In this interview, AZoM talks to Joana Pinto, a senior researcher at RPCE, about the importance of powder characterization and how Granutools plays a role in aiding this.
For our readers, can you provide a brief introduction to RCPE?
The Research Center for Pharmaceutical Engineering (RCPE) is a global leader in pharmaceutical engineering sciences. We help our partners to create and manufacture advanced medicines for patients around the world, through optimizing products and processes.
The core of our science-based approach is the validation of predictive theories in a customer-focused experimental facility. Leveraging the expertise of our unique multidisciplinary team and our state-of-the-art capabilities in modeling, material science, process design, quality assurance, and control, we redefine current thinking in the field of healthcare offering cutting-edge, scientific solutions tailored to customer needs.
RCPE’s services encompass the entire value chain of pharmaceutical product development: continuous API synthesis, advanced formulations, next-generation manufacturing, and also device design and optimization.
What is the importance of powder characterization in your field of study?
Most of the medicines available on the market are solid powder-based (e.g. tablets, granules, dry powder inhalers, lyophilized injections). To develop medicinal products with the necessary quality it is crucial to identify and understand how powder characteristics impact drug stability, processability, handling, and in vivo performance. To this end, a multiscale knowledge approach enabling the understanding of the multitude of factors affecting powder performance is of the utmost importance; i.e. material/particle properties, type of dosage form being formulated, and processes used to this end, etc. Once this is achieved one can engineer, control and predict the powder characteristics that guarantee a successful performance space for medicinal products. Within this context, comprehensive powder characterization has been more than ever crucial to pharmaceutical product development, especially in a time where we are witnessing pharma manufacturing moving from batch to continuous and other advanced process technologies like 3D printing are implemented.
How can tribo-charging impact powder performance?
As mentioned previously, a multitude of factors can affect powder performance and the consequent quality of dosage forms. A particular example of this is powder tribo-charging.
Tribo-electrification is a charge transfer process in the course of frictional contact and separation of two solid surfaces. Tribo-charging can lead to issues such as un-intended particle agglomeration and adherence to container surfaces, leading to poor processability and product performance or even in extreme cases to dangerous dust explosions. Typical cases such as clogging of feeders during powder processing, strong caking, and charge-based segregation within a unit operation or during powder transport between unit operations can have a dramatic impact on the formulated product quality such as homogeneity, assay, dissolution, dispersion, etc. For metals, tribo-charging can be explained by their electronic state property called work function. However, as pharmaceutical powders are usually insulators, charging here is not yet fully understood. Likewise, it's crucial to better understand this phenomenon and find strategies able to mitigate its impact on product quality.
How could the tribo-charging of powders be controlled/mitigated?
Powder tribo-charging depends on the interacting impact of several factors, such as particle/material characteristics, formulation properties, process type, and environmental conditions. Consequently, a plethora of different strategies can be used to achieve mitigation. From a particle engineering perspective, properties such as solid-state, size, shape, and roughness can be tailored in order to mitigate charging. During formulation and processing, tailoring of the particle size distribution or addition of antistatic agents could also be used. Concerning the process equipment, this could be engineered with antistatic coatings, in process discharging/relaxation of charge or others in order to be less likely to induce electrification upon contact. Lastly, temperature and relative humidity could be tightly monitored and adjusted to provide conditions more amenable to low charging.
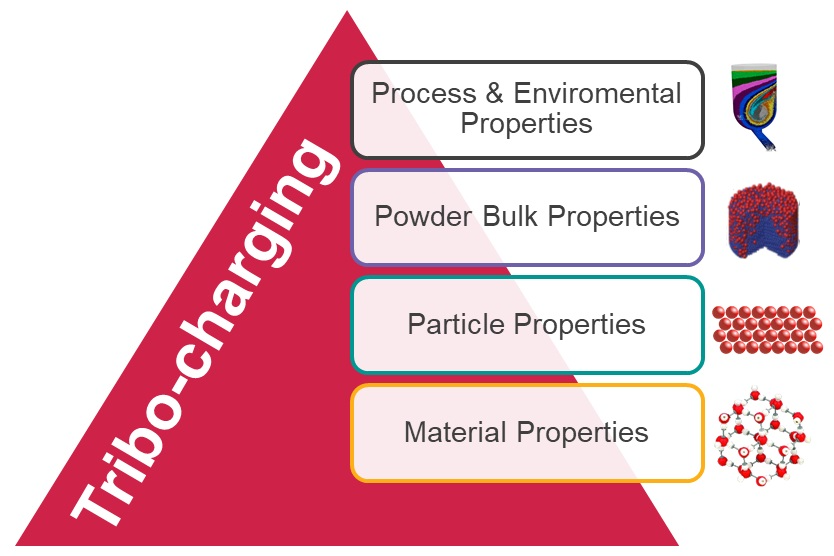
Why did you choose Granutools?
We choose Granutools as a partner for our analytical characterization of powder due to its strong scientific knowledge in the field and its robust, intuitive to use equipment. In particular the GranuCharge, a one of the kind equipment, able to quickly and precisely measure the electrostatic charges created inside a powder during flow. The flexibility of the equipment in providing the use of different surface materials (such as stainless steel and PVC) as well as the opportunity to precisely control environmental conditions provides a wide opportunity to understand tribo-charging under different various settings. Likewise, GranuCharge has been of great value in order to support us and our industrial partners in a better understanding of the impact of charging on the performance of pharmaceutical powders.
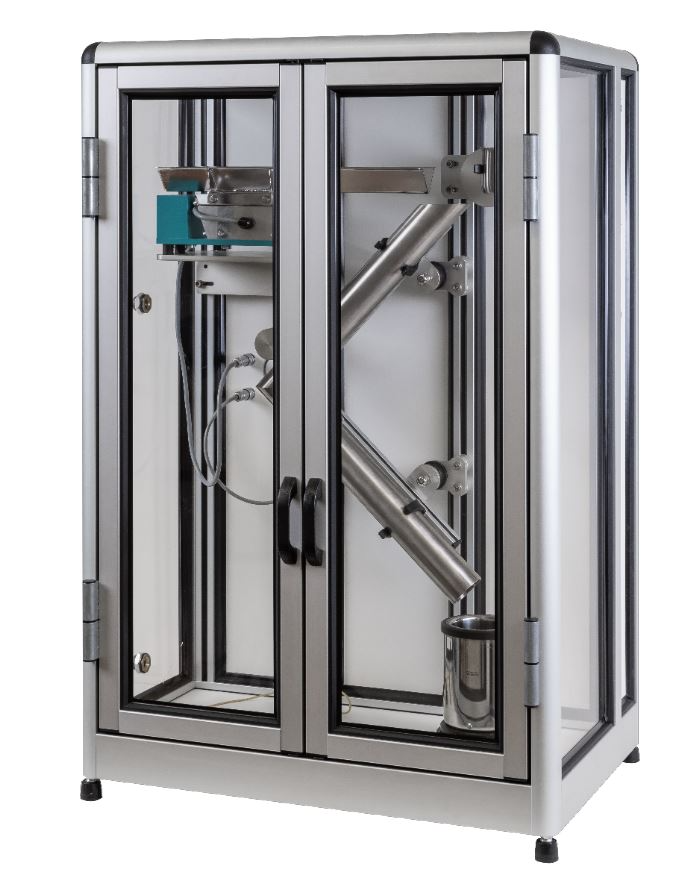
The Granucharge from Granutools
What are the next steps, plans, and challenges in the study of the tribo-charging of powders?
As a continuation of our studies focusing on material and particle properties (Brunsteiner et al., 2019, Pow. Tech. 359 and Zellnitz et al., 2019, Pharm. Res. 36), processing (Beretta et al., Int. J. Pharm., submitted) and humidity impact on tribo-charging (Pinto et al., 2020, AAPS PharmSciTech 21) we hope to achieve tailored, innovative solutions able to improve the processing and delivery of highly charged pharmaceutical materials. We also aim to further excel in building robust computational approaches for the prediction of powder tribo-charging. This includes, but will not be limited, to the prediction of tribo-charging of solid-state pharmaceuticals accounting crystal surface anisotropy and other related properties as well as the incorporating long range inter-particle interactions associated with tribo-electrification to our in-house discrete element method (DEM). Topics such as how to decouple impacting effects from one another and the standardization of experimental protocols are challenges to be tackled in the near future.
About Joana Pinto:
Joana Pinto is a senior researcher experienced in the topics of physical pharmacy and solid-state science for formulation engineering. At RCPE she is working and leading R&D projects for the pharmaceutical industry in the areas of particle engineering for advanced formulation development. Her work in the area of powder characterization and others can be found in several published papers.
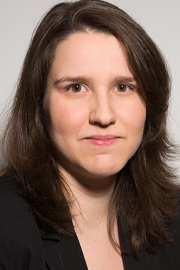
Disclaimer: The views expressed here are those of the interviewee and do not necessarily represent the views of AZoM.com Limited (T/A) AZoNetwork, the owner and operator of this website. This disclaimer forms part of the Terms and Conditions of use of this website.