Precise measurement data is required by simulation engineers, while test engineers require high-quality equipment.
This data is crucial for performing essential tests to meet the demands of decreasing fuel consumption by utilizing composite materials, ensuring safety and drive concepts and with CAE-supported development processes and new materials.
Vibration sensors that deliver accurate results in a non-intrusive manner can benefit both the development of new NDT techniques or a classic modal test and turbine durability validation.
This article demonstrates how tools from Polytec have assisted its customers in performing crucial applications in the area of dynamic measuring technology.
Vibration Measurement in Aerospace Development
Structural testing is an integrated stage of aerospace manufacture, development and product design. It is a vital stage to validate reliability, safety, quality and performance in the end product.
The current pressure on the market for affordable, new, high performance aerospace products is expanding the complexity of tested structures and the number of product variants.
Product design and development refinement teams require modal testing that is more efficient to enhance throughput while maintaining a precision that sufficiently correlates with FE analysis models, for example, acoustic radiation, load analysis and more.
A significant amount of spatial data points are also required by these new structures. The combination of more measurement points and more structures is quickly increasing the costs of performing a conventional modal test, with its labor intensive approach of furnishing structures with multi-channel data acquisition systems and accelerometers.
Noise, Vibration and Harshness
Aerospace manufacturers seek competitive advantages in two major areas, increased passenger comfort and fuel economy, due to the fight for commercial aircraft orders.
As such, modern aerospace engineers are more focused on noise measurements than their predecessors were. Aircraft engineers increase the comfort of passengers and their desire to travel in a next-generation commercial jet by enhancing interior sound quality.
When exterior noise is reduced, the designer can increase the acceptance of aircraft in urban locations where air traffic is quickly increasing. Vibrometers from Polytec are a necessity for major aerospace companies aiming to perform NVH measurements on their latest aircraft.
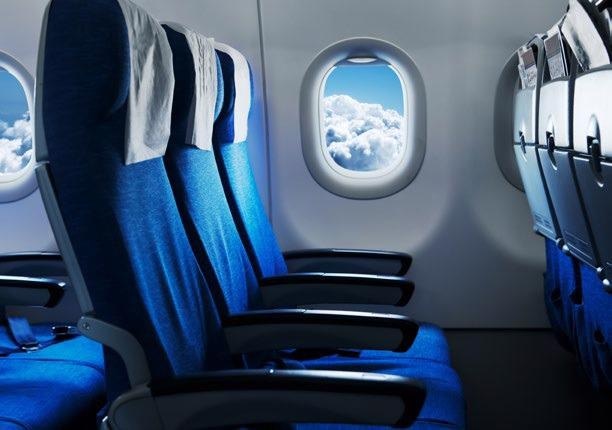
Image Credit: Polytec
Flutter Certification
Polytec’s PSV-3D Scanning Vibrometer technology is utilized at the Air Force Institute of Technology (AFIT) to quantify the vibration features of Unmanned Aerial Vehicles (UAV) and other complex vehicular and aerospace structures.
The use of this tool has optimized the flutter analysis results for airplane FE and has significantly decreased the post processing analysis and test duration.
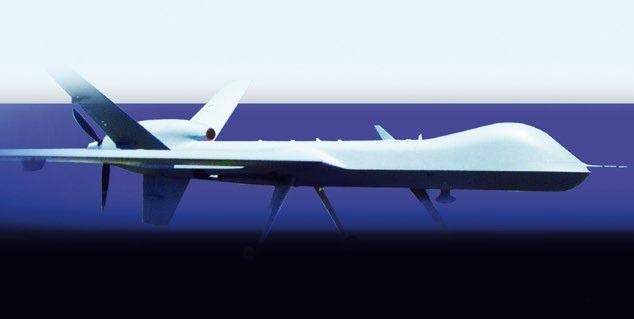
Predator UAV. Image Credit: General Atomics
Ground Vibration Testing
Ground vibration testing (GVT) is an expensive requirement for new aerospace and aircraft structures. The data acquired can be utilized for finite element (FE) model correlation and modal analysis, flutter certification and for loads analysis to stop structural failure.
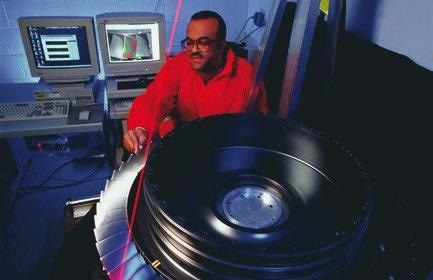
Measurement of turbine blade vibrations. Image Credit: Greg Roberts, Pratt & Whitney
Component Testing
A vibration analysis of an aircraft component can identify the main frequencies, define a complete modal model of the component and can characterize the structural dynamics of the component. For example, aircraft tires are important components that must adhere to incredibly high quality specifications.
Engine Testing
Engine design is being pushed to new limits with the rise in demand for more powerful and environmentally friendly jet engines. Laser vibrometry can be effectively used to solve one of the most important yet challenging tasks, which is an accurate interpretation of lifetime-relevant vibration phenomena.
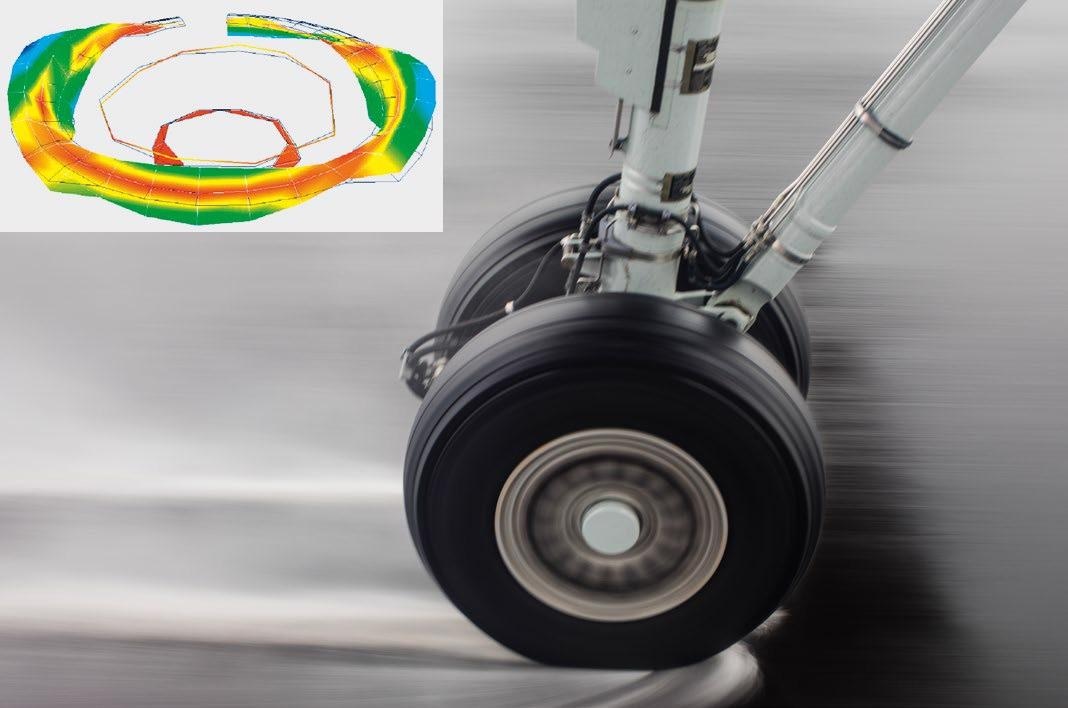
Operational deflection shape of an aircraft wheel. Image Credit: Polytec
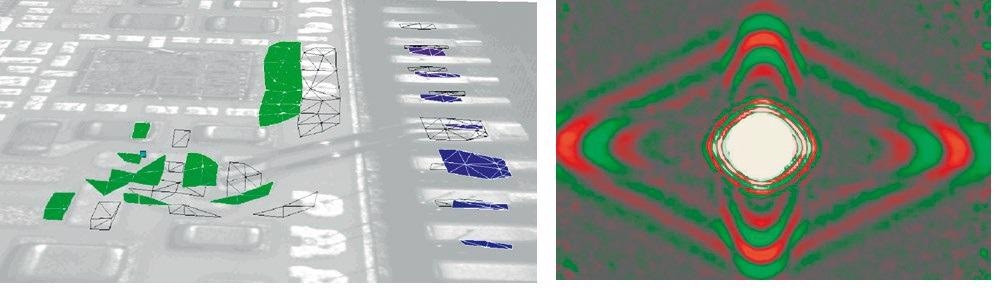
Propagation of compression waves in a CFRP panel. Image Credit: Polytec
MEMS and PCB testing
Laser vibrometry is the preferred choice for micro-electro-mechanical actuators and sensors and vibration testing printed circuit boards.
Material Testing
Material cracking and delamination are popular defects that can strongly decrease aerospace product performance. To identify localized defects, both lamb wave detection and nonlinear laser vibrometry are effectively employed as a means of non-destructive testing (NDT).
Flying the Best
Scanning laser vibrometry includes efficient, non-contact (no mass loading) and full field vibration measurement with high frequency and spatial resolution. Aerospace development scientists and engineers can decrease both the complexity and duration of vibration testing by using scanning vibrometers from Polytec.
Vibrometers from Polytec are the industry standard for non-contact vibration measurements in aerospace quality control, development and aircraft health monitoring.
Sail Away: Laser Vibrometry Helps to Validate Gossamer Space Structures
NASA is initiating the production of large ultra-lightweight structures that are widely known as Gossamer space structures. These structures have small aerial densities and large areas, which significantly complicates ground testing because gravity loading and the ground operations interfaces can become challenging.
Laser vibrometry has been established as a crucial sensing technology for verifying the dynamical characteristics of these Gossamer structures because of its range, precision and non-contacting (zero mass loading) nature.
For many years, NASA has been producing Gossamer space structures to utilize the novel capabilities of specific concepts and to decrease launch costs.
For example, dish antennas (Figure 1) are currently being investigated as they can be inflated in space to sizes as big as 30 meters and then rigidized to facilitate high data rate communications.
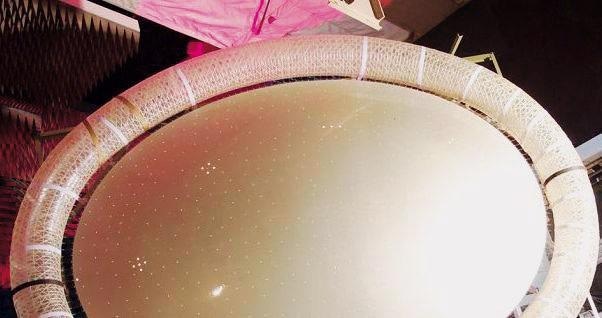
Figure 1. Inflatable 4x6-meter communications antenna concept. Image Credit: Polytec
A solar sail is another example of a Gossamer structure that delivers an inexpensive source of propellantless propulsion. Very large areas are covered by solar sails to acquire momentum energy from photons and to use it to propel a spacecraft.
While small, the thrust of a solar sail is constant and functions for the duration of the mission with no requirement for propellant. New developments in ultra-lightweight Gossamer structures and materials have opened up a range of beneficial space exploration missions that use solar sail propulsion.
A team that includes NASA Langley Research Center, ATK Space Systems and SRS Technologies, under the management of the NASA In-Space Propulsion Office (ISP), has evaluated and developed a scalable solar sail configuration (Figure 2) to meet the future space propulsion requirements of NASA.
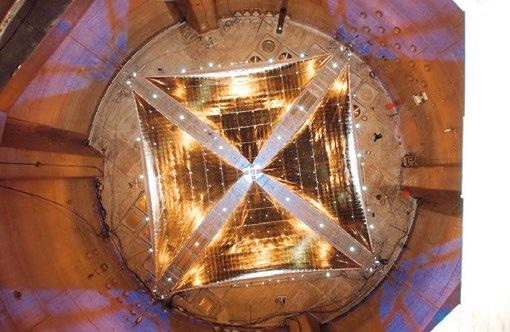
Figure 2. Deployed 20- meter solar sail on vacuum chamber floor. Image Credit: Polytec
Three main challenges were faced by engineers when testing solar sails on the ground:
- In-vacuum tests were required due to the significant air mass loading under ambient conditions
- The surface had to be partitioned into manageable areas due to high modal density
- Measurements had to be performed on large surface areas that were thinner than paper.
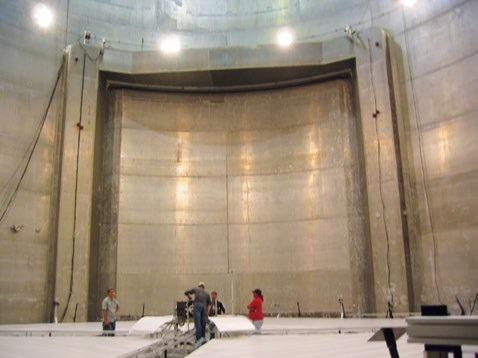
Figure 3. Vacuum chamber facility. Image Credit: Polytec
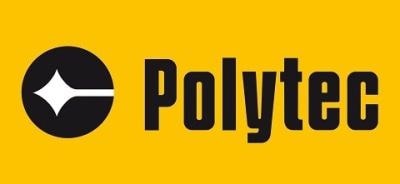
This information has been sourced, reviewed and adapted from materials provided by Polytec.
For more information on this source, please visit Polytec.