Teaming up with Tesat-Spacecom in 2015, Sheaumann developed a space-qualified laser module, which is now deployed in LEO and GEO satellites. This three year intensive project demanded an update that improved upon Sheaumann’s flagship 2-Pin ‘SheauPac’ module.
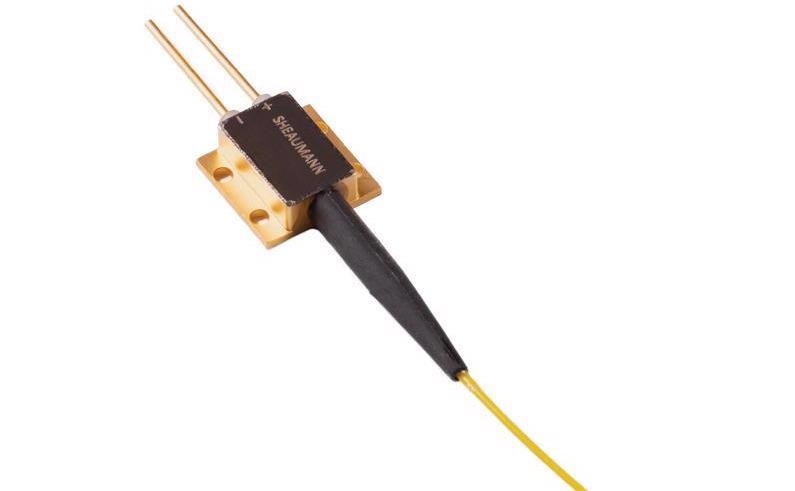
Image Credit: Sheaumann Laser, Inc.
The challenge was creating a module that could continuously operate in the hostile environment of space for over 20 years without recalibration or repair.
Customizing the module was a task necessary to overcome certain obstacles where a stock product would have performed way below the operating standards required.
Sheaumann Laser is proud to be an OEM supplier of laser modules to Tesat for its satellite communications applications. Such business relationships are founded on product quality/performance, support, transparency, and mutual respect.
Jim Hsieh, CEO, Sheaumann Laser, Inc.
Challenges and Solutions
Extreme Temperatures
When orbiting the Earth, the satellite experiences extreme temperatures and conditions that surpass those experienced on the Earth’s surface, especially when the module transitions from sunlight to darkness and vice versa. This can lead to shifts in the positioning of the chip and fiber, resulting in power reduction and the potential for system failure.
The solution involves revising the processes for fixing the laser diode and fiber to the unit, enabling it to withstand 100,000 cycles from -55°C to +85°C.
Noise in the Signal
When the laser is transmitting optical data back to Earth, the quality of each and every photon is vital for the accuracy of signal transmission. ‘Noisy’ output can be caused by laser light in the fiber cladding, which is unacceptable.
By designing a proprietary fiber preparation and alignment solution, the cladded light was significantly reduced, improving the beam quality. What’s more, a redesign of the epitaxial structure of the diode and the addition of an extra processing step for the facet enhanced the output.
Gamma Radiation
When exposed to radiation in space, standard fiber will typically degrade over time. This requires the acquisition of a custom batch of fiber that is radiation-tolerant while modifying other processes to guarantee compatibility.
Launch G-Forces
During the launch of a satellite, conditions can create high mechanical stresses, such as extreme shock and vibration; this can damage the laser. Employing a proprietary component dampening technology previously developed for a military application helps mitigate and offer a solution.
Tin Whiskers
System failures in space-based applications have been caused by tin forming in an arrangement known as ‘whiskers’ – the presence of tin is due to its frequent use in solder.
Reformulating the solder by reducing the tin content offers a solution while making sure the appropriate thermal conductivity and matching are sustained.
Offgassing
Conventional adhesives, including epoxy, will offgas over time, which can result in failure of the laser if deposited on the facet. By acquiring a space-grade epoxy with extra component to insert into the module enables the absorption of destructive emissions.
Minimal Payload
Due to certain restrictions on the space and power of a satellite, minimal power consumption, size and weight of the laser module is necessary. The compact size of the 2-Pin ‘SheauPac’ package made it the perfect solution for this project.
Redundancy
It is necessary that redundant laser modules are employed to make sure operation is continuous in case of failure, but they must be switched on automatically without the need for extra circuitry or complexity.
In the event of a module failure, a simple passive component allows constant operation of the system.

This information has been sourced, reviewed and adapted from materials provided by Sheaumann Laser, Inc.
For more information on this source, please visit Sheaumann Laser, Inc.