In this interview, AZoM talks to Lyndon Newman, Lead Engineer for Rail at TRB Lightweight Structures, about the use of TRB's composites in the Rail industry.
Could you give us an overview of TRB Lightweight Structures' history in the rail industry?
TRB has been manufacturing parts for rail vehicles for around 50 years. To my knowledge, the oldest parts we manufactured were doors built for District Line underground trains that went into service around 45 years ago. These trains have recently been taken out of service and sold on to another company for refurbishment and are now being used as battery-powered trains, with the same doors.
What types of trains do TRB Lightweight Structures manufacture for?
TRB manufactures for anything transport-based, including trams, underground and overground trains, commuter trains, and high-speed trains. It largely depends on the performance and customer requirements.
The lightweight structures are usually manufactured from bonded assemblies (generally aluminium skins and honeycomb). The fibrous composite structures that we manufacture lend themselves to high-speed trains where weight is critical. Bonded composite structures may not be competitively priced as bonded metal structures, but what you gain is a more sustainable construction that lasts longer and requires less maintenance.
Our lightweight structures also appear in the door structures on underground trains and parts for trams, floors, ceilings, and interior walls. We work with a wide variety of components and applications - it all depends on the customer’s requirements.
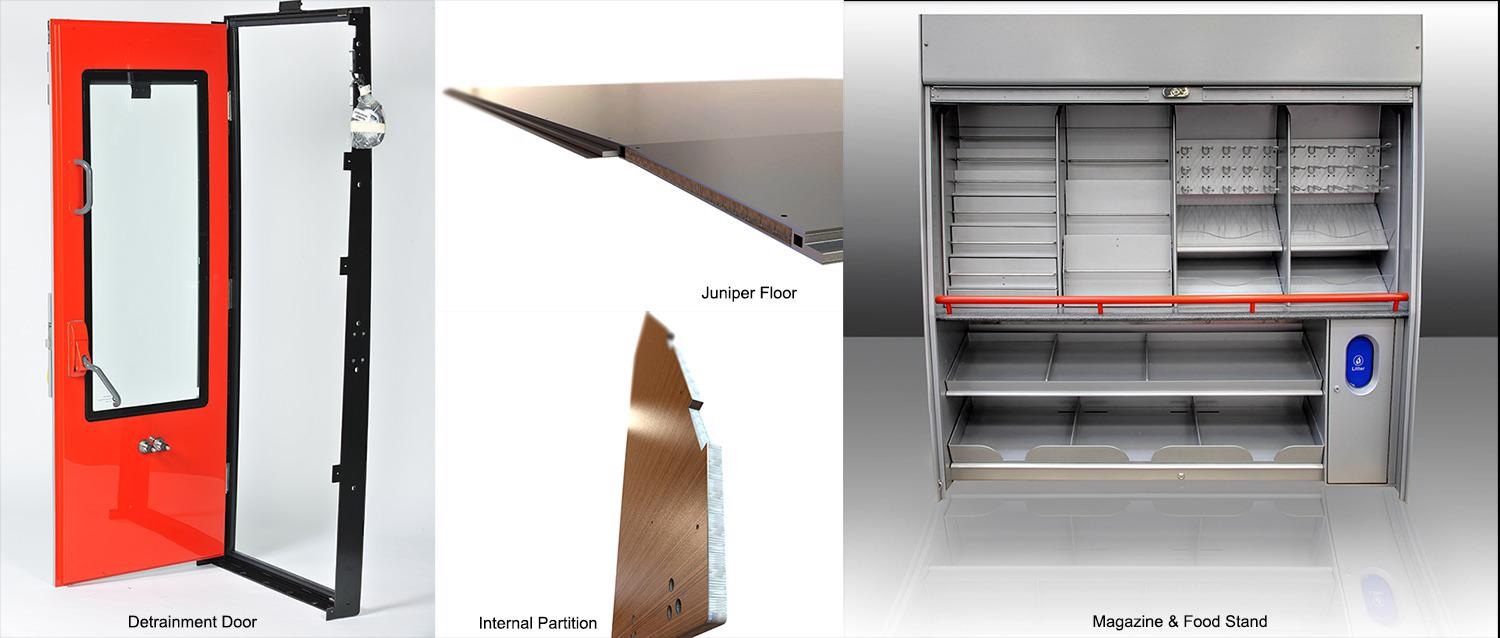
What are some of the challenges associated with designing and manufacturing for the rail environment?
One of the biggest challenges to design is weight and performance. Historically they have taken large pieces of metal, cast iron and wood, then assembled these to manufacture locomotives and carriages. This has been satisfactory in the past, but it takes a lot of energy to move a train made from such heavy materials and now the rail sector, along with all transport sectors, are looking to move towards greener solutions, that lower emissions and are better for the environment. So with this in mind, the provision of weight-saving products into the vehicles is of a huge benefit, the lighter the train the less energy required to drive it. Lighter trains can run more efficiently not just using existing power supplies such as electricity, but also using alternative sources such as Hydrogen.
As composite and bonded assemblies can be produced by bringing a combination of lightweight materials together, we can also offer options that provide the necessary performance characteristics.
When TRB initially starts working with a customer, one key challenge is load case requirements. The train has to perform to a specific standard, and this involves several tests such as impact, crash, fire, acoustic, and possibly thermal testing. Developing a component that will meet all of these requirements requires experience and knowledge. Depending on where the train runs, these requirements could be much stricter, for example, an underground train would likely have much more stringent fire requirements than an overground train.
We manufacture all our products to excel at meeting all relevant standards. We offer concepts, designs and material selection advice, and go through what we refer to as ‘validation’ testing. During validation, we perform the full range of fire, impact, and load testing. Impact testing is especially interesting because it uses special air-cannons that shoot a projectile, anything up to 300 kilometres an hour, at point-blank range, into an external structure component, quite impressive to watch!
Internal structures do not generally require this sort of testing because the shell of the vehicle protects them, but we still have to think about several potential scenarios. For example, what happens if the train comes off the rails, or if a person or a piece of luggage falls and hits a toilet door (one of our typical components)? These are things that commuters often take for granted when they walk up and down a train, but they are integral design considerations.
Now trains are designed to last around 40 years from being new. This is a long time for any component to last, so we have to make sure that what we provide can stand up to the demanding rail environments over the life cycle of the vehicle.
How do TRB Lightweight Structures help customers to solve these challenges?
TRB has designed and created a myriad of train components, including floors, doors, ceilings, partitions, and more, these components are seen on trains that people travel on everyday, including the Hitachi IEP trains operating on the Great Western and East Coast Mainline routes.
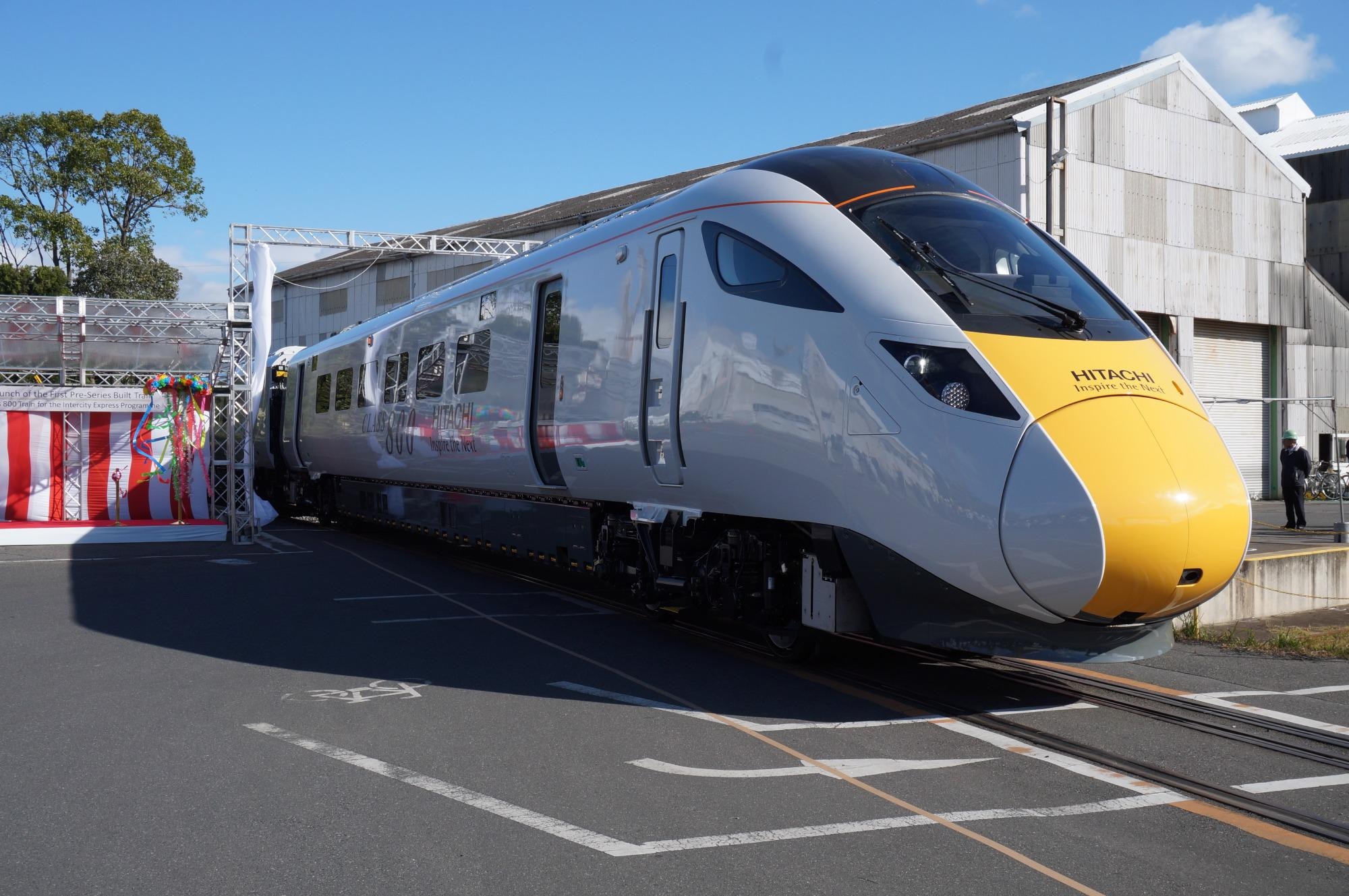
When working on these projects we study what works best and record all the necessary information detailing the best way to meet the challenges, focusing on quality and performance. We then use this experience and our unique specialist knowledge to inform customers of what our products can achieve, what they can do, how they will work in practice, and what the product can offer to enhance the customer’s project.
Many of the products we manufacture tend to be structural components, based around features such as toilet cubicles and partitions between train carriages. These are also generally made from bonded composite sandwich structures (having historically been made of plywood).
How does the design of lightweight structures impact energy construction?
When current train carriages are big and heavy, they take a lot of power to move. When the weight of these is reduced, it makes sense that movement becomes a lot easier. There can be anything from two to eleven carriages on a train, meaning that there is a total weight of hundreds of tons across a large number of components.
Composites offer an ideal means of reducing overall weight. As an example, most commuter trains have grab-rails for passengers to hold onto, these tend to be made from three-to-four-millimetre steel. We recently developed a composite grab rail using carbon fibre, for an underground train. We calculated that, for every carriage, we could save one metric ton of material weight (based on over 40 grab-rails being in place). In instances with nine carriages in the row of vehicles (referred to as a rake), this results in nine tons of weight-saving - meaning that an electric motor or a diesel motor would not need to work nearly as hard to move the train. Logically when an engine does not have to work as hard, the energy used is less and the emissions are not as high, making it better for the environment.
What is next for TRB in the rail industry?
It is still taking time for the rail industry to move away from the traditional methods of items being manufactured from heavier materials such as cast-iron and steel. I have worked in the industry for 35 years, and it has only been in the last 10 years that the use of lighter materials have started to become commonplace.
The more transport moves away from fossil fuel-driven vehicles (such as diesel engines) towards greener energies, the more efficient vehicles will need to be. To be more efficient, we need to consider materials such as the ones noted in this article and even more exotic composite materials that are in development.
As a good example of this, last year, we completed a program with a customer in the West Midlands who are building what they refer to as a ‘very light rail vehicle’. We were fortunate to build the body-sides, which are large, three metre by three metre, carbon-fibre, honeycomb structures, and window cutouts. These were made from fully composite materials, so no welding or large metal pieces were required, apart from a few small brackets. This prototype light tram is mainly made up of lightweight composite structures and potentially designed to run in town centres around existing travel infrastructure. It is an innovative and exciting new direction for light rail vehicles and we were delighted to be part of this program.
Overall in the future, I think there will be a move to more high-tech and perhaps more cost-effective composites. Composites tend to be not as competitively priced as their metallic counterparts because of the nature of the material and the associated processes, but TRB has recently developed a new system that allows us to produce composites in what we refer to as ‘fast-pressed cure’ method. Making it now possible to produce high volume parts faster and more cost-effectively than we could previously due to automating the process.
Due to this increased cost-effectiveness, carbon fibre, and glass-fibre composites will become more prevalent than metal composites over the next 10-15 years as advanced transport systems become the norm.
Do you think composites will ever make their way to the general consumer market?
Composites are already present in many places. Technically, composites include everything from the GRP used to make a bathtub to the materials used in various components found in the water industry.
The higher-end composites such as carbon fibre and glass fibre prepregs are found in the public domain, but they tend to be reserved for more high-end applications because of the cost - these are not something that you would see often. For example, a car’s dashboard may include a carbon-fibre look-a-like trim, but in many cases, this is a printed high-pressure laminate, similar to those in use on tabletops at home.
Composites are found on high-end motorbikes and high-end cars. Carbon-fibre is used because people like the look, but it has the added benefit of being exceptionally strong, exceptionally stiff, long-lasting and offering excellent performance characteristics compared to steel.
If you ever go on the London Eye gondolas, all the floor structure panels were built by TRB in Huntingdon, and these are made of honeycomb composite. The London Eye’s owners wanted lightweight structures for obvious reasons; because a wheel continuously moving works well if it is not too heavy!
Composites are found in everyday life, but they tend to be well hidden. I always refer to our industry as a stealth industry because it is everywhere, but you cannot always see it.
About the interviewee
Lyndon Newman is the Lead Engineer for rail at TRB Lightweight Structures and has a career with the company stretching back to 1996. In this time he has been responsible for delivering major interior solutions for OEM’s in the Rail Industry. These include interior products for the West-Coast Pendolino for Alstom, the design of the SSL “M” door for London Underground and most recently in overseeing the bike storage unit; galleys and partitions package for the Class 800/801 interiors for Hitachi.
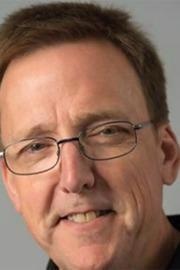
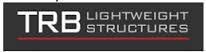
This information has been sourced, reviewed, and adapted from materials provided by TRB Lightweight Structures Ltd.
For more information on this source, please visit TRB Lightweight Structures Ltd.
Disclaimer: The views expressed here are those of the interviewee and do not necessarily represent the views of AZoM.com Limited (T/A) AZoNetwork, the owner and operator of this website. This disclaimer forms part of the Terms and Conditions of use of this website.