At odds with traditional energy resources, experimental energy resources such as Shale Oil, Shale Gas, Tight Oil, Tight Gas, and Methane Gas in a coal bed are distributed extensively in the tiny cracks and fissures of a shale reservoir, known as grikes.
In preparation for increasing the recovery rate of atypical energy resources, it is crucial to carefully examine the structure of the fine pores in the shale reservoir.
Using a Scanning Electron Microscope (SEM), mineral distribution and pore structure can be observed in the mechanically polished slice of a specimen from a traditional reservoir.
Yet, it is difficult to monitor the pores in an unconventional reservoir due to the fact they are vulnerable to damage throughout the polishing process.
The surface of the specimen of the unconventional reservoir is pre-treated by the FIB (Focused Ion Milling) system and examined with SEM, but using this method means that only a small area of the specimen can be pre-treated and analyzed.
For this purpose of this experiment, a new measurement method was developed utilizing a Coxem CP-8000 Ion Milling System to pre-treat a large area and used a Coxem SELPA (Scanning Electron Microscope Particle Analysis System) to inspect the pore structure, as shown in Figure 1.
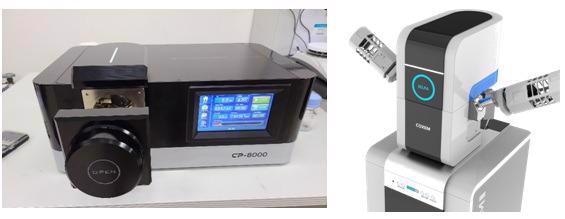
Figure 1. CP-8000 Ion Milling System and Coxem SELPA Particle Analysis System. Image Credit: COXEM Co., Ltd.
Experimental Method
As illustrated in Figure 2, an A-068 borehole was drilled and used in Besa River formation. The primary composition of the A-068 borehole sample is comprised of Calcite, Dolomite, Illite, Muscovite and Quartz, as identified by XRD measurements.
TOC (Total Organic Carbon) is broadly distributed and averages ~0.37 wt%. Utilizing a Coxem SELPA’s automation features to speed-up mapping processes and distribution measurement, core samples were mounted and then analyzed on the SELPA.
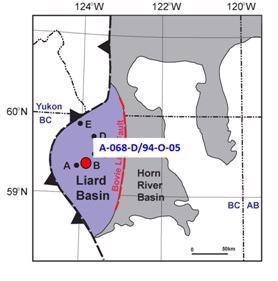
Figure 2. Location of A-068-D/94-O-05 core sample. Image Credit: COXEM Co., Ltd.
Results and Discussion
While observations of the pores in the nanometer scale can be seen utilizing SEM, analysis can only be completed over a small area of the specimen at any given time. This makes establishing the overall pore distribution a difficult task, as exhibited in Figure 3. SELPA provides accelerated analysis across a much greater area, as illustrated in Figure 4.
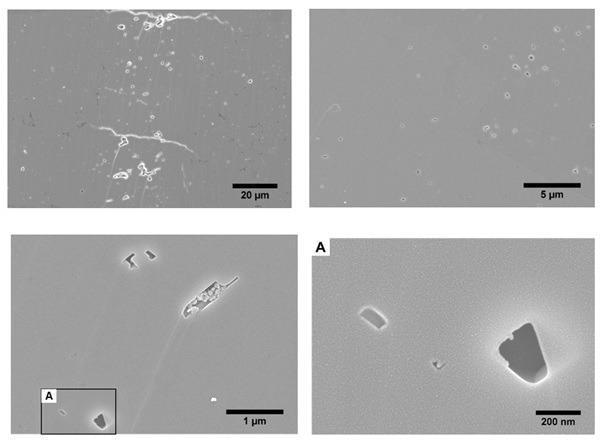
Figure 3. Secondary Electron Image of intraparticle pores of shale sample A-068-134, shown at four different magnifications. Image Credit: COXEM Co., Ltd.
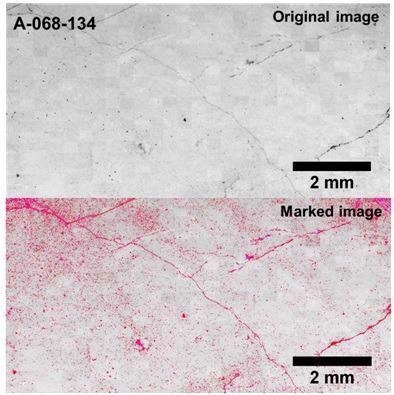
Figure 4. Composite tiled image obtained using SELPA. SELPA allows rapid imaging over a much larger area and pores are automatically identified and marked. Image Credit: COXEM Co., Ltd.
In this instance, over a time period of 1 hour and 29 minutes, a total of 513 fields were analyzed, covering an area totaling 5.04E+07 µm2. Figure 5 demonstrates the 58,729 singular characteristics that were detected, analyzed, measured, and mapped.
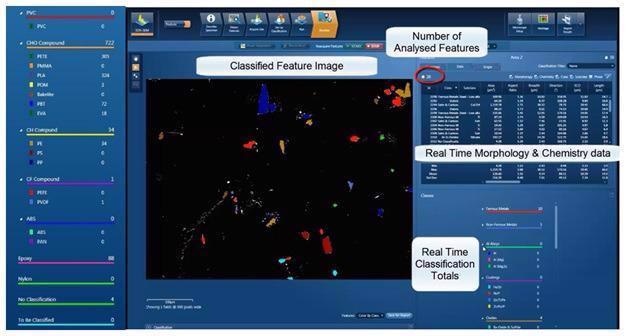
Figure 5. Utilizing Automated Feature Analysis, pores are scanned, identified, and classified simultaneously. Image Credit: COXEM Co., Ltd.
Additionally, as well as the ability to study the morphology of singular pores, SELPA offers a high-speed method for identifying both the size and distribution of the pores in the specimen.
In the highly carbonated sample A-068-134, it was established that ~30% of the pores are below 1 µm, ~35% of the pores are 1-2 µm and 14% of the pores are between 2 µm and 3 µm. This shows that the bulk of pores are below 3 µm, as seen in Figure 6.
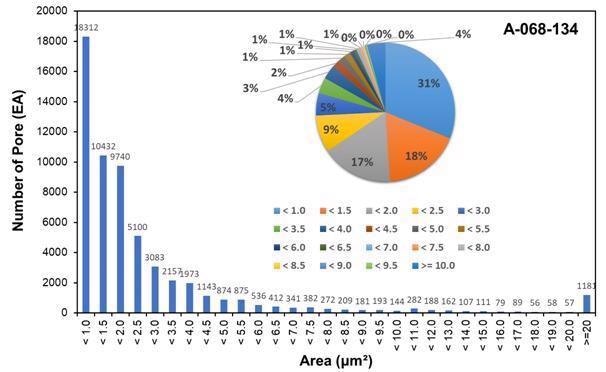
Figure 6. Distribution characteristics of pore area of the shale sample from Liard Basin. Image Credit: COXEM Co., Ltd.
When identifying pore size and distribution, equal significance should be given to sample preparation as is to the actual measurement. While traditional mechanical polishing techniques can ruin the sample surface, making analysis more complicated, Ion Milling maintains the sample integrity in order to provide precise measurements.
Traditional SEM analysis is accurate but also tends to be tedious and time-consuming. The entire process can be sped up by SELPA due to automation of the image stitching and thus automatically counting, measuring, and mapping pores within the shale sample. Resource recovery teams can then utilize this information for optimization of the gas recovery rate.
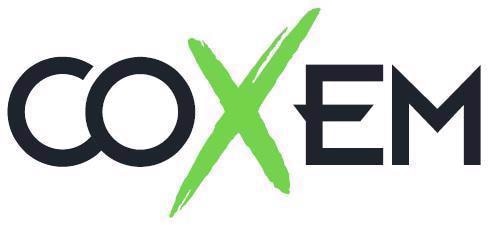
This information has been sourced, reviewed and adapted from materials provided by COXEM Co. Ltd..
For more information on this source, please visit COXEM Co. Ltd..