Metal strip for stamped parts is typically provided by service centers that purchase the material from large mills and slit it to width for their customers. At least, that is the common assumption. But there is an additional layer in the supply network, which often goes unnoticed.
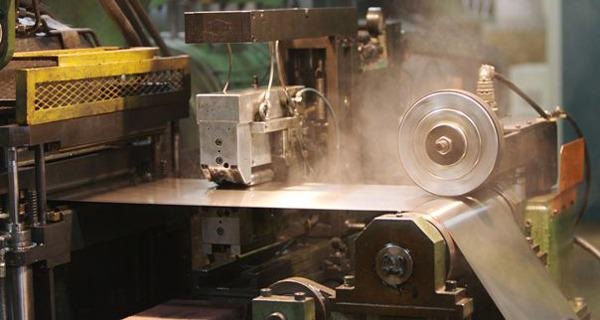
Image Credit: Ulbrich Stainless Steels & Special Metals, Inc.
These are the precision rerollers that produce the dimensional and metallurgical properties that exceed the capabilities of the equipment and narrow size range offered by most service centers.
Rerollers are becoming increasingly important each year as companies seek ways to enhance production, increase cost efficiency and, at the same time, produce a better level of quality for their customers.
Rerollers are found throughout the metal industry, but in the stainless, nickel, and cobalt alloy market, they have a significant role as these higher priced metals are required to meet more demanding specifications. The tiniest alteration in metallurgy or surface finish can be a critical factor regarding the performance of many stamped parts.
Some common services reroll mills perform: Rolling to specific gauge, improving formability, modifying grain size, adjusting temper, controlling spring back, enhancing surface finish and solving problems for the customer.
Rolling to Precise Gauge
Stainless steel strip and wire, as well as nickel and cobalt-based alloys made to standard mill tolerances in varying forms, can be acquired from integrated producers. Rerollers often stock large quantities of these materials: Ulbrich works with over 165 different alloys.
These mill partners provide metals that are readied for stamping by rolling close to thickness tolerances, customizing the mechanical properties and delivering the desired surface finish.
Worldwide, Ulbrich operates numerous rolling mills that vary in size to facilitate the many different material requirements they are expected to meet.
This equipment allows the company to fabricate high quality strip to the tightest possible gauge tolerances on a consistent basis while maintaining a precise, uniform thickness level throughout the entire coil.
If several passes are necessary for a rolling process, work hardening becomes a factor. This can be eliminated by processing the material through an annealing cycle in order to return it to the preferred level of formability. At Ulbrich, seven controlled-atmosphere, bright annealing furnaces are utilized to satisfy these metallurgical adjustments.
In addition to Ulbrich’s capacity to offer precision rerolling, Ulbrich operates multiple service centers throughout North America, which offer supply chain management services for customers who demand them.
No matter what the material needs or challenges presented, Ulbrich is there to meet them and provide exceptional manufacturing to its customers.
Providing Formability
Naturally, stampers desire material that is easy to cold form for their manufacturing operations. Formability, however, contradicts the very properties users may prefer when they specify the more specialized alloys – enhanced strength and hardness. Corrosion-resistant springs are one such example.
Creating an effective compromise between strength, hardness and formability is one of the main services offered by the metallurgical staff at the reroll source.
With close collaboration between engineers and Ulbrich’s expert metallurgists, alloys can be fabricated so they can be formed, drawn, blanked and even deep drawn, just as easily as other metals.
It is crucial to take into consideration the tool or machine being used with metal stamping, and a re-roller can help make sure the suitable material is chosen for a particular manufacturer.

Image Credit: Ulbrich Stainless Steels & Special Metals, Inc.
Spring Back
Another major issue stampers present is spring back. This property also can be mediated by annealing the material at particular points in the rolling sequence. However, spring back will vary among alloys as it is a basis of the relationship between tensile and yield strength of the metal.
Grain Size
The metallurgical standard most stampers use to measure the formability of strip products is grain size. If the grains lack uniformity or are too coarse, sidewalls of deep-drawn components may roughen-up and result in orange peel. If grains are too fine, the part may pull apart during forming.
When the grain size of the metal does not meet the target, rerollers can modify it in their annealing equipment. By carefully controlling the temperature of the furnace and the line speed of the strip passing through, it is feasible to generate a precise grain size range as measured by an ASTM grain size value widely accepted by the industry.
Grain size values range from 0 to 13, with the lower values specifying coarser grains and the upper values a finer grain. The recommended window for most deep drawing applications in stainless steel, 8 to 9 on the ASTM scale.
For blanking, a finer grain size between 10 to 11 is deemed appropriate. The greater hardness guarantees a good, clean punch through the material.
Temper
Meeting strip product specifications would be relatively easy if formability were the only objective, but there are other factors to regard. One of these is rolling the material to precise tempers.
Stainless steel, nickel and cobalt alloys can be detailed in either annealed (soft) or in cold-rolled tempers. The tempers are identified as quarter hard, half hard, full hard and extra full hard, contingent on strength requirements. These tempers are made by rolling particular percentage reductions in the thickness of the strip.
For stamping applications, a majority of the material is delivered in the annealed or soft state. Tempers of quarter hard require a considerable amount of effort to form. Tempers above that level are hardly used by the stamping industry, except for blanking.
Surface Finish
Surface finished of stainless steel, nickel-based and cobalt-based alloys can be performed by reroll shops to create either a bright reflective finish, a matte surface that transports lubricant more effectively or other particular surfaces required for good welding, brazing or bonding.
Finish can be designated either as an RMS (root mean square) value or as an arithmetic average of the surface roughness as recorded by a profilometer. It is recommended that stampers specify surface roughness inside a range of acceptable finishes.
Specifying a maximum 10 microinch RMS will produce a bright reflective finish as low as 4. As the roughness of the surface increases, rerollers must function in a wider range. For example, a designer should specify a 20 to 40 microinch RMS for a 25 microinch RMS.
In the rolling mill, surface finishes can be produced by the face of the work rolls. Extremely polished carbide rolls produce a mirror-bright reflective finish. Shot-blasted steel rolls are utilized for 20 to 40 microinch RMS matte finishes. An RMS 60 microinch is about as rough as it gets for a surface that can be fabricated.
Ulbrich also processes in excess of 70 stainless steel, nickel alloy and cobalt alloys in the metal wire format.
In its manufacturing, not only does Ulbrich offer the requisite dimensional and metallurgical characteristics for forming parts to specification, but its shaped wire division can also create special profiles, on top of round (for cotter pin applications), square, keystone and several others.
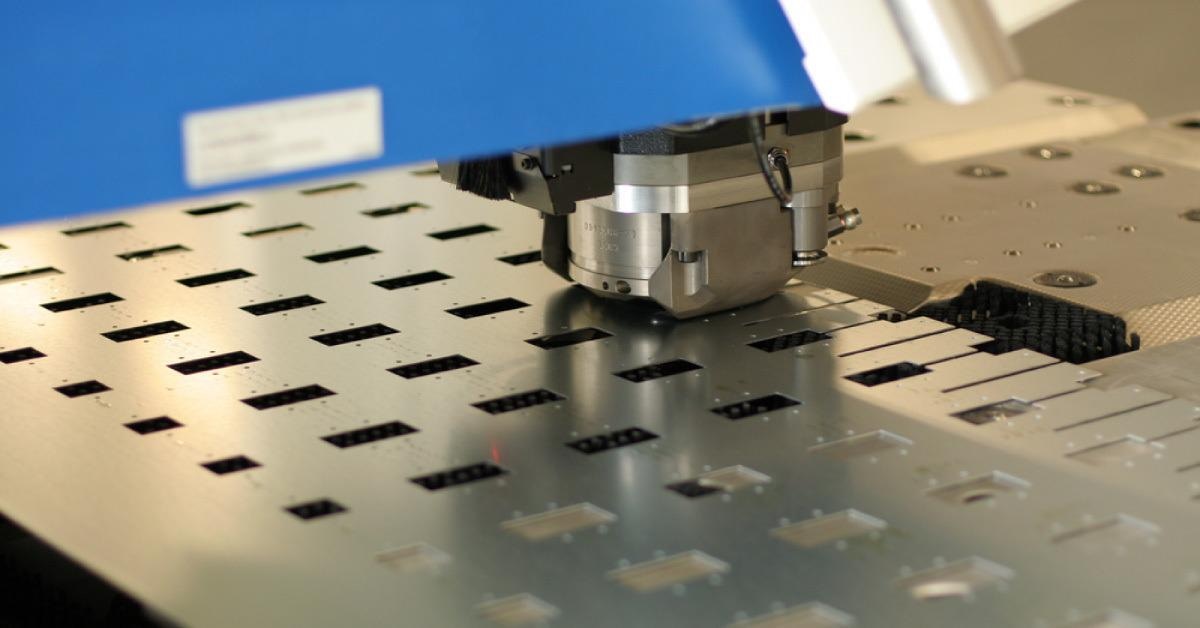
Image Credit: Ulbrich Stainless Steels & Special Metals, Inc.
Conclusion
With the various alloys in the market now, it can be wearisome trying to find something that meets the precise specifications, especially if when considering particular aerospace or medical application.
The wide range of stainless, nickel-based and cobalt-based alloys now supplied by the integrated mills means the presence of rerollers to customize them to meet stringent specifications.
Thus, the efficient channel of distribution from the service center industry offers stampers many options when trying to meet their customers’ expectations.
It is possible for stampers to utilize this marketing arrangement to optimally serve their customers by working in close collaboration with all three levels of suppliers. In short, re-rollers can collaborate with metal stampers to ensure the chain of supply is there to meet all requirements and demand for supply.
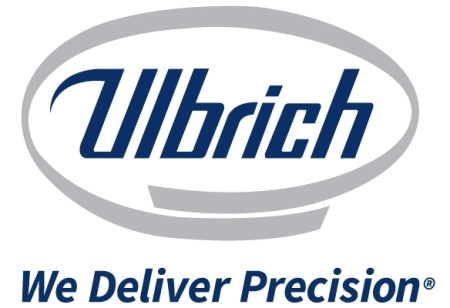
This information has been sourced, reviewed and adapted from materials provided by Ulbrich Stainless Steels & Special Metals, Inc.
For more information on this source, please visit Ulbrich Stainless Steels & Special Metals, Inc.