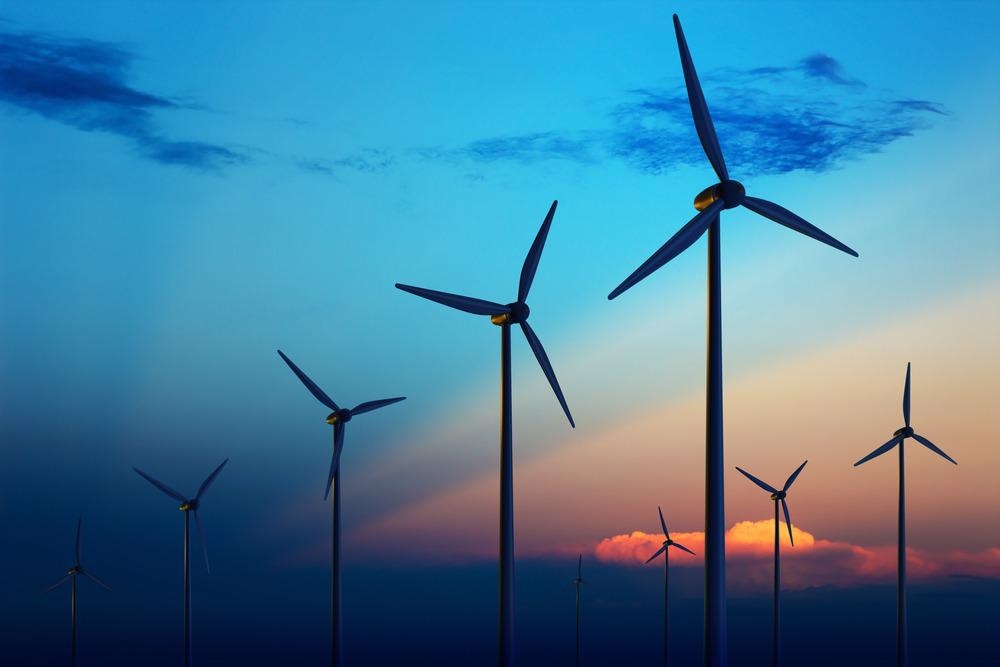
Image Credit: Johan Swanepoel/Shutterstock.com
The US Department of Energy recently chose three General Electric divisions to develop a revolutionary system for the design and production of 3D-printed wind turbine blades.
GE Renewable Energy, GE Research, and LM Wind Power will work with the Oakridge National Lab (ORNL) and the National Renewable Energy Lab (NREL) on a $6.7 million project to create an additive manufacturing method for making high-performance turbine blades for the turbines' large rotors that can be physically tested and put into use. The planned project will focus on developing a low-cost thermoplastic skin and printed reinforcement. The project’s emphasis on thermoplastics is noteworthy because this promising material could go a long way to making wind turbine blades more recyclable.
Rehauling the Wind Energy Industry
The public-private project intends to advance commercial wind energy competitiveness by reducing manufacturing cost, boosting supply chain versatility, and supplying lighter-weight blades that can be shipped more efficiently. Project leaders also hope to reduce design cycle time, enabling wind farm optimization and lowering costs.
Debuting light composite blades for jet engines more than 20 years ago, GE does have a significant history with the project’s essential supplies and techniques.
In 2019, GE unveiled 12-inch, 3D-printed turbine blades for its GE9X jet engines. Made for Boeing’s 777X jet, the carbon fiber blades effectively lowered overall engine weight and optimized power. The 777X successfully staged its first flight in 2020, with more than 300 parts made with 3D printing technology. The GE9X is currently the world’s biggest commercial jet engine from GE, with a front fan measuring more than 130 inches across.
Through the years, GE's aviation know-how has been increasingly used in the wind energy industry. In June 2020, GE's Renewable Energy division partnered with a 3D printing construction business called COBOD and construction materials company LafargeHolcim to create 3D-printed wind turbine towers. These towers could potentially increase global clean energy production while significantly lowering costs.
The new $6.7-million project results may also be game-changing for the development of larger-sized rotors for onshore and offshore turbines. The NREL has indicated that refinements in the production of blade parts could increase US-based manufacturing competitiveness. This can then lead to potential costs through extremely optimized, massive blade models that sidestep logistical limitations.
3D Printing Wind Turbine Blades
NREL and ORNL scientists have been looking at the large-scale 3D printing of wind turbine blades for some time. In an NREL paper published last year, the government organizations announced plans to develop "sandwich composite" models that take advantage of the most up-to-date technology and techniques to make lightweight, contour-optimized blade cores. The plan is to make structural cores that can support a 13-meter demonstration blade 3D-printed at ORNL, with a full-sized blade manufactured and tested at NREL.
Cutting Costs of 3D-Printed Turbines with Green Materials
Meanwhile, the University of Maine has been presented with a $2.8 million government award to produce a 3D printing process for developing large, recyclable blade molds for wind turbines.
Molds and tooling for these big blades may cost more than $10 million, and the molds’ time to market of between 16 and 20 months can constrain innovation. The carbon-reinforced thermoplastic material commonly used in massive 3D printing projects costs more than $11 per kilogram.
The university has announced plans to integrate green materials sourced from timber to lower feedstock material expense to under $4.40 per kilogram. In 2019, the university utilized the world’s largest polymer 3D printer to supplement its wind blade evaluating facility, the second biggest in the US.
University officials said the project could lead to greater sustainability in the industry by combining the latest 3D printing technology and bio-based raw materials. They pointed out that molds made using green materials could be ground up and repurposed, possibly in new molds. This is a much more sustainable approach than current ones.
The feedstock being developed by the university project appear to have mechanical properties comparable to those of aluminum but at lower fabrication costs.
Along with the $2.8 million federal award from the US Department of Energy, the university will also partner with ORNL, which was recently given a $4 million grant to develop technology that can better regulate mold surface temperatures. This is a vital aspect of mold manufacturing. The new ORNL technology could facilitate automated deposition of heating elements that lower the time and cost associated with mold fabrication.
References and Further Reading
GE Research. New Project to Design and Manufacture 3DP Thermoplastic Wind Turbine Blades. Omnexus. [Online] Available at: https://omnexus.specialchem.com/news/industry-news/3dp-thermoplastic-wind-turbine-blades-000223995
Everett, H. GE to Advance Competitiveness of Wind Energy with 3D Printed Turbine Blades. 3D Printing Industry. [Online] Available at: https://3dprintingindustry.com/news/ge-to-advance-competitiveness-of-wind-energy-with-3d-printed-turbine-blades-183959/
Agyepong-Parsons, J. World's largest 3D printer to cut wind turbine blade costs by half. Windpower Monthly. [Online] Available at: https://www.windpowermonthly.com/article/1705890/worlds-largest-3d-printer-cut-wind-turbine-blade-costs-half
Disclaimer: The views expressed here are those of the author expressed in their private capacity and do not necessarily represent the views of AZoM.com Limited T/A AZoNetwork the owner and operator of this website. This disclaimer forms part of the Terms and conditions of use of this website.