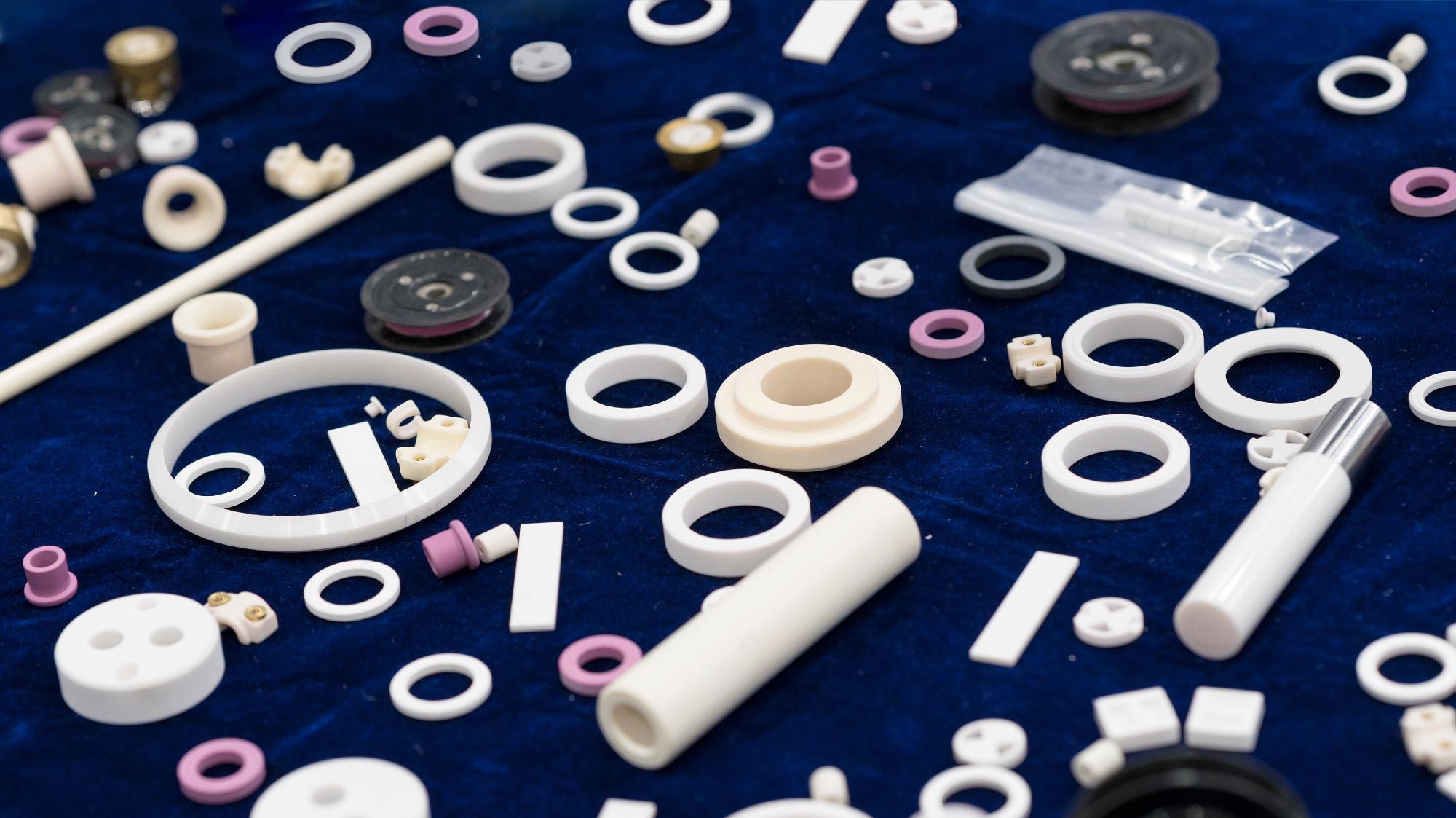
Image Credit: Aumm graphixphoto/Shutterstock.com
While the method of flash sintering can reduce the temperatures and time required to process ceramics in comparison with traditional methods, the technique often produces lower-quality products. An updated flash sintering method has been proposed that can overcome this limitation, enabling the production of multiple useful ceramic products, such as solid-state batteries, faster and at lower temperatures.
The Limitations of Flash Sintering
Over the past few decades, scientists have focused their efforts on developing energy-efficient firing techniques to satisfy growing environmental demands to reduce energy use and emissions as well as increasing economic demand to make processes more cost-effective. During the past decade, numerous novel low-energy consolidation technologies have been established, with flash sintering emerging as one of the most promising.
Flash sintering is a technique of ceramic processing that intensively heats the ceramic product via an electric current. This heats the ceramic internally rather than externally as traditional furnace heating does. The technique uses lower temperatures and can process the ceramics in shorter times meaning that, in using this technique, ceramics can be processed alongside other materials such as metals, as well as being effective at reducing energy use. Densifying ceramics via flash sintering may improve the viability of the more complex ceramic products it is used to create, such as components of solid-state batteries.
While the technology has many benefits, it also has a major drawback. Products made by flash sintering can sometimes be of lower quality than those produced by traditional techniques. This is because they are more prone to weaknesses caused by inhomogeneities in the microstructure that are a result of the thermal gradients provoked by flash sintering.
To overcome this limitation, researchers at WMG, University of Warwick, UK, an international team of researchers from various academic and industrial institutions based in France, Italy, China, and the USA, have established a new updated method of flash sintering that mitigates the impact of these thermal gradients.
The modified flash sintering technique, outlined below, will be invaluable to all fields that rely on ceramic processing, allowing them to benefit from higher quality products that have been produced in shorter time frames and with less energy.
Modifying the Flash Sintering Technique
The team reviewed the flash sintering technique with a focus on investigating how the method impacted the formation of inhomogeneous regions which result in weakening the finished ceramic product. These inhomogeneous regions currently limit how much flash sintering techniques can be used for large-scale production, which effectively limits its potential. Overall, the team’s review concluded that the thermal gradients introduced by flash sintering are the underlying cause of such microstructural inhomogeneities. They, therefore, suggested a novel method to limit the impact of these effects.
In a paper published in January 2021 in the journal MRS Bulletin, the research team, including Gareth Jones and Dr Claire Dancer from Warwick University and collaborators from the University of Trento, Wuhan University of Technology, Normandie Université, and Lucideon Ltd, demonstrate how they gathered deeper insights into the origins of microstructural variations in ceramics that undergo flash sintering.
Through this exploration, the team found that these microstructural variations could be reduced by adapting the methods of applying electrodes, using insulation to enhance the level of thermal homogeneity, adjusting the frequency of the AC current, and establishing contactless methods of introducing the electric current.
The team’s findings offer direction for future research projects as it outlines numerous routes to explore in terms of how to improve the sintering technique. The findings of the review will likely accelerate research in this area and help speed up the development of a new process that can be adopted in industry.
Meeting Global Emissions Reduction Targets
Further to providing a roadmap to future research. The team’s findings have also demonstrated a way of adapting the flash sintering technique so that it helps manufacturers meet increasing global emissions reduction targets. Current methods are energy-intensive and require long periods to process products, resulting in a great deal of spent energy. The current review highlights how flash sintering can be improved to significantly reduce energy usage of ceramics manufacturing.
The ceramic manufacturing industry is faced with the task of adapting to meet global emissions reduction targets. The work that has been achieved by the team at Warwick will likely be a significant step towards achieving these goals. However, before this can happen, much more research is needed. In particular, the team highlighted the need to investigate the impact of adapting paste compositions as they believe this would help to develop the flash sintering method further.
In the near future, we can expect further research and development of the flash sintering process, as well as the widespread adoption of the updated method.
References and Further Reading
Biesuz, M. and Sglavo, V., 2019. Flash sintering of ceramics. Journal of the European Ceramic Society, 39(2-3), pp.115-143. https://www.sciencedirect.com/science/article/abs/pii/S0955221918305442
Jones, G., Biesuz, M., Ji, W., John, S., Grimley, C., Manière, C. and Dancer, C., 2021. Promoting microstructural homogeneity during flash sintering of ceramics through thermal management. MRS Bulletin, 46(1), pp.59-66. https://link.springer.com/article/10.1557%2Fs43577-020-00010-2
Yu, M., Grasso, S., Mckinnon, R., Saunders, T. and Reece, M., 2016. Review of flash sintering: materials, mechanisms and modelling. Advances in Applied Ceramics, 116(1), pp.24-60. https://www.tandfonline.com/doi/full/10.1080/17436753.2016.1251051
Disclaimer: The views expressed here are those of the author expressed in their private capacity and do not necessarily represent the views of AZoM.com Limited T/A AZoNetwork the owner and operator of this website. This disclaimer forms part of the Terms and conditions of use of this website.