In recent years, those supplying metal parts to the medical device industry have recorded outstanding gains in the quality of their performance. With the emergence of statistical process control, ISO 9000 certifications and other initiatives, the overall quality of these alloys has never been better.
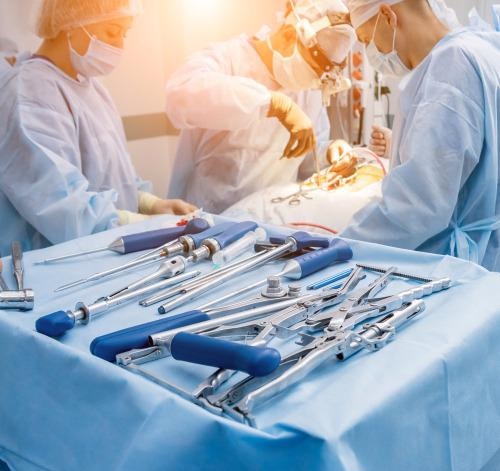
Image Credit: Ulbrich Stainless Steels & Special Metals, Inc.
Manufacturers of medical instruments and implantable devices have a broad range of effective metals to choose from today.
Knowing the differences between these materials and the diverse possibilities offered by each metal provides designers some amount of freedom when selecting a suitable grade or alloy that appropriate for the application.
Great strength and flexibility can be combined with bright, clean surfaces that aid sterile conditions.
Given the fact many of today’s surgical procedures involve significant complexities and ever-present concerns about the safety and comfort of patients, device makers need to be confident that the parts and materials they are purchasing are the optimal choices for the job at hand.
The development of minimally invasive and non-invasive procedures, in which surgeons do not have direct eye contact when working with the operating field, has brought extra attention to the key factor that equipment should work the first time, every time, without any issues.
Metal parts acquired via stamping houses and fabricators, along with the raw materials from which they are manufactured, are under particular scrutiny because buyers are persistently looking for inexpensive, more efficient alternatives.
While plastics continue to make important advances in the medical field – including supplanting metals in some devices – metals are still crucial to a large number of vital medical applications.
Designers today can choose from an ever-expanding range of metal materials and metal forms – a vast array of options at hand to help meet the goals of the medical equipment industry, achieving higher levels of quality and enhanced device performance.
How Does Metal Selection Play a Role?
For parts that must offer excellent strength and stiffness, metals are the preferred choice, particularly in small cross-sections.
They are also prime candidates for parts that need to be formed or machined to complex shapes, including blades, points and probes; for mechanical parts that work in unity with other metal parts, such as gears, levers, slides and triggers; for parts that undergo sterilization in high heat atmospheres; and for any other parts that require mechanical or physical properties surpassing those of polymer-based materials.
Typically, metals offer a robust, bright surface that helps facilitate easy clean-up and sterilization, which is good for the cleanliness requirements of most health-care applications.
Yet, metals that oxidize on the surface in an uncontrolled and destructive manner, such as steel, aluminum, or copper, are the main reason that materials such as stainless steel, nickel alloys, titanium, or titanium alloys are usually the most prominent in the medical equipment field.
These high performance metals offer special characteristics, certain limitations and exceptional versatility. Product engineers more familiar with common metals or plastics will uncover a wide range of possibilities when working with these materials, which tend to necessitate a new approach to design.
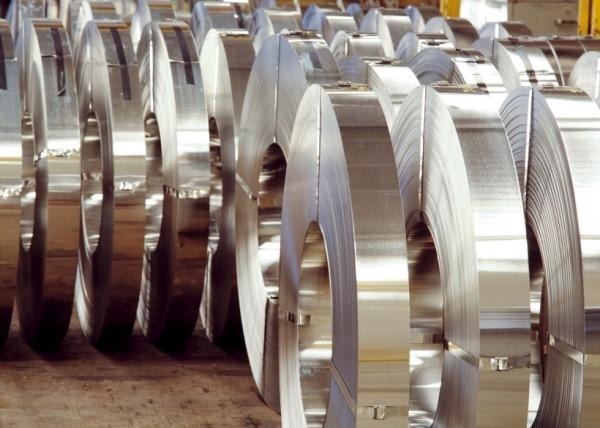
Image Credit: Ulbrich Stainless Steels & Special Metals, Inc.
Stainless Steel
When indication is given for a metal part to be incorporated into the design of a medical instrument, the usual choice is one of the 300 series stainless steels.
These alloys are effectively non-corrosive; can be fabricated in a range of surface finishes, from reflective to matte; offer superior mechanical and physical properties; and are comparatively easy to cold form or fabricate into distinct parts.
Stainless steel alloys are made up of 17 to 25% chromium and between 8 to 25% nickel. The presence of chromium provides some of the corrosion resistance of the stainless steel by forming a study, adherent and invisible chromium oxide film on the surface of the alloy.
This film is also self-healing if it suffers mechanical or chemical damage. Sometimes, additions of molybdenum of up to 7% are incorporated to further improve corrosion resistance.
The most prominent stainless steel grades for medical parts are 301, 304, 304L and 305. These versions slightly differ from one another in alloy composition, and the choice of which grade to use is informed by corrosion requirements, formability, or availability in the necessary thickness and temper.
Other key design parameters include surface condition and strength.
Stainless steel alloys have the capacity to be cold worked to great tensile and yield strengths while preserving good ductility and toughness.
At room temperature, they show yield strengths between 30 and 200 ksi, depending on the amount of cold work and overall composition. Stainless grades identified as ‘austenitic’ or ‘martensitic’ refer to the metallurgical structure of the metals after they are heated above the optimal temperature and then cooled rapidly.
The final structure is determined by the combination of alloys and the time and temperature of the heat treatment. Austenitic stainless steels are more formable, whereas martensitic grades are more dense and robust.
For most medical device parts using austenitic stainless steels contain 16 to 20% chromium and around 6 to 14% nickel. The presence of chromium meets the preferred corrosion resistance by forming a durable adherent and invisible chromium oxide film on the surface of the alloy.
If mechanically or chemically damaged, this film self-heals. In some grades, up to 7% molybdenum is added to further boost corrosion resistance.
Among today’s medical applications, surgical staplers are an effective showcase of 300 series stainless steel parts, including the springs, cartridge slides, frames, anvils and jaws. The staples themselves are fabricated using various grades of stainless steel wire.
Further applications of 300 series stainless include catheters, arterial-plaque removers and diagnostic instruments. An alloy with higher nickel content, stainless grade 316, is occasionally specified for braces due to its high creep strength at raised temperatures.
Grades 304L and 316L are low carbon versions of the respective alloys and are endorsed when welding is expected.
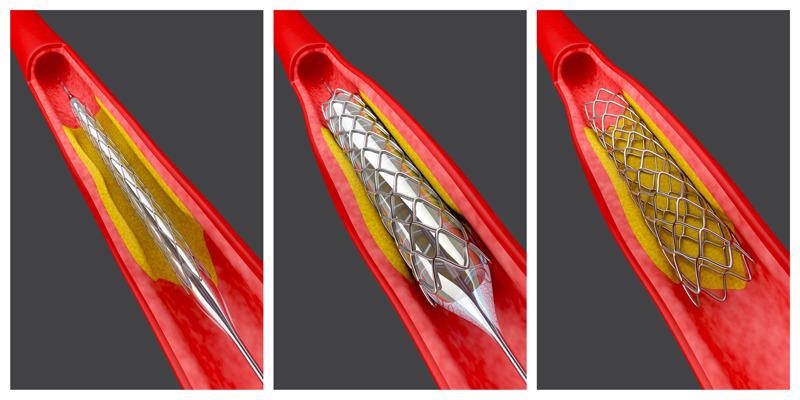
Image Credit: Ulbrich Stainless Steels & Special Metals, Inc.
Hardenable Alloys
400 series stainless steels, frequently utilized for surgical instruments, are not as corrosion resistant when compared to the 300 series but can be refined through heat treatment to greater strength and hardness levels.
The two most frequently used grades, 410 and 420, contain a limited amount of chromium and no nickel. The general purpose grade is 410, whereas 420 has an increased carbon content and can be hardened to greater strengths.
Type 410 martensitic stainless steel is also utilized for surgical instruments. While corrosion resistance does not match the 300 series, grades can be refined through heat treatment to achieve greater strength and hardness levels. Type 410 carries around 11.5 to 13.5 percent chromium and no nickel.
When a part requires enhanced strength and stiffness – for example, in equipment housing – the designer may choose one of the precipitation-hardening stainless steels, such as 17-7 PH or 17-4 PH.
These metallurgical hybrids are extremely similar in composition to stainless type 301, the exclusive difference being tiny additions of copper, aluminum, phosphorus, or titanium.
After a part has been shape into its final form, it receives an age-hardening treatment in which these added elements provoke a phase transformation. The result is the formation of intermetallic compounds that considerably increase the strength and hardness of the part, sometimes by as much as 40%.
Titanium
Of the commonly used metal materials, pure titanium is the most inert and the most expensive - typically utilized for ultra-high reliability parts or those that stay inside a patient post-surgery. These include replacement joints, pacemaker cans and other metal implants.
Titanium alloys are also primarily used in the medical field in parts for which stainless steel cannot meet the hardness, strength, corrosion-resistance, or additional specifications.
Titanium gives the strength of steel at less than two-thirds its weight, making it a superior biomaterial. Its excellent corrosion resistance is based on its capacity to form a close-fitting adherent, protective oxide film upon exposure to air or other oxidizing media.
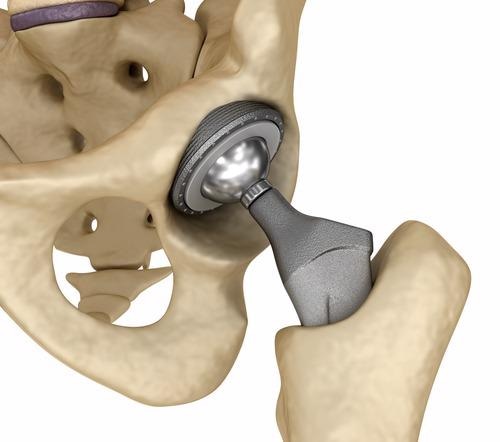
Image Credit: Ulbrich Stainless Steels & Special Metals, Inc.
This passive film can withstand all types of corrosion and will reform even after the metal’s surface has been damaged.
One of the most intense applications in the medical field is also one of the most novel in terms of fabrication and use of available alloys.
The common hip-joint replacement is intended to be a prosthesis lasting a lifetime and subsequently demands materials of extremely high strength, exceptional wear resistance and superior corrosion resistance.
Designs from different manufacturers do vary slightly, but one favored type is made up of a titanium-alloy cup that sits into the hip socket, which is mounted onto a cobalt-chromium head onto and a cobalt-chromium stem that slots into the femur.
For those manufacturing titanium hip stem joints, Ti-6AL-4V titanium alloys, including the low oxygen ELI grade, are generally the preferred choice for implantable applications, in both plate and bar. Bar is the most frequently used starting material when the part will be forged and is accessible in diameters up to seven inches.
The most commonly used titanium alloy, Ti-6 AL-4V, has a minimum room-temperature tensile strength of 120,000 psi. It is completely heat-treatable in section sizes to one inch.
Both strength and hardness can be enhanced by about 20% by heat treatment. After aging, the standard yield strength of a one-inch bar is 150,000 psi, with a hardness of 360 Bhn.
Why are Certain Product Forms Preferred?
Stainless steels, hardenable alloys and titanium alloys can be manufactured into different forms as required by the medical industry, including wire, strip, sheet, rod, plate, foil and bar.
Due to the fact medical device parts are typically very small and intricate, automatic stamping presses are commonly used to form the shapes. Strip and wire are well suited to this type of processing and are the most frequently used starting materials.
These mill shapes are available in a broad range of sizes. For instance, strip varies from ultrathin foil of 0.001 in. up to a thickness of 0.125 in., while flat wire can be supplied in thicknesses of 0.010 to 0.100 in. and widths of 0.150 to 0.750 in.
Considering Flat Wire as an Alternative to Strip
Precise widths are required in order to process strips through automatic stamping machines; this also minimizes scrap. Slitting to width is a task that can be completed by strip rerollers or by strip service centers with equivalent skill.
For most stamped parts, suppliers can remove the slit edge by deburring, rounding, or squaring it off when edge condition is a factor.
When requiring a smooth edge, designers have the choice to use flat wire rather than a strip. Because dies are used on all four sides when rolling flat wire, a clean, uniform edge is ensured for the whole length. This can provide more benefits as well as saving the cost of conditioning the edge.
One of the major benefits is producing a ‘strip’ product that is extraordinarily thick for its width. For very thin gauges, a regular strip can be obtained in slit widths as narrow as 0.035 in.
Yet, as the thickness increases, the slitter requires more space between the knives in order to sustain flatness, camber and other shape parameters. When the thickness of the strip approaches 20% of the width, flat wire can usually give increased tolerances, particularly in widths under 0.75 in.
Purchasers have nearly as many choices of alloys for wire as they do for strip, so accessibility is not a problem. Wire comes in many varieties, including 300 and 400 series stainless steels, titanium and precipitation-hardening alloys.
What are Some Characteristics to Keep in Mind?
Machining
The machining properties of the 6-4 alloy are close to those of austenitic stainless steels. Both rated around 22% of AISI B-1112 steel. Yet, titanium reacts with carbide tooling and heat intensifies the reaction; thus, it is recommended heavy flooding with cutting fluid is used.
Fluids that contain halogen should not be used due to the risk of causing stress corrosion if they are not removed thoroughly after machining operations.
Formability
While stampers prefer materials that are simple to cold form, formability is conversely related to the exact things buyers may want when they identify these alloys in the first place – exceptional hardness and strength and hardness.
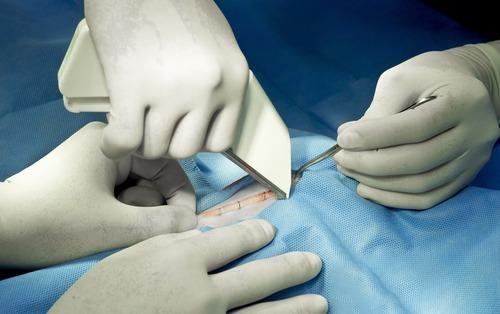
Image Credit: Ulbrich Stainless Steels & Special Metals, Inc.
For instance, despite a very slim cross-section, surgical staples require maximum strength, so they do not separate. But they also must be sufficiently formable so that surgeons can tightly close them without using noninvasive staple tools.
Pulling off an effective trade-off between strength and formability can be readily achieved during the reroll stage. A suitable level of formability is produced while the strip is being rolled down to gauge, with annealing between the passes to eliminate the effects of work hardening.
By alternating heat treating and cold rolling, rerollers offer a formable material that is prepared for forming, drawing and punching on traditional multislide and multidie stamping equipment.
The ductility of titanium and its alloys may be lower than other common structural metals, but strip products can be easily formed at room temperature, although at a reduced rate when compared to stainless steel.
Titanium springs back after cold forming due to its low modulus of elasticity, about half that of steel. The greater the strength of the metal, the higher the spring back.
Since the ductility of titanium grows with temperature, forming operations can be performed at increased temperatures when room temperature efforts are insufficient. Unalloyed titanium strip and sheet are typically cold-formed.
One exception being alpha alloys which are occasionally heated up to 600°-1200°F to prevent spring back. Oxidation of titanium surfaces becomes a factor at temperatures beyond 1100°F, so it may be necessary to perform a descaling operation.
Due to the cold-welding characteristics of titanium being greater than those of stainless steel, lubrication is vital when conducting any operation in which titanium is in moving contact with forming equipment or metal dies.
Controlling Hardness
Finding a balance between formability and strength can be readily achieved when rolling the alloy for thickness. By annealing between the passes to eliminate the effects of work hardening, cold rolling offers the desired temper, one that keeps the material’s strength intact and supplies the requisite formability.
To meet the typically strict specifications set out for these alloys and to limit costs as much as possible, Ulbrich has metallurgists to assist in the selection of alloys, as well as helping calculate a rolling/annealing sequence that will offer the optimal combination of properties.
Surface Finish
The surface finish on titanium-based and stainless steel strip products is also produced at the reroll stage. Product designers can choose from a range of products, including a bright, reflective finish, a matte surface that effectively transfers lubricant, or other special surfaces needed to facilitate welding, brazing, or bonding.
Surface finishes are generated by the face on the work rolls in the rolling mill. For instance, extremely polished carbide rolls offer a mirror-bright reflective finish, while shot-blasted steel rolls a 20-40 µin. RMS matte finish and shot-blasted carbide rolls supply an 18-20 µin. RMS dull finish.
This process is capable of producing a surface of 60- µin. RMS, which is about as rough a surface can get.
What is the Best Way to Source Your Materials?
Most metal materials are freely available because the grades in the highest demand for medical equipment parts are also extensively used outside the medical field. This means that local and regional service centers generally stock these grades in the requisite gauges and tempers.
When the preferred combination of temper and gauge cannot be immediately sourced, the services of a stainless steel and high alloy reroller like Ulbrich Stainless Steels may be called upon.
These specialists utilize heavy-duty rolling mills for reducing strip thickness or wire diameters to precise dimensions. They also possess the furnaces to anneal the metal between passes, eliminating the effects of work hardening and delivering a temper that keeps the material’s strength and produces the appropriate formability.
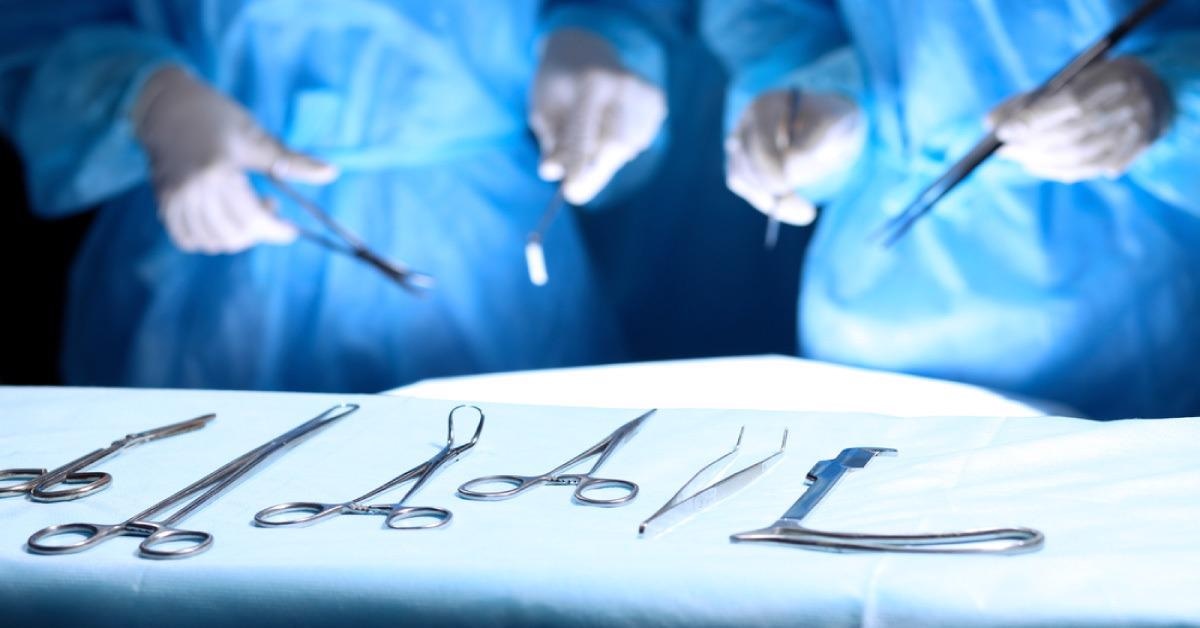
Image Credit: Ulbrich Stainless Steels & Special Metals, Inc.
Which Metal is Right for Your Medical Device?
While stainless steel, titanium and nickel-based alloys are comparatively more intricate from a user’s standpoint than materials in more frequent use, they also provide a considerably wider range of capabilities.
These ‘metallurgical animals’ can be tailor-made via heating, cooling and quenching to demonstrate specific mechanical properties.
If preferred, they can be modified further throughout processing: for instance, hardening can be achieved by rolling out thinner gauges, whereupon follow-up annealing can retrieve lost properties delivering a precise temper for cost-effective forming.
Once designers are familiar with the intricacies of the materials, they will soon see that these exceptional metals offer several unparalleled benefits in numerous medical products, including unequaled corrosion resistance, optimal mechanical properties, a broad range of surface finishes and exceptional production versatility.
Ulbrich is at hand as a development partner and can answer any questions pertaining to the necessary medical applications.
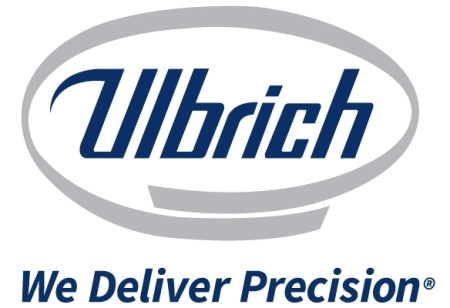
This information has been sourced, reviewed and adapted from materials provided by Ulbrich Stainless Steels & Special Metals, Inc.
For more information on this source, please visit Ulbrich Stainless Steels & Special Metals, Inc.