Selecting the appropriate condenser for an evaporator system is a key decision as the glass condenser is a foundational component when acquiring a new rotary evaporator system. The diversity of glass condensers available can more or less be divided in two main sections: dry ice condensers and condensers with cooling coils.
Condensers with colling coils operate using a tap water connection, or in combination with a recirculating chiller. Both variants have their advantages and disadvantages that must be considered for the purchase decision.
This whitepaper sets out to compare the handling and performance of a Heidolph G5 dry ice condenser and a Heidolph G3 XL cooling coil condenser combined with a recirculating chiller .
Reasons and Beliefs for Using Dry Ice Condensers
Many researchers prefer the dry ice condenser because of the following reasons: There is no need to purchase additional equipment and the necessity to connect to a tap water source is eliminated.
Consequently, the evaporator system has a more compact footprint in comparison to a system with a recirculating chiller and there is no need for tubes to carry the cooling liquid, regardless of whether using tap water or a coolant. In addition, the use of a dry ice condenser does not necessitate primary energy consumption such as running a recirculating chiller.
One of the main elements of reason leading to the purchase of a dry ice condenser is that the colder the better – which is, in fact, not true. The glassware is often placed under great stress due to the high temperature variations present in an evaporator system with a dry ice condenser.
If the hot steam produced by a solvent meets a surface cooled to –78°C by a mixture of dry ice and isopropanol or acetone, the glass experiences a temperature difference of 118°C, assuming that the heating bath temperature is 40°C.
Although glass condensers are made using highly stress-resistant borosilicate glass, the high stress on the glass leads to a particularly greater tendency of glass breakage during the work with a dry ice condenser.
While advantageous for very low boiling solvents like diethyl ether, the very low temperature of a dry ice condenser can be a disadvantage if a higher boiling solvent needs to be evaporated because high boilers have the tendency to condensate too early, before making it to the condenser surface.
A performant use of a dry ice condenser with solvents that have a high vaporization temperature, like ethanol or water, is almost impossible.
Another major consideration is that operation over several hours or even overnight unattended is not possible with a dry ice condenser. This is due to the fact that constant refilling of dry ice is required to maintain the appropriate temperature and performance. If the evaporation process with a dry ice condenser is left unsupervised over an extended period of time, then there is a greater risk of the solvent used for the cooling mixture heating up and evaporating into the ambient air. This can cause intoxication and the danger of ignition.
Dry ice must be handled with care, otherwise skin burns and suffocation are a possibility. It is compulsory to wear protective gloves when working closely with dry ice. It is necessary to prepare the cooling mixture for every single use.
The condenser cannot be filled all at once due to the potential of a severe reaction between the dry ice and the solvent. This means each step must happen gradually to avoid spillage of the solvent used for the cooling mixture.
The dry ice condenser is capable of holding up to 800g dry ice per filling. This needs to be taken considered when looking at the acquisition costs of the system: The dry ice cannot be re-used as it sublimates during the process.
The solvent required for the mixture is largely disposed of because it tends to absorb ambient moisture which causes a reduction in performance after a few cycles. Dry ice and solvents cause running costs when using this type of system.
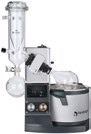
Image Credit: Heidolph North America
Condensers with Cooling Coils Provide a Broader Usage Spectrum
In contrast to the dry ice condensers, condensers with cooling coils, specifically high performance models that produce a large cooling surface, can be used with a wide range of solvents.
In combination with a recirculating chiller, precise temperature control that can be adjusted to the process is facilitated.
The expansive range of recirculating chillers to choose from, ranging from lower power levels like 250 Watts to high performance ones like 1200 Watts, mean that finding the appropriate model required for the process, running with the evaporator system, is possible.
This generates two significant advantages: it is very unlikely that glass breakages of a condenser with cooling coil, due to high temperature differences, will occur. Condensers with cooling coils typically run at a temperature between 15–5°C.
The temperature difference the glass is exposed to is reduced to 25–35°C, which the glass can easily withstand.
In addition, the evaporation of low boiling solvents like diethyl ether becomes as functional as the evaporation of exceptionally high boiling solvents like DMSO, due to the possibility of adjusting the cooling temperature in-line with the process to optimize the workload of the glass condenser.
It is also possible to leave the evaporator system with a recirculating chiller over extended periods of times, without losing performance efficiency or producing safety risks. The handling is simple – once fully installed it only has to be switched on and off again.
Some evaporator systems even have the capacity to control the temperature of the recirculating chiller via the evaporator’s control panel.
Post-purchase and installation, the operating costs are limited to the energy consumption of the system with a recirculating chiller. Therefore, it is a preferential choice compared to a setup where tap water is wasted. The cooling liquid can be recycled over long periods of time, since it is contained in a cooling cycle and has substances to inhibit the formation of algae.
Objective: Comparison of a Dry Ice Condenser and a High-Performance Condenser with Cooling Coils in Combination with a Recirculating Chiller
Heidolph has compared two variations of glass condensers with respect to their handling and performance: A Hei-VAP Expert Control evaporator system with a Rotavac Vario control rpm regulated vacuum pump was fitted with a G5 dry ice condenser and a G3 XL high-performance condenser with cooling coils combined with a Hei-CHILL 350 recirculating chiller.
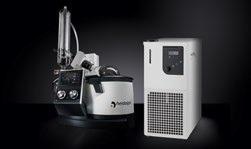
Image Credit: Heidolph North America
Method: Performance and Handling Comparison of a Heidolph G5 Dry Ice Condenser and a Heidolph XL Cooling Coil Condenser
The G5 dry ice glass set was fitted as identified on the Hei-VAP Expert Control evaporator system utilizing the silicone ring provided for sealing to ensure the best possible system tightness. A cooling mixture of dry ice and isopropanol was (temperature 78°C) was provided with the condenser.
The dry ice was refilled after every experiment. The G3 XL glass set with cooling coils was installed as noted on the Hei-VAP Expert Control evaporator system and fixed to a Hei-CHILL 350 recirculating chiller, filled with 20 l of Kryo 30 cooling liquid. The recirculating chiller was set to a temperature of 5°C.
The evaporation times were established as follows: The heating bath was filled up to the second fill line and the water then preheated to 50°C. The rotation and vacuum values were set as outlined to table 1. After the rotation was started and it reached the set value, the vacuum process commenced.
Table 1. Parameters for the determination of the evaporation times. Source: Heidolph North America
Solvent |
|
Set heating bath temperature |
Set rotation
speed |
Set vacuum value |
Water |
50 ml |
50°C |
140 rpm |
20 mbar |
Water |
250 ml |
50°C |
140 rpm |
20 mbar |
Ethanol |
50 ml |
50°C |
140 rpm |
60 mbar |
Ethanol |
250 ml |
50°C |
140 rpm |
60 mbar |
The flask was placed into the heating bath – 10 mb before the set value – and the time measurement with a stopwatch began. Once no solvent was visible in the flask, the measurement was stopped. (Characteristic: towards the end of the process a ring of solvent forms inside the flask which is initially clearly visible before fading. Time is stopped after the ring has faded).
A: Experiments with Water
Complete evaporation of 50 ml of water takes 6 minutes and 30 seconds. While the pump was not contaminated, ice crystals formed on the condenser due to the low temperature (Fig. 1). Because of that ice formation, it was only possible to recover 32 ml from the 50 ml of water
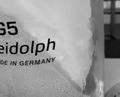
Figure 1. Ice crystals form inside the G5 condenser. Image Credit: Heidolph North America
Around half of the dry ice has sublimated just 6 minutes after commencing the evaporation of 250 ml water. After 14 minutes there are deviations in the vacuum starts and after 16 min all of the dry ice has completely sublimated. Shortly after the entire condenser is steamed up (Fig. 2).
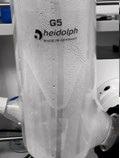
Figure 2. Completely steamed G5 condenser after 17 min water evaporation. Image Credit: Heidolph North America
The heat is no longer transported and the pressure continuously rises as the process stagnates. Condensate appears inside the tubing (Fig. 3), which is indicative of an insufficient cooling capacity.
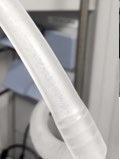
Figure 3. Condensate inside the tubes during water evaporation with G5 dry ice condenser. Image Credit: Heidolph North America
The heat of the condenser rises to the point that the isopropanol starts to reflux, therefore it was necessary to stop the process after 30 min. 5 ml water remained inside the pump, 15 ml was left in the flask meaning recovery of 230 ml.
Table 2. G3 XL cooling coil condenser vs. G5 dry ice condenser; evaporation times of water. Source: Heidolph North America
Parameters |
Time G3 XL |
Time G5 |
50 ml water
50 °C
140 rpm
20 mbar |
06:20 min |
06:30 min |
250 ml water
50 °C
140 rpm
20 mbar |
21:30 min |
cancelled after 30 min |
B: Experiments with Ethanol
Complete evaporation of 50 ml of water takes 6 minutes and 30 seconds. While the pump was not contaminated, ice crystals formed on the condenser due to the low temperature (Fig. 1). Because of that ice formation, it was only possible to recover 32 ml from the 50 ml of water
Around half of the dry ice has sublimated just 6 minutes after commencing the evaporation of 250 ml water. After 14 minutes there are deviations in the vacuum starts and after 16 min all of the dry ice has completely sublimated. Shortly after the entire condenser is steamed up (Fig. 2).
The heat is no longer transported, and the pressure continuously rises as the process stagnates. Condensate appears inside the tubing (Fig. 3), which is indicative of an insufficient cooling capacity. The heat of the condenser rises to the point that the isopropanol starts to reflux, therefore it was necessary to stop the process after 30 min. 5 ml water remained inside the pump, 15 ml was left in the flask meaning recovery of 230 ml
When using ethanol, there is no discernable difference in evaporation times and recovered solvent between the two condensers. Tab. 3 summarizes the results of the experiments where ethanol was used.
Table 3. G3 XL cooling coil condenser vs. G5 dry ice condenser; evaporation times of ethanol. Source: Heidolph North America
Parameters |
Time G3 XL |
Time G5 |
50 ml EtOH
50 °C
140 rpm
60 mbar |
03:15 min |
03:15 min |
250 ml EtOH
50 °C
140 rpm
60 mbar |
11:00 min |
11:00 min |
C: Discussion of the Results and the Handling
The performance of the G5 dry ice condenser matches the G3 XL cooling coil condenser for small volumes and volatile solvents.
One issue is establishing the appropriate process parameters because it is not possible to see if use of the capacity is optimized. The G3 XL cooling coil condenser comes supplied with a marking on the condenser that shows when the optimal workload is achieved.
The G5 dry ice condenser is unsuitable for heavy solvents: it fails to condense 250 ml of water if the user does wish to constantly add dry ice to keep the process running. The G3 XL cooling coil condenser system is suitable for a wide range of solvents and is not impeded by a narrow range of boiling points.
It is possible to run the system unattended over several hours or even overnight.
During the running process, a severe reaction of the dry ice was observed inside the G5 condenser. The greater the load the condenser is placed under, the quicker the dry ice sublimates which causes a severe bubbling.
If the condenser is fully packed with dry ice it may occur that the solvent runs out of the condenser and down along the surface.
Under heavy load, continuous refilling of the condenser is necessary to sustain the full capacity of the cooling system.
If that refill is not managed correctly, leads to rapid heating of the condenser which can result in a reflux of the solvent inside which is released as gas into the surrounding atmosphere – this is potentially dangerous.
By way of contrast, the G3 XL cooling coil condenser does not require additional maintenance after being switched on and set to the desired temperature.
Due to the high temperature variations towards the ambience, air moisture condenses and coats the G5 dry ice condenser constantly.
As this coating of air moisture forms, it drops down on the condenser and onto the surface on which the evaporator sits. If the settings of the recirculating chiller are correctly fixed, there is no formation of air moisture at the G3 XL cooling coil condenser.
Furthermore, ice crystals from air moisture can form inside the G5 dry ice condenser if the evaporator system is left open between two processes, meaning, if no rotation flask is attached (Fig. 4).
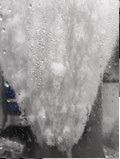
Figure 4. Ice crystals from air moisture form inside the G5 condenser between processes. Image Credit: Heidolph North America
This can result in product contamination with water when the next evaporation process is performed. With the G3 XL cooling condenser, this formation of ice does not occur.
Conclusion: High-Performance Condensers with Cooling Coils Facilitate Working with a Broader Spectrum of Solvents
These tests and observations have established that dry ice condensers offer satisfactory performance levels when working with limited amounts of solvents with low to medium boiling points.
For larger amounts of solvents or those with increased boiling points, the work with a dry ice condenser becomes labored due to the necessity of constant maintenance to ensure the process runs continuously.
With regards to simple handling and the potential to evaporate a wide range of solvents at high rates, a system with a high performance condenser, cooling coils, and a recirculating chiller specifically selected to fit the purpose, enables an extensive range of applications with limited surveillance and maintenance.
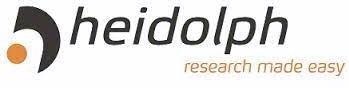
This information has been sourced, reviewed and adapted from materials provided by Heidolph North America.
For more information on this source, please visit Heidolph North America.