Lithium-ion batteries were commercially introduced in 1991, presenting new analytical challenges in the quest to improve the quality, safety, and lifespan of this fastest-growing battery chemistry. The basic structure of Lithium-ion batteries (LIB) contains as many as 10 different thin films that are synthesized to form at least that many solid−solid interfaces. These interfaces consist of thin layers of cathode material, insulating barriers, anode materials, metal current collectors, and the electrolyte. These various components are in the form of powders, sheets, and fluids and require an assessment before and after assembly and after repeated charge/discharge operations.
Scanning Electron Microscopes (SEM) supports the development of new LIB technologies with morphological observation at the micrometer to the nanometer scale, as well as the chemical analysis needed to create high-performance coatings and powders. Ultra-low-voltage imaging combined with signal filtering in the SEM allows direct imaging and analysis of battery constituents (anode and cathode) with nanometer resolution. Additionally, one of the important aspects of the analysis is the ability to probe the chemistry of the constituents at the nm scale (Fig. 1). JEOL FESEM offers the ability to perform microanalysis with energy dispersive spectroscopy (EDS) at extremely low voltages to pinpoint localized makeup of the specimens and, in particular, low atomic number materials such as carbon and fluorine. Moreover, the unique JEOL Soft X-ray spectrometer (SXES) allows researchers to analyze Li.
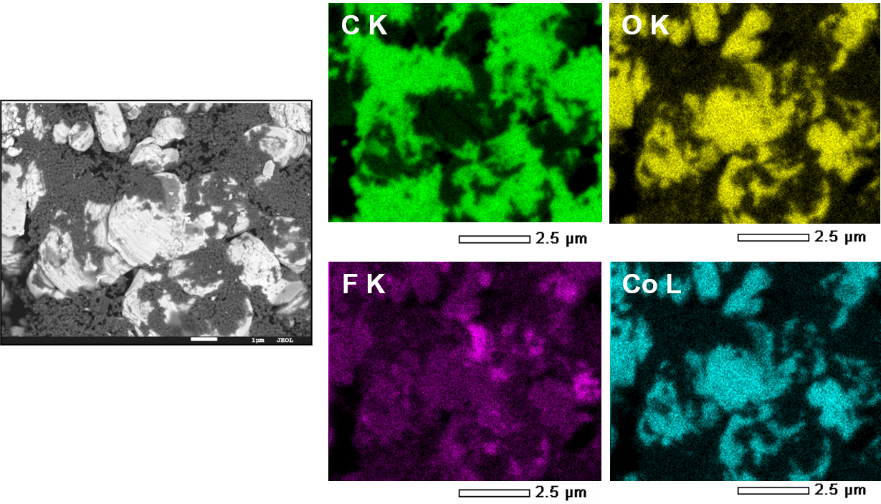
Fig. 1. EDS map of LiB cathode at 1.2kV, 6nA, 10kX. The map shows the distribution of C, F, Co, and O. Taken with JEOL FESEM.
“A significant thrust of the current research is focused on correlating electrochemical behavior to what is physically happening within the cell,” Dr. Ahmed Al-Obeidi (Ionic Materials, Woburn, Massachusetts) says. “In order to do that, one often needs to study the 3D microstructure of the battery components as well as the interfaces formed between those layers. Broad beam ion milling is a robust way to obtain clean cross-sections that provide microstructural information which, when combined with EDS, enables high spatial resolution with phase and chemical mapping. LIB composed of ceramics, metallic foils, and polymers presents a complex system that is difficult to get an artifact-free cross-section of using more traditional mechanical cross-sectioning techniques.” Ion milling is one of the only reliable techniques to get a clear sense of different layers as well as interfaces between layers (Fig. 2).
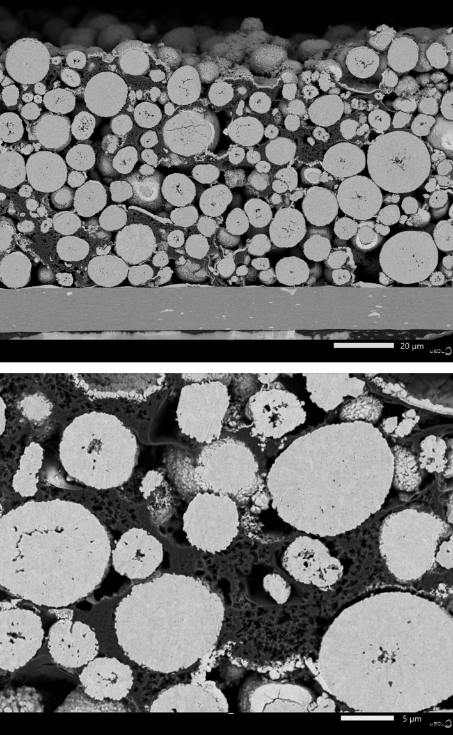
Fig. 2. Backscatter image of LIB cross-section prepared with JEOL CP polisher.
Moreover, for the evaluation of lithium-ion battery materials that potentially react and degrade upon exposure to air, it is indispensable to have techniques to prevent the exposure of the specimen to the atmosphere. For that purpose, JEOL has established a designated workflow that includes a common air-isolated transfer vessel that is used to transfer a specimen that has been prepared in an inert gas environment (such as in a glove box) to the designated specimen preparation equipment (broad ion beam polishing equipment, Cryo Cross-section Polisher), and subsequently into the SEM through a specimen exchange chamber without exposing the specimen to the atmosphere, so that it can be observed using the FE-SEM (Fig. 3). In the example here, specimens of a lithium-ion battery positive electrode material containing LiCoO2 are first observed without being exposed to the atmosphere, and then the same location is observed after exposing the specimen to air. There are no deposits observed on the unexposed specimens, but when the same locations are observed after exposure to air, the deposits are observed. This demonstrates the effect of the transfer vessel for preventing specimen exposure to the air.
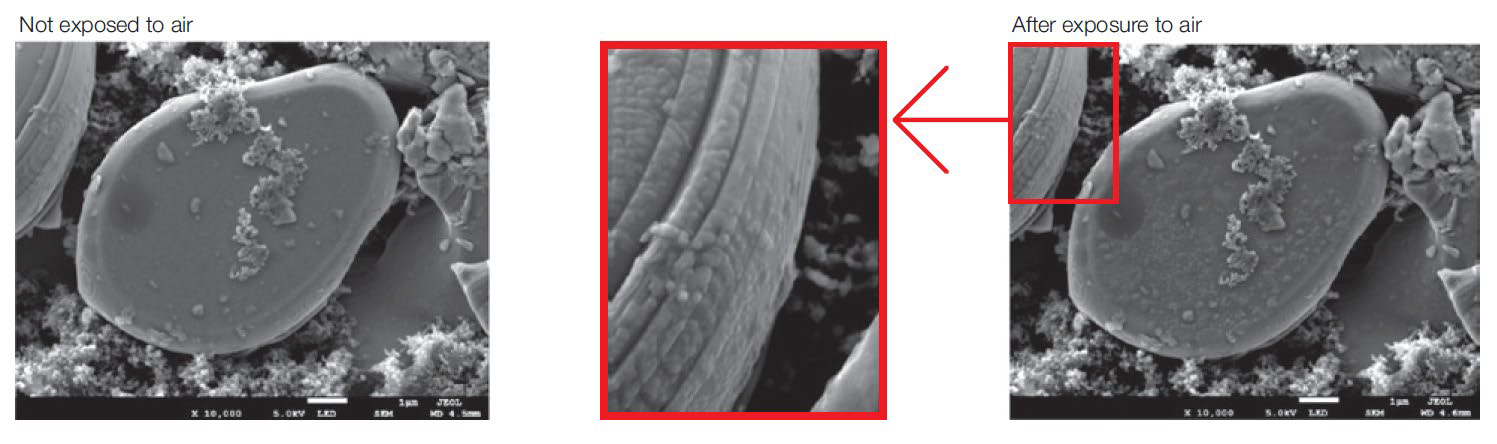
Fig. 3. LiCoO2 particles in the positive electrode before and after air exposure. Clearly, air exposure introduces various artifacts affiliated with specimen reactivity with atmospheric oxygen.
The combination of the air-isolated specimen preparation and transfer workflow and exceptional data fidelity make JEOL FE SEMs uniquely suited to meet the requirements of the LIB research needs. ‘We sent our samples to get imaged over several weeks, and they were unbelievable – really beautiful images – JEOL has a very skilled team and powerful imaging capability. All of the SEMs that we had access to (until now) didn’t have an inert transfer method, which is important for electrochemical or chemically active materials, and JEOL instrumentation offers are the necessary solutions’, says Dr. Ahmed Al-Obeidi. Ionic Materials are awaiting delivery this month of the IT800 FE SEM and the Cryo Cross-section Polisher.
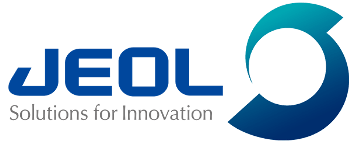
This information has been sourced, reviewed and adapted from materials provided by JEOL USA, Inc.
For more information on this source, please visit JEOL USA, Inc.