There is a new generation of fiber optic sensing systems, which can be employed to great utility in the monitoring of well conditions within the oil and gas industry, resulting in improved performance.
The engineer and scientist onsite can make decisions that support operational optimization using critical data from the downhole well environment from distributed fiber optic sensing (DFOS). This informed decision naturally leads to well production performance enhancement along with safety at the well site, and ultimately works towards optimizing production from oil and gas wells. Currently, there is no other method that obtains the same quality and level of detail about physical conditions in a wellbore when compared to fiber optics.
Chiefly, distributed acoustic sensing (DAS) is used to listen to hydraulic fracturing related signals, fluid and gas flow signals, along with sensing seismic source response, such as that which takes place in a vertical seismic profile (VSP). DAS senses changes in small physical acoustic vibrations along a glass fiber optic strand encased in a cable to measure vibrations. The fiber in the subsurface fiber optic cable offers thousands of detection points.
Continuous, real-time measurements are facilitated by DFOS technology, which takes place along the entire length of a fiber optic cable at minimal spatial intervals. Distributed sensing does not rely upon manufactured, discrete sensors, unlike conventional sensor systems that rely on discrete sensors measuring at pre-determined points, but instead uses the optical fiber itself as a sensing device as well as a two-way transmitter of the signal (light). The sensing element is optical fiber, without any additional transducers in the optical path. Surface instruments termed interrogator units (IU) are used to send a series of laser light pulses into the fiber and additionally to record the return of the naturally occurring back-scattered light signal, as a function of time. During this process, the distributed sensing system can measure at all points along the fiber, which occur at a pre-determined clock-time interval over periods of well operational time.
Thanks to the fact that fiber optic cable is durable and can be installed in harsh environments for long periods of time, the technology offers the opportunity for those seeking to implement environmental monitoring in sensitive geologic operations. Often, geofluid systems need dynamic acoustic, strain, temperature and pressure monitoring that can take place in extreme environments like those found at a great depth, pressure or temperature. Thanks to their ability to withstand such adverse or challenging environments, sensors that employ fiber optic cables are in high demand for such use. Downhole application includes their use in flow-back operations, geothermal wells, oil and gas wells (hydraulic fracture completion operations, long-term well monitoring, and well-integrity monitoring), along with other harsh environment applications like deep industrial waste disposal wells.
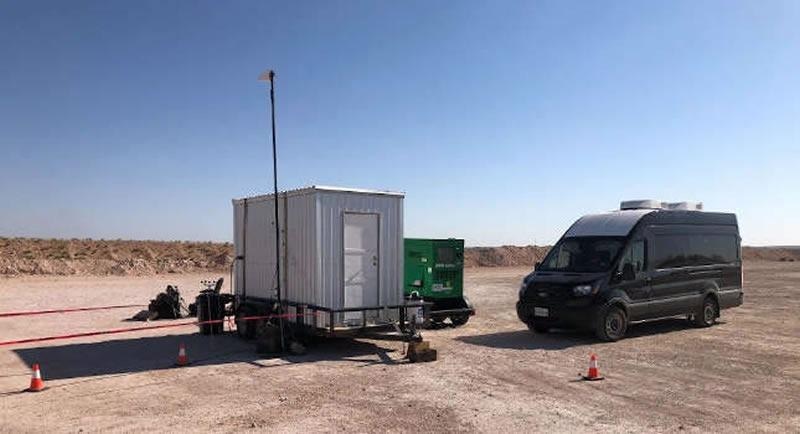
Neubrescope set up on site near well operations. Image Credit: Neubrex Energy Services
The capability of measuring multiple physical phenomena along the complete length of an internal borehole is critical, and a capability that is provided by distributed fiber optic sensing. In addition, distributed fiber optic sensing also monitors the conditions of the near-well bore region of subsurface rock formations, as well as used in a number of other applications. These include the characterization of contaminated bedrock aquifers, the provision of data to help manage petroleum and geothermal reservoirs, along with the monitoring, verification and accounting of geologic carbon sequestration projects.
There are undeniably huge benefits to DAS technology. However, with the increasing need for monitoring geofluid systems, like those at work in hydraulic fracture operations, there have been developments in more specialized technologies; ones that are suitable for harsh operational environments but remain capable of high sensitivity and reliability. One of the technologies that has been developed in this vein is distributed temperature and strain sensing (DTSS), a field-tested, revolutionary and complementary technology to DAS.
Distributed Temperature, Strain Sensing
Though DAS has undoubtedly had its moment in the spotlight and remains useful for multiple applications, DTSS is arguably the next front-runner technology. The technology DTSS offers temperature measurements, as well as the absolute, differential and dynamic strain deformation profiles which are present along the full length of optical fiber. This latter measurement can operate over distances reaching up to tens of kilometers, offering a spatial resolution of the DTSS measurements which is generally an order of magnitude better than DAS.
In addition to providing additional sensing capabilities when compared to DAS, DTSS provides detects and records simultaneous and independent measurements of both temperature and strain distribution. This is performed at centimeter-order spatial resolution, which is significantly more spatial resolution than DAS is can deliver. Spatial resolution, of course, refers to the measurement determining how small an object should be in order for it to be detected by an imaging system, which is measured in line pairs per centimeter (lp/cm).
This particular type of distributed temperature and strain sensing system has been developed by Neubrex Ltd., Kobe, Japan, and is used by Neubrex Energy Services, which represents the U.S. division of Japan-based Neubrex Company, using a DTSS product line called Neubrescope.
Neubrescope DTSS is well designed for monitoring hydraulic fracturing operations. Nevertheless, oil and gas industry companies are still in the learning, testing, qualification and acceptance phase of using fiber optics and how it can be reliably, safely and economically installed and used in a well. Once installed in a well, they are also learning what measurements can be made, and how it differs from competing technologies. The value proposition of the technology application is actively being explored by many oil and gas companies, both domestically in the U.S. and internationally in numerous oil and gas wells.”
Dana Jurick, General Manager, Neubrex Energy Services
Jurick further commented that temperature, acoustics, strain, and pressure – DTSS, DPS and DAS measurements – can be taken in real-time while hydraulic fracturing is occurring. She commented:
“This helps field engineers better understand what is happening in these deep wells much better than with previous technologies. Subsequently, data-driven changes or adjustments to operational plans can be made when warranted, to optimize the operation to hopefully make wells with better long-term production potential.”
DAS technology permits tens-of-thousands of points down the well to be measured simultaneously every two meters. The continuous glass fiber strand inside the cable can sense small acoustic vibrations at a large range of frequencies. These vibrations are most often related to injected fracturing fluid dynamics and fracture propagation, and growth associated with hydraulic fracturing physics. These measurements are valuable to engineers who use the data to sense what is occurring deep in well where they cannot see.
Dana Jurick, General Manager, Neubrex Energy Services
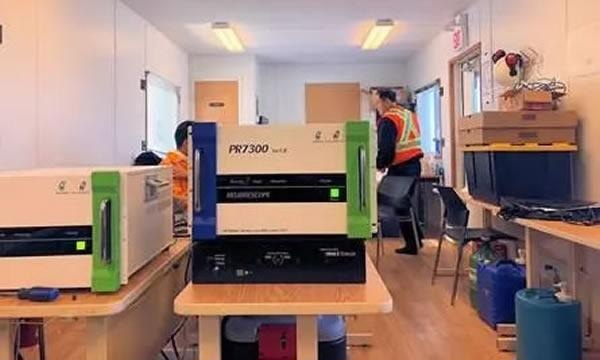
Neubrescope set up on site near well operations. Image Credit: Neubrex Energy Services
Minimizing Background Vibrations
Modern laser and optical receiver components are employed by DAS Interrogator Unit (IU) systems, which are housed inside the IU. In addition, the IU is utilized on site near well operations, where many forms of acoustic and vibratory noise can originate.
Background noise is created in sites that are busy in this way – from trucks, pumps and other equipment – which generate a significant number of low-frequency and variable-frequency vibrations that complicate sounds between the emitted laser pulse and the received light. This type of background noise is superfluous and, therefore not beneficial to the intended measurement objective. In addition, this complication from background noise can diminish the dynamic range and the system’s intended purpose, which is to measure the vibrations produced on the downhole fiber optic strand within the cable, which is attached to the well casing and the subsurface earth.
The latest DAS technology from Neubrex has been paired with an advanced, portable vibration isolation system, in order to maximize the system’s dynamic range.
Negative-Stiffness Vibration Isolation
Minus K Technology is an OEM supplier to makers of scanning probe microscopes, micro-hardness testers and other vibration-sensitive instruments and equipment, such as for testing zero-g simulation of spacecraft. Minus K Technology has developed negative-stiffness vibration isolation, and the company’s isolators are used by over 300 government laboratories and universities in 52 countries today.
The vibration isolators created by Minus K Technology do not require compressed air or electricity and are compact, which allows the instruments to be placed wherever they are needed - whether at a well head or an O&G production facility. The isolators have no chambers, motors or pumps, and therefore no maintenance is required as there is no internal machinery to wear out. The isolators operate purely in a passive mechanical mode.
Negative-stiffness isolators have a significant advantage in that they are able to achieve a high level of isolation in multiple directions, and have the flexibility of custom tailoring resonant frequencies to 0.5 Hz horizontally and vertically (some versions are at 1.5 Hz horizontally). It is important to note that isolation begins at 0.7 Hz and improves with increase in the vibration frequency for an isolation system that has a 0.5 Hz natural frequency. The system performance is more commonly described by the natural frequency.
Dr. David Platus is the inventor of negative-stiffness isolators, and President and Founder of Minus K Technology.
Vertical-motion isolation is provided by a stiff spring that supports a weight load, combined with a negative-stiffness mechanism. Net vertical stiffness is made very low without affecting the static load-supporting capability of the spring. Beam-columns connected in series with the vertical-motion isolator provide horizontal-motion isolation. A beam-column behaves as a spring combined with a negative-stiffness mechanism. The result is a compact passive isolator capable of exceptionally low vertical and horizontal natural frequencies and high internal structural frequencies.
Dr. David Platus, President and Founder, Minus K Technology
A transmissibility curve measures the high performance delivered by negative-stiffness isolators. The measure of the vibrations that are transmitted through the isolator relative to the input vibrations is known as vibration transmissibility. When adjusted to 0.5 Hz, negative-stiffness isolators achieve approximately 93% isolation efficiency at 2 Hz; 99% at 5 Hz; and 99.75% at 10 Hz.
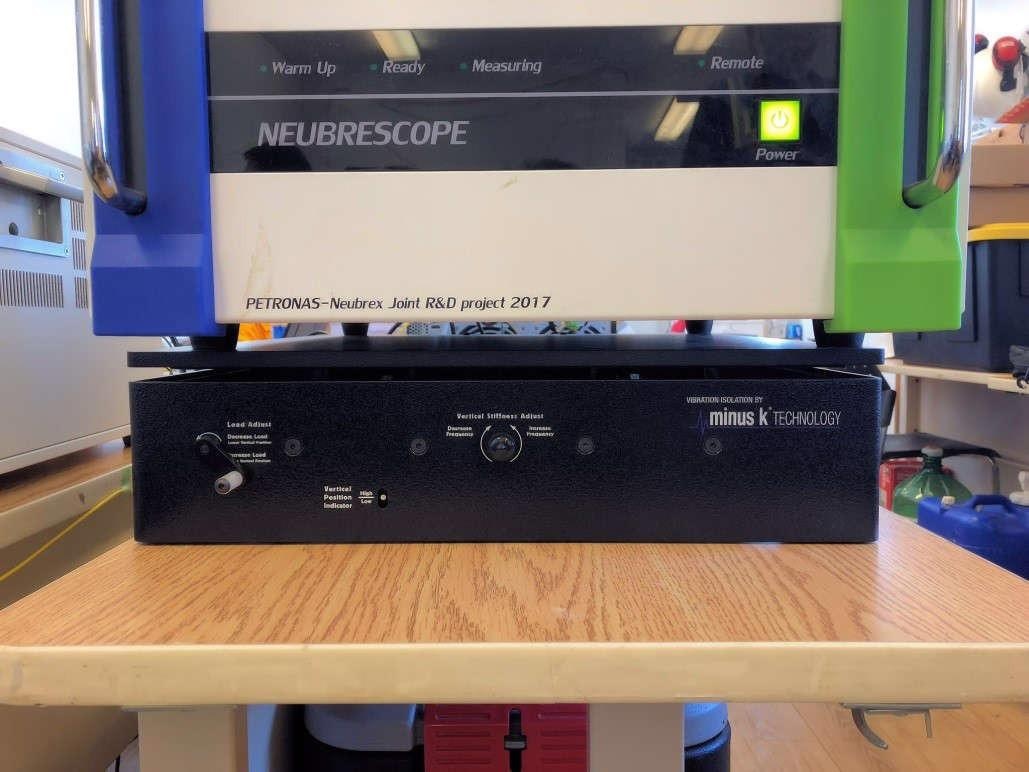
Negative-stiffness BM-8 vibration isolator beneath the Neubrescope. Image Credit: Neubrex Energy Services
DAS System Variations
In order to permit variations in measuring capabilities, the distributed acoustic sensing interrogator unit system is designed to operate over a wide spectrum of laser wavelengths. The measurement of acoustic vibrations is conducted by the system in a distributed spatial sense at meter-order scale, at a fast temporal sampling rate to support Nyquist sampling theorem. (Nyquist sampling theorem states that if the waveform is sampled over twice as fast as its highest frequency component, a bandlimited continuous-time signal can be sampled and perfectly reconstructed from its samples). Negative-stiffness vibration isolation is incorporated to insure the dynamic range along with the signal-to-noise ratio of the system measurements.
While detecting and recording simultaneous and independent measurements of both temperature and strain distribution, DTSS offers additional sensing capabilities to DAS, and performs these sensing capabilities at centimeter-order spatial resolution. This is, as stated, significantly more spatially resolved than DAS can deliver.
Spatial resolution is measured in line pairs per centimeter (lp/cm), and is a measurement to determine how small an object should be in order for it to be detected by an imaging system.
Neubrex Ltd., Kobe, Japan developed distributed temperature and strain sensing systems, and is employed in application by Neubrex Energy Services, which is the U.S. division of Japan-based Neubrex Company. The DTSS product line of the company is called Neubrescope.
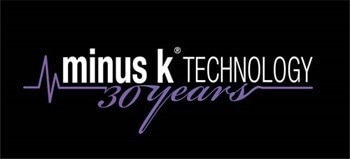
This information has been sourced, reviewed, and adapted from materials provided by Minus K Technology.
For more information on this source, please visit Minus K Technology.