Fabrication of 3D NAND devices involves a challenging and complex deposition and etch process. Two etch processes have been identified as substantially impacting 3D NAND product yields: silicon nitride sacrificial removal and W etch-back in the 3D NAND word-line formation.
This article investigates an automated online chemical management system that has been specifically developed to facilitate real-time monitoring and control of both the sacrificial silicon nitride removal and W etch-back processes.
A central challenge in 3D NAND is the effective scaling of stack height to ensure higher bit density. While 2D planar NAND is limited by lithography, bit density of 3D NAND is constrained by complex deposition and etch process steps while vertically stacking the NAND structures.
3D NAND fabrication starts with multi-layered silicon nitride and oxide deposition. This is followed by a high aspect ratio hole etch for the word-line and channel. The silicon nitride utilized in the word-line is a sacrificial layer.
This is eliminated by immersion wet-etch, followed by a dielectric (ONO) and tungsten metal gate, deposition and finally etch-back.1
Silicon nitride sacrificial removal and W etch-back have been identified as the two critical steps in this process flow. Each of these steps requires accurate real-time process control and metrology.
Critical Wet Etch Processes
Sacrificial Silicon Nitride Etch Using Hot Phosphoric Acid
The use of hot phosphoric (Hot Phos) acid to etch silicon has been used in semiconductor manufacturing for many years and is well understood.
Control of nitride and oxide etch rates involves effective control of temperatures and water content in H3PO4. Seasoning the Hot Phos etching bath with silicate also results in further reduction of the etching rate of SiO2 as well as improvements in etch selectivity.
It is theoretically possible to achieve critically high etch selectivity by seasoning the H3PO4 with a high concentration of silica.
Dynamic bath loading behavior and etch by-products mean that maintaining a stable etch process with exceptionally high etch selectivity over time is particularly challenging without the use of real-time monitoring and control.
The ability to reliably monitor and control Si in real-time is also important in the prevention of process induced defects resulting from Si precipitation.
ECI has established a suite of methods2,3 for the accurate analysis of Hot Phos etch bath components, enabling stable and reliable control and monitoring of the etch process.
These methods facilitate a reliable and stable etch process throughout the whole lifetime of the etching solution while improving feed, bleed and cost savings, ultimately extending the lifetime of the etching baths.
Real-time results can be obtained using the methods applied in ECI’s automated online system QUALISURF QSF-500 (Figure 1).
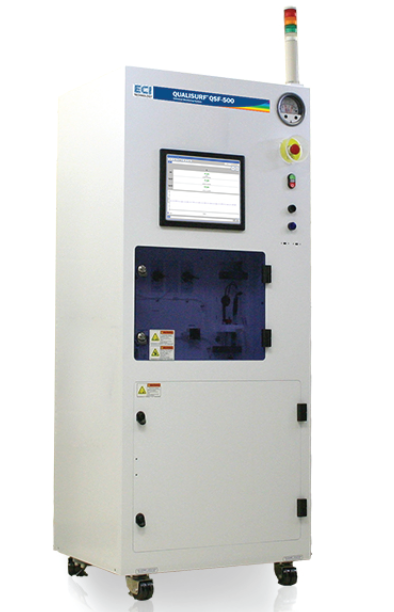
Figure 1. QUALISURF®QSF-500 wet process chemical monitoring system. Image Credit: ECI Technology
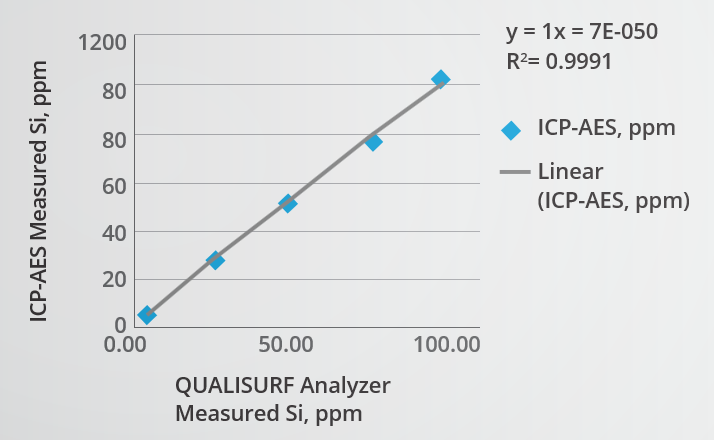
Figure 2. Comparison of measured Si vs. ICP-AES. Image Credit: ECI Technology
Real-time results were measured and compared with off-line Inductively Coupled Plasma Atomic Emission Spectrometry (ICP-AES) (Figure 2) in order to confirm that they were accurate.
The seasoning and etch experiments outlined here have successfully demonstrated the accurate monitoring and control capabilities of the Hot Phos silicon nitride etch process. Results of these experiments are displayed in Figure 2 and Figure 3.
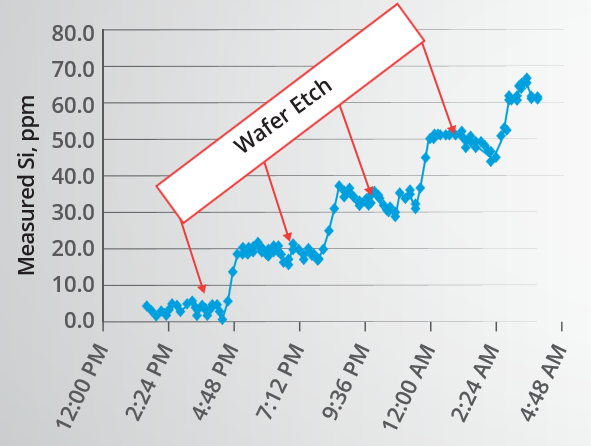
Figure 3. Seasoning process. Image Credit: ECI Technology
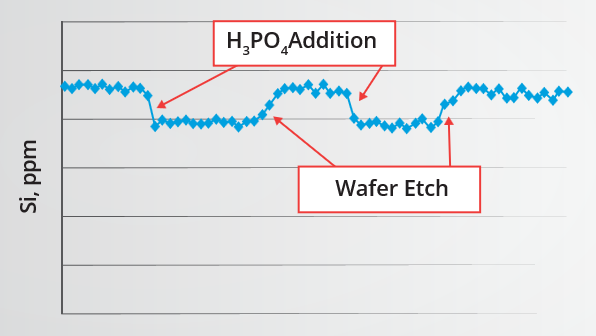
Figure 4. Monitoring Si during “Feed and Bleed,” etch process. Image Credit: ECI Technology
Seasoning Process
PAN Tungsten (W) Etch
PAN (Phosphoric-Acetic-Nitric acid) is commonly used when a well-controlled selective etch of aluminum over Si or SiO2 is required. PAN is also an option for W etch-back during the 3D NAND process.
Like aluminum etch, W also oxidizes in the nitric acid forming a by-product (W(NO3)x) which will dissolve in the phosphoric acid. The acetic acid in PAN facilitates the etch process by acting as a wetting agent, therefore removing the H2 by-product.
The concentration of H3PO4 increases over the PAN solution’s lifetime. This is due to the evaporation loss of nitric/acetic/H2O. H3PO4 concentration should be controlled if a stable, consistent etch rate of W is to be maintained. Inconsistent etch of W will cause 3D NAND devices to short, particularly when W under-etches (Figure 5).
ECI has developed an online automated chemical management system capable of accurately monitoring and controlling PAN components. Different concentrations of H3PO4 were added into the bath during a spiking experiment, and the system was able to accurately measure the H3PO4 component concentrations (Figure 6).
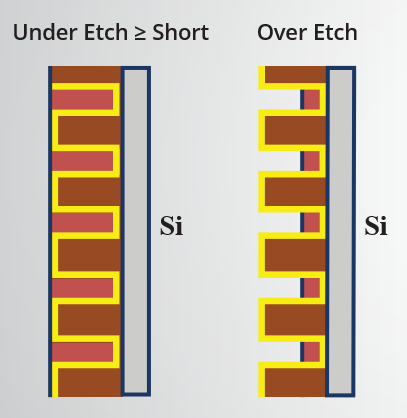
Figure 5. Tungsten (W) under and over-etch. Image Credit: ECI Technology
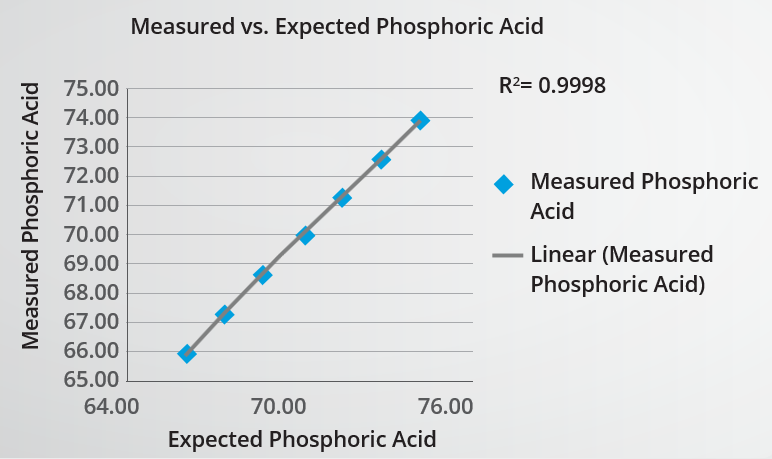
Figure 6. PAN spiking experiment showing matched results of measured and expected. Image Credit: ECI Technology
Conclusion
Continuing demand for a higher bit density in 3D NAND will push fabrication process and stack height limits. Monitoring and control of this process are increasingly important as the quantity of stacking layers increases.
This article outlined the results of real-time online automated solutions and their ability to accurately monitor and control Si3N4 and W etch.
References
- J.H. Jang, H.S.Kim, W.Cho and W.S.Lee, “Vertical cell array using TCAT (Terabit Cell Array Transistor) technology for ultra-high density NAND flash memory,” IEEE Symposium on VLSI Technology, page 192-193 2009.
- ECI Technology, Inc. Press Release, “QualiSurf Qualifies in Japan and Taiwan Fabs”, Totowa, NJ, Feb 2, 2012.
- C. N. Bai, G. Liang, E. Shalyt, “Metrology for High Selective Silicon Nitride Etch”, Solid State Phenomena, Vol. 255, pp. 81-85, 2016.
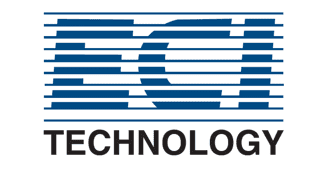
This information has been sourced, reviewed and adapted from materials provided by ECI Technology.
For more information on this source, please visit ECI Technology.