Cyclic voltammetry stripping (CVS) is widely recognized as a potent tool for monitoring concentrations of organic additives in plating baths.
Concentrations of additives in the plating bath have a considerable impact on the deposit’s ductility, tensile strength, and solderability. Regular and ongoing CVS analysis of organic additives can help ensure continuous, problem-free operation.
Information on the plating bath provided by CVS is more objective than that of a Hull Cell. While a Hull Cell provides a qualitative indication of the condition of the bath, CVS allows the plater to precisely replenish additives, thus ensuring the bath continues to operate properly.
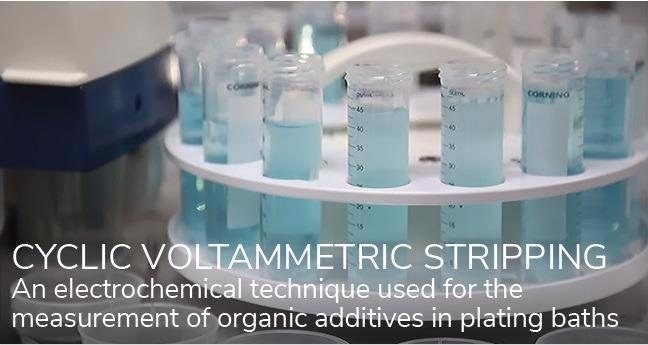
Image Credit: ECI Technology
CVS Analysis
CVS is an electrochemical technique utilized in the measurement of organic additives in plating baths. CVS is centered around the impact of additives on the electroplating rate –- the activity of any type of organic additive (leveler, brightener, grain refiner, etc.) will be reflected in a change in the plating rate.
Analysis is undertaken in an electrochemical cell utilizing a three-electrode system. One of these electrodes is a platinum rotating disk electrode, and the potential of this electrode is controlled by the instrument during measurement.
Potential is scanned at a constant rate, switching back and forth between the electrode’s negative and positive voltage limits.
A minimal amount of metal from the plating bath will be plated onto and then stripped off the working electrode as the potential changes. Throughout the scan, the current at the working electrode is measured and recorded as a function of potential. Additive activity will impact the plating rate of the metal onto the electrode.
Plating rate is established by calculating the charge necessary to strip the metal off the working electrode. The relationship between the stripping charge and the activity of the additives can therefore be utilized to quantitatively measure additives and their components.
Fresh additive is used as a standard. This is used as supplied by the manufacturer, and the additive’s activity in the production bath is stated as a concentration (ml/l) of fresh additive.
ECI Technology’s QUALILAB® Elite Plating Bath Analyzer is able to perform the patented CVS analysis automatically. QUALILAB analyzers have been specifically designed to analyze plating baths.
The user is guided through comprehensive analytical procedures, and the analyzer performs appropriate calculations before reporting active concentrations of additives present in the bath.
Using CVS for Plating Bath Analysis
Figure 1 displays an example voltammogram (plot of the measured current vs. applied potential) for an acid copper plating bath.
The image in Figure 1 is a display from the QUALILAB Plating Bath Analyzer. Within this image, potential governs the electrochemical reaction that occurs.
Potential is displayed on the X-axis, with potentials becoming increasingly positive from left to right. A positive-going potential will become more strongly oxidizing, while a negative-going potential will produce a more strongly reducing condition.
Current is displayed on the Y-axis. Here, a positive current corresponds to oxidation, while a negative current is the result of a reduction.
The voltammogram has multiple regions of interest. These are outlined below.
Plating Region: Points 1 to 2 and 2 to 3
As the platinum electrode is plated with metal, the current is negative in this region. Because plating time is robustly defined by the scan rate, the plating rate in this region can be accurately estimated as the amount of metal plated in the plating region.
Cleaning Region: Points 4 to 5 and Back From 5 to 6
A positive potential on the electrode is employed to desorb organics, as well as to clean the platinum electrode’s surface. This cleaning segment is essential if accurate and reproducible results are to be ensured when using CVS.
This region is also commonly used to monitor chloride levels and oxidizable organic contaminants in acid copper baths.
Stripping Region: Points 3 to 4
The metal is stripped off the electrode as its current becomes positive. The area of the stripping peak signifies the charge needed to strip any deposited metal.
The instrument works by integrating the current in order to measure the area underneath the stripping peak. This area is reported in milli-Coulombs (mC) and is displayed in the box on the lower right of Figure 1.
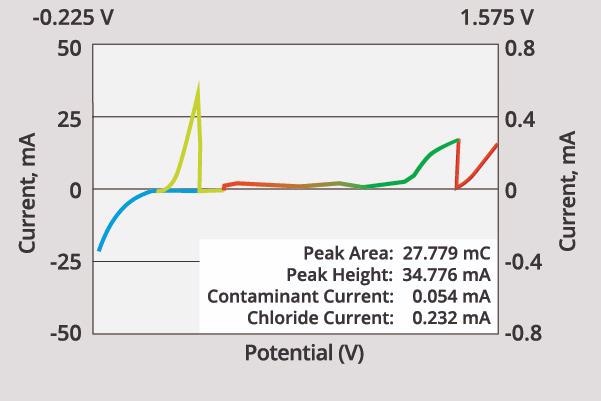
Figure 1. A typical CVS voltammogram for an acid copper plating bath. Image Credit: ECI Technology
Because the stripped metal quantity and the plated metal quantity are equal, the stripping peak area is proportional to the volume of metal plated.
It is, therefore, more accurate to measure the quantity of metal plated via integration of the current in the Stripping Region as opposed to the Plating Region.
Other electrochemical processes could also be occurring in the Plating Region, for example, hydrogen reduction.
Adsorption Region: Points 5 to 6
Organic additives are adsorbed onto the electrode surface in this region, despite there being no metal plated. Adsorption occurring in this region improves the sensitivity of CVS.
Figure 2 displays the influence of a number of organic additives on the plating rate. Additives such as wetters or levelers will generally function as suppressors, decreasing the plating rate.
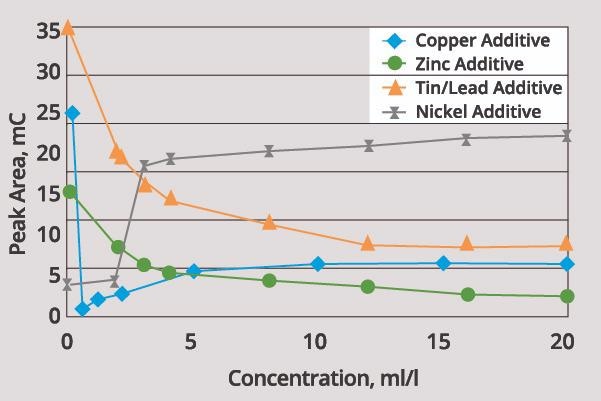
Figure 2. Effect of some organic additives on the plating rate of metals. Image Credit: ECI Technology
Brighteners, on the other hand, will increase the deposition rate. It should be noted, however, that there is no standard terminology for additives within the industry, meaning that care should be taken at all times.
Organic additives undergo a range of chemical transformations, including oxidation, fragmentation, reduction, and polymerization during the electroplating process. The majority of the products of these transformations will also impact the plating process.
CVS affords users with measurements of the effective concentration of additives. Effective concentration is best understood as the activity of the additive in terms of the fresh additive.
This is more relevant than the concentration of a particular substance. However, many analytical techniques such as HPLC and spectroscopy will measure absolute concentration.
This transformed additive will continue to be electroactive, but it will not be responsive to spectroscopy or vice versa. Since CVS is based on the plating process, it remains the only viable technique for users looking for a true measure of the activity of organic additives.
Determination of Additives and Their Components
Quantitative determination of organic additives is centered on the CVS response of the production bath prior to and following the addition of an established amount of a particular standard. Fresh additive is used as the standard, and this is used as supplied by the manufacturer.
Because the fresh additive is utilized as the standard, the concentration of the additive in the production bath will be expressed as equivalent activity of the fresh additive. Replenishment of the bath to the appropriate additive level is highly convenient due to this approach.
It is generally possible to quantify every additive in the plating bath. Figure 3 displays an example of this, using an acid copper bath.
The carrier functions as a suppressor, inhibiting the rate of the plating process. This is evident in the reduction in peak area observed as the carrier’s concentration is increased.
It should be noted that the activity of the carrier is very high, and even a minimal increase in concentration has a significant impact on the plating rate. Fresh carrier (as supplied by the manufacturer) was used to spike the solution in this example.
Plating rate changes considerably as the amount of carrier is increased from 0-1 ml/l. Once carrier concentration is increased beyond 1 ml/l, however, there is little additional impact on the rate of plating.
The impact of brightener is different, however. Increased brightener concentration prompts an increase in plating rate when in the presence of the carrier.
Activity of the brightener is lower than that of the carrier, meaning that the difference in activity between carrier and brightener can be employed to quantify each component.
A number of manufacturers are able to provide a pre-mixed solution that contains both the brightener and the carrier. Figure 3 provides an example of this, whereby these components can be clearly distinguished.
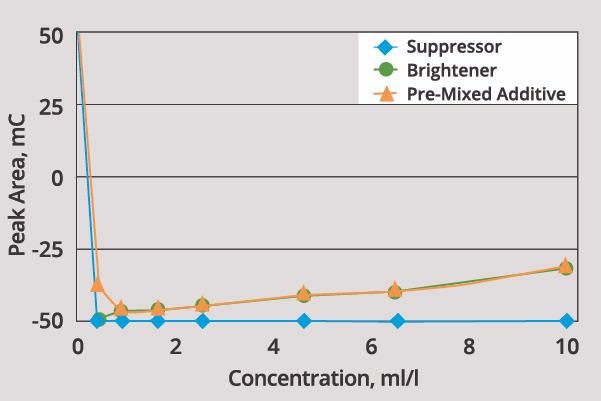
Figure 3. CVS response of carrier and brightener in acid copper bath. Image Credit: ECI Technology
CVS can be utilized to confirm that the brightener and carrier remain in balance within the production bath.
Analysis of plating baths using CVS greatly benefits from the leveraging of appropriate experience. ECI Technology has invested more than 15 years in the development of CVS methods for a wide range of plating baths.
As well as manufacturing CVS instrumentation, ECI Technology remains an industry leader in the provision of CVS application information. All users of ECI Technology products can benefit from this CVS consultation.
Outgoing and Incoming Inspection of Additives
CVS is a robust tool highly suited for the outgoing inspection of additives by suppliers and the incoming inspection of additives at users’ sites.
Figure 4 provides an example of the extent of variations between multiple lots of the same brightener. Thankfully, the user in this example was able to avoid underdosing or overdosing the brightener and losing control of the bath by performing a rapid, straightforward assay.
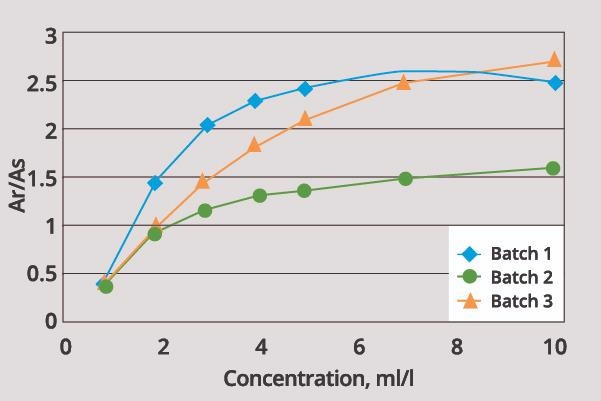
Figure 4. Variation in response of different lots of the same additive from the same manufacturer. Image Credit: ECI Technology
The Industry Standard
CVS was initially developed in the late 1970s and has experienced enormous growth since that time, significantly contributing to the work of both suppliers and users of plating chemistries.
This patented technology is currently employed by almost every major chemistry supplier for routine analysis or quality control of customers’ baths.
ECI Technology remains the primary driving force behind the development and application of CVS. The company’s CVS instrumentation and analytical procedures have been essential to the continued growth of CVS.
Many companies and organizations use CVS instrumentation from ECI Technology, including the most trusted manufacturers of semiconductors and printed wiring boards such as IBM, Texas Instruments, Motorola, Intel, Northrop, Tyco, Photocircuits, Sanmina and more.
CVS is found in plating laboratories in the Americas, Asia and Europe.
The innovative engineering of ECI Technology was also recognized by an R&D 100 Award.
Applications of CVS
It is important to keep the chemistry in balance when looking to prevent plating problems by quantitative measurement of organic additives in plating solutions. CVS is highly suited for a number of key applications, including:
- Quantitative determination of additives and their respective components
- Individual fingerprinting of plating solutions
- Incoming and outgoing plating additive inspection
- Monitoring levels of contamination in plating solutions
- Scheduling baths for carbon treatment and optimization of this treatment
CVS is also an important technique in the study, development, and optimization of new plating technology. This includes:
- Studying the impact of numerous plating process parameters process on plating solution performance; for example, the concentration of additives, current density, mass transport, and temperature
- Studying the consumption and transformation of additives throughout the plating process
- Studying the impact of different additives on the plating process
References
- Cyclic Voltammetric Stripping (CVS) is a patented technology.
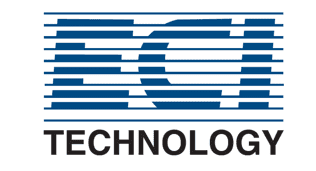
This information has been sourced, reviewed, and adapted from materials provided by ECI Technology.
For more information on this source, please visit ECI Technology.