The applications of lasers in space in the past are well known; they play a key role in assisting various missions to the moon, planets and wider reaches of the solar system. The space industry is an ever-expanding one, and now more than ever the idea of low Earth-orbit satellite constellations (LEOs) is one gripping the entire sector.
LEOs are anticipated to supply the further growth of global wideband internet coverage which requires economical, low-cost lasers that meet a set of particular design requirements, as well as being robust enough to survive the vacuum of space. They have been lauded and praised in the news by public figures including Elon Musk, who has overseen the concept for the Starlink project. The technology required for LEO satellites must be state-of-the-art and innovative enough to spark a new era of space laser applications: this means the traditional design rules will have to be torn up and rewritten.
Sheaumann can manufacture, assemble, and package all of its products in house, making it possible to monitor and carefully inspect every laser diode from beginning to end. No stranger to manufacturing space-grade lasers that are proven to stand the test of time, Sheaumann has strong ties with German satellite equipment manufacturer Tesat-Spacecom. The partnership between Sheaumann and Tesat-Spacecom led to the production of cutting-edge laser modules for satellite communication applications.
Sheaumann was seeking a company that was responsive, versatile, and already involved in the global market while demonstrating a proven ability to offer innovative, cost-effective solutions. The outcome of the partnership was the output of space quality lasers that earned the approval of the European Space Agency - lasers that are in fact at work in low-Earth-orbit right now.
The Rigors of Space
Due to the extreme environmental conditions of space, the physical constraints of almost every scientific process, technique, and component are pushed to their outer limit. For a spacecraft to thrive and succeed on its mission, all components - including lasers - must maintain performance as well as survive the testing conditions of outer space. Therefore, the reality is that many of these lasers must go decades without repair. They will also need to resist exposure to extreme cold, heat, shock, and vibration while remaining as compact and powerful as possible.
Tesat-Spacecom places an emphasis on getting things right the first time. When sending lasers into the vacuum of space, there is virtually no margin of error; if something goes wrong, not only will the equipment need to be replaced but potentially the supplies.
Thermal Cycling
One environmental stress challenging manufacturers is thermal cycling, since the various thermal expansion coefficients between the materials within the package can result in a shift in fiber-coupled output power. Over time, these differing expansion rates may cause the laser package to shear itself apart. The ability of the laser to overcome and endure a hostile environment depends on reworking the way a diode laser chip is designed and mounted inside a package. Long-lifetime lasers must, therefore, survive exposure to thousands of temperature cycles; most military-grade laser diodes cannot typically survive more than 500 cycles. Fundamentally, the harsh environment of space offers the optimal test conditions to perfect extreme reliability.
The Metal Stack
Common design features of a laser diode require several layers of solder and various metals between the laser chip and the package. The solder joins the chip to a submount, which is affixed by another solder to a base mount, which in turn is joined to the package by an additional layer of solder (Figure 1). Each of these layers indicates a potential thermal expansion mismatch, and when exposed to extreme cycling tests, the metal matrix of the solder can disintegrate.
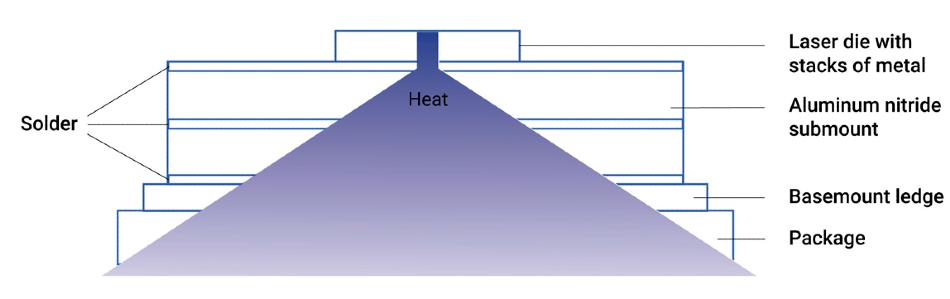
Figure 1. Illustration of a die, submount, and package.
Therefore, the selection of materials should be based on three essential criteria: 1) compatible thermal expansion through the metal stack; 2) high thermal conductivity to remove heat from the die, and 3) material strength to uphold structural integrity under high shock and vibration.
Thermal stress between the layers can, therefore, be minimized with innovative and carefully planned design. In turn, producing a type of laser module with the ability to survive over 2000 temperature cycles and the extreme g-forces and vibration profiles analogous with the launch.
The Laser Chip
When lasers travel through space, repairs or recalibration may not be carried out for over two decades of operation. Thus, a key part of achieving extended lifetime requires optimizing the thermal performance of the die itself. If a chip consistently overheats, it will become stressed and eventually burn out.
Improving the heat dissipation extends the life of the laser. Designing the best metal layers and thicknesses to circumvent high thermal impedances between the layers is vital. This process requires several layers of metal to be deposited on the gallium arsenide (GaAs) chip that thermally couples the die to the solder and joins it to the submount (Figure 2). If layers are not appropriately chosen, heat then reflects back to the chip. Although modeling tools are at hand to assist in this task, decades of experience are necessary to really master this art; so subtle is the methodology that it has not yet been fully rendered or integrated into modeling tools. The chip must effectively operate at very high junction temperatures.
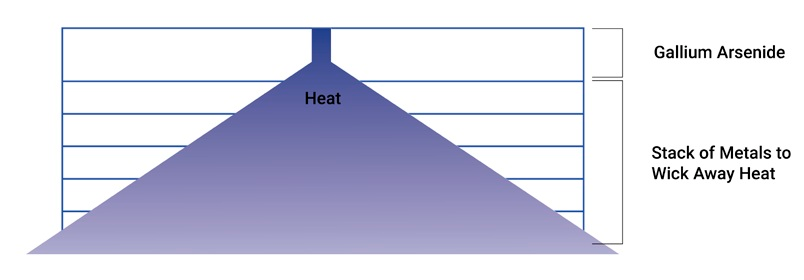
Figure 2. Detail of a laser die.
Performance
The laser module must maintain high optical performance in addition to enduring the environmental extremes of outer space. Thermal expansion repositions the fiber relative to the aperture of the die and limits the light coupled into the fiber. The system must be made less sensitive to this movement to sustain consistent power into the fiber.
One unique approach to reduce sensitivity necessitates a change to the quantum well structure of the die to modify and change how the light is emitted from the aperture. This determines a higher coupling into the acceptance angle of the fiber. An in-house packaging and laser die design system can facilitate the creation and fabrication of novel die structures. By modifying the physical properties of the beam emitted from the die, it is possible to sustain consistent power into the fiber across the requisite temperature range.
We have succesfully demonstrated reliability with longer chip lengths, which allows us to achieve significantly higher power levels across all of our wavelengths for single-mode. Our ability to custom design specific wavelengths and produce these new high-power diodes is very unique in the industry, and we look forward to further expansion of our wavelength capabilities in the near future.
Gary Sousa, President and CTO - Sheaumann Laser, Inc.
Hermeticity
Other than thermal management, package hermeticity also presents designers with a challenge. High levels of hermeticity are intrinsic to a laser’s lifetime. Telcordia specs are two orders of magnitude below what is required for a laser to last for at least 25 years in space. One way to ensure these levels are maintained involves an innovative process that seals the snout of the package together.
Advanced procedures are used to test the package for fine and gross leaks at these levels. Because cutting-edge technology is required for a laser module to thrive in space, conventional design rules will need to be broken and the designs remade from scratch. Possessing the ability to modify laser diode design and fabrication, along with the ability to process and package in-house, are vital components to a company’s success.
Acknowledgments
Produced by Sheaumann Marketing from materials originally authored by Adam Erlich, Director of Business Development.
Sources and Further Reading

This information has been sourced, reviewed and adapted from materials provided by Sheaumann Laser, Inc.
For more information on this source, please visit Sheaumann Laser, Inc.