Sponsored by Mo-SciMay 20 2021
Sealing glasses are used to make reliable hermetic seals between ceramic, metal, and glass components. They also offer resistance to chemical attack, stability under thermal cycling, and tunable thermal expansion properties.
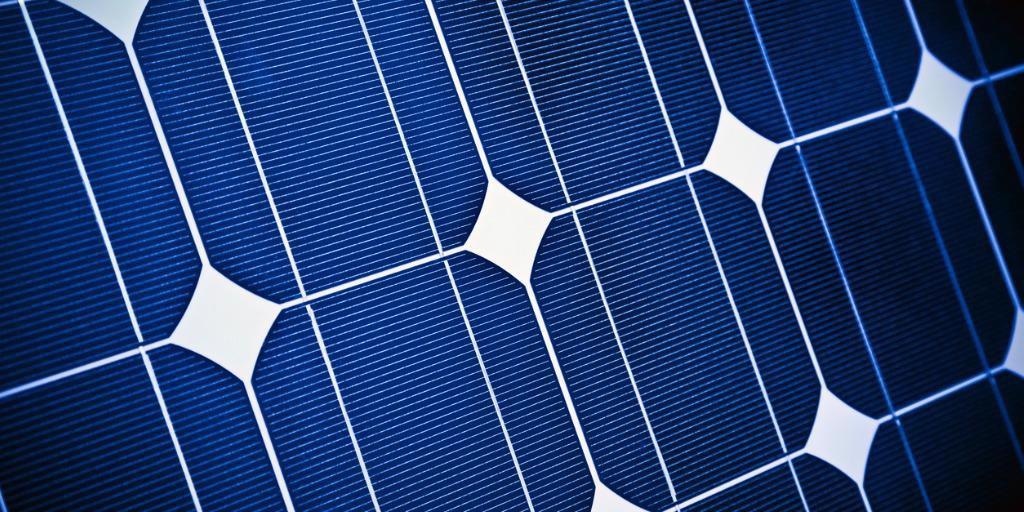
Image Credit: iStock
What Makes Sealing Glasses so Useful?
Using glass as a sealing material has many benefits, including the fact that it is possible to tune its coefficient of thermal expansion (CTE) during production. Because many materials expand when heated, having two sealed components expand at different rates means that the seal between them can be compromised.
The thermal expansion coefficient of sealing glasses can be made to match that of a range of different engineering materials by adjusting the manufacturing and composition parameters. This means that when components undergo thermal expansion, the glass seals remain sealed.
Sealing glasses have widespread use because of this property. The material is used especially in the production of reed switches, electric discharge tubes, vacuum tubes, and other electronic components, as well as in other glass-to-metal applications.
Specialized sealing glasses can be made to have other desirable properties, including the ability to be laser-bonded, stability under thermal cycling, and resistance to chemical attack. Below, this article will explore some of the high-spec applications for which these characteristics render sealing glasses suitable.
Solar Cells
There has been significant attention in recent years being paid to a class of minerals with an ABX3 structure known as perovskites as these may be an alternative to silicon in photovoltaic cells.1
The material promises both high photovoltaic efficiency and low manufacturing costs, and worldwide efforts are underway to commercialize them.
Exposing perovskites to even small amounts of moisture can cause complete loss of functionality, which is one of the issues facing the development of perovskite solar cells. It is therefore essential to hermetically encapsulate perovskites, both to prevent lead-containing chemicals from leaking out and to prevent moisture from getting into the cell.
Using sealing glasses to encapsulate perovskite photovoltaic elements can ensure that they remain completely sealed from the external environment.
Perovskite crystals can be protected from moisture incursion and have their lifetime drastically increased using laser-assisted bonding of glass frit, additionally ensuring long-term hermetic encapsulation.2
Long-term stability of the entire cell is ensured by matching the thermal expansion coefficient of the surrounding materials to that of the glass.
Metal Ion and Thermal Batteries
The battery industry has been undergoing radical changes as it adapts to a wider transition towards renewable energy sources and increased demand for more compact and efficient energy storage solutions such as those used in electric cars.
For both commercial and experimental battery technologies, sealing glass plays a vital role. The current go-to for renewable energy storage applications and electric vehicles are lithium-ion (Li-ion) batteries, which require hermetic seals that exhibit long-term stability at high temperatures and resistance to chemical attack.
This is also true of sodium-ion (Na-ion) batteries, which are currently being investigated as a low-cost alternative to lithium-ion technology.
The ideal solution for metal ion batteries is sealing glasses. Specialized sealing glasses offer reliable performance under thermal cycling and resistance to alkali ion corrosion, in addition to offering a wide range of customizable thermal expansion coefficients and operating temperatures.
One application in which sealing glasses are widely used is for molten salt batteries, where they act as a high-performance alternative to metal or polymeric seals.
Glass seals can easily withstand the required operating temperatures of molten salt batteries (approx. 300-350 °C) and are also capable of withstanding harsh chemical conditions.3,4
High-Temperature Sensors
Another common use for glass seals is as feedthroughs for sensors deployed in high-temperature conditions. Glass seals provide predictable thermal expansion, enabling sensor feedthroughs to remain tightly sealed under extreme thermal stresses.
This is particularly useful in automotive applications and chemical processing plants. Thanks to thermal cycling and resistance to corrosion, glass feedthroughs provide reliable hermetic sealing over a long lifetime.
Solid Oxide Fuel Cells (SOFCs)
SOFCs, or solid oxide fuel cells, are characterized by the use of high operating temperatures and a solid electrolyte. They are attracting attention as a highly versatile and efficient way to produce electrical power from fuel.
They have high operating temperatures (typically 500°C to 1000°C), which poses a significant engineering challenge. Despite this, they are hoped to offer long-life power generation at low cost.
The electrolyte, cathode, and anode must remain hermetically separated inside a SOFC. Conventional polymeric gasket seals are not suitable for use in SOFCs because of high-temperature corrosion, oxidation, and creep.
In order to address this, a range of viscous compliant glass seals for SOFC applications has been developed by Mo-Sci. These glasses are designed to remain completely vitreous throughout their application, in contrast to conventional glass-ceramic seals, which are partially crystallized.
These viscous glass seals can heal themselves if any cracking occurs due to thermal cycling by remaining in a glassy, amorphous state throughout use. This ensures excellent bonding with ceramics and metals while still providing increased resistance to the extreme thermal stresses within SOFCs.5
The hope is that the widespread use and commercialization of SOFCs will be aided by this revolutionary glass sealing technology.
References
- Extance, A. The reality behind solar power’s next star material. Nature 570, 429–432 (2019).
- Emami, S., Martins, J., Ivanou, D. & Mendes, A. Advanced hermetic encapsulation of perovskite solar cells: the route to commercialization. J. Mater. Chem. A 8, 2654–2662 (2020).
- Lu, X., Xia, G., Lemmon, J. P. & Yang, Z. Advanced materials for sodium-beta alumina batteries: Status, challenges and perspectives. Journal of Power Sources 195, 2431–2442 (2010).
- Smeacetto, F. et al. Glass-ceramic joining material for sodium-based battery. Ceramics International 43, (2017).
- Hsu, J.-H. et al. An alkali-free barium borosilicate viscous sealing glass for solid oxide fuel cells. Journal of Power Sources 270, 14–20 (2014).
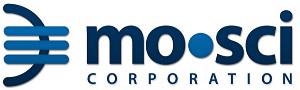
This information has been sourced, reviewed, and adapted from materials provided by Mo-Sci Corp.
For more information on this source, please visit Mo-Sci Corp.