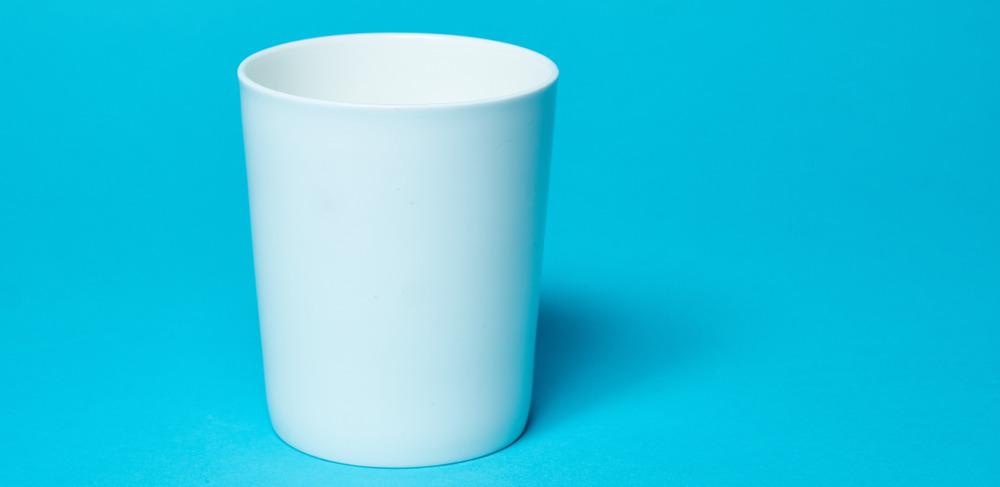
Image Credit: eugenehill/Shutterstock.com
A team of scientists at the University of Science and Technology Inner Mongolia, China, recently published findings of its study in which it established the optimum heat-treatment regime for glass-ceramics using an orthogonal experimental design.
The techniques of differential thermal analysis and scanning electron microscopy were implemented to measure the impact of heat treatment on crystallization in the glass ceramics, and, therefore, help establish the optimum heating parameters. The team found that a nucleation temperature of 750 °C for two and a half hours and a crystallization temperature was 930 °C for one hour. Their results demonstrated that under these conditions, the glass-ceramic performed better than under alternative experimental conditions, providing evidence that the selected parameters were optimal for producing higher-quality glass-ceramics.
Optimizing Blast Furnace Techniques
Water-quenched slag is often used as a raw material to create slag powder and cement. While there are benefits of this method, it also has numerous disadvantages, such as the high cost of operation set-up, the low added value of products, and the inefficient use of slag heat.
Calcium oxide (CaO), silicon dioxide (SiO2), magnesium oxide (MgO), and aluminum oxide (Al2O3) are the main chemical components of slag used in blast furnaces, accounting for roughly 90% of total slag. It provides an ideal raw material for producing glass-ceramics used for decorative purposes and presents an opportunity to increase the added value to blast furnace slag. The production of glass-ceramics from molten blast furnace slag on the large-scale poses an opportunity to enhance the utilization of slag and improve the efficiency of the use of its heat energy.
Research into glass-ceramics has revealed that the proportion of blast furnace slag is up to 60%. A new study conducted by the team at the University of Science and Technology Inner Mongolia, China, in the Journal of High Temperature Materials and Processes, has established a methodology using thermal analysis and electron microscopy to optimize this process and raises the proportion of blast furnace slag to 70%. The team’s results, which are detailed below, demonstrate an enhanced method that optimizes the use of slag and heat energy.
Using Thermal Analysis and Electron Microscopy to Investigate Glass-Ceramics
A glass sample was ground into a powder of particles less than 0.074 mm diameter and α-Al2O3 was adopted as a reference. The team then used differential thermal analysis (DTA) to analyze the glass powders and establish the heat-treatment temperature. A scanning electron microscope was used to determine the sample’s microstructure. The glass-ceramics were produced by combining 70% blast furnace slag with nucleating agents of 1% Cr2O3 and 4% TiO2.
From previous research, it is understood that the precipitation of crystal nuclei is an endothermic process and that crystallization is an exothermic process. Therefore, the differential scanning calorimetry (DSC) curve can be analyzed to read the endo- and exothermic peaks that represent the nucleation and crystallization processes of the glass, respectively. The results showed an endothermic peak at 710 °C and two exothermic peaks at 944.7 °C and 988.8 °C.
The sample was then heat-treated to further analyze the crystallization temperature by determining the temperatures of the two exothermic peaks. The team found that the physical and chemical properties of the glass were determined by factors such as grain size, quantity, and distribution. It was concluded that to ensure glass-ceramics are produced with a good microstructure, it is vital to use an appropriate heat-treatment protocol.
Conclusions
Using a raw material of 70% blast furnace slag and nucleating agents of 1% Cr2O3 and 4% TiO2 in an orthogonal experiment, the team based in China were able to optimize the heat-treatment process used for producing glass-ceramics of calcium oxide (CaO), silicon dioxide (SiO2), magnesium oxide (MgO), and aluminum oxide (Al2O3).
The crystallization temperature was found to have the most significant impact on the glass-ceramics’s flexural strength. Nucleation time was found to be the second most influential factor on this strength, followed by nucleation temperature. Crystallization time was shown to have the least influence on flexural strength.
The team’s findings will help enhance blast furnace processes, allowing for higher-quality glass-ceramics to be produced with improved physicochemical properties and fewer defaults. Glass ceramic manufacturers now have a solution to remedying the defects caused by the high addition of blast furnace slag by optimizing the heat-treatment parameters.
It was concluded that the optimal parameters for preparing glass-ceramics with a flexural strength of as much as 102.2 MPa were a nucleation temperature of 750 °C for two and a half hours and a crystallization temperature of 930 °C for one hour.
References and Further Reading
Erkmen, Z., Çataklı, E. and Öveçoğlu, L., 2009. Characterisation and crystallisation kinetics of glass ceramics developed from Erdemir blast furnace slags containing Cr2O3and TiO2nucleants. Advances in Applied Ceramics, 108(1), pp.57-66. https://www.researchgate.net/publication/233515475_Characterisation_and_crystallisation_kinetics_of_glass_ceramics_developed_from_Erdemir_blast_furnace_slags_containing_Cr2O3_and_TiO2_nucleants
Liu, Z., Zong, Y. and Hou, J., 2015. Preparation of slag glass ceramic from electric arc furnace slag, quartz sand and talc under various MgO/Al2O3ratios. Advances in Applied Ceramics, pp.1-8. https://www.tandfonline.com/doi/abs/10.1179/1743676115Y.0000000052
Wang, Y., Liu, P., Luo, G., Liu, Z. and Cao, P., 2020. Optimization of heat treatment of glass-ceramics made from blast furnace slag. High Temperature Materials and Processes, 39(1), pp.539-544. https://www.degruyter.com/document/doi/10.1515/htmp-2020-0059/html
Disclaimer: The views expressed here are those of the author expressed in their private capacity and do not necessarily represent the views of AZoM.com Limited T/A AZoNetwork the owner and operator of this website. This disclaimer forms part of the Terms and conditions of use of this website.