Fine powders and granular materials are commonly utilized in industrial applications. These materials must be characterized with precision to optimize and control processing techniques.
The characterization techniques correspond either to the behavior of the bulk powder (electrostatic properties, blend stability, density, flowability) or the characteristics of the grains (chemical composition, morphology, granulometry).
In relation to the physical behavior of the bulk powder, the majority of the techniques utilized in quality control or R&D laboratories are established on outdated measurement methods.
GranuTools has revised these techniques over the past decade to satisfy the current demands of production departments and R&D laboratories. Stringent initialization techniques have been produced and the measurement processes have been automated to acquire results that are interpretable and reproducible.
The accuracy of the measurement has been enhanced through the use of image analysis techniques. A number of industries have already adopted the range of instruments by GranuTools in various disciplines, such as bulk material handling, food processing, pharmaceuticals, and additive manufacturing. This article will primarily focus on additive manufacturing.
Polymer and metallic powders are frequently incorporated in Additive Manufacturing (AM) procedures, in Selective Laser Sintering (SLS) and Selective Laser Melting (SLM) for example. During these processes, thin layers of powder are produced in succession with a rotating cylinder or with a ruler.
Individual layers are then partially melted or sintered using an energy beam to construct the parts. The printer’s vertical resolution is determined by the layer thickness, where a higher resolution is achieved by a thinner layer.
The powder must be as fine as possible in order to achieve a thin layer. Unfortunately, the spreadability declines and the cohesiveness increases as the grain size becomes smaller.
The fatigue behavior and final strength of the constructed pieces crucially depend on the density of the parts created through AM processes, and the volume of pores within the part (for example, Leuders et al. 2013).
In a recent study, Riener et al. (2020) have highlighted the relationship between the final density of the build parts and the density of the deposited layer. Parts of a higher density are produced by layers of a higher density, which results in a stronger final piece.
For this reason, the powder’s spreadability is not the only key characteristic to measure. A powder that packs well will result in a powder layer of a higher density. Therefore, the powder’s packing behavior should also be measured.
The focus of this article is to highlight how the homogeneity of the layers created during recoating within SLM printers is affected by the packing dynamic properties of metal powders.
The GranuPack, an automated tapped density analyzer, was used to quantify packing characteristics in this study.
These results have been related to the homogeneity of the powder bed acquired using in situ SLM printer measurements. These have been outlined in full in a previous article: “Linking Powder Rheology Characterization to Spreadability in Powder Bed-Based AM”.
GranuPack
The GranuPack instrument (Figure 1) is an enhanced and automated tapped density measurement technique created using the latest and most crucial research findings. The automated instrument analyzes the behavior of a powder that is subjected to repeated tapping.
The final density after n taps ρ(n) and the initial density ρ(0) provide the Hausner ratio (Hr), which is quantified with precision. The number of taps is normally constant at n=500. Known as the number of taps necessary to achieve half of the final compaction, a dynamical parameter n1/2 can be extracted to measure the packing behavior (review Appendix 1).
The powder is positioned in a metallic tube where a stringent automated initialization procedure occurs. A light, the hollow cylinder is then positioned above the powder bed to ensure that the air/powder interface remains flat throughout the process of compaction.
The tube where the powder sample is contained increases to set height of ΔZ and carries out free falls. The height of the free fall is usually predetermined at ΔZ = 3 mm or ΔZ=1 mm. After each tap, the height h of the powder bed is quantified automatically. The volume V of the pile is calculated from the height h.
The density ρ is observed and noted after every tap due to the powder mass m being known. The ratio between the powder bed volume V and mass m provides the density. With the GranuPack technique, even a small amount of powder (normally 35 ml) will provide reproducible results.
The Hausner ratio Hr corresponds to the ratio of compaction and is determined through the equation Hr = ρ(500) / ρ(0) , where ρ(500) is the tapped density calculated after 500 taps and ρ(0) is the initial bulk density.
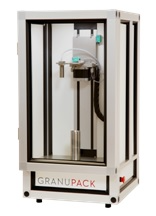
Figure 1. The GranuPack, a high resolution tapped density analyzer.
Powders Description
Four metallic powders supplied by the Sirris were chosen for this investigation: two aluminum alloys (AlSi7Mg06, Scalmalloy®) and two Nickel alloys (Inconel®, Inconel® fine). The particle size distribution is presented in Table 1:
Table 1. Summary of the PSD (D10 and D90) of the four powders.
Powder |
d10 (µm) |
d90 (µm) |
Inconel®fine |
3,6 |
22 |
Inconel® |
14 |
46 |
AlSi7Mg06 |
20 |
63 |
Scalmalloy® |
20 |
59 |
Spreadability Assessments
Experiment Protocol and Results
The powder bed’s homogeneity after each recoating procedure has been quantified within an SLM printer. An image is captured by a CCD camera positioned inside of the printer for each new layer of powder.
An image analysis software (GranuLayer) is then utilized to calculate an interface fluctuation, which shows the layer’s homogeneity in relation to each of the powders.
Figure 2 shows the interface fluctuation compared to the recoater speed captured with the image processing technique:
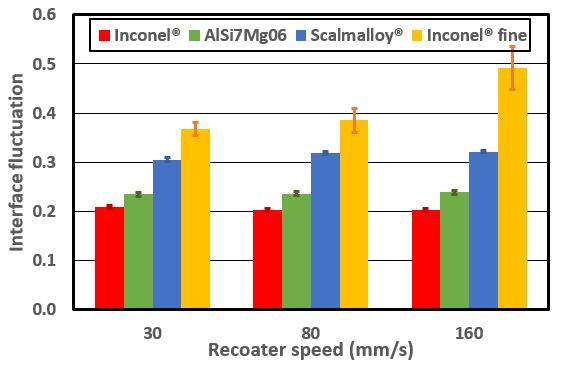
Figure 2. Interface fluctuations as a function of recoater speed (in mm/s).
Discussion
AlSi7Mg06 and Inconel® exhibit a smaller interface fluctuation, which means more homogeneous layers are produced within the printer for each of the recoater speeds.
Despite its particle sizes being smaller, the Inconel® produces a slightly lower interface fluctuation. As the recoater speed only affects these powders slightly, processing at 160 mm/s is estimated to be the most effective recoating velocity.
Scalmalloy® provides a greater interface fluctuation because of the existence of parallel waves on the powder bed but exhibits steadier behavior as the recoater speed increases.
The Inconel® fine exhibits a greater interface fluctuation which demonstrates the very weak processability seen in the printer. Less spreadability and greater cohesiveness is caused by the smaller particle sizes of the Inconel® fine.
GranuPack Analysis
Experimental Protocol
500 taps were given to the sample with a taps frequency of 1 Hz for each experiment with the GranuPack. The measurement cell free-fall was 1 mm (∝ tap energy).
In order to assess reproducibility, the measurements were repeated three times. Prior to each experiment, the temperature (21 °C) and the air relative humidity (28% RH) were noted.
Experimental Results
After the GranuPack procedure has finished, the final bulk density (at a number of taps, n = 500; i.e. ρ(500)), the initial bulk density (ρ(0)), and the Hausner ratio/Carr index (Hr/Cr) are noted. The table below compares the experimental data:
Table 2. GranuPack results for the four powders.
Sample Name |
ρ(0) (g/ml) |
ρ(500) (g/ml) |
Hr |
Cr |
AlSi7Mg06 |
1,394 |
1,681 |
1,21 |
17,08 |
Inconel® |
4,130 |
5,059 |
1,23 |
18,36 |
ScalmAlloy® |
1,209 |
1,553 |
1,28 |
22,16 |
Inconel® fine |
3,947 |
5,461 |
1,38 |
27,73 |
Figure 3 shows the full packing curve, for example ρ(n) versus tap number:
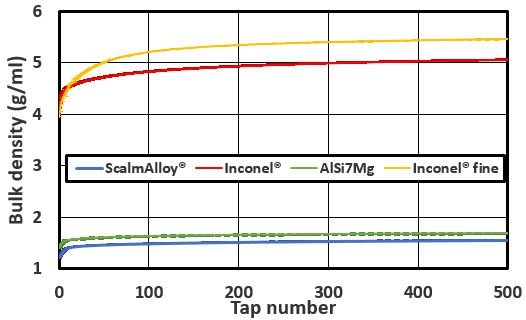
Figure 3. Bulk density variations versus taps number for all powders. Error bars may be comprised in the thickness of the line.
Discussion
The packing ability of a powder can be discovered using the Hausner ratio (Hr). The powder can maintain a lower bulk density when highly cohesive interactions occur between the grains.
Due to this, the packed density can be significantly higher compared to the bulk density, resulting in a high Hausner ratio. The Hausner ratio can be seen as an indirect way to quantify powder cohesiveness.
The results in Table 2 show that AlSi7Mg06 has the smallest Hausner ratio (Hr = 1.21), slightly more than Inconel® (Hr=1.23). Scalmalloy® provides a higher Hr of 1.28, and the Inconel® fine is clearly the highest with a Hausner ratio that is greater than 1.30.
It is apparent that Inconel® and AlSi7Mg06 are the least cohesive and are estimated to create layers of powder with a higher density.
The two aluminum alloys (AlSi7Mg06 and ScalmAlloy®) have the greater particle sizes shown in the PSD outlined in Table 1. The Inconel® provides a lower Hausner ratio compared to ScalmAlloy® which could show that the shapes of the particles are the key parameter of the packing dynamic in this example.
The Hausner ratio calculated using the GranuPack agrees with the interface fluctuation acquired from in situ measurements. This demonstrates that the packing behavior of the powder performs an important role in spreadability throughout the process of recoating.
The classification of powders in relation to their packing behavior enables their performance regarding powder bed homogeneity to be predicted.
Conclusions
- To ensure the build parts are strong, homogeneous powder bed density is crucial.
- The investigated powders can be categorized in relation to their packing dynamics.
- An increase in homogeneity in the layers within the printer and low interface fluctuation is observed when powders with a low Hausner ratio are used.
Acknowledgments
GranuTools thanks Sirris (Olivier Rigo) for carrying out all the 3D printing experiments and for providing the powders.
Appendix 1: Data Interpretation with GranuPack
The dynamical parameter n1/2 relates to the number of taps required to achieve one half of the compaction curve. The compaction is more efficient when this parameter is lower (which corresponds to experimental data).
A theoretical model describes the compaction curve in order to acquire the parameter tap number τ. The compaction is faster when this parameter is lower (in line with modeling data).
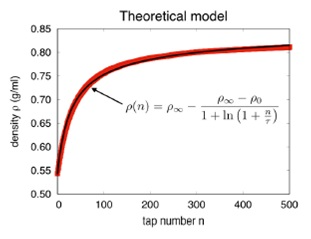
References and Further Reading
- Cascade of granular flows for characterizing segregation, G. Lumay, F. Boschin, R. Cloots, N. Vandewalle, Powder Technology 234, 32-36 (2013).
- Combined effect of moisture and electrostatic charges on powder flow, A. Rescaglio, J. Schockmel, N. Vandewalle and G. Lumay, EPJ Web of Conferences 140, 13009 (2017).
- Compaction dynamics of a magnetized powder, G. Lumay, S. Dorbolo and N. Vandewalle, Physical Review E 80, 041302 (2009).
- Compaction of anisotropic granular materials: Experiments and simulations, G. Lumay and N. Vandewalle, Physical Review E 70, 051314 (2004).
- Compaction Dynamics of Wet Granular Assemblies, J. E. Fiscina, G. Lumay, F. Ludewig and N. Vandewalle, Physical Review Letters 105, 048001 (2010).
- Effect of an electric field on an intermittent granular flow, E. Mersch, G. Lumay, F. Boschini, and N. Vandewalle, Physical Review E 81, 041309 (2010).
- Effect of relative air humidity on the flowability of lactose powders, G. Lumay, K. Traina, F. Boschini, V. Delaval, A. Rescaglio, R. Cloots and N. Vandewalle, Journal of Drug Delivery Science and Technology 35, 207-212 (2016).
- Experimental Study of Granular Compaction Dynamics at Different Scales: Grain Mobility, Hexagonal Domains, and Packing Fraction, G. Lumay and N. Vandewalle, Physical Review Letters 95, 028002 (2005).
- Flow abilities of powders and granular materials evidenced from dynamical tap density measurement, K. Traina, R. Cloots, S. Bontempi, G. Lumay, N. Vandewalle and F. Boschini, Powder Technology, 235, 842-852 (2013).
- Flow of magnetized grains in a rotating drum, G. Lumay and N. Vandewalle, Physical Review E 82, 040301(R) (2010).
- How tribo-electric charges modify powder flowability, A. Rescaglio, J. Schockmel, F. Francqui, N. Vandewalle, and G. Lumay, Annual Transactions of The Nordic Rheology Society 25, 17-21 (2016).
- Influence of cohesives forces on the macroscopic properties of granular assemblies, G. Lumay, J. Fiscina, F. Ludewig and N. Vandewalle, AIP Conference Proceedings 1542, 995 (2013).
- Influence of particle size distribution and morphology on the properties of the powder feedstock as well as of AlSi10Mg parts produced by laser powder bed fusion (LPBF), K. Riener, N. Albrecht, S. Ziegelmeier, R. Ramakrishnan, L. Haferkamp, A. B. Spierings, G. J. Leichtfried, Additive Manufacturing 34, 101286 (2020).
- Linking compaction dynamics to the flow properties of powders, G. Lumay, N. Vandewalle, C. Bodson, L. Delattre and O. Gerasimov, Applied Physics Letters 89, 093505 (2006).
- Linking flowability and granulometry of lactose powders, F. Boschini, V. Delaval, K. Traina, N. Vandewalle, and G. Lumay, International Journal of Pharmaceutics 494, 312–320 (2015).
- Measuring the flowing properties of powders and grains, G. Lumay, F. Boschini, K. Traina, S. Bontempi, J.-C. Remy, R. Cloots, and N. Vandewalle, Powder Technology 224, 19-27 (2012).
- Motion of carbon nanotubes in a rotating drum: The dynamic angle of repose and a bed behavior diagram, S. L. Pirard, G. Lumay, N. Vandewalle, J-P. Pirard, Chemical Engineering Journal 146, 143-147 (2009).
- Mullite coatings on ceramic substrates: Stabilization of Al2O3–SiO2 suspensions for spray drying of composite granules suitable for reactive plasma spraying, A. Schrijnemakers, S. André, G. Lumay, N. Vandewalle, F. Boschini, R. Cloots and B. Vertruyen, Journal of the European Ceramic Society 29, 2169–2175 (2009).
- On the mechanical behavior of titanium alloy TiAl6V4 manufactured by selective laser melting: Fatigue resistance and crack growth performance, S. Leuders, M. Thöne, A. Riemer, T. Niendorf, T. Tröster, H.A. Richard, H.J. Maier, International Journal of Fatigue 48, 300-307 (2013).
- The flow rate of granular materials through an orifice, C. Mankoc, A. Janda, R. Arévalo, J. M. Pastor, I. Zuriguel, A. Garcimartín and D. Maza, Granular Matter 9, p407–414 (2007).
- The influence of grain shape, friction and cohesion on granular compaction dynamics, N. Vandewalle, G. Lumay, O. Gerasimov and F. Ludewig, The European Physical Journal E (2007).
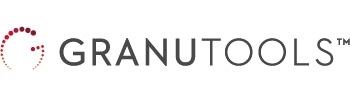
This information has been sourced, reviewed and adapted from materials provided by Granutools.
For more information on this source, please visit Granutools.