In this interview, AZoM talks to Francis Arthur, Operations Manager for TRB, about TRB's solutions for transport and its composite products.
Could you give us an overview of the solutions that TRB Structures manufactures?
TRB manufactures lightweight components for transport applications. Our goal is to make transport lighter for rail, electric vehicles, cars, automotive, or aircraft. Much of the company’s work so far focuses on manufacturing interior parts for trains, including partition walls, flooring, ceilings, storage modules, or toilet modules.
More recently, we have started working with composites, and that is certainly my background. One of the things that we are currently looking at is composite battery boxes within electric vehicles. We are essentially using composite materials to produce a battery container, which is fire-retardant enough to keep the vehicle safe during any incident.
Composites offer a lightweight alternative to what was previously aluminum or steel. They are particularly useful from an electric vehicle point of view because lighter vehicles will have superior range and battery lifetimes.
TRB is different from other transport solutions companies. Many companies offer one material, such as composites or an aluminum machining company. TRB offers lightweight structures and we can use a range of materials based on the application that we are working with. We are not weighted or tilted towards one particular solution in terms of a material choice - we can offer the best for the customer.
What are the key challenges involved with manufacturing components for the various transport sectors TRB operates within?
Our three main transport areas are rail, air, and road, and each of these presents different challenges. We have worked with the rail industry the longest. Our main challenges are new design work and improving production efficiency to be as competitive as possible. However, in the last few years, we see a change in the rail industry, as they move towards using more greener energies, lighter materials have become more commonplace.
We are carrying out excellent work and innovation here. For example, we have worked on two pilot projects using complex composite sandwich structures, one for a train door, and the other for a section of carriage wall for a prototype light tram. Rail has been generally less focused on weight reduction, so there is less demand for composites. However, there are significant benefits to lightweighting specific components such as doors to reduce wear on opening mechanisms and increase lifetime.
There is increasing interest in train applications that require lightweighting, for example, battery power trains have range challenges, and lightweighting can improve this.
In contrast, air transport is heavily driven by weight restrictions. Our challenges here are around producing solutions with the lightest weight possible. We are working less with large passenger or large-scale aerospace at the moment and more with electric vehicles such as flying taxis and delivery drones.
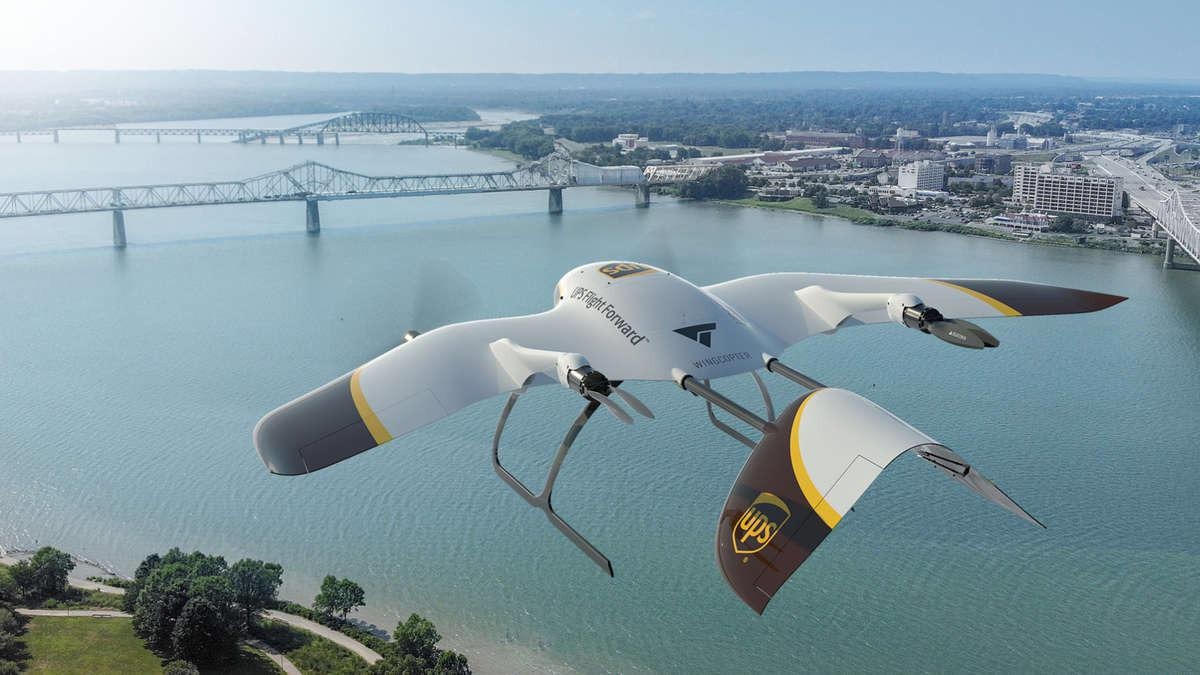
Weight is critical because anything that flies needs to be lightweight to be efficient. However, reduced weight also increases payload and increased range, which are essential considerations from an electric vehicle point of view.
Challenges around road transport are linked to cost and weight, but volume is also a big problem. A key challenge when looking to use composites in the automotive industry is that the volume requirements are at odds with what the composites industry can develop and deliver.
Composites historically are used in low volume industries such as Formula 1. However, realising the benefits of composites in everyday automotive requires the manufacture of tens of thousands or hundreds of thousands of parts a year. Delivering high quality, cost-effective, lightweight parts into an automotive application is a real and current challenge. TRB has developed a high volume composite manufacturing process called FPC to address this challenge.
What parts do composite materials play in reducing energy consumption for transport?
There are multiple benefits to using composites, but it is mainly about reducing weight. Using lightweight versions of components is the most apparent means of reducing energy consumption.
Composites have a lower density than typical metallic components, so the same part will be lighter. More importantly, composites have a higher stiffness which means that you can reduce the quantity of material required to make a part of the same mechanical performance. Furthermore, it is possible to optimise the part design and the fibre orientation to ensure strength in the direction or specific area you need.
There are many different ways of using composite materials. However, they all have the same goal of making a part equivalent to mechanical performance while being much lighter.
How is TRB making use of new materials to increase sustainability?
A significant element of sustainability is trying to reduce energy usage, and this is the crucial vision of TRB and something the company has always focussed on.
Sustainability and recyclability are already big focuses in the composites industry. There are two current challenges in the industry. The vast majority of resin systems used are all oil derived, and using raw materials from the oil and gas industry is not the most sustainable route. The second issue is that the end of life of composites is difficult. By nature, they do not corrode or break down, and it is challenging to get rid of them in an environmentally friendly way. At the moment, these either go into landfills or are burned.
Rather than using oil-derived materials, TRB is one of the first companies to use a resin system called PFA (polyfurfuryl alcohol), a resin derived from biomass waste in the sugar cane industry.
PFA has strengths and weaknesses and performs most similar to a phenolic resin. On the plus side, it performs well in terms of FST (fire, smoke, and toxicity), an area where many resin systems generally struggle. On the downside, it has relatively low bond strength and mechanical performance, meaning it is challenging to use PFA to make structural components or sandwich panels.
We have done a lot of work to maximise the benefits of PFA while working on improving its bonding performance. It took around three years, but we have developed a solution by which we can use PFA to make a sandwich panel with good structural performance. We can now use this resin system for structural products sold to customers, and that is something we are very proud of.
It is still in the early stages of development, but we are also working with a company that has created a fully recyclable resin system. This will mean that this resin can dissolve at the end of its life and be made into a resin again before starting more composite components. This is the kind of technology that could turn composites into a circular economy or a circular manufacturing system.
What do you think the future holds for composites in the transport industry?
I think the future is looking very positive. There will inevitably be significant growth in the use of composites in transport. Composites offer a unique solution to making transportation lighter, and the technology’s benefits are too good for it not to be rolled out wider into the transport industry.
For example, Formula 1 cars are 80-90% composite in terms of their bodywork. I do not see why the performance benefits that this provides could not be rolled out into the wider car industry. This has already started to a degree. The BMW i3, for example, was a production car and had a body shell that was an entirely composite material.
There are a lot of areas of composite research that will be of benefit to the industry. A few examples include; ongoing work to reduce the cost of carbon fibre, and as this becomes cheaper, it will almost certainly be used in more applications. The joining of composites and multi-material structures - using composites in conjunction with metals, for example, to realise mutual benefits of different materials. I think there will also be a rise in multifunctional composites using the additional material properties of glass and carbon fibres such as thermal conductivity and electrical conductivity. We will also see the continued increased use of thermoplastic resins, strengthening the recyclability and manufacturability of composites. Automation is another key factor that will increase productivity and improve the industry, further strengthening the introduction of composites across the wider transport sector.
Having said all of that, I think there are two significant hurdles that composites must overcome. One is the sustainability and end of life issue mentioned already. Until this is fully solved, I think it will slow the rate of increased use of composites. The second hurdle is ensuring effective and efficient volume production. An adequately integrated, high-volume composite production system is essential.
What is TRB doing to stay at the forefront of reducing energy consumption?
My view is that composites will be used more in mass transport, so solving the mass volume issue already mentioned is the most significant barrier to that at the moment. TRB has been working for around two years on a production line that will manufacture composite parts at a medium to high volume rate.
The newly developed process takes us from woven carbon fibre to a finished composite part at the other end. This process involves using a prepreg machine that takes fibre and turns it into prepreg, an automated cutting station that cuts plies as they come off the prepreg machine, and an automated means of accurately placing those prepregs into a press-forming process to create a composite part. Once this has been completed, an automated de-flash is used to finish the part, with stations available as required to add metallic inserts, a liquid gasket, or other additional materials onto the composite component, as required by the customer.
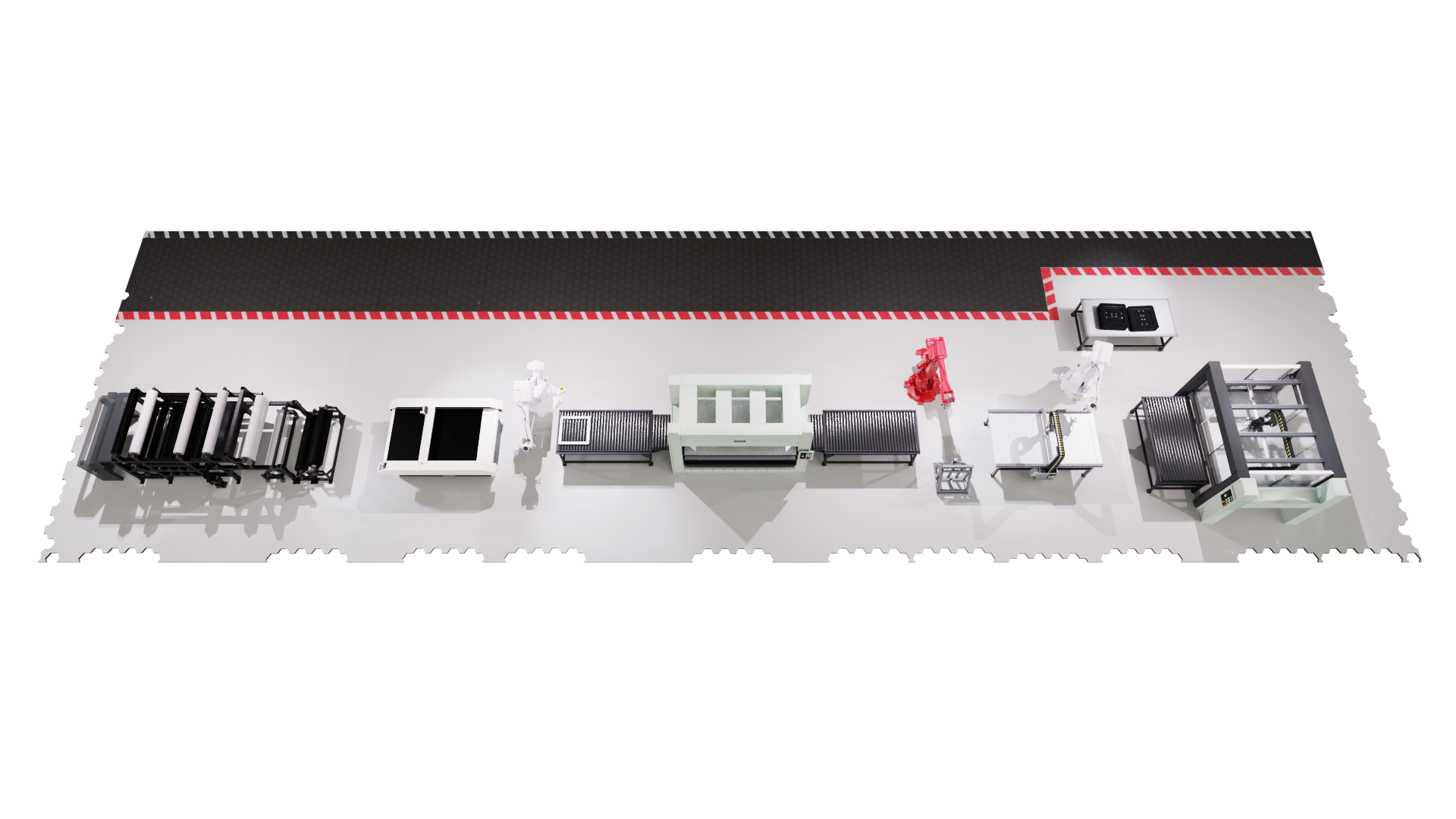
We aim to have that whole process running in an automated fashion with a single-digit figure of tack time. This is a step-change in terms of the manufacturing rate for composites, and not something that currently exists to my knowledge.
I think that is the future, and that is what TRB is doing; realising that future to develop increasingly lighter weight transport solutions.
About the interviewee
Francis Arthur is the Operations Manager for TRB and is responsible for the engineering, and manufacture of TRB’s products. Prior to this, he was the R&D manager developing and implementing innovative new materials and processes into TRB to drive the manufacture of their environmentally conscious lightweight solutions.
Francis has a master's in material science and has excellent knowledge of Polymers, Thermoset and Thermoplastics. He has been instrumental in utilising his expertise in developing TRB's new vertically integrated, fully automated composite manufacturing process. Francis has been an active board member of Composites UK for the last two years.
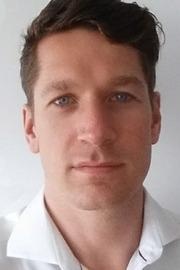
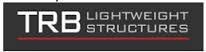
This information has been sourced, reviewed, and adapted from materials provided by TRB Lightweight Structures Ltd.
For more information on this source, please visit TRB Lightweight Structures Ltd.
Disclaimer: The views expressed here are those of the interviewee and do not necessarily represent the views of AZoM.com Limited (T/A) AZoNetwork, the owner and operator of this website. This disclaimer forms part of the Terms and Conditions of use of this website.