Nov 13 2020
Powder coatings are on the surface of many things that we touch, from appliances, garden furniture, operational engine parts, wheels on vehicles, and electrical bus bars in industrial settings to rebar for real reinforcement. The universal occurrence of powder coatings is due, in part, to their appearance, stability, and environmentally responsible application process.
What are Powder Coatings?
Powder coatings are created using polymeric resins that are combined with pigments, curatives, flow modifiers, leveling agents, and additional additives. They are both solvent- and water-free systems. Their deposition produces a continuous, durable, anti-corrosive, and abrasion-resistant high-quality surface finish on metallic substrates.
What is the Coating Process?
There are two main powder coating practices, and the selection is usually based on part size and geometry. Big workpieces need the use of a controlled, factory-applied process known as electrostatic spray deposition (ESD). The coating method is made up of a micronized powder coating applied using a spray gun, whereby the powder is drawn to a grounded element through an induced electrostatic charge. Acrylics and polyesters are typically employed when coatings are decorative in nature., For industrial applications, epoxies are the norm, with hybrid resins gathering interest.
In the fluidized-bed procedure, preheated components are dipped in a trough, which contains the powder coating, with air blown in from underneath the particles. The part is instantly dipped in this floating bath and taken out, producing a discrete film.
The coating is consistent, the procedure is effective and environmental exposure is reduced in both spraying and dipping. Following the application of the powder coating, parts go into a curing oven in which the polymer resin chemically reacts, creating a uniform, homogeneous coating of long molecular chains with greater cross-link density. The part can then be put into service.
Applications: From Delicate…
Multiple possible applications exist for utilizing powder coatings, varying between small and fragile to large and tough.
Electronic components inhabit a broad range of devices, including computers, smartphones, tablets, TVs, stereos, and more. Printed circuit boards reside within these devices, containing resistors, capacitors, and sophisticated semiconductors. Powder coatings provide insulation and thermal resistance.
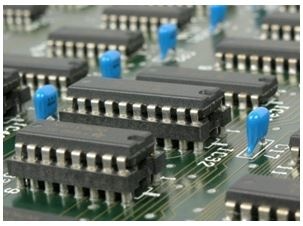
Figure 1. Powder-coated electronic components. Image Credit: CABB
…to Rugged
Pipelines employed in oil and gas exploration and delivery are powder coated on both the outside and inside to offer a safeguard from the environment, temperature, and chemical exposure.
The abrasion and corrosion resistance of underground pipe coatings are enhanced by epoxy powder coatings. These pipes are exposed to bacteria, soil acids, and alkalis, fungus, and soil stress. Additionally, underwater pipe coatings are protected against corrosive gases, solvents, wastewater, petrochemicals, and saltwater.
In this specific industrial setting, epoxy powder coatings are additionally known as fusion-bonded epoxies (FBE), cured with phenolics, dianhydrides, or dicyandiamides, subject to the degree of performance necessary. In each case, dianhydrides offer the best amount of protection.
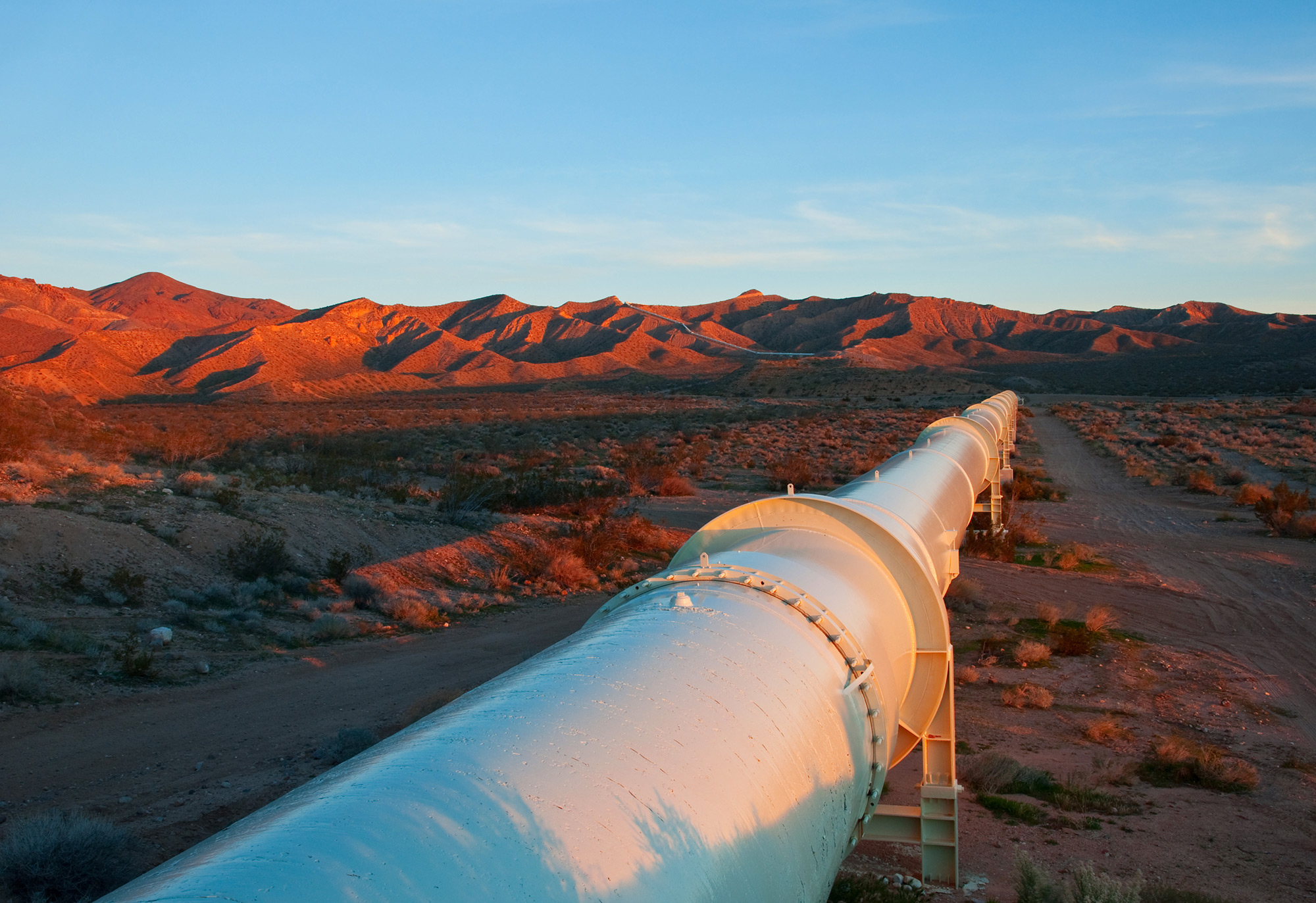
Figure 2. Pipelines require coatings inside and outside to address the harsh environments of both.
What are Dianhydrides?
Dianhydrides are important epoxy thermal curatives, providing sustainable physical, mechanical, and electrical assets even in unfavorable thermal environments.
Heat resistance is provided via broad crosslinking credited to the tetrafunctional structure of dianhydrides. The polymer network avoids chemicals and abrasion; insulates; and enhances dielectric behavior. Although these properties are advantageous, dianhydride-cured epoxies may be overly rigid, requiring tougheners to enhance bending resilience. Skillful formulators accomplish the right balance for every application.
The BTDA® Edge
A dianhydride which is frequently used for epoxy coating powders is 3,3’, 4,4’-benzophenone tetracarboxylic dianhydride (BTDA). This is a hard-working curative, which has been used since the 1970s.
BTDA is renowned for Tg enhancements as high as +30 °C in certain epoxy resins, especially those based on DGEBA. BTDA is available in both powder and micronized forms and as such, it is ideal for dry blending methods standard in powder coatings. BTDA enables epoxies to keep their properties when subjected to soldering, hot crude oil, and other adverse environments.
Summary
Although powder coatings have been around for decades, the evolution of performance requirements across several applications is calling for their continued specification. Powder-coated articles in a range of colors and textures can be seen everywhere in the workplace, vehicles, public transport, and throughout households. Modern manufacturing methods guarantee uniform film thickness and increased quality while addressing environmental impacts of overspray and waste.
Despite BTDA’s 50-year existence, this dianhydride continues to be widely recognized as the flagship epoxy thermal curative. An assortment of grades, supply chain security and high-temperature performance, provide a competitive edge to powder coating formulators seeking to excel in today’s and tomorrow’s marketplace.
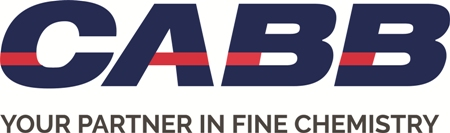
This information has been sourced, reviewed and adapted from materials provided by CABB Group GmbH.
For more information on this source, please visit CABB Group GmbH.