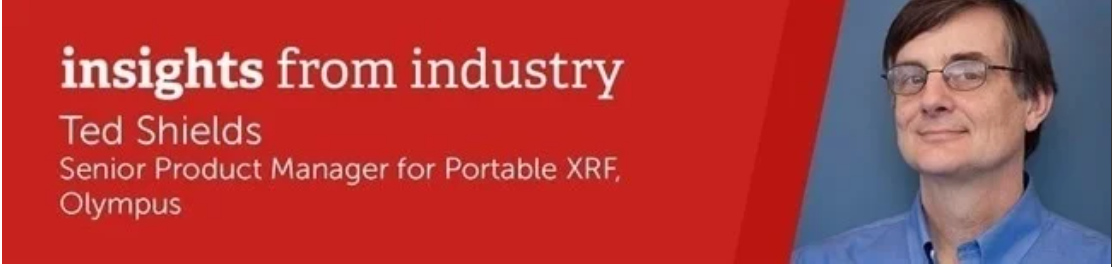
AZoM recently spoke with Ted Shields from Olympus about the new Vanta™ iX in-line XRF analyzer—a versatile system that automates material and alloy identification on the manufacturing line. Ted highlights the system benefits and explains the importance of in-line, automated XRF testing in metal fabrication and geo processing.
Why should someone consider the Vanta iX in-line XRF analyzer?
The Vanta iX analyzer can add value and reduce reworks in the inspection process since it verifies that a test material is what it is supposed to be. Nothing beats the confidence derived from 100% automated inspection. In-line, automated XRF eliminates the mistakes made by inspector fatigue or human error. In fact, one of our customers did a study and found that 100% manual inspection only caught 66% of the errors.
Olympus has made a name for the Vanta handheld XRF series thanks to its high throughput, stability, and count rate. How does the Vanta iX analyzer incorporate these features, and how does it differ from the handhelds?
For the Vanta iX analyzer, we kept the heart of the analytical engine—our ability to count X-rays. Our in-line clients benefit from years of development we did on the handheld front. We then added the features needed for production facilities (e.g., inputs and outputs for PLC control, easy mounting surfaces, and a sturdy metal enclosure) to build a rugged system that is simple to integrate and control.
The Vanta iX analyzer is ideal for geo processing. What features benefit this application?
Several clients have integrated the Vanta handheld analyzers into core logging equipment. They chose the Vanta series because of its outstanding analytical capability but needed to make engineering efforts to overcome the limitations inherent in the handheld form factor. With the Vanta iX analyzer, integration is much simpler.
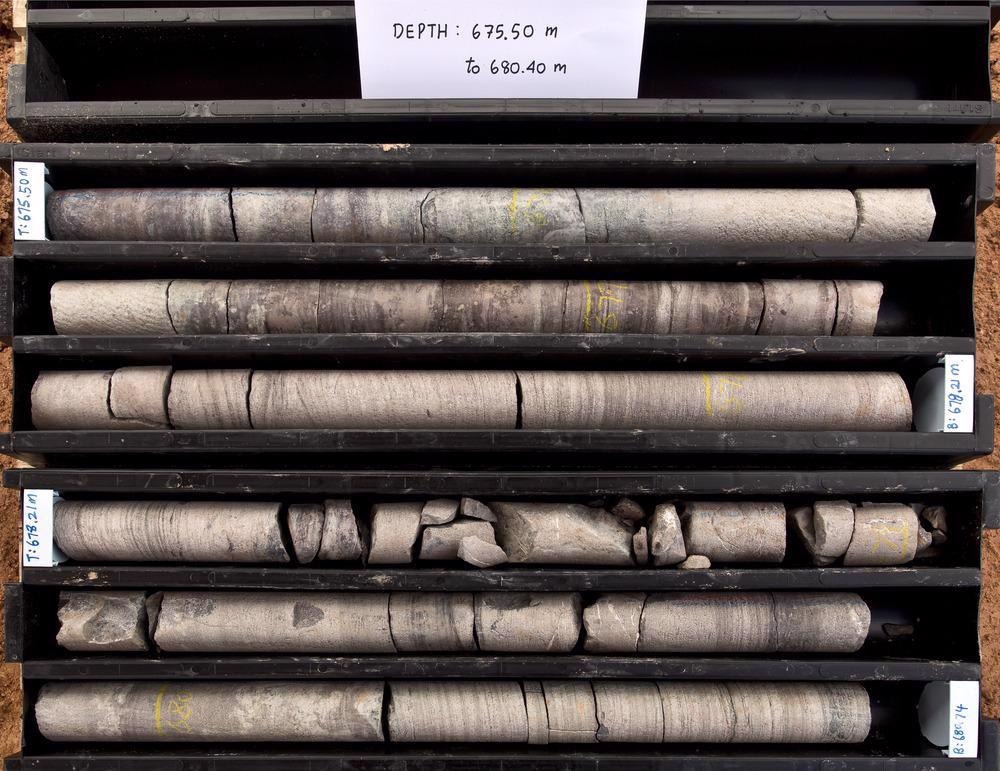
The Vanta iX analyzer is ideal for geo processing. Image Credit: Shutterstock.com/ribeiroantonio
What other applications is the Vanta iX analyzer suitable for?
I expect the most common application for the Vanta iX analyzer will be the verification of metal alloys in production. Steel or metal manufacturers that make different materials with each batch can use the analyzer to make sure that the materials do not get mixed up. Or they can verify the chemical content as parts are made. If the material composition is vital to the part’s function, then you want to check the composition before you put in the effort to machine and assemble the part.
How do the Vanta iX analyzer’s inspection capabilities give metal fabricators a competitive edge?
Some obvious savings are due to the prevention of mix-ups and any potential liability from shipping the wrong material. Anyone who has had to deal with the fallout from a material mix-up knows how costly that can be. Also, customers of metal fabricators increasingly want to know that their part is made from the right material. Historically, this was done at (or even after) installation. Customers are pushing this requirement up the supply chain, so a manufacturer with 100% inspection and analysis of outgoing material has a competitive advantage.
Tell us about the Vanta iX integration options and how this flexibility benefits users.
We built in as much flexibility as we could for the integration process. First, we provided options on how to power it—DC power or Power over Ethernet. The next area is control. You can use a traditional PLC and hard-wired voltages to inputs/outputs or use the more modern, flexible API command set. We support either option because the XRF instrument should not dictate the system that the rest of your plant runs on.
How do the versatile communication and data transfer options make the analyzer easy to control?
Olympus developed a complete WebSocket API for the Vanta iX analyzer. It contains the full set of commands to control the analyzer. Anything a person can do from the screen of a handheld XRF analyzer, the API can do from the control room of a factory.
What types of results can be configured using the Vanta iX analyzer?
The Vanta iX analyzer can be configured to return simple pass/fail results, answering the question: “Does this result match what this part is supposed to be?” The analyzers can also return a grade identification or a complete chemical analysis. The right configuration depends on the information needed for your process.
The Vanta iX analyzer is built to be rugged and durable. What environments can it be used in?
We tested the Vanta iX analyzer to run continuously in temperatures up to 50 °C (122 °F). If your environment is hotter, we can add fans or water jackets to cool the instrument. Testing hot samples calls for some requirements on the instrument’s analysis window, but we have the options and experience to cover that too. Our testing also included immunity to industrial electromagnetic noise and vibration. Finally, the Ethernet connection provides a robust communication channel over distance compared to older communication methods.
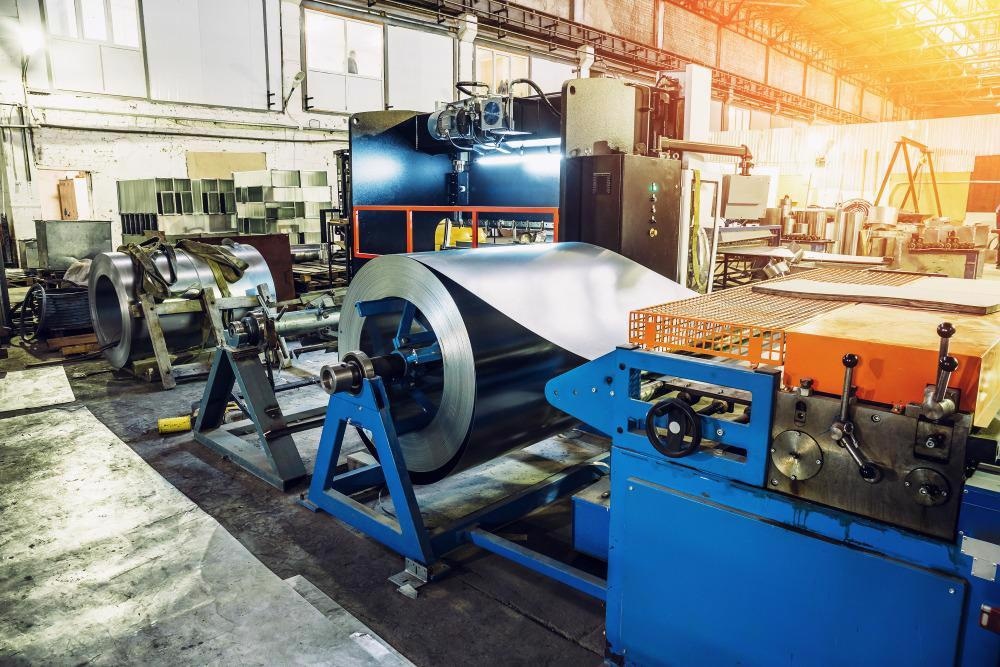
The Vanta iX analyzer’s inspection capabilities give metal fabricators a competitive edge. Image Credit: Shutterstock.com/DedMityay
How is the Vanta iX analyzer designed to provide easy repairs?
Our strict quality procedures at Olympus make one Vanta iX analyzer very much like another Vanta iX model. This means that in the event of a service need, the user can just unplug one analyzer, swap in another, reconnect the cables, and continue their work. Typically, there is no need for a site-specific calibration on the new probe or specialized skills. With a spare Vanta iX analyzer and a straightforward procedure, the user’s maintenance team can almost eliminate downtime.
How does the Vanta iX analyzer compare to other systems in the market?
There are not many comparable instruments that are purpose-built for integration. On one hand, there are many handheld analyzers. But we know from firsthand experience the challenges that come with integrating instruments designed for continual human intervention. On the other hand, there are larger cross-belt systems. Yet they are more expensive and bulkier than the Vanta iX analyzer and are really designed for large conveyor belt ore operation.
Where is the future of XRF analysis going, and how will Olympus be a part of it?
Olympus is committed to moving the XRF field in its practical uses outside of the laboratory. Scrap metal dealers, exploration geologists, RoHS compliance officers, and oil/gas positive material identification specialists have long known the value of XRF in the handheld form. I believe the value of knowing the composition of your material will become more obvious to the manufacturing sector. Terms like “Industry 4.0”, “100% inspection”, and “full material verification” are common when we read about the industry, showing its potential to benefit from the automation of Vanta iX in-line XRF analysis.
Where can readers find more information?
To learn more about the Vanta iX in-line XRF analyzer, visit Olympus-IMS.com/Vanta-iX or contact a local Olympus sales representative. And be sure to read our recent blog post, 9 Reasons to Automate Material Analysis with the Vanta iX In-Line XRF Analyzer.
About Ted Shields
Ted Shields is the Director of Product Management, Analytical Instruments at Olympus and has worked in the XRF field for over 13 years. As a Product Manager, he oversaw the introduction of the Vanta handheld XRF analyzer series that has led to the continual growth of XRF sales and market share for Olympus.
Disclaimer: The views expressed here are those of the interviewee and do not necessarily represent the views of AZoM.com Limited (T/A) AZoNetwork, the owner and operator of this website. This disclaimer forms part of the Terms and Conditions of use of this website.