In this interview, AZoM speaks to Paul Haigh, Product Manager at CARBOLITE GERO, about the QA of raw materials process testing within the cement industry.
Can you start by giving our readers an overview of the Verder Scientific group of companies?
The Verder Scientific group is made up of a number of companies, each with its own specialism.
These include materialography and hardness testing from QATM, heat treatment solutions from CARBOLITE GERO, elemental analysis from ELTRA, milling and sieving solutions from RETSCH, and particle characterization and absorption technology from Microtrac MRB.
The group is supported by 22 global sales offices and solutions centers. These centers can offer custom solutions, trials, and proof of concept work for almost any specific process.
What is the connection between Verder Scientific’s portfolio and the cement industry?
All cement-producing facilities should be carrying out small-scale tests on a routine basis or even pilot plant production.
Tests often take place in laboratories at temperatures from ambient up to 1600°C. CARBOLITE GERO manufactures a range of lab and industrial products suitable for use at ambient to 3000°C and these products are suitable for use within the cement industry for both quality control and for process improvement.
There was a dramatic increase in global cement production in 2010, with demand continuing to rise. Top global cement producers include LafargeHolcim with 108 plants and 386-million-ton capacity; followed by Anhui Conch, then China National Building Material.
A number of national and international standards govern cement production and there are a number of types of cement available to meet each of them. The current British and European standard for the 27 types of common cement available in Europe is EN 197-1:2011.
For cement and for masonry cement, it is EN 413-1:2011. These product specifications are all supported by standardized test methods in the EN 196 series. Verder Scientific frequently works to all of these standards.
What are some common applications in the cement industry and how do the CARBOLITE GERO principles of design apply to these?
There are six very common applications in the cement industry. These are drying material samples, ashing, calcining, loss on ignition testing, testing burnability of cement, and testing free lime content of cement.
Cement research labs within a university, a civil engineering department, or otherwise sponsored by a production company may also need to investigate pilot plant production clinker and perform research into alternative heating fuels, such as waste tires, bone meal, and solid recovered fuels. Each of these applications will be covered by relevant testing standards.
Behind every furnace and oven that CARBOLITE GERO manufacture, we work to a core set of principles.
The first principle is ‘world-class every time’ - we always look to offer the best solution on the market. Our principle of ‘high-quality components’ means that we never compromise with inferior parts - we innovate and continuously improve.
We work to a principle of ‘designed for long life,’ which means we provide high-value products with a built-in life expectancy that offers a significant product lifetime, therefore saving on cost.
Finally, we work on the principle of ‘not designed for obsolescence’ - all our products are designed to be serviced and maintained during a long working life. Applications in the cement industry can be particularly challenging. We believe that our principles of design make CARBOLITE GERO highly suited to support customers in this demanding industry.
Can you give our readers an overview of the typical features and uses of a CARBOLITE GERO fan convection oven?
A fan convection oven can be used for chemical analysis of cement, determination of total organic carbon, or determination of moisture content of solid recovered fuels.
Typically, these applications are performed below 300°C, but we offer an oven capability of up to 700°C. Generally, 30 to 440 liters is a typical volume range, although we also offer a three-meter cube size and bespoke larger sizes.
Our ovens have chemically resistant stainless-steel liners throughout, offering rapid heating and temperature recovery with excellent temperature uniformity.
Our ovens offer a number of other key features, for example, excellent moisture extraction. Fresh air enters an inlet port before reaching the heating elements and moist heated air leaves through an outlet port.
The amount of fresh air entering - and therefore moisture exiting - can be controlled. Where applications involve significant levels of moisture, we can add a dedicated moisture extraction unit that increases the airflow through the chamber, offering better, faster, and more efficient drying.
The oven’s chemically resistant liner is manufactured from stainless steel, which is both physically hard-wearing and provides a long lifetime. Finally, CARBOLITE GERO only purchases from well-established and proven heating element suppliers.
This world-class heating technology combined with our 80+ years of experience ensures that all our products offer excellent temperature uniformity and fast heat up and recovery times.
What benefits do these features offer to a typical process owner?
Our moisture extraction option with faster and better drying will result in samples requiring less time in the oven.
This results in a faster turnaround, potentially reducing the need for multiple ovens to meet that same throughput requirement and ultimately leading to a reduction in space requirements, a reduction in capital cost and also a reduction in the amount of time that users need to spend using the oven.
Using a resistant liner will result in a long-term return on the capital investment. In some instances, we found that when compared to a competitor's unit, our liners can last up to three times as long in a potentially corrosive environment.
A corrosion-resistant liner allows us to ensure that we do not see any corrosion in the test sample inside the oven, therefore reducing the risk of contamination. Finally, the heat tech offering a faster turnaround leads to more flexibility and further potential reductions in capital cost and space requirements.
Can you give our readers more information on the AAF Ashing Furnace, its potential applications, and benefits?
The AAF ashing furnace is ideally suited for loss on ignition testing, determination of total organic carbon, and determination of ash content.
It offers class-leading temperature control and thermal insulation with a highly durable, hard-wearing refractory installation. The instrument’s maximum temperature is 1200°C and it is available in four sizes: 3, 7, 18 or 32-liter models.
A high flow of preheated air ensures complete combustion of the sample, while the furnace elements are protected from any build-up of combustible products and the upward opening front door ensures radiant heat is minimized for the operator. Sample holders are also available, which maximize the working area and allow for easy preparation of samples.
In addition to the standard AAF Ashing Furnace, we also offer an integrated balance option. This can form a basic loss of mass against temperature recording instrument and a very basic thermogravimetric analysis system.
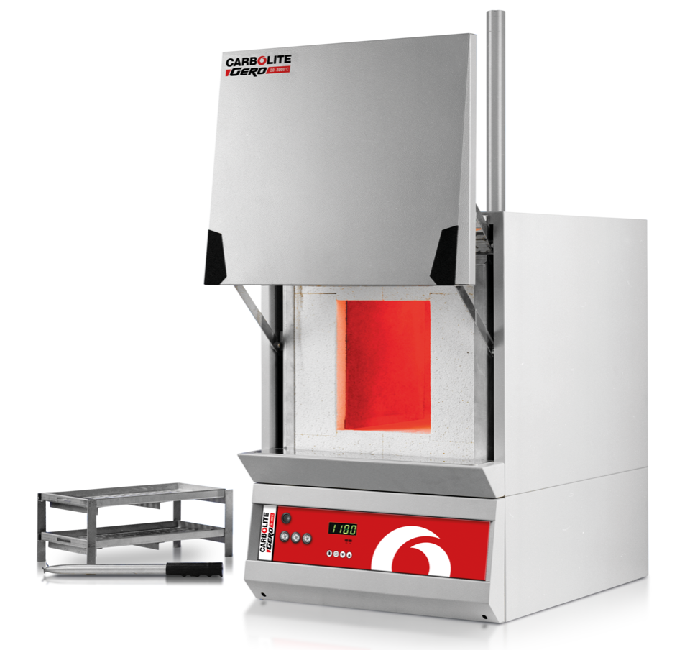
AAF Ashing Furnace. Image Credit: CARBOLITE GERO
We can use this measurement for the determination of ash content and also the determination of total organic carbon. A typical unit would have an upper working limit of 1100°C and a maximum capacity for the balance of three kilograms.
These furnaces have hard-wearing insulation so can withstand the demands of a busy testing laboratory. The heating elements are protected from chemical contamination from the sample, ensuring product longevity, while the thermal insulation materials used to make for a cooler external casing.
The vertical lift door provides added protection for the operator from heat radiation if the door is opened under high temperatures, which is a requirement of some test standards such as EN 610 10. Finally, a preheated airflow through the chamber speeds up the ashing process and ensures that moisture is fully removed from the samples.
In terms of the benefits for the end-user, the hard-wearing insulation results in a lower lifetime cost of the unit while also reducing the risk of contamination. The furnace is well specified, using refractory instead of cheaper materials such as low thermal mass insulation that a budget solution might use.
The furnace should last many times longer than the competition’s products. The upfront cost may be higher, but the return on investment from this durable world-class design pays for itself many times over. With high-quality insulation, there won’t be flaking of insulation into the sample that could potentially contaminate results.
How do the CWF General Purpose Furnace and RHF High-Temperature Furnace compare to the AAF in terms of potential applications and features?
The CWF General Purpose Furnace is also well suited to the chemical analysis of cement, fly ash for concrete, and the verification of chemical and physical requirements. These models are available with maximum temperatures up to 1300°C and we have 5, 13, or 23-liter standard models available.
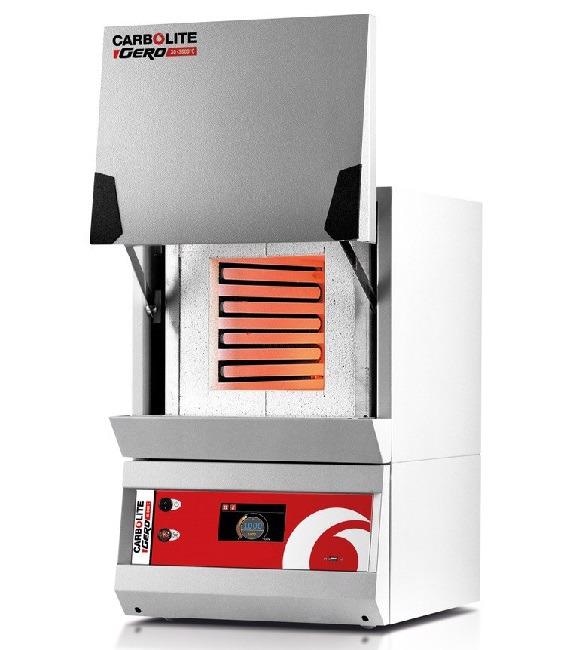
CWF General Purpose Furnace. Image Credit: CARBOLITE GERO
Larger sizes are also available if required. These models benefit from improved versatility, thanks to a higher operating temperature than the AAF range, plus uniformity due to their reduced airflow.
Again, the upward opening front door once ensures that radiant heat is minimized for the operator.
The RHF High-Temperature Furnace offers even higher temperature potential and is ideal for burnability testing of alite and belite as these applications require a higher temperature.
The RHF furnaces are available with maximum temperatures of 1400, 1500, or 1600°C, and both the 3 and 8-liter models are an ideal choice for this type of test.
Robust high-quality silicon carbide elements provide a long working life for this range and again, the upward opening front door ensures radiant heat is minimized towards the operator.
Both the CWF and RHF furnaces have the same features and corresponding performance as the AAF ashing furnaces and all of those benefits are realized for both groups of products.
However, these products have less airflow than the dedicated ashing furnace, meaning that they offer a better temperature uniformity within the working chamber.
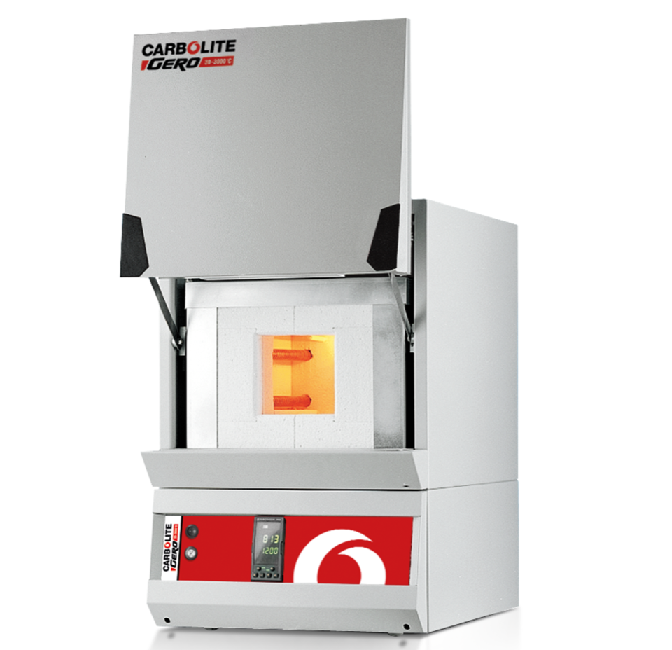
RHF High-Temperature Furnace. Image Credit: CARBOLITE GERO
What are the benefits and potential applications of employing a rotating tube furnace solution?
We offer two rotating tube furnace solutions, both of which are designed to agitate a sample whilst heating it. We offer a batch solution as well as a continuous system.
Testing with the batch testing system involves a small sample of the material being placed inside the rotating vessel before being rotated and agitated.
It is built using our class-leading new tube furnace range and is typically a smaller unit designed for working with granules and powders in a sealed system with gas flow control. The residency time of the sample within the vessel is controlled by the operator.
The continuous process system has all the same features as the batch process instrument but with continuous flow. Here the sample material is fed into the work tube via a hopper arrangement. The speed that the sample material passes through the furnace is controlled by the speed that the work tube rotates and the angle that the work tube is held at. This level of flexibility means that it is also possible to work with temperature gradients, gradually increasing or decreasing the temperature over time.
We have this type of product available in our solution center for trials as we understand that this may be a novel solution for some forms of testing.
Rotating tube furnaces offer a number of distinct benefits to users. The distribution of power is optimized along the work tube, giving optimum temperature uniformity.
These new models also incorporate increased insulation thickness with improved performance compared to previous models. This delivers lower power usage, a positive environmental impact, and the safety benefit of a lower furnace case temperature.
The agitation of the samples exposes the surface area of the material so that both the heat and the atmosphere within the work tube are effectively managed. This significantly reduces process time compared to a static system.
As well as flexibility and cost savings due to reduced power usage, rotating tube furnaces also offer space savings, reducing the potential footprint of the furnace because it is possible to achieve an equivalent heated body in a much smaller system.
Finally, how does the CC-T1 Temperature Controller work with the range of furnace products available?
The CC-T1 Temperature Controller is our class-leading intuitive touchscreen controller which is available with all the units discussed earlier. It has a full-color touchscreen, three password-protected user levels, ten programs with 24 segments for each unique program, data logging to a USB stick in CSV format, and eight user-selectable languages.
Overall, CARBOLITE GERO’s 80 years of industry knowledge and product know-how have been condensed into our class-leading product range, with the CC-T1 Temperature Controller providing a uniform interface suitable for use with our full range of products.
About Paul Haigh
Paul Haigh is a Chartered Engineer. He has worked on the continuous development of laboratory and industrial furnaces and ovens for much of his career.
Initially, Paul worked with Carbolite Gero as a ‘Teaching Company Assistant’ (now known as a KTP) introducing a ceramic forming process. After many years working in the engineering team and managing product development, Paul has spent the last five years as the Product Manager for Carbolite Gero in the U.K.
Disclaimer: The views expressed here are those of the interviewee and do not necessarily represent the views of AZoM.com Limited (T/A) AZoNetwork, the owner and operator of this website. This disclaimer forms part of the Terms and Conditions of use of this website.