What is FAC?
A well-known source of problems in fossil fuel and nuclear powerplants is flow accelerated corrosion, also known as FAC. This kind of corrosion can occur when carbon steel piping and its components become degraded through the presence of steam water or flowing water that has low-dissolved oxygen.
FAC occurs when the normally protective oxide layer on the inside surface of low alloy steel and carbon piping dissolves. De-oxygenated water at elevated temperatures removes the naturally-formed iron oxides on the pipe’s exposed surface.
This thins the pipe wall, which can potentially cause leaks and catastrophic ruptures, negatively impacting both plant reliability and personnel safety.
Regulatory bodies, utilities and industry groups such as the Electric Power Research Institute (EPRI) have started paying attention to this issue due to highly publicized accidents. OSHA discussed FAC in feedwater piping systems in a hazards bulletin issued in 1996.
The insurance industry has, in recent years, become interested in the economic impact of FAC in terms of personnel hazards, equipment loss and plant downtime. There has been research done over more than 20 years to better understand the cause of FAC and methods to prevent it.
Research completed through the EPRI showed that there are a number of variables that influence FAC, including:
- Water flow variables, such as upstream influences, fitting geometry, diameter and fluid velocity
- The temperature of the water being used, as well as the dissolved oxygen levels and pH at temperature in the water
- The steel’s composition, especially the alloying elements of molybdenum (Mo), copper (Cu) and chromium (Cr)
Of these variables, the material composition has been shown to exert the most influence of FAC through both plant experience and laboratory testing.1
FAC Prevention Methods
The rate of FAC has been shown to greatly reduce small quantities of alloying elements; chromium, in particular, is used.
Michel Bouchacourt of Electricite de France has conducted research that demonstrates substitution of chromium creates an oxide structure of FeCr2O4 at higher levels of trace chromium (above ~0.1%); this is significantly less soluble than the usual magnetite (Fe3O4) oxide layer present in carbon steel piping.2
Because of this research, when inspecting for FAC, it has become an industry convention to closely monitor trace alloy content. The planning of inspection protocol is additionally approved by monitoring trace alloy content.
As an example, it might be possible to omit inspected piping from future FAC inspection if it contains sufficient chromium content. The composition data can also be entered into EPRI CHECWORKS™ software, which improves the overall FAC data model and assists in interpreting the inspection data.
The usual way to perform chemical analysis of carbon steel piping in FAC inspection is through laboratory analysis of filings or through using spark-based optical emission spectroscopy.
This is because of the need for the detection of very low levels of chromium (~0.02%). Multiple advantages for an FAC prevention program are provided by the Thermo ScientificTM NitonTM XL5 Plus analyzer.
Handheld x-ray fluorescence (XRF) technology has developed into an ideal method for the FAC analysis application, thanks to its improved detection limits.
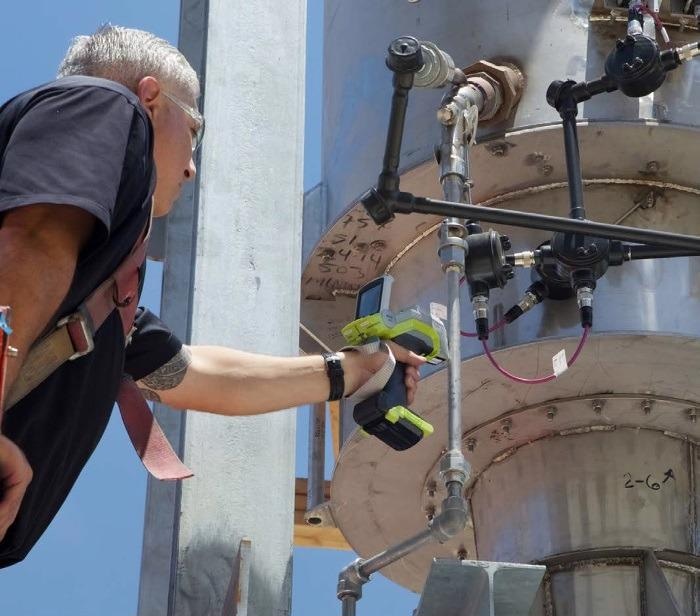
An inspection is conducted using the handheld Niton XL5 Plus XRF analyzer. Image Credit: Thermo Fisher Scientific – Handheld Elemental & Radiation Detection
Niton XL5 Plus Handheld XRF as Part of the FAC Inspection Protocol
The lightest and smallest high-performance XRF metal analyzer currently on the market is the new Niton XL5 Plus. Operator fatigue is reduced, and a greater number of test points can be accessed because of the Niton XL5 Plus’s lightweight and small size.
The best light element sensitivity and highest performance for the most demanding applications, such as FAC measurement, are enabled by and the latest silicon drift detector technology, a powerful 5W X-ray tube and compact measurement geometry.
Accurate and fast elemental analysis in demanding power generation applications is delivered by the Niton XL5 Plus. This analyzer provides the fossil and nuclear power-generation industries many benefits, including:
- Rugged housing, dustproof and splashproof to handle rough environments
- Accurate image capture and sample positioning enabled by small spot analysis and integrated camera
- East optimization for specific applications (like FAC measurement) and custom workflow solutions enabled by a flexible user interface
- Testing and productivity in tight spots without operator fatigue improved by the lightweight and small size
- Reliable and fast FAC testing facilitated by excellent Mo, Cu and Cr trace element detection
- Confident results every time thanks to unparalleled metal-grade and chemistry accuracy
The latest release in the market leading Niton handheld XRF product line is the Niton XL5 Plus. This device is designed to deliver the fastest analysis time for discovering trace elements (like Mo, Cu and Cr), high accuracy and low detection limits.
The Niton XL5 Plus is engineered for ease of use, reliability and high performance. This is in line with Thermo Scientific’s reputation for leadership through excellence in innovation.
Test Method and Results
After ensuring the surface was clear and clean of any contaminants, certified samples and reference standards were analyzed. The minimum analysis time and the sample preparation requirements used were dictated by data quality objectives.
Carbon steels are the typical metal alloys that are at risk of FAC. When exposed to atmospheric conditions, these alloys will oxidize. When performing an XRF analysis, the accuracy of the reading can be impacted by this oxide coating.
This means that in order to ensure an accurate reading, it is of extreme importance to remove any corrosion.
The surface can also often have grease, oil, or paint on it, in addition to oxidation. The results of the analysis can be impacted by calcium or metals such as zinc or titanium, which are typically found in paint.
Molybdenum and other additives can be found in grease. All surface contamination must be removed in the area to be analyzed in order to get accurate trace element readings.
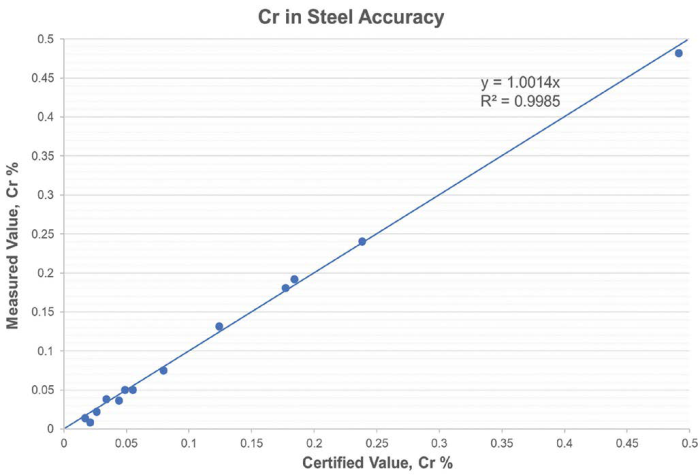
Figure 1. Chromium in steel accuracy using the Niton XL5 Plus analyzer. Image Credit: Thermo Fisher Scientific – Handheld Elemental & Radiation Detection
The correlation curve, certified results vs. the Niton XL5 Plus analyzer results is shown in Figure 1. The coefficient of determination (R2) value is a measure of how closely the data sets correlate with each other, where a perfect correlation would have an R2 of 1.
The data demonstrate a very good (R2 > 0.99) agreement between laboratory results and Niton XL5 Plus results. The excellent repeatability for low levels of Mo, Cu and Cr using the Niton XL5 Plus is demonstrated in the data in Table 1.
Table 1. Accuracy and repeatability for Cr, Cu and Mo in carbon steel (15 second total test time). Source: Thermo Fisher Scientific – Handheld Elemental & Radiation Detection
Measurement |
Cr |
Cu |
Mo |
1 |
0.079 |
0.051 |
0.0040 |
2 |
0.078 |
0.051 |
0.0047 |
3 |
0.071 |
0.055 |
0.0037 |
4 |
0.078 |
0.048 |
0.0044 |
5 |
0.081 |
0.053 |
0.0055 |
6 |
0.073 |
0.047 |
0.0040 |
7 |
0.072 |
0.057 |
0.0046 |
8 |
0.076 |
0.047 |
0.0042 |
9 |
0.083 |
0.047 |
0.0048 |
10 |
0.074 |
0.055 |
0.0044 |
Average |
0.077 |
0.051 |
0.0044 |
Std. Dev. |
0.004 |
0.004 |
0.0005 |
Ref Value |
0.079 |
0.050 |
0.0047 |
This test used a total of 15 seconds of measurement time. Using a longer measurement time can further improve the repeatability and sensitivity of Cr measurement.
Conclusion
Excellent trace element precision and sensitivity are provided by the Niton XL5 Plus for low levels of Cu, Ni and Cr.
These results agree with the laboratory results. The new analyzer is able to reliably detect 0.01% Cr levels in steel when given appropriate sample preparation. Even better results can be achieved by using extended measurement time.
The ideal solution for the most difficult analytical requirements is provided through the combination of direct industry experience, software and hardware when low detection limits or the highest sample throughput are critical.
The Niton XL5 Plus is the ideal tool for nuclear or fossil power plant FAC programs because of its improved analytical capability for trace quantities of Mo, Cu and Cr, as well as its other unique capabilities.
The Niton XL5 Plus can also provide other services in addition to FAC measurement, including quickly providing full chemical analysis and grade identification for different alloy grades used in the power-generation industry.
References
- Chexal, B., Goyette, L.F., Horowitz, J.S., Ruscak, M., Predicting the Impact of Chromium on Flow Accelerated Corrosion, PVP-Vol 338, Pressure
- Vessels and Piping Codes and Standards, ASME 1996 Chexal, Goyette, Horowitz, Ruscak, op. cit., loc. cit.
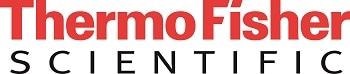
This information has been sourced, reviewed and adapted from materials provided by Thermo Fisher Scientific – Handheld Elemental & Radiation Detection.
For more information on this source, please visit Thermo Fisher Scientific – Handheld Elemental & Radiation Detection.