Particles come in many shapes and sizes; thus, being able to analyze particles in food and beverage ingredients and correctly characterize them is important, as they can have a significant effect on the taste, appearance, stability, and processability of the final product.
CP Kelco, a prominent producer of specialized hydrocolloids headquartered in San Diego, offers various texturizing and stabilizing ingredients for food processors. To ensure top-notch product quality, they employ Flow Imaging Microscopy (FIM) to swiftly and effectively detect particle variations.
Ross Clark, a Distinguished Research Fellow at CP Kelco, enjoys the freedom to explore solutions to challenging problems and follow hunches in his enviable position. One such hunch about particle behavior in a customer’s powder eductor motivated him to conduct further investigations.
For the materials in question, operators had already effectively adjusted airflow to resolve occasional powder-flow blockages. Meeting product quality specifications was never at risk. No one even thought there was a problem. Yet Clark suspected that particle shape variation from batch to batch was causing some amount of variability.
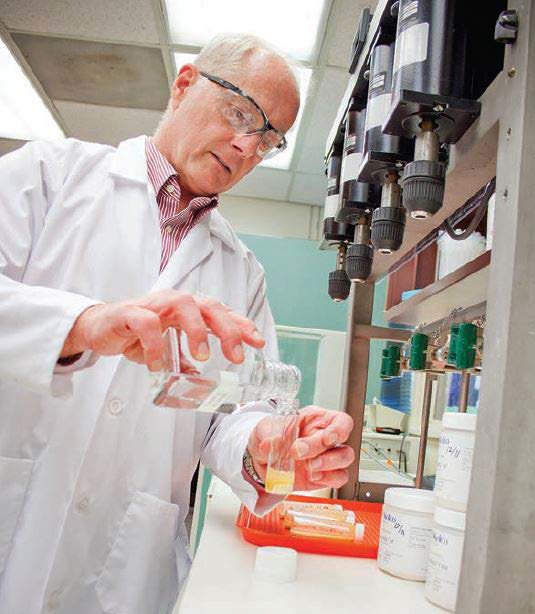
Ross Clark. Image Credit: Yokogawa Fluid Imaging Technologies, Inc
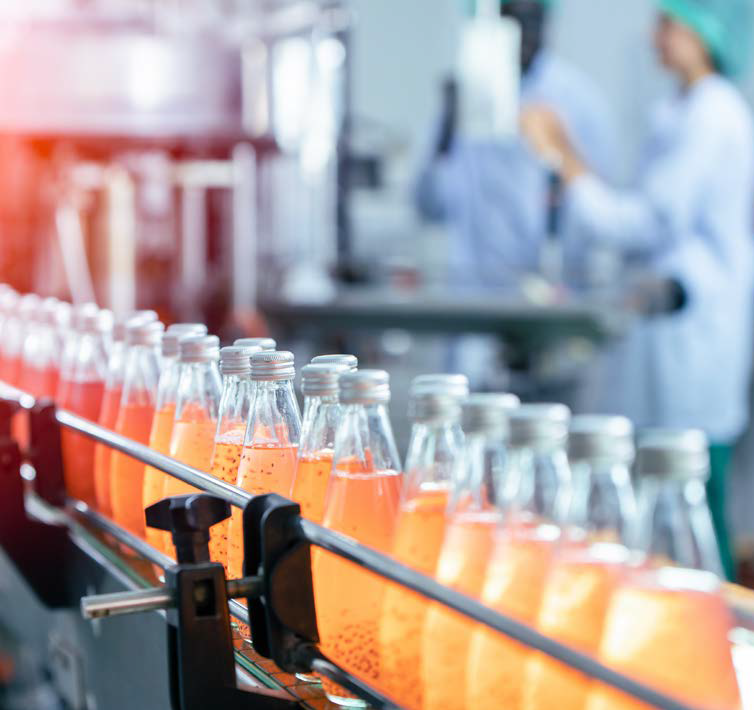
Image Credit: Yokogawa Fluid Imaging Technologies, Inc
Finding a Better Method
In search of a superior method to compare individual particle shapes, Clark considered studying laboratory samples using a microscope.
This approach was time-consuming and involved setting up slides, making it difficult to view particles accurately due to overlap and alteration of their original shapes. The reliance on human judgment was another concern, as it hindered the acquisition of statistically significant samples.
Manual microscopy was just too cumbersome and slow. It was difficult to see more than a handful of particles, certainly not enough to get a statistically significant sample.
Ross Clark, Distinguished Research Fellow, CP Kelco
At a rheology trade fair, he found a way to improve the process. “When I saw the FlowCam, I thought, ‘This is so cool!’ Now, I can get 10,000 images of individual particles in less than a minute.”
The Tools of a Detective
FlowCam, a flow imaging microscope, has been intentionally designed to detect particles and cells within samples. The system captures high-resolution digital images of each particle passing through a flow cell, saving both images and measurement data for subsequent review and analysis.
By integrating the rapidity of flow cytometers with microscopy’s visual capabilities, the system images thousands of particles in seconds while measuring over 40 diverse particle properties. These measurements range from basic size assessments to advanced morphology, such as circle fit, elongation, perimeter, and roughness.
Through the utilization of FlowCam, Clark swiftly validated his suspicion regarding the impact of particle morphology on powder flow.
While the product satisfied all required specifications, the conventional screening method for measuring particle size failed to account for individual particle shapes, resulting in variations in shape despite meeting size requirements.
This is significant as pneumatically conveyed particles of different shapes exhibit distinct flow behaviors. For instance, a spherical or irregularly shaped particle behaves differently in an airstream compared to a flat or square particle like a crystal.
Seeing digital images of individual particles with FlowCam provided the documentation I needed to prove what was happening.
Ross Clark, Distinguished Research Fellow, CP Kelco
Further Steps Taken
Clark employed FlowCam to compare the size and shape of xanthan gum samples produced at two different plants. Although batches from both facilities met screen-size specifications and appeared identical, customers experienced performance variations from one batch to the next.
By imaging thousands of particles from each location, minor differences in particle size distribution were identified, documented, and addressed. While mesh screens set a limit on particle size, they may not account for very small particles and dust.
“FlowCam has advanced measurement technology beyond what people are used to measuring,” Clark says, “so the metrics people have traditionally used to assess quality are probably outdated for most manufacturers, especially for those offering products where particle characterization is as important as it is for gums.”
CP Kelco products like xanthan gum and guar gum are employed to provide thickening, stabilizing, suspending, texturizing, and other properties to foods, beverages, chemicals, pharmaceuticals, and personal care products.
The meticulous formulation, production, and packaging of these products are crucial in meeting requirements for dispersibility, hydration rate, powder flow, and other key performance attributes. Individual particle size and shape play a pivotal role in these aspects.
Similarly, agglomerated particles and blends such as pectin blended with sugar demand compatible particle sizes to ensure they remain locked together. If they become separated, the required characteristics are not being delivered.
“The worst part of a particle size or shape issue is that it probably never occurs to the processor to check gum particle size or shape or that of any other ingredient. Instead, the recipe or the machinery are blamed,” says Clark.
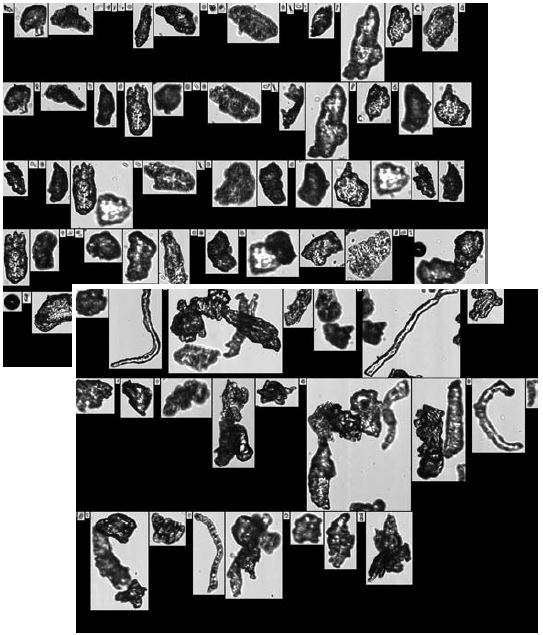
Xanthan gum and cellulose gum particles, as imaged by FlowCam. Image Credit: Yokogawa Fluid Imaging Technologies, Inc
The Power of Images
Clark usually distributes particle images to customers, distributors, and colleagues worldwide via email. Seeing actual images on screen after years of working with these products in formulation, manufacturing, or packaging projects causes quite a reaction.
Most particle analyzers base their measurements on an idealized model where every particle must be considered a round sphere. The FlowCam...bases its measurements on the actual size and shape of the particle.
Ross Clark, Distinguished Research Fellow, CP Kelco

This information has been sourced, reviewed and adapted from materials provided by Yokogawa Fluid Imaging Technologies, Inc..
For more information on this source, please visit Yokogawa Fluid Imaging Technologies, Inc.