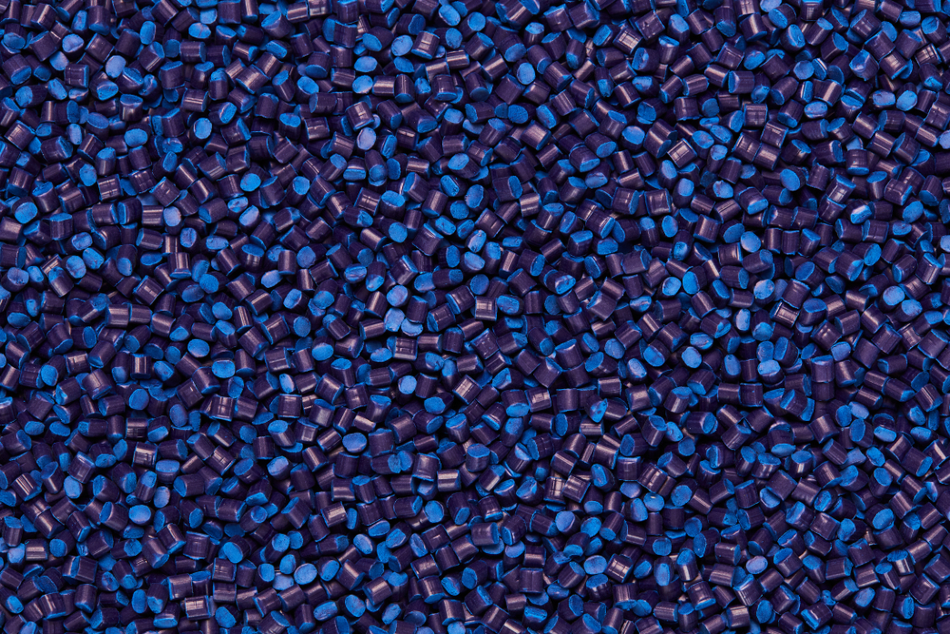
Image Credit: sveticluka/Shutterstock.com
An industrial partnership between Braskem, one of the largest producers of polypropylene and biopolymers in the Americas, and Advanced Laser Materials (ALM), a leading supplier of materials and equipment for additive manufacturing applications, brings an innovative thermoplastic polymer to the market that can be used in Selective Laser Sintering (SLS) powder bed 3D printing.
The growing success of the additive manufacturing technology is underpinned not by individual products such as printers or materials, but by providing an end-to-end solution that combines product design, printing technology, and material development into a single package suitable for a wide range of customer applications.
As one of the world's leading suppliers of 3D printing technology, ALM (a wholly-owned subsidiary of EOS Group) boasts a comprehensive portfolio of laser sintering solutions and advanced materials for industrial 3D printing applications.
Growing Demand for New Materials Suitable for Additive Manufacturing Applications
However, the insufficient material variety has been a long-standing limiting factor for the wider adoption of SLS for industrial manufacturing applications.
Joining forces with the Brazilian petrochemical company Braskem, a leading supplier of polypropylene to the industry in North America, allows ALM to offer powdered polypropylene as their newest addition to the additive manufacturing materials available on the market. The new material promises to deliver superior 3D printing capabilities compared to other available materials such as polyamide (Nylon) powders.
Affordable and Versatile Polymer Material with Countless Applications
Polypropylene (or polypropene) is a thermoplastic polymer synthesized through the polymerization of propylene (or propene, a colorless hydrocarbon gas produced by oil refining). The material's semi-crystalline molecular structure provides high mechanical strength (with a typical tensile strength of around 1.9 GPa) combined with excellent flexibility.
Click here to find out more about chemical analysis equipment.
Polypropylene's versatility and affordability make it the second most widely produced commodity plastic in the world (after polyethylene). It is used in a wide variety of industrial applications where its long-term durability and high resistance to impact, wear, and aggressive chemicals ascertain the material's vital role as a manufacturing material.
Because of its semi-crystalline structure, the polypropylene presents extra difficulties, such as a tendency to shrink and warp, when processed in additive manufacturing applications. Traditionally, the majority of the industrial polypropylene components are manufactured by injection molding.
How Does Selective Laser Sintering Work?
SLS, also known as powder bed fusion, is a laser-based additive manufacturing technology that uses powdered materials, typically metals or thermoplastic polymers. It is the “workhorse” technology for industrial 3D printing because of its suitability for serial manufacturing and its ability to handle large-scale components with complex shapes.
A thin layer of powdered material is spread across a support platform, creating a powder bed. A computer-controlled laser beam selectively melts and binds together the particles in the powder bed, forming a thin slice of the manufactured object(s). The support platform is then lowered by a distance equal to the powder layer thickness, and another layer is deposited across the bed. The process is repeated layer-by-layer and the material is fused to create a solid 3D object.
As the powder in the bed is self-supporting, SLS does not require sacrificial support structures when printing components with complex shapes. An added benefit is the fact that a large number of components, even with different shapes and sizes, can be printed in parallel, resulting in better cost-efficiency and minimal waste. SLS is also a highly sustainable manufacturing process, as the unused powder can be fully reused.
The new polypropylene powder developed by Braskem and ALM offers the same properties as the polypropylene commonly used in injection molding. The same polymer materials can now be used for the fabrication of 3D-printed components with reduced weight, enhanced mechanical strength and chemical resistance, and improved recyclability.
Additive Manufacturing of Polypropylene Sparks Immediate Interest in Manufacturers
Braskem and AML envisage numerous immediate applications of the new thermoplastic polymer. For example, prototype parts manufactured from 3D-printed polypropylene offer the unique advantage of being made of the same material as the final product.
In the automotive industry, where polypropylene is widely used in the vehicle's interior and exterior finishing, the manufacturers will be able to use the same thermoplastic polymer for prototyping and mass-production of the final parts.
Sustainable Polymer Materials for 3D Printing Applications
Additive manufacturing of the new thermoplastic polymer would enable mass production of consumer goods and packaging solutions with durable snap-fit assemblies or functional features such as living hinges (flexible seamless joint made from the same material as the joined parts) for an improved end-user experience.
Read more: 3D printing equipment, materials and processing
Looking into the future, Braskem and ALM intend to continue their joint R&D effort and expand the range of SLS-compatible materials by offering sustainable bio-based polymer materials.
The ultimate goal of the two partner companies is to enable high-performance 3D-printed components to replace injection-molded products in many industrial sectors, including as the automotive and aerospace industries, consumer goods manufacturing, and the biomedical industry, where an optimal balance between the material's performance and cost is desired.
References and Further Reading
L. Griffiths (2020) Braskem and ALM collaborate on new polypropylene additive manufacturing powder. [Online] www.tctmagazine.com Available at: https://www.tctmagazine.com/additive-manufacturing-3d-printing-news/braskem-alm-launch-polypropylene-additive-manufacturing/ (Accessed on 29 June 2020).
Braskem (2020) Braskem and ALM Announce the Launch of Polypropylene Powder for Additive Manufacturing. [Online] www.braskem.com.br Available at: https://www.braskem.com.br/usa/news-detail/braskem-and-alm-announce-the-launch-of-polypropylene-powder-for-additive-manufacturing (Accessed on 29 June 2020).
I. F. Ituarte et al. (2018) Additive Manufacturing of Polypropylene: A Screening Design of Experiment Using Laser-Based Powder Bed Fusion. Polymers, 10, 1293. Available at: https://doi.org/10.3390/polym10121293
ALM (2019) Braskem and Advanced Laser Materials (ALM) Announce Partnership for the Development of Advanced Polyolefins for 3D Printing and Additive Manufacturing. [Online] https://www.advancedlasermaterials.com/ Available at: https://www.advancedlasermaterials.com/blog/ (Accessed on 29 June 2020).
Disclaimer: The views expressed here are those of the author expressed in their private capacity and do not necessarily represent the views of AZoM.com Limited T/A AZoNetwork the owner and operator of this website. This disclaimer forms part of the Terms and conditions of use of this website.