What are the properties worth considering when selecting a particular metal alloy for a medical device?
The short answer: any decision made on the mechanical, chemical and physical properties of metal alloys is extremely dependent on what task will be performed by the medical device and the environment in which it will work.
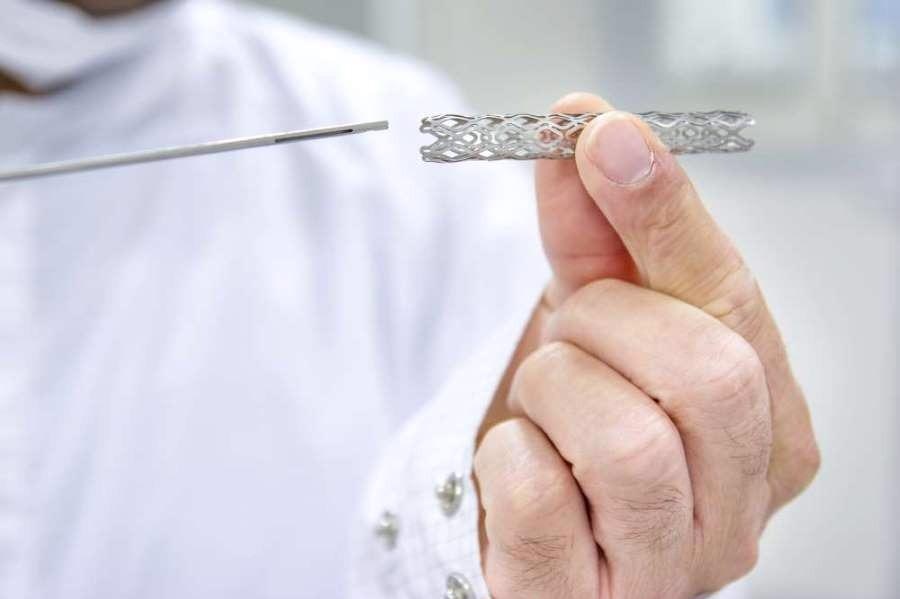
Image Credit: Ulbrich Stainless Steels & Special Metals, Inc.
End-use applications determine every single decision made when selecting an alloy, identifying its shape and size and quantifying the volume of material needed.
Other properties medical manufacturers and buyers need to consider may be magnetic properties, manufacturing properties, electrical properties, environmental properties and atomic properties, such as radiological properties, castability or machinability and sometimes thermal properties of the material.
When determining an appropriate alloy for a medical application, precise and uniform chemical properties should be decided early on in the metal selection process.
Taking due care and attention to choose the correct chemical makeup of an alloy enables precision re-rollers or other metal suppliers to source high quality, accurate raw material - that has been smelted or manufactured long before arriving at the loading bay.
Engineers, Product Managers and experienced Sales professionals at Ulbrich work in collaboration to communicate the optimal route required for best material selection.
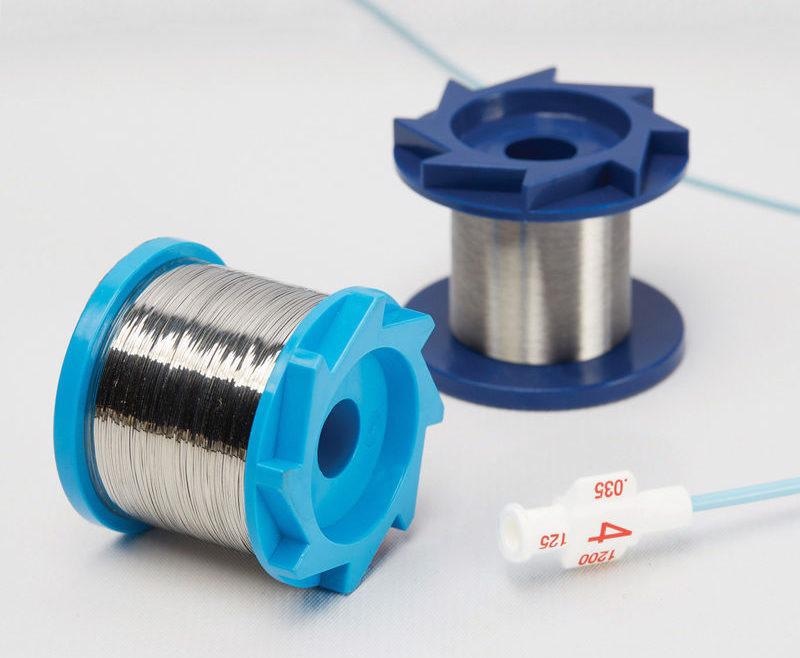
Image Credit: Ulbrich Stainless Steels & Special Metals, Inc.
Ulbrich has medical manufacturing and metallurgical experts who assist customers in the selection and procurement of the right material with the right properties based on their specific application demands.
This is facilitated at Ulbrich Specialty Wire Products in Westminster, South Carolina, where the majority of medical device customers purchase precise round and flat wire.
For medical braid wire applications, the most common mechanical properties are high strength and dimensional control. For Mandrel applications, surface smoothness, dimensional control and elongation have also become key factors.
These days, mechanical properties and oxide layers associated with the specialty metal Nitinol which is a shape-memory alloy, are known to be crucial elements to the medical device industry.
Biocompatibility, or the capability of the human body to accommodate contact with metal such as Titanium, is also a key factor that medical manufacturers must frequently consider. For example, Titanium rods utilized in oral surgeries bind to human flesh.
The Titanium rods are effectively set in place permanently, making their biocompatibility of utmost importance to avoid rejection, corrosion, or infection.
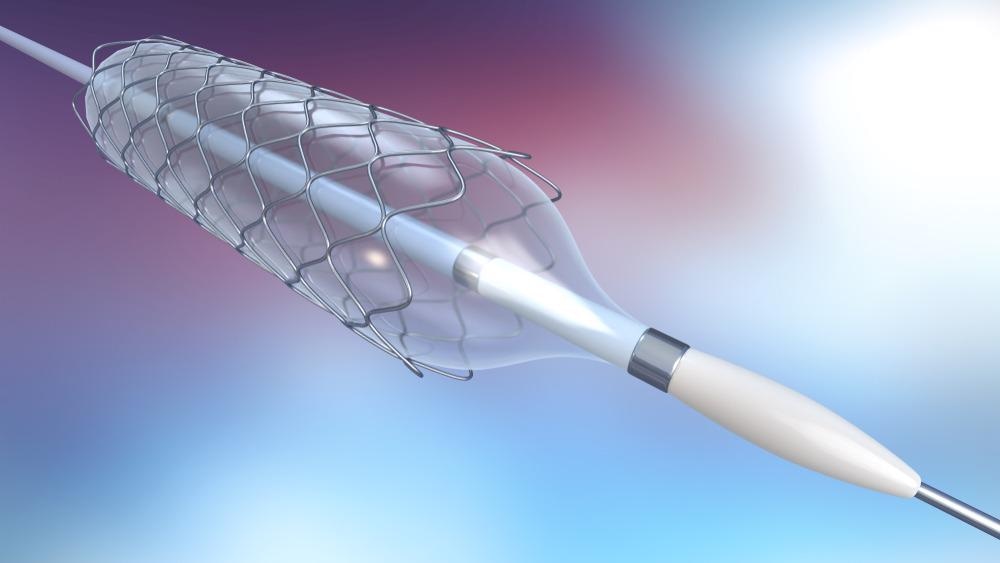
Image Credit: Ulbrich Stainless Steels & Special Metals, Inc.
Titanium is extremely biocompatible, making its use frequent in medical manufacturing such as dental implants, allowing patients to quickly heal and to use their jaw/teeth with minimal disruption.
A great number of medical manufacturers utilize a spring temper flat, round or custom shaped wire for various applications.
The required characteristics that may be desired can differ based on manufacturing process or end use which might necessitate annealed, full-hard, half-hard and quarter-hard wire, which wire manufacturers can offer upon request.
The harder the temper, the more solid the structure will be. This provides a good torque response to the device, also known as ‘torquability.’ For instance, in the manufacture of catheters, unique maneuverability is critical to success, making the torquability of the material a key component.
Catheters are medical devices that are typically placed inside the body to treat diseases or perform surgical procedures. Mechanical properties have a significant role when selecting the appropriate metal for making catheters.
Medical device customers make the decision between coiled-enforced or braid-enforced catheters for their application. In the manufacturing process, customers are now choosing nitinol for coiled catheters, especially for sensitive surgeries like neural or cardiovascular surgeries where precision is paramount.
What are some of the Different Methods for Ensuring Material Quality for Medical Wire and What Do they Accomplish?
Methods for ensuring high quality stainless steels and specialized metals for medical wire should be a key focus, not only for quality assurance teams but should be an overall expectation that is of key importance to the medical rolling mill.
Continuous dimensional data collection (SPC data) should be gathered as the metal is fed through the mill because it enhances performance consistency for manufacturing processes and the device.
Working in close collaboration with metal manufacturers with experienced metallurgists on staff that can demonstrate the knowledge of how metal is shaped and sized at the microscopic, mathematical level is a key benefit for medical device manufacturers.
This type of quality control makes sure that defects are infrequent and, therefore, providing time and energy savings that benefit medical device or component businesses by streamlining your production while limiting waste, scrap and failure.
Above all, dimensional data collection guarantees that materials meet specifications and are within all regulatory and manufacturing guidelines.
Surface cleanliness is another key factor that has an effect on either enhancing or diminishing material performance in challenging medical applications. Methods that achieve good cleanliness can never be strict enough as people’s lives are literally on the line.
Precision strip, flat wire and round wire must be free of particulate as much as possible to ensure results at the highest degree of accuracy because anything else could be disastrous.
Quality Control Coordinators, Machine Operators and Helpers at Ulbrich are persistently inspecting every single work order with extreme attention to detail. Team communication and collaboration are crucial to make sure high quality standards are achieved throughout the supply chain.
When choosing a materials partner, it should be evaluated whether if they have an equal level of commitment to quality up and down the org chart as expected.
Compliance with the latest ISO certifications can be well-meaning, but to meet the material needs of medical device customers, extra special care and attention should not only be standardized in the process but inherent in the culture.
Personal Protective Equipment (PPE) is just the first step to maintaining materials that are free of contamination. Custom guards, barriers and other ways of preventing contamination should be installed on the machinery at each stage of material production to safeguard metalwork in progress (as well as Machine Operators).
This will make sure that the materials received are ready for and fabricated to the same level of cleanliness and attention to quality and performance that medical manufacturers come to expect.
Purchasing is an early method on the front end that initiates the manufacturing process. Buying material from reputable sources and qualified vendors is crucial.
The chemical makeup of the material must be duly inspected while at the same time, inclusion rates should be at the lowest possible levels (non-existent in an ideal scenario).
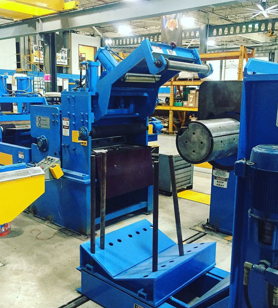
Image Credit: Ulbrich Stainless Steels & Special Metals, Inc.
By choosing a supplier and an alloy, medical device customers must look for those sources who sell materials with consistent and unwavering mechanical properties, which are vital to processing medical wire.
Manufacturing sources, as well as production methods, are of equal importance in the supply chain to achieving success in the world of high tech medical devices.
Lastly, labor-intensive spooling methods that prevent tangles throughout production are also of key significance. When medical device customers proceed to use bulk, Steeger or Wardwell bobbins, they do not need any tangling wires that cause breakages.
With round wire as thin as 0.00075” for nitinol and stainless alloys, tangling can cause excessive strain on medical device production. Ulbrich takes care when wrapping wire on spools with the next operation in mind, and the company always requests feedback on the spooling performance.
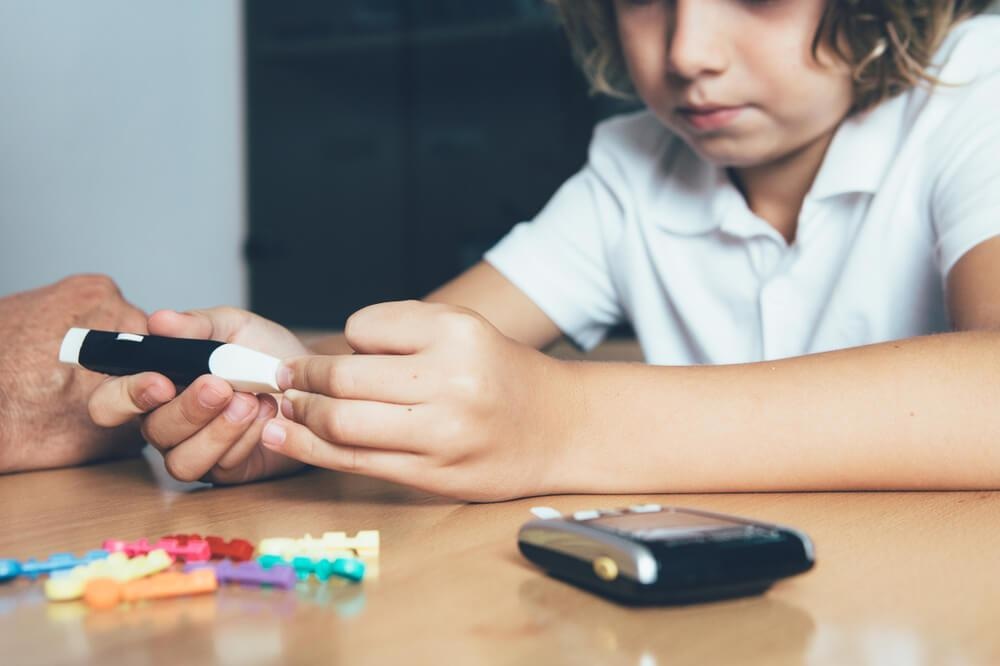
Image Credit: Ulbrich Stainless Steels & Special Metals, Inc.
What Environmental or Contextual Factors are Medical Devices Subjected to that Affect Material Selection?
Will the device be inserted or grafted into the body, and/or what is the timescale the device will remain in the body? Biocompatibility and response to blood is a critical factor here. MRI Compatibility may also be necessary depending on your application.
How Important are the Corrosion Resistant Properties of Stainless Steel or Special Metal Wire for Medical Manufacturing?
Extremely important. For instance, 304V stainless steel wire has been remelted using a vacuum arc so that chemistry is more uniform with limited voids and contaminants. 304V is a ductile study material that can be soldered or welded easily.
304V Stainless Steel Wire is utilized in numerous medical applications due to its low-cost in comparison to other materials that meet the minimum corrosion resistance standards.
What are Some Common Materials We See Medical Manufacturers Turning to?
Bi-metals are becoming more popular and seeing an increase in application. Various metals and special alloys, such as a developmental project-based alloy, MP35N, provide state-of-the-art, high performance capabilities for surgeons.
Other bi-metals like nitinol with a platinum core (cladded) and a Nitinol with a Tantalum core have seen their exposure skyrocket in the medical device marketplace as of late.
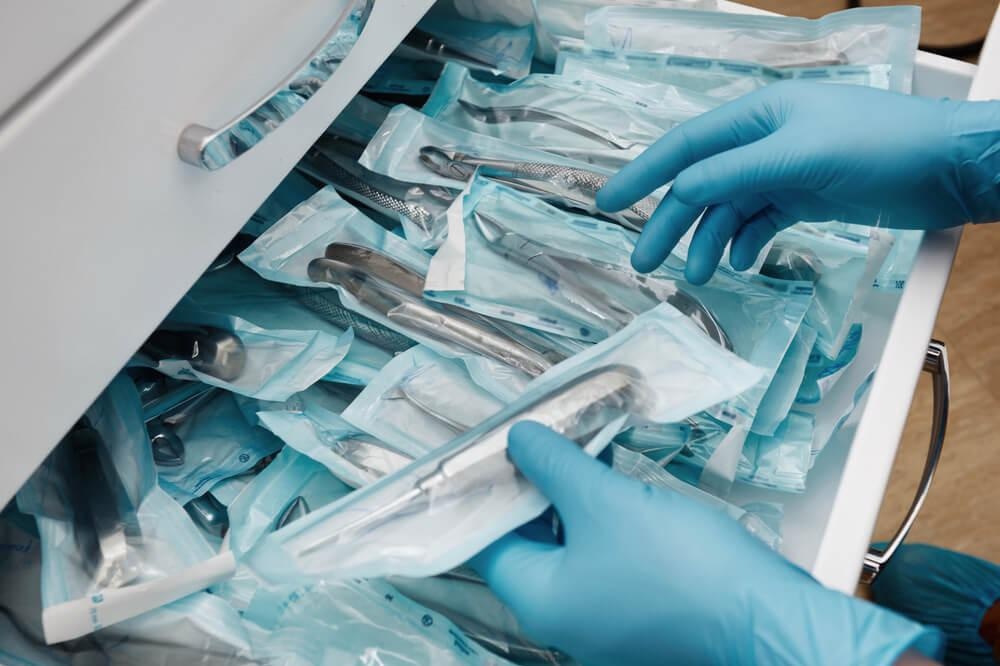
Image Credit: Ulbrich Stainless Steels & Special Metals, Inc.
Heavy metals like platinum, tantalum,and tungsten can be seen with exceptional clarity under a fluoroscope during cardiovascular surgery, for instance. This allows surgeons to see where they are moving within the human body.
Though 304V stainless steel wire is still the most popular in most medical applications due to the alloy meeting corrosion resistance minimum standards while being a safe and productive material.
What is Critical to the Production & Performance of Surgical Instruments?
Where surgical instruments are concerned- primarily Austenitics, Martensitics and Precipitation Hardening Grades - it is critical and common that stainless steel alloys are shaped and developed to perform very specific tasks.
Alloys used to manufacture medical instruments should be fabricated to withstand the demands of daily use in healthcare environments, with extreme attention to detail and quality.
From cutting and pricking to stapling, the demands placed on medical devices and surgical instruments demand precision manufactured alloys with the precise specifications necessary to perform the job.
Ulbrich is Driving Medical Instrument Innovation Through Precision Alloys
With the assistance of precision special metals and alloys, doctors and professionals in the medical field can rehabilitate and preserve the health of ailing people. Ulbrich takes great pride in the fact that the company is a key component —no matter big or small—in ensuring the health of millions.
And that’s precisely why Ulbrich ensures its machines and processes are maintained to the highest of standards. Precision alloys facilitate innovative surgical (increasingly robotic) instruments which have the power to transform lives.
Surgical Instruments Made with Precision Alloys are Simply Better
Various surgical instruments and incision tools demand a wide range of alloys and alloy properties.
Choosing the optimal materials and having them manufactured to precise chemical, mechanical and physical specifications makes sure the resulting product or component offers more consistency, reduced waste and limited failure rates.
Ulbrich has an extended history of supplying alloys and bimetals to the medical industry due to the company’s strategic sourcing methods, as well as a vast inventory of alloys and impressive rolling and annealing capabilities. This competitive advantage is one that Ulbrich is able to pass on to its customers.
So, whether applications and medical devices demand an alloy to be heat-treated to a higher hardness (like PH Grade alloys) or something non-magnetic and extremely resistant to corrosion (like Austenitic alloys), Ulbrich can make it happen.
Surgical Instruments Made with Precision Alloys include:
- Cardiovascular Clamps
- Catheters
- Lances
- Needles
- Scissors
- Sheers
- Stapler Springs, Staples
- Strip Square
- Surgical Draws
- Surgical Grills and Grinders
- Surgical Staplers/Anvils
- Surgical Robotic Instruments
- Tissue Grabbers
- and more
Precision alloys utilized in surgical instruments include but are not limited to:
Stainless Steel Grades:
- 304 Stainless Steel
- 304V Stainless Steel
- 304LV Stainless Steel
- 304LVM Stainless Steel
- 316 Stainless Steel
- 316LVM Stainless Steel
Special Metals:
- Aluminum
- Beryllium Copper
- Copper
- L605
- Molybdenum
- MP35N
- Nitinol
- Phosphor Bronze
- Titanium
- Tungsten
- Many other ‘bimetals’ (combinations of cladded wire which may include Silver or Platinum).
Other Specialty Alloys include:
- 17-4PH® Stainless Steel UNS S17400
- 17-7PH® Stainless Steel UNS S17400
- 305 Stainless Steel UNS 30500
- 410 Stainless Steel UNS S41000
- 420 Stainless Steel UNS S42000
- 420 High Carbon Stainless Steel UNS S42000
- 420 LC Stainless Steel UNS S42000
- 440A Stainless Steel UNS S44002
Ulbrich, are Always Looking for Ways to Innovate and Improve Upon Medical Devices
In addition to Ulbrich’s innovation and immense capabilities in rolling, slitting and annealing, the company is persistently researching, testing and analyzing alloys the chemical and mechanical properties of alloys to optimize performance potential.
This means that when a company partners with Ulbrich, it receives both the best-of-the-best in personnel, process and product, as well as a team that is passionate about making medical devices that are consistent, successful and effective.
Global Representation with Service and Distribution Centers Worldwide
Ulbrich Stainless Steels & Special Metals, Inc. is a family-owned company in its fourth generation of stewardship. Established in 1924, Ulbrich has become a key supplier of stainless steel and special metals throughout the Medical Device Industry.
During this time, Ulbrich has engaged in the design and manufacturing of hundreds of state-of-the-art medical products.
With Dimensional Control that leads the industry, real time gauging and Statistical Process Control (SPC), an extensive range of medical alloys and supreme customer service, Ulbrich strives to manufacture and distribute the best quality materials.
Ulbrich is made up of a series of manufacturing divisions that provide specialty strip and precision wire, all with local management and all developed to offer custom metals products that meet the original demands of the medical devices equipment manufacturers.
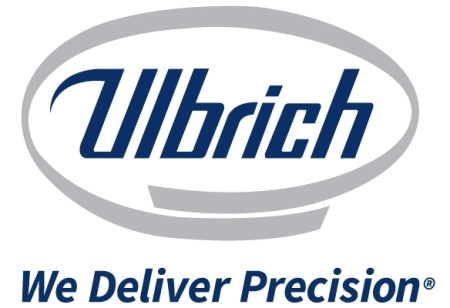
This information has been sourced, reviewed and adapted from materials provided by Ulbrich Stainless Steels & Special Metals, Inc.
For more information on this source, please visit Ulbrich Stainless Steels & Special Metals, Inc.