Over the past few decades, composite materials have become increasingly prevalent in the manufacture of aerostructures. This recent trend is primarily driven by factors such as toughness performance, fuel efficiency, and carbon emission reductions. Design engineers are steadily moving away from the use of more traditional metal structures, preferring those made from composites.
Glass and carbon fiber reinforced composites are highly regarded for their high strength, stiffness, and lightweight. As such, they are used in a wide range of applications requiring a combination of structural high performance and relatively low weight. While high-performance composites do exist, their toughness, cure flexibility, and processing potential still leave much room for improvement.
Systems are available that can provide high toughness composites, but these suffer from poor hot/wet performance, particularly at higher service temperature ranges (>82 °C/180 °F).
Furthermore, many toughened epoxy systems are unsuitable for processing (either OOA/VBO or autoclave), instead of requiring cure flexibility (from 135 °C to 180 °C) to deliver comparable mechanical properties.
Throughout the industry, a wide range of approaches is being used to create toughened prepregs. Highly toughened resins can be created by using toughening agents (for example, thermoplastics, and rubbers), improved fiber/resin compatibility, or approaches involving the use of homogeneous and heterogeneous resin mixtures.
One of the more common approaches to manufacturing highly impact-resistant laminates involves the development of an extremely tough, strong interlayer between fiber plies. It is commonly understood that the interply toughness should be improved or at least different from the intraply (fiber bundles) toughness, to ensure the prevention of crack propagation after impact.
This article explores the performance of the TC380 system. It evaluates this with Toray T800GC 24K 150 gsm fibers, which include 35% resin content. This content was confirmed after processing and curing in an out-of-autoclave condition at 135 °C (275 °F) for 6 hours, 150 °C (300 °F) for 4 hours, and 180 °C (356 °F) for 2 hours.
Composite performance of each of these three different cure profiles was assessed on laminate quality following C-scan inspection. Their mechanical properties were also assessed using various tools including CAI, G₁C, G₂C, OHC, and OHT. The TC380 system’s exothermic behavior was examined to ascertain whether or not runaway exotherm had the potential to damage thick parts made from it.
A 91-ply fabricated wing spar with a variety of ply drops was prepared to investigate an OOA-process TC380 system’s performance when creating intricate geometric shapes.
Experiment
Numerous experiments were performed in order to thoroughly evaluate the TC380 toughened resin system. The primary material utilized in this experiment was UD tape T800GC 24K 150 gsm with 35% resin content, but additional results are also included for TC380 resin on HTS40 3K 2x2 twill fabric 192 gsm with 42% resin content.
The fabric-toughened system and UD tape were produced at Toray Advanced Composites (formerly TCAC), which is based in Morgan Hill, California.
Lamination and Mechanical Testing
Initially, TC380 resin mixes were comprehensively degassed to reduce the possibility of trapped air. The vacuum level was maintained at a level of at least 27 inHg throughout resin mixing in order to ensure proper degassing at mixing temperatures.
Unidirectional prepreg was created using T800GC 24K carbon fiber with TC380 resin, and this was cured at three different curing temperatures to properly compare its mechanical properties.
A proprietary film and calendaring methodology were used to produce prepregs that were optimized for OOA processing. Validation of the prepreg’s appearance and quality was undertaken using resin content, resin flow, FAW, and volatile tests.
Prepregs were cut and hand laid-up before being OOA cured. Laminates created for each mechanical test followed guidelines laid out in the appropriate ASTM test method. Appropriate debulking prior to curing OOA laminates is a central factor in ensuring high laminate quality.
Prepregs were debulked for 15 minutes, every four plies, until all required plies were ready. Vacuum continued to be maintained at a minimum of 27 inHg. Furthermore, a ply of porous Teflon-coated glass (TX1040) was utilized to assist in trapped air removal – this was replaced every two or three debulk cycles.
The fundamental cure cycle employed in the fabrication of mechanical test laminates was as follows:
- Apply vacuum (minimum 27 inHg)
- Hold vacuum for 4 hours at room temperature
- Heat at 0.6 °C (1 °F)/min to 107 °C ±3 °C (225 °F ± 5 °F)
- Hold at 107 °C ±3 °C (225 °F ±5 °F) for 1 hour
- Heat at 0.6 °C (1 °F)/min to 180 °C ±3 °C (356 °F ± 5 °F)
- Hold at 180 °C ±3 °C (356 °F ±5 °F) for 2 hours
- Cool at 3 °C to 4 °C (5 °F to 7 °F)/min to below 60 °C (140 °F)
Several thermocouple wires were used in the monitoring and recording of temperatures, while a vacuum sensor was used to observe vacuum levels throughout the curing process. Cured laminates were also C-scanned to evaluate the OOA cure process’s overall quality.
C-scan results were assessed, and these were amplified by cross-sectioning where this was deemed necessary. A diamond saw was used to wet cut mechanical test specimens to sizes specified by the ASTM method in question, and following machining, specimens were dried at 100 °C (212 °F) for a 1 hour period.
Specimens were kept at 21 °C ± 6 °C (70 °F ±10 °F) after drying, and these were desiccated until tested. Following drying, wet specimens were conditioned via water immersion at 71 °C (160 °F) for a 14 day period. All specimens were tested within 30 minutes of being removed from conditioning.
Testing of all laminate samples was done in line with ASTM test methods (Table 1). A total of five specimens were tested, with averages reported and evaluated for each individual test and condition. These included:
- 180 °C cure specimens ETW and ETD were tested at 121 °C.
- 135 °C cure specimens ETW and ETD were tested at an 82 °C chamber temperature.
- 150°C cure specimens ETW and ETD were tested at both temperature conditions because wet Tg (after 14 days of water conditioning) was found to withstand at the 121 °C test temperature.
Table 1. Test Methods Used. Source: Toray Advanced Composites
Test Panel |
Test Method |
Tensile Strength & Modulus |
ASTM 3039 |
Compression Strength & Modulus |
ASTM D 695 |
Compression Combined Loading Test (CCLT) |
ASTM D 6641 |
Short Beam Shear |
ASTM D2344 |
Flexural Strength & Modulus |
ASTM D 790 |
In-Plane Shear Strength & Modulus |
ASTM D 3518 |
Open-Hole Tensile Strength (OHT) |
ASTM D 5766 |
Open-Hole Compression Strength (OHC) |
ASTM D 6484 |
Compression After Impact test (CAI) |
ASTM D 7136/7137 |
Interlaminar Fracture Toughness Mode 1 (G1C) |
D6-83079-131 |
Interlaminar Fracture Toughness Mode 2 (G2C) |
D6-83079-132 |
Analysis of Laminate
All laminates were analyzed using the following methods:
Ultrasonic Non-Destructive Inspection
C-scan was used to analyze composite laminates, while laminate quality was measured using amplitude, B-scan, thickness, and amplitude histograms. An NDT automation ultrasonic immersion scanner was employed alongside U-Twin software for data analysis. Every laminate was inspected after curing via pulse echo fitted with a 5 MHz transducer.
Microscopy
Cross-sectional samples were potted and cured before microscope inspection took place. Samples were then polished with an Ecomet 4000 variable speed grinder-polisher from Buehler – specifically using a polycrystalline diamond polishing medium solution with 9 to 0.05-micron particle sizes.
An Olympus BHT digital camera was used to capture images at magnifications noted in the figures. Additionally, the void percentage in each sample was assessed using an Image J software analyzer.
Fiber Volume by Acid Digestion
Acid digestion was undertaken using a Mars Machine from CEM Corporation. Samples were inserted into a plastic vessel along with 40 ml of concentrated nitric acid before being run through a pre-programmed digestion cycle.
Degree of Cure Study by DSC
The degree of cure was confirmed with a TA Instruments DSC Q20 using a heat rate of 10 °C/min. Various cure profiles were completed in order to establish the system’s optimum cure.
Part Fabrication Demonstration
A 91-ply demonstration wing spar section possessing variable cross-sectional thicknesses was created using the consolidation, lay-up techniques, and cure cycles outlined area. After it had been fabricated, the part was sectioned before determining its void content at various locations.
Thermal Stability
TC380’s thermal stability was evaluated from 100 plies to 800 plies. This involved plies being cut in the 0° orientation before being sequentially debulked in sets of five. Thermocouples were inserted in between layers during the consolidation and laminate forming steps, allowing for temperature measurements inside different areas of the laminate.
The thermocouples’ temperature readings were then plotted and evaluated to look for temperature spikes or exothermic reactions. Laminates were laid-up as previously described, before being cured at 180 °C (356 °F) for 2 hours.
Results
The goal of this process was the development of an extremely toughened prepreg system, displaying both a balance of properties and comparable mechanical properties at various curing temperatures and cure profiles in both VBO/OOA and autoclave processes. The results of evaluations on various composite laminates are outlined below.
Laminates were processed under three different cure cycles at RTD, ETD, and ETW. Mechanical properties for laminates are provided under each of these cycles, as well as for fabric impregnated with TC380. Lastly, the final outcome of TC380 constructed to a thick-section aerostructure is also displayed.
Composite Mechanical Properties
Tests were undertaken on all properties at different conditions. UD tape results were normalized to 60% fiber volume and fabric data was normalized at 55%, except for properties that were resin dominated. It was observed that all failure modes were good and acceptable during the test. The tables and figures presented below detail the results of this set of experiments.
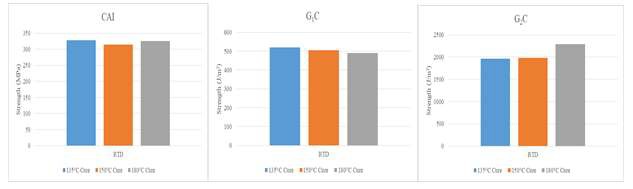
Figure 1. Comparison of CAI, G₁C, and G₂C RTD mechanical strength. Image Credit: Toray Advanced Composites
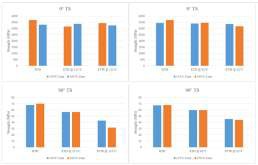
Figure 2. Comparison of tensile strength. Image Credit: Toray Advanced Composites
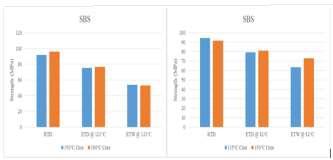
Figure 3. Comparison of SBS. Image Credit: Toray Advanced Composites
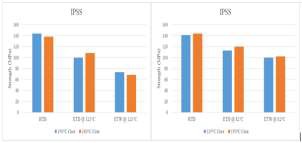
Figure 4. Comparison of shear strength. Image Credit: Toray Advanced Composites
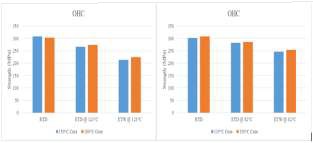
Figure 5. Comparison of OHC. Image Credit: Toray Advanced Composites
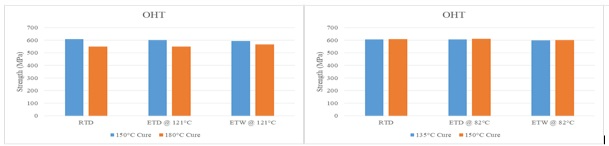
Figure 6. Comparison of OHT. Image Credit: Toray Advanced Composites
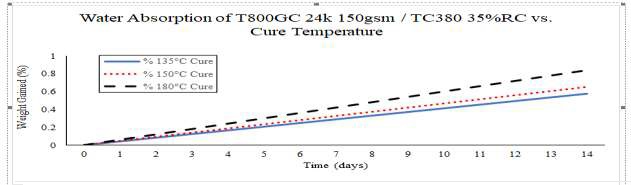
Figure 7. Water absorption of composite with three different cures. Image Credit: Toray Advanced Composites
Here, three 2x2" specimens were conditioned for 14 days at 71 °C (160 °F). Water absorption percent averages were reported for all cure cycles. Eq. 1 displays the formula used to calculate water absorption percentage.
Equation 1. Water Absorption (%)

where;
W1- dry weight of specimen W2= wet weight of specimen after 14 days of conditioning
Table 2. T800GC 24K 150 gsm/TC380 35% RC 180 °C OOA Cure. Source: Toray Advanced Composites
Mechanical Properties |
180 C° cure – 121 C° H/W |
Units |
RTD |
ETD |
ETW |
SBS at 0° |
MPa (ksi) |
96.1 (13.9) |
76.6 (11.1) |
52.9 (7.67) |
Flex Strength at 0° 16 plies |
MPa (ksi) |
1503 (218) |
1090 (158) |
883 (128) |
Flex Modulus at 0° 16 plies |
GPa (Msi) |
117 (17.0) |
108 (15.7) |
99.2 (14.4) |
Flex Strength at 0° 8 plies |
MPa (ksi) |
1883 (273) |
1276 (185) |
1069 (155) |
Flex Modulus at 0° 8 plies |
GPa (Msi) |
121 (17.6) |
106 (15.4) |
99.2 (14.4) |
CS695 at 0° |
MPa (ksi) |
1193 (173) |
1090 (158) |
1048 (152) |
CM695 at 0° |
GPa (Msi) |
150 (21.7) |
254 (22.4) |
143 (20.8) |
CS695 90° |
MPa (ksi) |
230 (33.3) |
183 (26.6) |
138 (20.0) |
CM695 at 90° |
GPa (Msi) |
8.34 (1.21) |
8.20 (1.19) |
8.13 (1.18) |
CS6641 back out to 0° properties |
MPa (ksi) |
1621 (235) |
1462 (212) |
1359 (197) |
UNC Strength QI |
MPa (ksi) |
639 (92.7) |
564 (81.8) |
446 (64.7) |
UNC Modulus QI |
GPa (Msi) |
54.7 (7.93) |
54.4 (7.89) |
54.3 (7.87) |
Tensile Strength at 0° |
MPa (ksi) |
3297 (478) |
3366 (488) |
3248 (471) |
Tensile Modulus at 0° |
GPa (Msi) |
172 (24.9) |
191 (27.7) |
187 (27.2) |
Poisson’s Ratio |
|
0.440 |
|
|
Tensile Strength at 90° |
MPa (ksi) |
70.3 (10.2) |
56.8 (8.24) |
31.7 (4.60) |
Tensile Modulus at 90° |
GPa (Msi) |
8.13 (1.18) |
6.48 (0.940) |
5.79 (0.840) |
In-Plane Shear Strength Ultimate |
MPa (ksi) |
138 (20.0) |
108 (15.6) |
68.3 (9.90) |
In-Plane Shear Modulus |
GPa (Msi) |
3.78 (0.490) |
2.76 (0.400) |
2.07 (0.300) |
V-Notch Shear Strength 0.5% offset |
MPa (ksi) |
59.2 (8.59) |
48.7 (7.06) |
36.8 (5.33) |
V-Notch Shear Modulus 0.5% offset |
GPa (Msi) |
3.86 (0.560) |
3.24 (0.470) |
2.83 (0.410) |
Open-Hole Compression Strength |
MPa (ksi) |
303 (44.0) |
274 (39.7) |
224 (32.5) |
Open-Hole Tensile Strength |
MPa (ksi) |
550 (79.8) |
550 (79.8) |
567 (82.2) |
Filled-Hole Tensile Strength |
MPa (ksi) |
562 (81.5) |
|
|
CAI (6.7 J/mm, 1500 in-lb/in impact) |
MPa (ksi) |
326 (47.3) |
|
|
G1C |
490 J/m2 (2.80 in-lb/in2) |
G2C |
2291 J/m2 (13.1 in-lb/in2) |
TG by DMA |
C° |
Dry – 202.86; Wet – 163.94 |
Water Absorption |
% |
0.84 |
Table 3. T800GC 24K 150 gsm/TC380 35% RC 150 °C OOA Cure. Source: Toray Advanced Composites
Mechanical Properties |
150 C° cure – 121 C° H/W |
Units |
RTD |
ETD |
ETW |
SBS at 0° |
MPa (ksi) |
91.6 (13.3) |
75.2 (10.9) |
52.9 (7.67) |
Flex Strength at 0° 16 plies |
MPa (ksi) |
1538 (223) |
1207 (175) |
945 (137) |
Flex Modulus at 0° 16 plies |
GPa (Msi) |
117 (17.0) |
120 (17.4) |
112 (16.2) |
Flex Strength at 0° 8 plies |
MPa (ksi) |
1828 (265) |
1407 (204) |
1159 (168) |
Flex Modulus at 0° 8 plies |
GPa (Msi) |
130 (18.8) |
113 (16.4) |
111 (16.1) |
CS695 at 0° |
MPa (ksi) |
1234 (179) |
1000 (145) |
986 (143) |
CM695 at 0° |
GPa (Msi) |
152 (22.1) |
142 (20.6) |
144 (20.9) |
CS695 90° |
MPa (ksi) |
230 (33.3) |
184 (26.7) |
154 (22.3) |
CM695 at 90° |
GPa (Msi) |
9.58 (1.39) |
9.10 (1.32) |
9.09 (1.31) |
CS6641 back out to 0° properties |
MPa (ksi) |
1621 (235) |
1366 (198) |
1255 (182) |
UNC Strength QI |
MPa (ksi) |
592 (85.8) |
556 (80.6) |
509 (73.9) |
UNC Modulus QI |
GPa (Msi) |
58.4 (8.47) |
58.4 (8.47) |
51.9 (7.53) |
Tensile Strength at 0° |
MPa (ksi) |
3683 (534) |
3159 (458) |
3421 (496) |
Tensile Modulus at 0° |
GPa (Msi) |
172 (25.1) |
176 (25.6) |
196 (28.4) |
Poisson’s Ratio |
|
0.32 |
|
|
Tensile Strength at 90° |
MPa (ksi) |
68.0 (9.86) |
56.7 (8.22) |
42.8 (6.20) |
Tensile Modulus at 90° |
GPa (Msi) |
8.48 (1.23) |
7.03 (1.02) |
6.27 (0.91) |
In-Plane Shear Strength Ultimate |
MPa (ksi) |
144 (20.9) |
100 (14.5) |
73.1 (10.6) |
In-Plane Shear Modulus |
GPa (Msi) |
3.45 (0.500) |
2.76 (0.400) |
0.320 (2.21) |
V-Notch Shear Strength 0.5% offset |
MPa (ksi) |
57.4 (8.32) |
48.4 (7.02) |
35.7 (5.17) |
V-Notch Shear Modulus 0.5% offset |
GPa (Msi) |
4.07 (0.590) |
3.51 (0.510) |
3.03 (0.440) |
Open-Hole Compression Strength |
MPa (ksi) |
308 (44.7) |
266 (38.5) |
213 (30.9) |
Open-Hole Tensile Strength |
MPa (ksi) |
609 (88.3) |
601 (87.2) |
594 (86.1) |
Filled-Hole Tensile Strength |
MPa (ksi) |
641 (93.0) |
|
|
CAI (6.7 J/mm, 1500 in-lb/in impact) |
MPa (ksi) |
314 (45.6) |
|
|
G1C |
506 J/m2 (2.89 in-lb/in2) |
G2C |
1979 J/m2 (11.3 in-lb/in2) |
TG by DMA (C°) |
C° |
Dry – 181.14; Wet – 150.33 |
Water Absorption |
(%) |
% 0.65 |
Table 4. T800GC 24K 150 gsm/TC380 35% RC 135 °C OOA Cure. Source: Toray Advanced Composites
Mechanical Properties |
135 C° cure – 82 C° H/W |
Units |
RTD |
ETD |
ETW |
SBS at 0° |
MPa (ksi) |
94.6 (13.7) |
79.3 (11.5) |
63.3 (9.18) |
Flex Strength at 0° 16 plies |
MPa (ksi) |
1448 (210) |
1245 (180) |
1141 (165) |
Flex Modulus at 0° 16 plies |
GPa (Msi) |
116 (16.8) |
113 (16.4) |
115 (16.7) |
Flex Strength at 0° 8 plies |
MPa (ksi) |
1684 (244) |
1459 (225) |
1354 (196) |
Flex Modulus at 0° 8 plies |
GPa (Msi) |
117 (17.0) |
113 (16.4) |
117 (17.0) |
CS695 at 0° |
MPa (ksi) |
1271 (184) |
1155 (168) |
1113 (161) |
CM695 at 0° |
GPa (Msi) |
147 (21.3) |
149 (21.6) |
153 (22.2) |
CS695 90° |
MPa (ksi) |
225 (32.7) |
193 (28.0) |
168 (24.4) |
CM695 at 90° |
GPa (Msi) |
10.1 (1.46) |
9.72 (1.41) |
9.72 (1.41) |
CS6641 back out to 0° properties |
MPa (ksi) |
1627 (236) |
1554 (225) |
1391 (202) |
UNC Strength QI |
MPa (ksi) |
610 (88.5) |
537 (77.9) |
491 (71.2) |
UNC Modulus QI |
GPa (Msi) |
53.1 (7.71) |
51.7 (7.5) |
50.9 (7.39) |
Tensile Strength at 0° |
MPa (ksi) |
3440 (499) |
3391 (492) |
3349 (486) |
Tensile Modulus at 0° |
GPa (Msi) |
151 (22.0) |
179 (26.0) |
186 (27.0) |
Poisson’s Ratio |
|
0.35 |
|
|
Tensile Strength at 90° |
MPa (ksi) |
67.3 (9.76) |
59.7 (8.65) |
45.4 (6.58) |
Tensile Modulus at 90° |
GPa (Msi) |
8.20 (1.19) |
7.79 (1.13) |
6.89 (1.00) |
In-Plane Shear Strength Ultimate |
MPa (ksi) |
141 (20.4) |
113 (16.4) |
100 (14.6) |
In-Plane Shear Modulus |
GPa (Msi) |
3.65 (0.530) |
0.440 (3.03) |
2.83 (0.410) |
V-Notch Shear Strength 0.5% offset |
MPa (ksi) |
61.5 (8.92) |
50.3 (7.30) |
44.3 (6.42) |
V-Notch Shear Modulus 0.5% offset |
GPa (Msi) |
4.27 (0.620) |
3.58 (0.520) |
3.86 (0.560) |
Open-Hole Compression Strength |
MPa (ksi) |
302 (43.7) |
283 (41.0) |
247 (25.9) |
Open-Hole Tensile Strength |
MPa (ksi) |
606 (87.9) |
607 (88.0) |
599 (86.9) |
Filled-Hole Tensile Strength |
MPa (ksi) |
822 (90.2) |
|
|
CAI (6.7 J/mm, 1500 in-lb/in impact) |
MPa (ksi) |
328 (47.6) |
|
|
G1C |
520 J/m2 (2.97 in-lb/in2) |
G2C |
1968 J/m2 (11.2 in-lb/in2) |
TG by DMA |
C° |
Dry – 175.84; Wet – 145.59 |
Water Absorption |
% |
0.58 |
Table 5. T800GC 24K 150 gsm/TC380 35% RC 150 °C OOA Cure. Source: Toray Advanced Composites
Mechanical Properties |
150 C° cure – 82 C° H/W |
Units |
RTD |
ETD |
ETW |
SBS at 0° |
MPa (ksi) |
91.6 (13.3) |
80.9 (11.7) |
73.1 (10.6) |
Flex Strength at 0° 16 plies |
MPa (ksi) |
1538 (223) |
1307 (190) |
1071 (155) |
Flex Modulus at 0° 16 plies |
GPa (Msi) |
117 (17.0) |
114 (16.5) |
15.7 (10) |
Flex Strength at 0° 8 plies |
MPa (ksi) |
1828 (265) |
1560 (226) |
1301 (189) |
Flex Modulus at 0° 8 plies |
GPa (Msi) |
130 (18.8) |
115 (16.6) |
110 (16.0) |
CS695 at 0° |
MPa (ksi) |
1234 (179) |
1046 (152) |
1036 (150) |
CM695 at 0° |
GPa (Msi) |
152 (22.1) |
136 (19.8) |
138 (20.0) |
CS695 90° |
MPa (ksi) |
230 (33.3) |
188 (27.3) |
157 (22.8) |
CM695 at 90° |
GPa (Msi) |
9.58 (1.39) |
8.41 (1.22) |
8.34 (1.21) |
CS6641 back out to 0° properties |
MPa (ksi) |
1621 (235) |
1486 (215) |
1482 (214) |
UNC Strength QI |
MPa (ksi) |
592 (85.8) |
554 (80.3) |
533 (77.3) |
UNC Modulus QI |
GPa (Msi) |
58.4 (8.47) |
54.9 (7.96) |
59.3 (8.60) |
Tensile Strength at 0° |
MPa (ksi) |
3683 (534) |
3455 (501) |
3171 (460) |
Tensile Modulus at 0° |
GPa (Msi) |
172 (25.1) |
179 (26.0) |
164 (23.8) |
Poisson’s Ratio |
|
0.32 |
|
|
Tensile Strength at 90° |
MPa (ksi) |
68.0 (9.86) |
59.8 (8.67) |
44.0 (6.38) |
Tensile Modulus at 90° |
GPa (Msi) |
8.48 (1.23) |
7.03 (1.02) |
6.55 (0.95) |
In-Plane Shear Strength Ultimate |
MPa (ksi) |
144 (20.9) |
120 (17.4) |
102 (14.8) |
In-Plane Shear Modulus |
GPa (Msi) |
3.45 (0.500) |
2.83 (0.410) |
2.55 (0.370) |
V-Notch Shear Strength 0.5% offset |
MPa (ksi) |
57.4 (8.32) |
49.2 (7.13) |
42.6 (6.17) |
V-Notch Shear Modulus 0.5% offset |
GPa (Msi) |
4.07 (0.590) |
3.38 (0.490) |
3.51 (0.510) |
Open-Hole Compression Strength |
MPa (ksi) |
308 (44.7) |
286 (41.4) |
254 (36.8) |
Open-Hole Tensile Strength |
MPa (ksi) |
609 (88.3) |
611 (88.6) |
602 (87.4) |
Filled-Hole Tensile Strength |
MPa (ksi) |
641 (93.0) |
|
|
CAI (6.7 J/mm, 1500 in-lb/in impact) |
MPa (ksi) |
314 (45.6) |
|
|
G1C |
506 J/m2 (2.89 in-lb/in2) |
G2C |
1979 J/m2 (11.3 in-lb/in2) |
TG by DMA |
C° |
Dry – 181.14; Wet – 150.33 |
Water Absorption |
% |
0.65 |
Table 6. HTS40 3K 2x2 Twill, 193 gsm/TC380 42% RC 180 °C OOA Cure—122 °C Hot/Wet. Source: Toray Advanced Composites
Mechanical Properties |
180 C° cure – 2 hours |
Units |
RTD |
ETD |
ETW |
SBS at 0° |
MPa (ksi) |
73.0 (10.6) |
60.6 (8.78) |
49.3 (7.15) |
Flex Strength at 0° 14 plies |
MPa (ksi) |
1068 (155) |
859 (125) |
735 (107) |
Flex Modulus at 0° 14 plies |
GPa (Msi) |
56.8 (8.24) |
43.0 (6.23) |
40.8 (5.92) |
CS695 at 0° |
MPa (ksi) |
810 (117) |
692 (100) |
657 (95.3) |
CM695 at 0° |
GPa (Msi) |
67.0 (9.71) |
62.9 (9.12) |
62.7 (9.09) |
CS695 90° |
MPa (ksi) |
843 (122) |
741 (107) |
692 (100) |
CM695 at 90° |
GPa (Msi) |
67.7 (9.83) |
64.0 (9.28) |
61.8 (8.96) |
CS6641 @ 0° |
MPa (ksi) |
700 (101) |
595 (86.2) |
541 (78.4) |
CM6641 @ 0° |
GPa (Msi) |
73.4 (10.7) |
66.9 (9.71) |
60.8 (8.82) |
CS6641 @ 90° |
MPa (ksi) |
701 (102) |
668 (96.9) |
631 (91.6) |
CS6641 @ 90° |
MPa (ksi) |
70.8 (10.3) |
66.2 (9.61) |
59.8 (8.68) |
Tensile Strength at 0° |
MPa (ksi) |
1051 (152) |
1111 (161) |
1060 (154) |
Tensile Modulus at 0° |
GPa (Msi) |
64.0 (9.29) |
77.1 (11.2) |
70.6 (10.3) |
Tensile Strength at 90° |
MPa (ksi) |
1065 (154) |
1067 (155) |
1029 (149) |
Tensile Modulus at 90° |
GPa (Msi) |
68.2 (9.89) |
78.1 (11.3) |
74.8 (10.9) |
In-Plane Shear Strength Ultimate |
MPa (ksi) |
151 (22.0) |
105 (15.2) |
88.3 (12.8) |
In-Plane Shear Modulus T |
|
3.10 (0.45) |
2.89 (0.42) |
3.10 (0.45) |
V-Notch Shear Strength 0.5% offset |
MPa (ksi) |
57.3 (8.31) |
|
|
V-Notch Shear Modulus 0.5% offset |
GPa (Msi) |
3.10 (0.45) |
|
|
Open-Hole Compression Strength |
MPa (ksi) |
308 (44.6) |
279 (40.5) |
258 (37.4) |
Open-Hole Tensile Strength |
MPa (ksi) |
399 (57.8) |
402 (58.3) |
395 (57.2) |
Filled-Hole Tensile Strength |
MPa (ksi) |
407 (59.0) |
|
|
CAI (6.7 J/mm, 1500 in-lb/in impact) |
MPa (ksi) |
320 (46.5) |
|
|
TG by DMA |
C° |
Dry – 207; Wet – 165 |
Water Absorption |
% |
50.74 |
Table 7. HTS40 3K 2x2 Twill, 193 gsm/TC380 42% RC 135 °C OOA Cure—82 °C Hot/Wet. Source: Toray Advanced Composites
Mechanical Properties |
135 C° cure – 6 hours |
Units |
RTD |
ETD |
ETW |
SBS at 0° |
MPa (ksi) |
73.8 (10.7) |
64.0 (9.28) |
52.5 (7.61) |
Flex Strength at 0° 14 plies |
MPa (ksi) |
979 (142) |
890 (129) |
821 (119) |
Flex Modulus at 0° 14 plies |
GPa (Msi) |
40.9 (5.94) |
42.0 (6.09) |
40.8 (5.92) |
CS695 at 0° |
MPa (ksi) |
814 (118) |
724 (105) |
681 (98.8) |
CM695 at 0° |
GPa (Msi) |
62.9 (9.13) |
62.5 (9.07) |
65.5 (9.50) |
CS695 90° |
MPa (ksi) |
862 (125) |
745 (108) |
731 (106) |
CM695 at 90° |
GPa (Msi) |
65.1 (9.45) |
61.1 (8.86) |
65.5 (9.50) |
CS6641 @ 0° |
MPa (ksi) |
663 (96.1) |
606 (87.8) |
564 (81.8) |
CM6641 @ 0° |
GPa (Msi) |
58.0 (8.41) |
57.0 (8.27) |
58.8 (8.53) |
CS6641 @ 90° |
MPa (ksi) |
666 (96.6) |
620 (89.9) |
584 (84.7) |
CS6641 @ 90° |
MPa (ksi) |
56.9 (8.26) |
57.3 (8.32) |
56.2 (8.16) |
Tensile Strength at 0° |
MPa (ksi) |
1014 (147) |
1041 (151) |
1034 (150) |
Tensile Modulus at 0° |
GPa (Msi) |
66.6 (9.66) |
69.6 (10.1) |
69.6 (10.1) |
Tensile Strength at 90° |
MPa (ksi) |
952 (138) |
993 (144) |
952 (138) |
Tensile Modulus at 90° |
GPa (Msi) |
63.7 (9.24) |
67.1 (9.74) |
68.9 (10.0) |
In-Plane Shear Strength Ultimate |
MPa (ksi) |
135 (19.6) |
108 (15.7) |
95.2 (13.8) |
In-Plane Shear Modulus |
GPa (Msi) |
3.58 (0.52) |
3.10 (0.45) |
3.03 (0.44) |
V-Notch Shear Strength 0.5% offset |
MPa (ksi) |
61.3 (8.89) |
|
|
V-Notch Shear Modulus 0.5% offset |
GPa (Msi) |
3.72 (0.54) |
|
|
Open-Hole Compression Strength |
MPa (ksi) |
317 (45.9) |
285 (41.3) |
260 (37.7) |
Open-Hole Tensile Strength |
MPa (ksi) |
383 (55.5) |
395 (57.3) |
399 (57.8) |
Filled-Hole Tensile Strength |
MPa (ksi) |
392 (56.9) |
|
|
CAI (6.7 J/mm, 1500 in-lb/in impact) |
MPa (ksi) |
333 (48.3) |
|
|
TG by DMA |
C° |
Dry – 162; Wet – 148 |
Water Absorption |
% |
0.48 |
Mechanical properties including the G₁C, G₂C, and CAI values from every temperature cure profile were found to be in a similar range (Figures 1 – 5). These results demonstrated that the cure temperature range at 135 °C – 180 °C had an identical effect on the impact resistance toughness and interlaminar toughness and of the material.
Overall, there was not much difference between RTD mechanical properties between the three different cure profiles (135 °C, 150 °C, and 180 °C).
In the instance where TC380 was cured at 180 °C. Tg was found to be around 202 °C while the wet Tg was found to be 165 °C. After being cured at 150 °C and 135 °C, dry Tg values were 180 °C and 175 °C, respectively. Wet Tgs were found to be 150 °C and 145 °C, respectively. The notable difference in Tg was understood as being due to differing cure temperatures.
The laminates cured at 150 °C and 180 °C and tested at 121 °C (ETD) resulted in similar mechanical properties to those listed in Tables 2 and 3. When tested at 121 °C, the thermal resistance of the material was not found to be affected by the 150 °C or 180 °C cure temperature.
Percentages of water absorption from the 180 °C, 150 °C, and 135 °C cures were recorded as being 0.84%, 0.65%, and 0.58%, respectively. Increased moisture absorption related to higher temperature cure profiles (from 180 °C to 135 °C) resulted from the presence of higher free volume.
However, higher moisture water absorption resulting from higher free volume did not lead to deterioration of hot/wet properties. ETW mechanical properties of the 150 °C and 180 °C cures were seen to generate comparable retention to their dry values (Tables 2 and 3).
Some lower temperature and part configuration restraints – such as low-temperature resistant tooling and/or the use of synthetic foam cores – mean that it is not possible to cure epoxy prepreg systems close to 150 °C. TC380 was cured at 135 °C in order to produce good overall mechanical properties (Tables 4 and 6).
ETW mechanical properties were tested at 82 °C because of an anticipated, somewhat lower dry and wet Tg. Despite this, general mechanical properties were found to be similar to the 180 °C cured property when tested at 121 °C.
Should potential fabricators only be able to cure prepreg systems below 150 °C, this system is still able to provide excellent continuous performance at an 82 °C service temperature.
C-Scan and Void Analysis
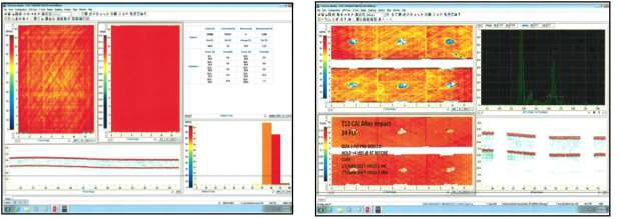
Figure 8. NDI C-scan of CAI cured laminate (180 °C/356 °F) before and after impact. Image Credit: Toray Advanced Composites
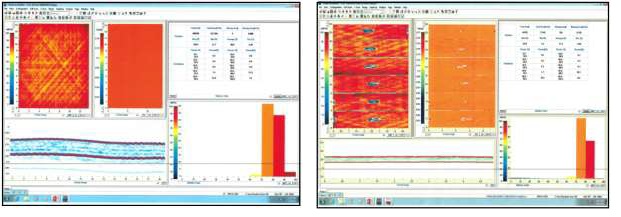
Figure 9. NDI C-scan of CAI cured laminate (150 °C/300 °F) before and after impact. Image Credit: Toray Advanced Composites
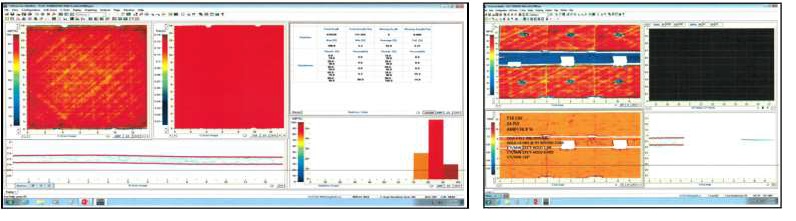
Figure 10. NDI C-scan of CAI cured laminate (135 °C/275 °F) before and after impact. Image Credit: Toray Advanced Composites
Pre-impacted CAI panels created via the OOA process were found to be uniform, possessing very few voids (Figures 8 to 10). After the impact of 6.7 J/mm (1500 in-lb/in), C-scans confirmed that impact damage was localized and did not spread through the specimens.
The system’s ability to inhibit the spread of damage irrespective of cure temperature ensures high compression after impact strengths (over 300 MPa), making this system ideal for structural applications susceptible to impact damage.
Degree of Cure
DSC was used to determine the degree of cure for each cure cycle. The total heat of the reaction was first determined by integrating the peak of uncured resin samples. Next, the residual heat of the reaction was measured by integrating the peak of a cured sample.
The residual heat of reaction was then compared to the neat resin heat of reaction in order to determine the degree of cure (Eq. 2). A higher temperature cure was found to give the least residual heat, resulting in a higher degree of cure.
Equation 2. Degree of Cure Calculation (%)

Table 8 displays the TC380 resin’s degree of cure following three different cures. Figures 11 and 12 display TC380 resin’s heat of reaction curve.
Table 8. Degree of Cure Comparison. Source: Toray Advanced Composites
Cure |
Degree of Cure (%) |
180 °C for 2 Hours |
93.52 |
150 °C for 4 Hours |
84.11 |
135 °C for 6 Hours |
78.76 |
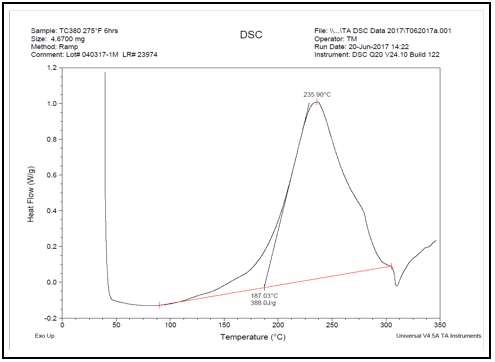
Figure 11. TC380 neat resin heat of reaction. Image Credit: Toray Advanced Composites
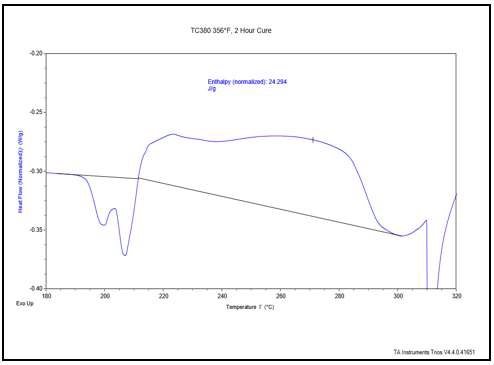
Figure 12. TC380 resin residual heat of reaction after 180 °C cure. Image Credit: Toray Advanced Composites
Thick Section Aerostructure Part Demonstration
Figures 13 illustrates configuration/void contents acquired for the 91-ply (thickest section) half wing spar, while Figure 14 shows detailed micrographs of the sectioned spar.
This particular part is 0.76 m long by 0.28 m across the edge flanges (30 " by 11 "). It uses a combination of IM7 UD tape (interior) and HTS40 fabric (outer plies), and this 91-ply half wing spar with TC380 clearly shows that intricate geometric shapes can be created with this system when using the VBO/OOA process with minimal void content.

Figure 13. TC380 91-ply wing spar image with void content in noted areas. Image Credit: Toray Advanced Composites
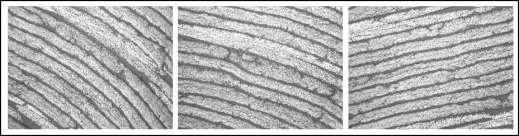
Figure 14. Microscopic cross section from Figure 11 part demonstrating very low porosity. Image Credit: Toray Advanced Composites
Thermal Stability and Exotherm Study
This study aimed to detect any violent exothermic reactions occurring during the curing of thick TC380 laminates. A temperature versus time data plot was documented using multiple thermocouples – in this study, 100, 300, 600, and 800-ply laminates were cured and examined.
Figures 15 includes images of the full range of cured laminates, while Figure 16 includes an NDI C-scan of the 100-ply laminate. Figure 17 displays cure profile graphs for all cured laminates - 0.6 °C/min to 107 °C and held for 1 hour, then 0.6 °C/min to 180 °C and held for 2 hours. It should be noted that this cure profile is identical to the standard cure profile employed in the generation of all mechanical properties cured at 180 °C.
As can be seen in Figure 17, no temperature spur was found in any graphs during the cure of all laminates. Thermocouple readings all returned similar results, irrespective of ply thickness. Following curing, all laminates were examined with no signs of exotherm detected (Figures 15 and 16).
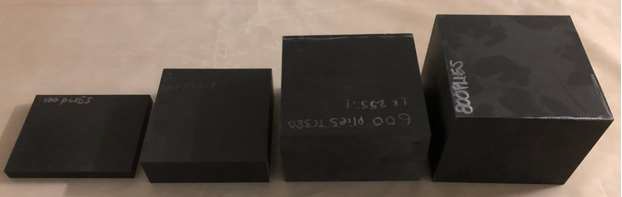
Figure 15. TC380 thick laminates (100 plies, 300 plies, 600 plies, and 800 plies). Image Credit: Toray Advanced Composites
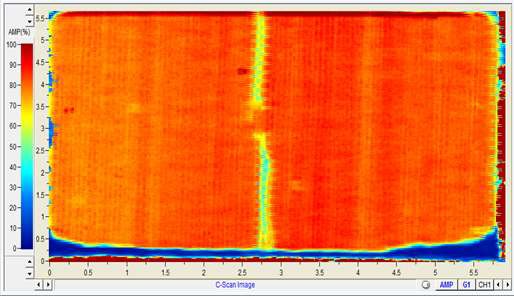
Figure 16. An ultrasonic image of a 100-ply panel shows a very low void outside of the thermocouple wires used inside the center of the laminate. Image Credit: Toray Advanced Composites
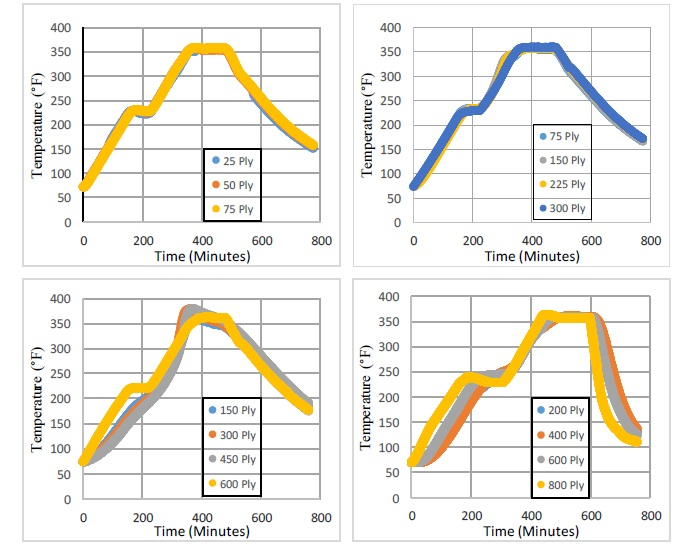
Figure 17. Plot of temperature versus time data from the 100-ply, 300-ply, 600-ply, and 800-ply cures of the TC380 resin system. Image Credit: Toray Advanced Composites
Conclusions
In summary, the TC380 resin system’s composite performance with T800GC 24K fiber was evaluated. This system showed highly comparable mechanical properties after curing at 135 °C, 150 °C, and 180 °C.
Interlaminate-related properties (CAI, G₁C, and G₂C) were found to produce comparable and equally superb results at each of the three cure temperatures. Retention from RTD to ETW - either at the 82 °C or 121 °C test condition - was generally excellent, with very little drop of properties across all of the cure profiles.
Mechanical properties of TC380 laminates cured at 150 °C were found to be similar to those of the 180 °C cure, when these were tested at 121 °C hot/wet conditions. This is indicated by the test results, as well as the related RTD and ETD values.
Furthermore, the system did not trigger runaway exotherm in tests up to 800-ply laminates. Void content was observed to be at a minimum when this was examined via the NDI C-scan.
Cure profile graphs recorded throughout cures appeared normal. while moisture resistance of each cure profile remained excellent following 2 weeks of water immersion at 72 °C (160 °F).
TC380 is ideal for part manufacture in a range of structural applications, thanks to its excellent moisture resistance, superior mechanical performance, and the fact that it is OOA processible at three different cure profiles.
Most notably, TC380 provides increased flexibility for manufacturers possessing limited cure resources, with manufacturers free to decide the most appropriate cure profile for their requirements and applications.
Toray Advanced Composites plans to continue investigating the TC380 system’s potential to accommodate shorter cure times at different cure temperatures.
References and Further Reading
- ASTM D3039, 2000, “Standard Test Method for Tensile Properties of Polymer Matrix Composite Materials” ASTM International, West Conshohocken, PA, 2010, DOI: 10.1520/D3039_D3039M-17, www.astm.org.
- ASTM D695, 2002, “Standard Test Method for Compression Properties of Rigid Plastics” ASTM International, West Conshohocken, PA, 2010, DOI: 10.1520/D0695-15, www.astm.org.
- ASTM D3518, 1995, “Standard Test Method for In-Plane Shear Response of Polymer Matrix Composite Materials by Tensile Test of a ±45° Laminate” ASTM International, West Conshohocken, PA, 2010, DOI: 10.1520/D3518_D3518M-18, www.astm.org.
- ASTM D2344, 2000, “Standard Test Method for Short-Beam Strength of Polymer Matrix Composite Materials and Their Laminates” ASTM International, West Conshohocken, PA, 2010, DOI: 10.1520/D2344_D2344M-16, www.astm.org.
- ASTM D6641, 2016, “Standard Test Method for Compressive Properties of Polymer Matrix Composite Materials using a Combined Loading Compression test Fixture” ASTM International, West Conshohocken, PA, 2010, DOI: 10.1520/D6641_D6641M-16, www.astm.org.
- ASTM D5766, 2011, “Standard Test Method for Open- Hole Tensile Strength of Polymer Matrix Composite Laminate” ASTM International, West Conshohocken, PA, 2010, DOI: 10.1520/D5766_D5766M-11, www.astm.org.
- ASTM D6484, 2014, “Standard Test Method for Open- Hole Compressive Strength of Polymer Matrix Composite Laminate” ASTM International, West Conshohocken, PA, 2010, DOI: 10.1520/D6484_D6484M-14, www.astm.org.
- ASTM D7137, 2017, “Standard Test Method for Compressive Residual Strength Properties of Damaged Polymer Matrix Composite Plates” ASTM International, West Conshohocken, PA, 2010, DOI: 10.1520/D7137_D7137M-17, www.astm.org.
- Villareal, H., Unger, S., Lee, F. Advancement of Out of Autoclave (OOA) Technology at Tencate Advanced Composites (II), USA. International SAMPE Symposium, Seattle, 2017.
Acknowledgments
Produced from materials originally authored by Henry S. Villareal and Frank W. Lee from Toray Advanced Composites, originally published at CAMX 2019.
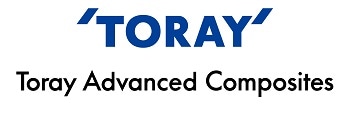
This information has been sourced, reviewed and adapted from materials provided by Toray Advanced Composites.
For more information on this source, please visit Toray Advanced Composites.