Key Issues
- Quick, on-line data acquisition for real-time process control
- Monitoring of abrasive, high-temperature materials
- Fiber optic coupling allows remote sampling to prevent damage to the instrument by TiO2 dust
- Feedback control of the reactor
Introduction
Titanium dioxide (TiO2) is a popular whitening additive, used in countless white colored commercial products such as paper, plastics, toothpaste, fabrics, and paint.
When it is prepared as a powder of microscopic crystals, TiO2 is an exceptionally potent whitener. The size of the crystals, coupled with their high refractive index, ensures that visible light is scattered efficiently. It also provides a wide dynamic range, delivering necessary sensitivity, as low as 100 ppm for key components.
Reaction Summary
The worldwide annual production of TiO2 currently amounts to millions of tons. A large portion of this TiO2 is produced via the rotary kiln process. Essentially, a kiln reactor is a large, slowly rotating cylinder supported at a slight incline. Kiln reactors are generally around 60 m long x 5 m diameter.
A powerful gas flame burner is fitted inside the lower end of the furnace, creating a thermal gradient that peaks at the lower end of the furnace – commonly close to 1050 °C.
The kiln feed is made up of a titanium oxide slurry, produced by dissolving either ilmenite ore or blast furnace slag or in sulfuric acid before hydrolyzing the result.
This titanium oxide slurry is introduced in a continuous feed, at the top of the furnace. The kiln’s rotary motion and inclination causes the slurry to steadily progress down the inner wall, being slowly ‘roasted’ at progressively higher temperatures. TiO2 product eventually drops out of the bottom of the kiln.
It normally takes around 12 hours for material to pass through the entire kiln. During this time, three processes will take place sequentially: drying, residual acid removal and calcination.
At the beginning, the oxide exists in a crystal form known as anatase. In the kiln’s hottest region, most of this will be converted into the rutile crystal phase. The end product – which consists of a mixture of these two phases continuously drops out of the kiln’s lower end.
After exiting the kiln, this is subsequently processed to form ultra-fine pigment powder. The ratio of rutile to anatase is a critical measure of product quality, due to its correlation with durability and whiteness.
Process Control
The aim of process control is to produce a consistent product while maintaining maximum throughput. It is very difficult to achieve good control of the kiln because of the process’s inherent complexities, but an advanced control model has been developed which is capable of varying the gas feed rate to the burner.
Historically, slow data sampling rates have limited the ability to use this control package. This was because previous methods were based on x-ray diffraction, which needed prolonged sample preparation, and even then lacked the level of accuracy required.
Before good control could become a reality, sampling rates had to be increased by an order of magnitude. The only clear means of achieving this combination of precision and speed was through the use of Raman spectroscopy (Figure 1).
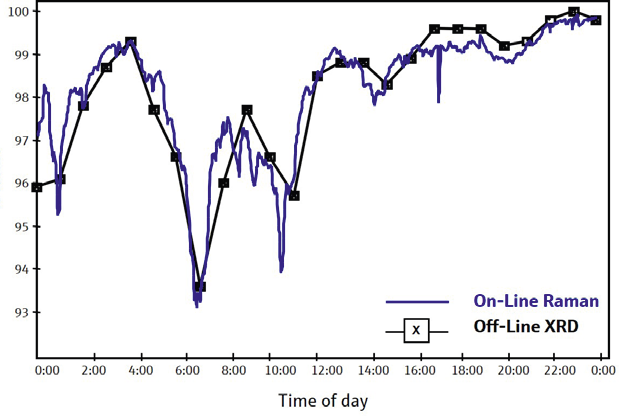
Figure 1. The short data acquisition time of Raman spectroscopy allows real-time process control. Compare the level of detail in data from the on-line Raman spectrometer to that from the off-line x-ray diffractometer (XRD). Image Credit: Kaiser Optical Systems, Inc.
Raman Monitoring
By using a Kaiser Raman analyzer with a filtered fiber optic probe head, it is now possible to control the kiln process in real time. Titanium dioxide crystals’ extreme hardness and small size make them highly pervasive, potentially damaging even the most hardened instrumentation.
To address this issue, each spectrometer is operated in a sealed enclosure, which is remote from the kiln. Fiber links of 50-100 meters in length are used to connect the spectrometer to the measurement probes located on each kiln.
Rather than view this process directly using a Raman probe, an automated sampling system was used instead. A screw feed mechanism continuously collects a small amount of product at the kiln output, pushing it across the Raman probe head’s focus. Because TiO2 produces strong Raman signals, it is possible to acquire spectra in mere seconds.
The probe head’s small sampling volume (around 50 μm diameter), coupled with the heterogeneous nature of the sample means that it is important to make measurements on a statistically representative volume of material. Therefore, spectra are obtained and averaged over a three-minute period, for each individual measurement.
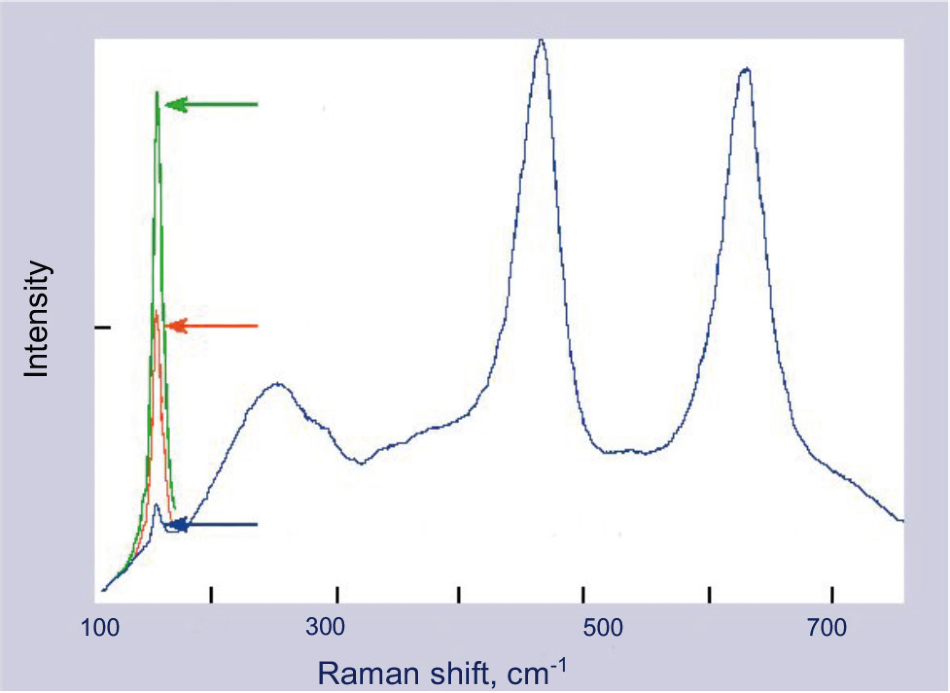
Figure 2. The percent anatase can be directly determined from the area of the characteristic peak at 142 cm–1. Image Credit: Kaiser Optical Systems, Inc.
Figure 2 shows the Raman spectra of the two phases, which are sharp and distinct,1,2,3 thus allowing simple peak areas to be used to derive concentrations, following correction to account for sample temperature. For each individual kiln, the rutile/anatase ratio derived from these peak measurements is then passed directly to the kiln controller, facilitating a genuine closed-loop operation.
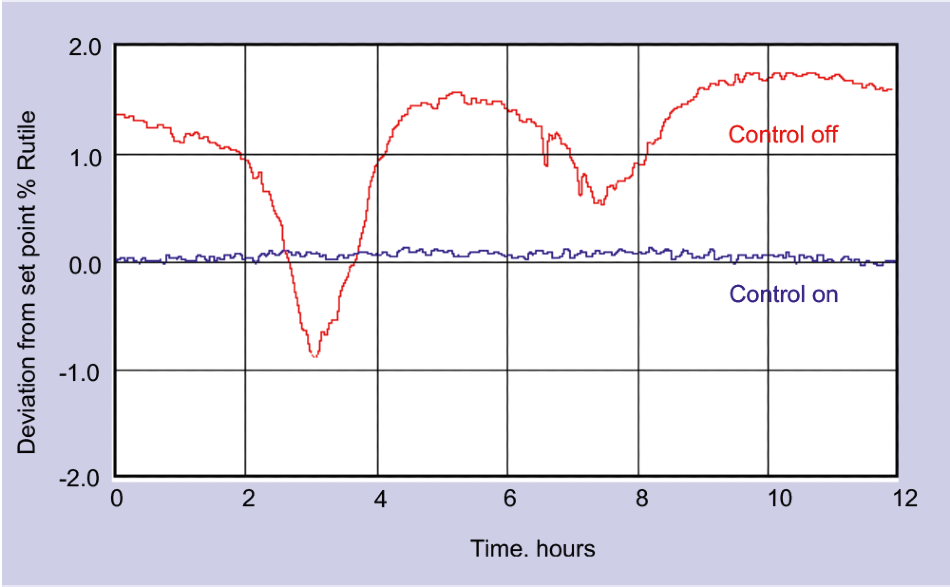
Figure 3. The short response time of Raman sampling enables much tighter process control than was possible using traditional (2 per hour) automated at-line analysis. Image Credit: Kaiser Optical Systems, Inc.
Improvement in Control
Figure 3 displays the level of control attained using real-time testing, in comparison with that of conventional at-line testing. As well as maintaining the required rutile/anatase ratio, real-time control is able to enhance the process’s general stability while also providing other quality benefits.
The most noticeable gain however, was a clear increase in productivity. When a chemical process can be run under steady control, that process is then much more suitable for running at higher throughput.
Additionally, the improved consistency as a result of this new approach delivered benefits at every subsequent stage of the process. While the exact figure is proprietary, the value of this ‘extra’ product is highly significant, confirming that Raman spectroscopy has great potential as a process control tool.1,2,3
References
- King, B.; Clegg, I; Everall, N., “Increasing TiO2 production by closed-loop Raman,” Raman Review, Fall 1999.
- Iida, Y.; Furukawa, M; Aoki, T.; Sakai, T., “Raman spectrum of ultrafine anatase powders derived from hydrolysis of alkoxide,” Applied Spectroscopy, Vol. 52, 1998, 673.
- Lewis, I.R. Process Raman Spectroscopy. In Handbook of Raman Spectroscopy; Lewis, I.R., Edwards, H.G.M., Eds. Marcel Dekker: New York, 2001; pp. 41–144
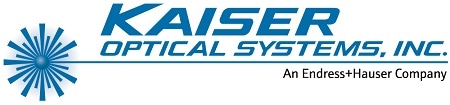
This information has been sourced, reviewed and adapted from materials provided by Kaiser Optical Systems, Inc..
For more information on this source, please visit Kaiser Optical Systems, Inc..