.jpg)
In this interview AZoM talks to Rohit Ramnath, Senior Product Engineer from Master Bond, about how to manage stresses caused by CTE mismatches in adhesive applications.
What types of adhesives should you select for bonding substrates with different coefficients of thermal expansion (CTE)?
There are two schools of thought when it comes to bonding materials with different coefficients of thermal expansion. The first is to select adhesives with CTEs as close as possible to the materials being bonded. The second is to provide for more flexible or toughened adhesives to compensate for the mismatches. The decision is not always very clear cut and it also depends on various factors including but not limited to the substrates being bonded, the service temperature range, and the thermo-mechanical stresses involved.
What are some examples of substrates with different CTEs?
Common examples include bonding metals with different CTEs, metals to glass, glass to plastics, ceramics to plastics and rubbers to metals.
Stress management is critical for adhesive applications, mainly due to the possibility of a CTE mismatch between the substrates themselves, and between the substrates and the adhesive. Although this can happen in assemblies where similar substrates are being bonded, it can be further accentuated in applications involving dissimilar substrates.
What factors should be considered?
Elements such as service conditions, joint design, geometry, and processing constraints such as curing temperatures, as well as automated dispensing needs, provide a complex mix of factors to consider when selecting an appropriate candidate for such adhesive applications.
How should you select an adhesive to mitigate these differences in thermal expansion?
One approach is to select an adhesive with as low a thermal expansion coefficient as possible. For an unfilled, rigid/stiff epoxy, the CTE might hover at around 40-50 ppm/°C at room temperature. This CTE can be reduced through the use of ceramic or even through specialty negative coefficient of thermal expansion fillers, to values as low as 10 ppm/°C at room temperature. Note that by adding such fillers, the modulus increases significantly. For example, the tensile modulus of an unfilled, relatively rigid two-component epoxy can range anywhere from 350,000-450,000 psi at room temperature, but adding fillers may increase this value in some cases to around 2 to 3 times. Therefore, typically, adhesives with very low CTE’s tend to be stiffer. The chart below for EP17HTND-CCM, a low CTE epoxy, shows the stress-strain curve. EP17HTND-CCM has a high modulus and is rigid.
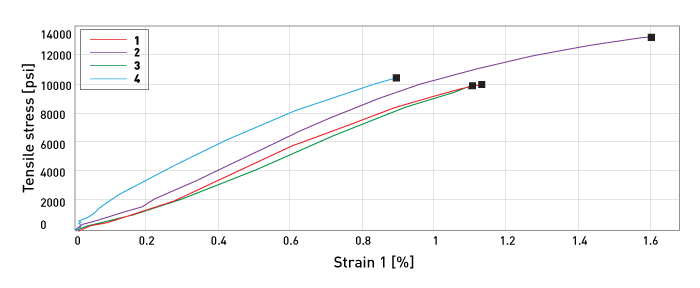
Stress-Strain Curve for Low CTE Epoxy EP17HTND-CCM
Can you comment on the flexible adhesive approach for managing the differences in thermal expansion?
The other approach to reduce stress on the bond joint is to utilize rubber toughened or “flexibilized” adhesive systems. These adhesives offer a toughened cure, and with select systems offering relatively high lap shear strength (for aluminum-aluminum bond), in excess of 1000 psi, and a tensile modulus in some cases not higher than 50,000 psi. Some of these systems also provide relatively high elongation values, ranging from 20% to 100% or even higher. Such products offer a higher thermal expansion coefficient, which could be around 80-150 ppm/°C at room temperature. The chart below shows the stress-strain curve for a higher CTE epoxy, EP40Med. EP40Med is a toughened, low modulus, high elongation epoxy.
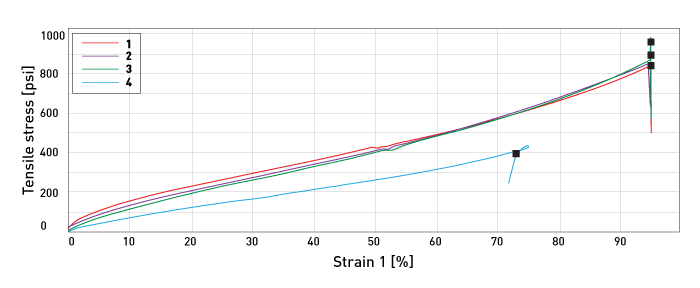
Stress-Strain Curve for Higher CTE Epoxy EP40Med
What other factors should a design engineer take into account when deciding how to best manage the stress of their application?
The engineer must weigh the benefits and tradeoffs of selecting either a flexible, low modulus adhesive system or a rigid/stiff, lower CTE product. Both types of adhesives (rigid/stiff, lower CTE & flexible / toughened, higher CTE), may be beneficial, since geometries, substrates, and the conditions can vary from application to application. It is important to look into running mock-up trials or simulations early in the selection process, by contacting adhesive suppliers to ensure not only that all the optimal processes are followed such as properly preparing the surfaces, and fully curing the adhesives according to the manufacturer’s recommendations, but also that the correct mechanical property estimates/ranges are used.
About Rohit Ramnath
Rohit Ramnath is a Senior Product Engineer for Master Bond Inc., a custom formulated adhesives manufacturer. He analyzes application oriented issues and provides product solutions for companies in the aerospace, electronics, medical, optical and oil/chemical industries. He graduated from Carnegie Mellon University with a Masters Degree in Chemical Engineering.
.jpg)
Disclaimer: The views expressed here are those of the interviewee and do not necessarily represent the views of AZoM.com Limited (T/A) AZoNetwork, the owner and operator of this website. This disclaimer forms part of the Terms and Conditions of use of this website.