Companies must seek out creative solutions to protect their employees as the world adapts to the ‘new normal’ brought about by COVID-19. This means that, for many, reorganizing the workspace to increase social distancing, better cleaning procedures, and the implementation of new health screening protocols are commonplace.
This article will outline a number of materials testing technologies that can enhance a facility's testing lab to reduce the risks posed by shared spaces and surfaces and improve social distancing.
Hands-Free Grip Operation
On a universal testing machine, one of the most high contact surfaces is the grips. Found in most testing labs, manual grips are the most common gripping solution but are also a source of potential contamination as the test operator must loosen and tighten them by hand every time a specimen is inserted and then removed.
Instron's 2712 Series pneumatic grips provide a safer alternative for testing capacities up to 10 kN as they can be equipped with a footswitch, which enables the operators to open and close the grips with minimal hand contact.
For 3400 and 6800 Series systems, the Smart-Close Air Kit with footswitch may be outfitted on all existing and new systems. The Automatic Air Control Kit comes with a dual pedal footswitch for 3300, 5900 and 5500 Series.
Manual Grips vs. Hands-Free Grips
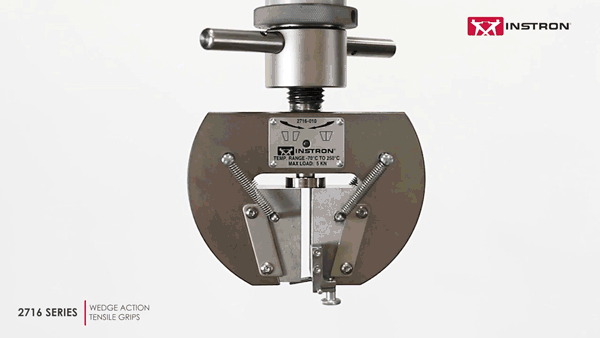
The tightening mechanism of a manual grip, like the mechanical wedge action grip shown above, involves frequent contact when opening and closing the jaw faces. Image Credit: Instron - USA
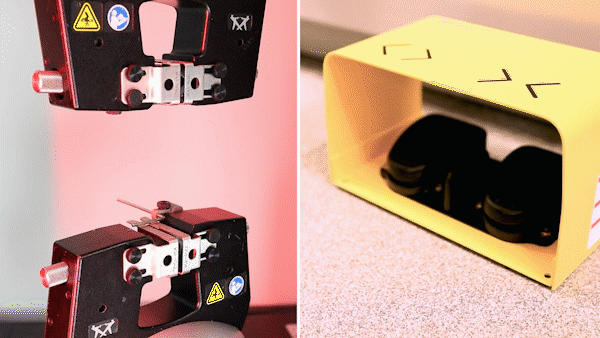
The pneumatic grips footswitch operation allows the operator to open and close the grips with their foot, without the operator needing to touch the grip with their hands. Image Credit: Instron - USA
The Smart-Close Air Kit for 3400 and 6800 Series systems permits the grip pressure to be pre-defined in Bluehill® Universal for further hands-free optimization.
The grip pressure is saved with the test technique to eliminate the requirement for the manual adjustment of a regulator when modifying test techniques for different specimens or materials.

Image Credit: Instron - USA
Operator Dashboards vs. Traditional PC Setups
A computer is another high contact surface on a universal testing machine. The latest Instron testing systems can be equipped with Bluehill Universal software and its touch-friendly Operator Dashboard, as can even older, out of production systems that have been retrofitted.
If touch friendly devices should be avoided at this time, compared to a traditional mouse and keyboard, it is much quicker and easier to sanitize a touch screen after each use.
The Instron Operator Dashboard also employs capacitive touchscreens, which are compatible with nitrile and latex gloves. This means it is possible to carry out all lab tasks in gloves if needed.

Image Credit: Instron - USA
The ability to heighten social distancing in the lab is the second key advantage to Instron's Operator Dashboard. By eliminating the need for a mouse, PC tower, monitor and keyboard, the Operator Dashboard saves a large amount of benchtop space over traditional PC setups.
The All-in-One (AiO) Operator Dashboard enables the user to adjust the angle and height of the Dashboard to better fit the operator by mounting directly onto a test frame via a t-slot mounting bracket.
When mounting it to a single column frame, mounting the Dashboard onto the frame saves up to 55% of benchtop space, up to 31% for dual column table models and up to 16% on floor models. This enables the user to create a healthier environment by permitting operators to be spaced further apart.
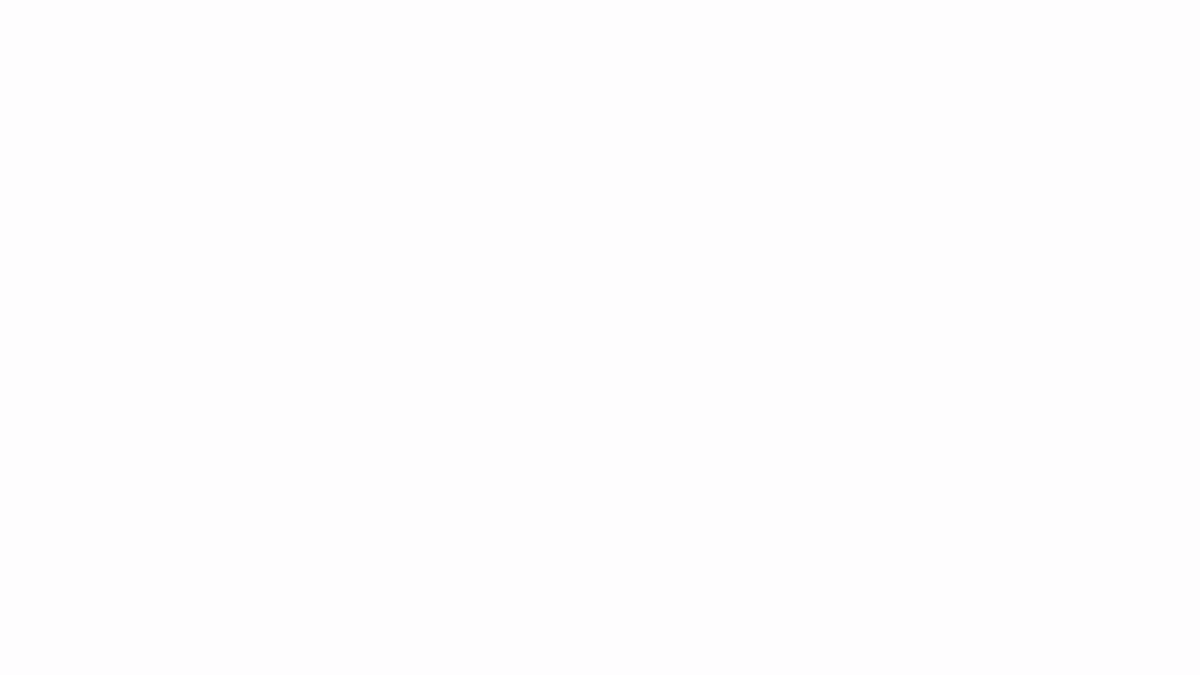
Image Credit: Instron - USA
Automatic Specimen Measurement Devices
In the lab, sharing equipment like micrometers or calipers can lead to a significant source of cross-contamination. Setting up a dedicated automatic specimen measurement device (ASMD) station at each of your Instron systems is one solution to this problem.
ASMDs can also be configured with a footswitch, which enables operators to input all specimen measurements straight into the software with a foot tap instead of by hand.
Automatic Specimen Measurement Devices Integrated with Bluehill® Universal
Video Credit: Instron - USA

Image Credit: Instron - USA
Equipment Add-Ons
Equipment add-ons, such as the Automated XY Stage and the Torsion Add-On 3.0 serve two key purposes: improving efficiency and expanding the testing capabilities of a system.
A user can often consolidate the equipment footprint in a lab by expanding the testing capabilities of a system, improving social distancing, and creating more space.
Torsion Add-On
In order to enable simultaneous (or non-simultaneous) axial and torsional testing, the Torsion Add-On 3.0 is an accessory that can be added to any 5900 or 6800 table model (dual or single column).
Performing torsional and axial testing on the same frame can be advantageous, as it enables the user to eliminate the extra steps needed to run the tests on separate systems while better simulating real-world applications of certain products.
Usually, if these tests were performed on separate testing systems, a standard tensile test frame and a torsion test frame would be required. If these are spaced six feet apart, they could take up as much as 13 feet of benchtop space.
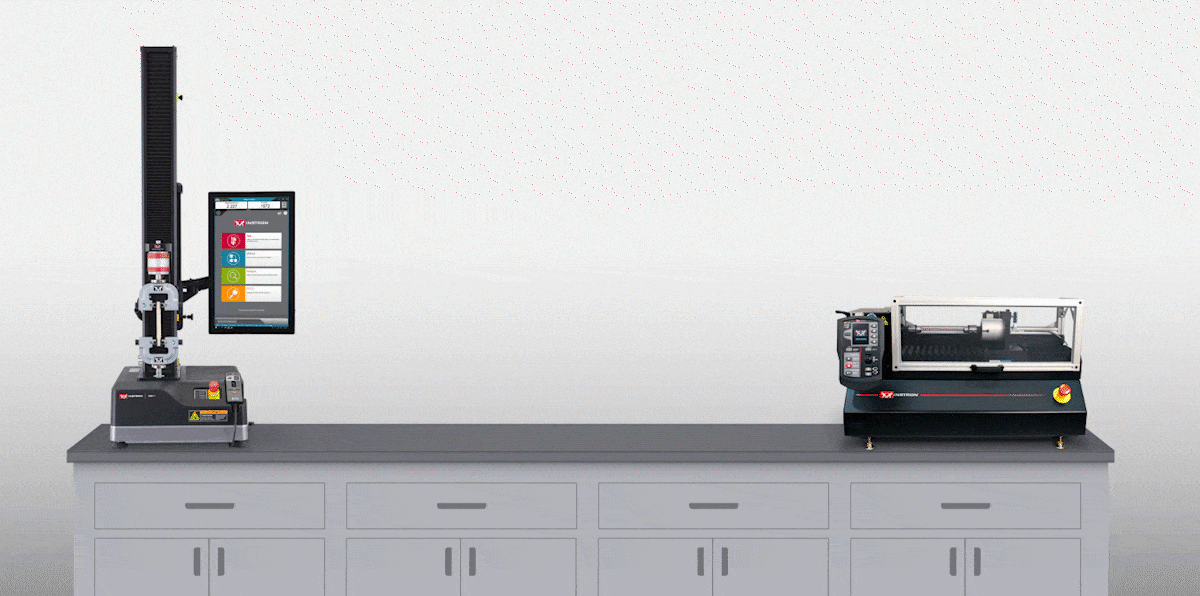
Image Credit: Instron - USA
By equipping a 6800 Series Dual Column table model with the Torsion Add-On 3.0, only 30 inches of benchtop space would be taken up, which is a reduction of 528%.
Automated XY Stage
Another add-on for 5900 and 6800 Series table models (dual or single column) is the Automated XY Stage. By increasing the functionality of a single system, it can decrease the benchtop space being used.
This add-on is utilized for automating flex, compression and tension tests on devices with numerous test points or multiple components with repetitive test points. This level of automation enables one operator to run multiple systems at the same time, decreasing the number of operators required in the lab to maintain testing throughput.
Equipping two test systems with an Automated XY Stage creates throughput capabilities comparable to three standard test systems. Again, three standard single column systems would account for at least 16.5 feet of benchtop space if they were spaced at least six feet apart.
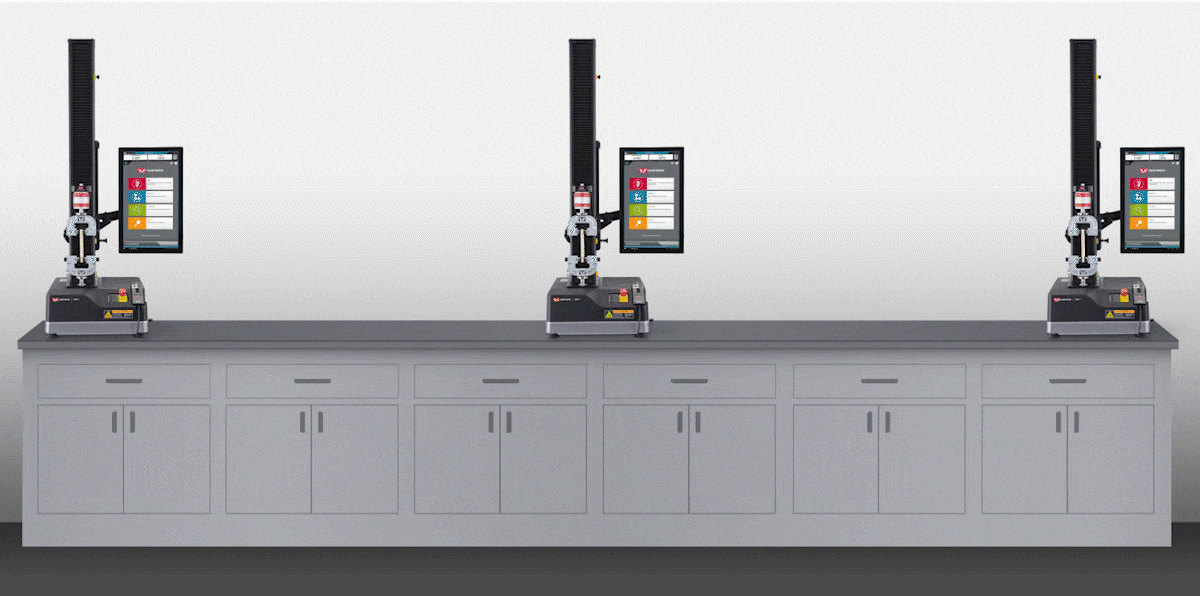
Image Credit: Instron - USA
In contrast, if two single column systems were equipped with Automated XY Stages and spaced six feet apart, they would only take up around nine feet of benchtop space, a reduction of 45% with the added advantage of fewer operators in the lab.
Automation Systems
A number of steps in the testing process can now be carried by some form of robot or non-robotic automation. The more automation in the process, the less hands-on work must be carried by a human operator, decreasing the risk of cross-contamination in the lab.

Image Credit: Instron - USA
All of the below steps in the testing process can be carried out by a robot:
- Extensometer operation
- Data output to database / LIMS
- Data input via barcode
- Specimen loading and removal
- Specimen dimensional measuring
- Grip operation
- Video extensometer dot marking
Automation is made up of a wide range of features that do not all need to be used together. Some labs might rely on a robotic system to automate almost everything, while some may only automate a few of these steps while still relying primarily on human operators.
The more a lab can automate, the less an operator is required to be around the testing system.
For instance, Instron's AT6 robotic test frame can be set up so that all the operator has to do is reload new specimens into the specimen racks while the system carries out the rest of the testing process. The operator can then leave the lab to focus on more value-added tasks or even leave the office to work from home.

This information has been sourced, reviewed and adapted from materials provided by Instron - USA.
For more information on this source, please visit Instron - USA