CMS Wool
Cellulose material solutions (CMS) wool is compact, moderates oxygen transfer through the material, and has fire-retardant properties in addition to its high insulation value. Additional properties include:
- A maximum temperature threshold of 2192 °F (1200 °C)
- Odorless
- Not a contributor to corrosion
- Sound absorbent
- Decay, vermin, and mold resistant
Fiberglass
Fiberglass is one of the most frequently used insulative materials utilized in the manufacture of insulation blankets. Similar to CMS wool, it is odorless, will not corrode metal, can absorb sound, and is resistant to rot or vermin damage.
However, it has a lower maximum temperature threshold of 1200 °F (649 °C) and can cause harm employees through continuous exposure if adequate safety equipment covering their eyes, skin, or breathing passages is not provided.
Mineral Wool
The wide-ranging category of mineral wool materials is inclusive of:
- Glass wool (produced using recycled glass)
- Rock wool (produced from basalt)
- Slag wool (most common mineral wool, produced from steel mill slag)
The thermal resistance of mineral wool is good, it does not absorb moisture, and it can stifle a reasonable level of sound. Its maximum temperature limit is 1200 °F (649 °C).
Insulation Materials from Firwins
Firwin Corporation utilizes specialty materials to ensure a facility’s equipment is well-insulated and safe for employees. The high-performance materials include:
Firwin 2000+ Insulation
This material has brilliant thermal resistance, in addition to resistance to chemicals or contamination. It keeps its insulative properties even after oil or water spills after the material has dried. Firwin 2000+ is a patented wool material manufactured from long AES fibers. It has low bio-persistence and high maximum temperature limits.

Image Credit: Firwin Corporation
Properties
- Rated Temperature 2192 ºF (1200 ºC)
- Sound absorbent
- Easy installation
- Brilliant thermal stability and insulation
- High levels of strength and good tear resistance
- Heat storage is low
- Irritant levels are low and enhanced softness
- Thermal conductivity is low
- Low levels of outgassing due to cleaning and removal of organic matter throughout manufacture
- Solubility in body fluids
Applications
This material is frequently used for the following applications:
- Acoustical service
- Annealing furnace linings
- Cryogenic insulation
- Expansion joint packing
- Fire protection
- Furnace kiln reformer and boiler lining
- Lining of furnace doors and seals
- Repair of furnaces
- Investment casting mold wrap
- Ovens in laboratories
- Removable insulation blankets
- Stress-relieving blankets
Board Insulation 15080 RHF™40
This is a stiffer material that consists of basalt rock and slag. It is a non-combustible material with brilliant fire and thermal resistance, water-repelling properties, and vapor permeability. Its melting point is at 2150 °F (1177 °C). This mineral wool can be safely used in high-heat applications up to 1200 °F (649 °C).
Properties
- Availability of fabrication and lamination options
- Chemically inert and non-corrosive
- Non-combustible
- Lightweight
- Produced from natural and recycled materials; free from CFC and HCFC
- Low moisture absorption
Applications
Facility managers can utilize Board Insulation 15080 RHF™40 for a number of applications. The team at Firwin’s can produce the material to match different stipulations without any lack of fire, thermal, and water resistance. One application it is most frequently used is pipe and tank wrapping due to the moisture resistance and insulating properties of the materials.
Rockwool Board Insulation 8LB
This is a non-combustible material that also consists of basalt rock and slag. It features durable water resistance while simultaneously maintaining vapor permeability. It has excellent fire and thermal resistance due to its high melting point of 2150 °F (1177 °C).
Properties
- Easy installation and use
- Availability of fabrication and lamination options
- Chemically inert and non-corrosive
- Non-combustible
- Lightweight
- Produced from natural and recycled materials; free from CFC and HCFC
- Low moisture absorption
Applications
This material withstands physical damage and compression from impacts. Additionally, it is a helpful insulation solution for applications that need outstanding thermal, fire, and moisture damage resistance.
Firwin Vermiculite Coated Fiberglass Fabric
This medium-weight, woven fiberglass material has good resistance to high temperatures. It also features a vermiculite compound coating that enhances thermal resistance.
Properties
- Can resist constant heat during long-term applications
- Might be subject to some physical degradation following extended exposure to high heat
- Has a continuous temperature limit of 1200 °F (649 °C) and an intermittent limit of 1500 °F (816 °C)
Applications
- Flame and high-heat barriers
- Silica or ceramic fabrics replacement
Firwin 1200 Insulation Mat
This glass fiber material is mechanically bonded from long, uniform fibers. The needling process generates an extremely uniform material that does not include binders. This material offers long-term insulation while exposed to high temperatures up to 1200 °F (649 °C).
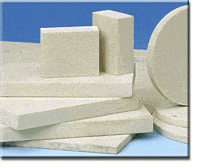
Image Credit: Firwin Corporation
Properties
- Easy installation due to drapability and flexibility
- No contribution to metal corrosion, decay, or mold
- Vermin-related damage resistant
- Stifles sound and vibration
- Odorless
Firwin Corporation is a specialist in high-quality, customizable insulation covers and other insulation solutions. They design covers for a broad variety of industries and applications, inclusive of general industrial applications, diesel and gas engines, and exhaust systems.
Acknowledgments
Produced from materials originally authored by Firwin from Firwin Corporation.
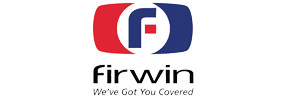
This information has been sourced, reviewed and adapted from materials provided by Firwin Corporation.
For more information on this source, please visit Firwin Corporation.