Additive Manufacturing (AM), commonly referred to as the 3D printing of metals, is a new and rapidly developing technique for manufacturing. It allows manufacturers to easily create parts and components with complex structures, by constructing them layer by layer from metal powder beds. Manufacturers can even produce items with hybrid metal-polymer printing techniques.
The AM technique is applied to a number of different metal alloys, such as Ti64 or AlSi10Mg. A range of stainless steel types is also very commonly used in the AM process as they possess broad ranges of properties. But what do all of these materials have in common? Quality control and quality assurance are necessary in order to control the printing parameters, consequently controlling the quality of the final product not just in industrial production and research and development applications, but also in academic research, too.
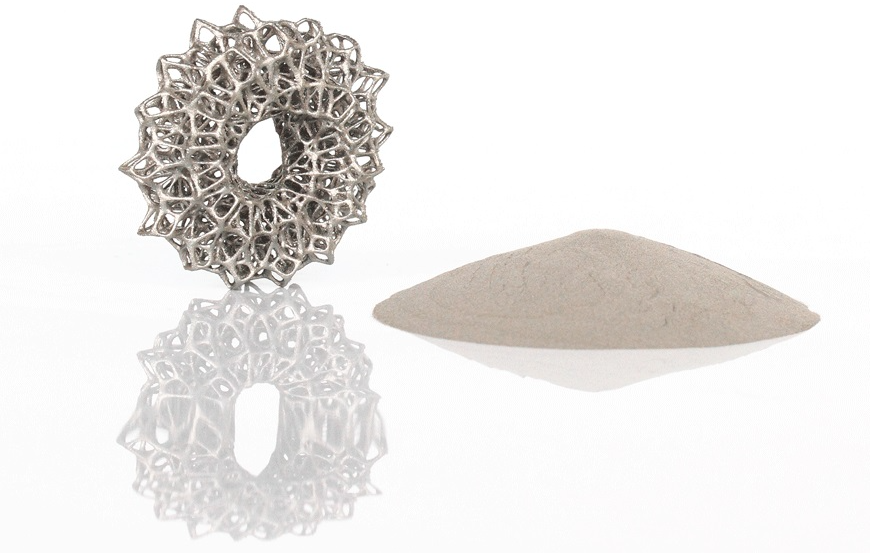
X-ray diffraction (XRD) stands as one of the most commonly used methods to assess the microstructure of metal alloys. With XRD, it is possible to directly measure crystallographic structures of related components and quantify their content. This is particularly beneficial when it is necessary to plan temperature treatment steps, analyze the anisotropy of the printing process, or obtain an indication of the mechanical properties in parts. It is even possible to vary the penetration depth (and the volume of the analysis as a result) just by choosing the type of radiation, for instance, Co or Mo radiation.
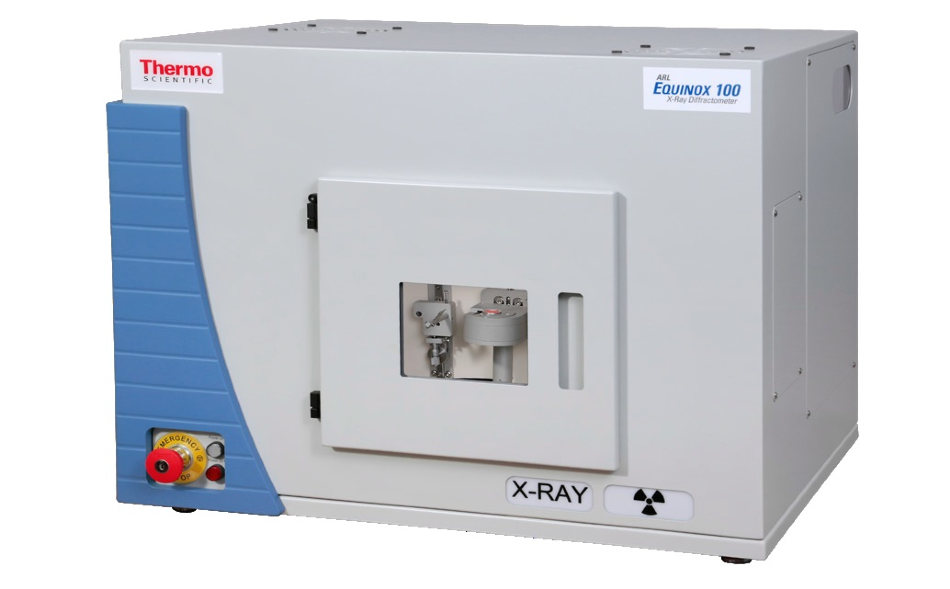
Figure 1. ARL EQUINOX 100 X-Ray Diffractometer.
About the Thermo Scientific™ ARL™ EQUINOX 100 X-Ray Diffractometer
The Thermo Scientific™ ARL™ EQUINOX 100 X-ray Diffractometer is built with a custom-designed Co (15 W) micro-focus tube with mirror optics for high flux, which entirely eliminates the need for external water chilling. The ARL EQUINOX 100 XRD also boasts rapid data collection times due to the unique curved position sensitive detector (CPS), which effectively measures all diffraction peaks at the same time. It is because of these features that it is very well suited to measurements of both reflection and transmission (Figure 1).
Case Study
To complete XRD measurements, a 410 stainless steel cube-shaped sample from AM was measured with Co Kα radiation for 5 or 15 minutes in reflection, utilizing an SSRZ sample holder, which included height adjustment and sample spinning when bulk samples were being used. MDI JADE 2010 facilitated qualitative and quantitative analysis.
Results
XRD measurements, longitudinal and transversal to the printing direction, reveal an anisotropy in the microstructure of the steel. This occurred because of variations in the Austenite content of the steel. No Austentite was detected longitudinal to the printing (c.f. Figure 2), but 1.3 wgt% Austentite was detected transversal to the printing direction (c.f. Figure 3).
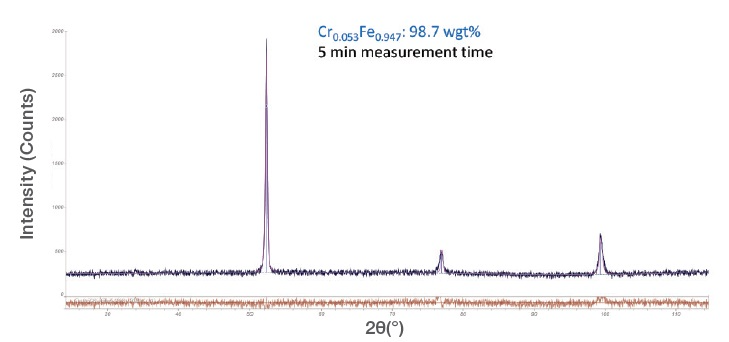
Figure 2. XRD measurement longitudinal to the printing direction.
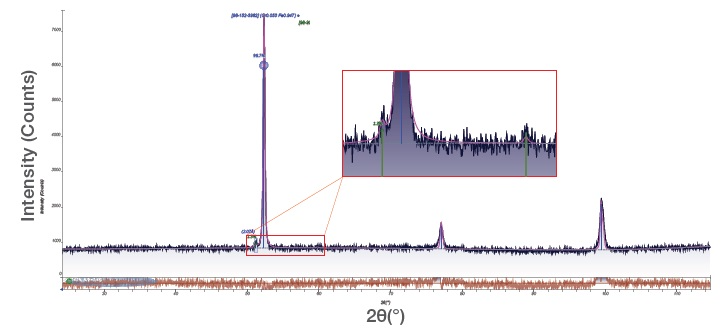
Figure 3. XRD measurement is transverse to the printing direction.
Summary
The ARL EQUINOX 100 benchtop diffractometer has been proven to be a convenient tool to investigate the microstructure of metal samples sourced from AM processes independent of the printing direction. The second investigation carried out in the case study was focused on surface effects because of the low penetration depth of low-energy Co radiation.
In opting for Mo radiation over Co radiation, it was also found to be possible to generate data from deeper regions in bulk samples when used in conjunction with MDI JADE 2010. This meant that the quantification of Austenite content could offer suggestions of residual stress, determined by the retained Austenite content in the samples of stainless steel.
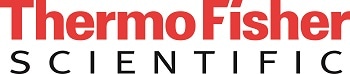
This information has been sourced, reviewed and adapted from materials provided by Thermo Fisher Scientific - Elemental Analyzers and Phase Analyzers.
For more information on this source, please visit Thermo Fisher Scientific - Elemental Analyzers and Phase Analyzers.