Printer toner particles’ size and shape have the potential to significantly affect a printer’s image resolution and efficiency. The consistency of these particles can also impact overall image quality because their consistency influences the distribution of charge that the particles hold.
Image characterization can be used to ascertain the size, shape, circularity, and material uniformity of printer toner particles, both before and following production (Figure 1).
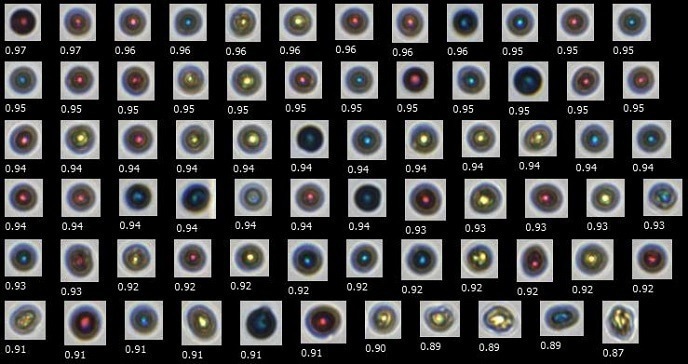
Figure 1. Color printer toner particles imaged by FlowCam. Circularity value is shown beneath each image. Particles are shown in order of decreasing circularity, where 1.00 is a perfect circle. Image Credit: Yokogawa Fluid Imaging Technologies, Inc.
This case study examines the use of Yokogawa Fluid Imaging Technologies’ FlowCam flow imaging microscope and VisualSpreadsheet® image analysis software to efficiently characterize printer toner in a quality control application.
FlowCam Analysis
Before analysis via FlowCam, a sample of printer toner was mixed with deionized water to create an aqueous slurry. Next, this slurry was fed into the FlowCam’s sample port, which was drawn through the flow cell. The instrument was then used to capture an image of each printer toner particle.
Next, FlowCam's VisualSpreadsheet software was employed to compile a collage of every particle image from the sample run. Using these images, the software could record over 40 morphological properties of the particles.
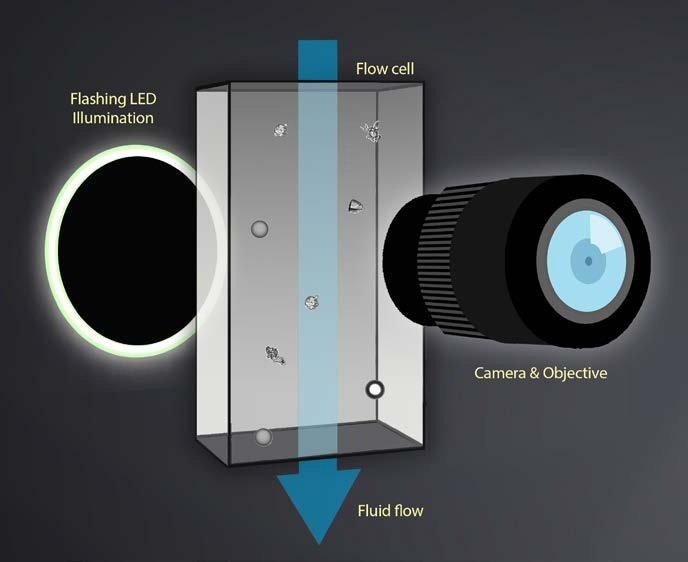
Figure 2. Flow path and optical components of the FlowCam system. Image Credit: Yokogawa Fluid Imaging Technologies, Inc.
The software associated each collected particle image with an ID number and correlated particle property values. This data can be exported from VisualSpreadsheet into CSV format, allowing additional data manipulation and analysis in the user’s package of choice (Table 1 and Figure 3).
To facilitate proper quality control, a software filter was generated in VisualSpreadsheet to determine which printer toner images met the predefined quality parameters and which did not.
This specific filter specified an acceptable Equivalent Spherical Diameter (ESD) of 4 μm to 8 μm, and an allowed Circularity of 0.80 to 1.00, whereby 1.00 represents a perfect circle or sphere.
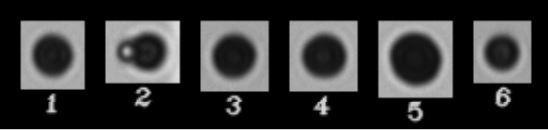
Figure 3. Black printer toner particles imaged by FlowCam. The particle ID number is shown beneath each image and correlates with the data in Table 1. Image Credit: Yokogawa Fluid Imaging Technologies, Inc.
Particle ID |
Diameter ESD (µm) |
Circularity |
1 |
6.25 |
1.00 |
2 |
6.62 |
0.89 |
3 |
6.62 |
0.96 |
4 |
6.62 |
0.94 |
5 |
7.91 |
0.97 |
6 |
5.18 |
1.00 |
Table 1. Exported diameter and circularity data for particles in Figure 3. Any and all particle properties can be selected for export to a CSV file format from VisualSpreadsheet. Source: Yokogawa Fluid Imaging Technologies, Inc.
The images, and data were sorted to calculate the percentage of particles that met the specified parameters, and a useful Summary Statistics table was generated to highlight the selected particle properties.
This table updates automatically as the sample is run, meaning that users can rapidly evaluate the quality of their samples in real-time. Table 2 displays the final statistics from the run.
Table 2. Summary Statistics calculated by VisualSpreadsheet from a single run of printer toner. A software filter was applied to this run to include particles with Circularity values between 0.80 and 1.00, and Diameter (ESD) ranging from 4.00 μm to 8.00 μm. Summary statistics are calculated in real-time to reflect the analysis. Source: Yokogawa Fluid Imaging Technologies, Inc.
Summary Stats |
Mean |
Minimum |
Maximum |
Std. Dev. |
% CV |
Circularity |
0.93 |
0.80 |
1.00 |
0.04 |
4.18 |
Diameter (ESD) |
5.86 |
4.00 |
8.00 |
0.97 |
16.40 |
Summary and Conclusions
This case study highlighted the capacity of image analysis enabled by flow imaging microscopy to measure particle circularity. This critical measurement parameter represents a fundamental property in terms of quality control analysis in printer toner manufacturing.
While a range of other high-volume particle analysis techniques can determine particle size, these techniques tend to assume that all particles are spheres. This means that they enable particle shape analysis and are much less suited to printer toner analysis.
FlowCam’s potential to enable particle size and shape monitoring is highly advantageous in quality control processes, such as those employed by printer toner manufacturers.
Implementing a robust QA/QC filter can help assess the overall quality of every analyzed sample.
FlowCam is suitable for use in a diverse array of applications that require rapid, quantitative results. The instrument’s intuitive design allows an operator to perform comprehensive on-site product testing with conformational data, statistics, and reporting.
Acknowledgments
Produced from materials originally authored by Yokogawa Fluid Imaging Technologies, Inc.
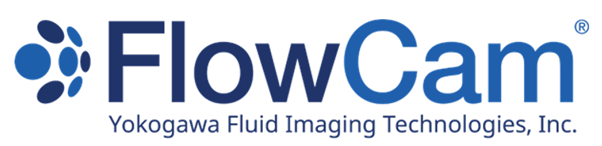
This information has been sourced, reviewed and adapted from materials provided by Yokogawa Fluid Imaging Technologies, Inc.
For more information on this source, please visit Yokogawa Fluid Imaging Technologies, Inc.