Master Bond offers a diverse array of adhesives suitable for a wide range of applications and industries. This article outlines some of the company’s most popular products, their characteristics and a number of usage examples.
Needle Bonding Adhesives
Certain grades of single component, no-mix epoxy and UV curable adhesive systems, may be used for needle bonding applications. These systems offer rapid cure speeds in bonding cannulae to hubs in syringe needle assembly applications.
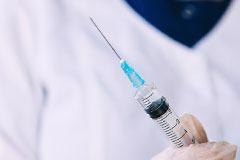
Image Credit: Master Bond Inc.
Needle bonding adhesives are available in a range of viscosities and are ideal for high volume production operations. They also meet USP Class VI certification requirements while resisting exposure to steam autoclaving, ETO and gamma radiation sterilization.
These formulations are able to prevent fluid leakage, making them an ideal solution for applications involving blood or medicines. They can also be used to secure a fixed positioning of the cannula.
Each chemistry offers a range of notable benefits, including:
Dual Curing Systems - UV + Heat
- Single part with no mix formulations
- Rapid curing
- Solvent-free
- Wide range of hardness and viscosity options
- Transparency
- Straightforward automation
One Part Heat Cure Epoxies
- No mix formulations
- High strength bonds
- Excellent toughness
- Strong depth of cure
- Easy application
- Solvent-free
Dual curing (UV + Heat) systems and one-part epoxies exhibit superb adhesion to metals, glass and plastics. The use of appropriate surface preparation can also ensure excellent adhesion to commonly used plastic hub materials, including:
- Acrylic
- Polystyrene
- Polycarbonate
- Polyethylene
- ABS
Needle bonding adhesives offer high thermal stability, and fluorescent compounds can be inspected using a low intensity blacklight.
UV22DC80-1Med - Nanosilica-Filled, Dual Cure Epoxy-Based System
UV22DC80-1Med has been specifically formulated to enable rapid curing upon exposure to UV light while offering the important ability to crosslink in shaded areas upon the addition of heat. Its key features include:
- Minimal shrinkage upon curing
- Low viscosity
- Excellent optical clarity
- In shadowed out areas, cures at 80 °C
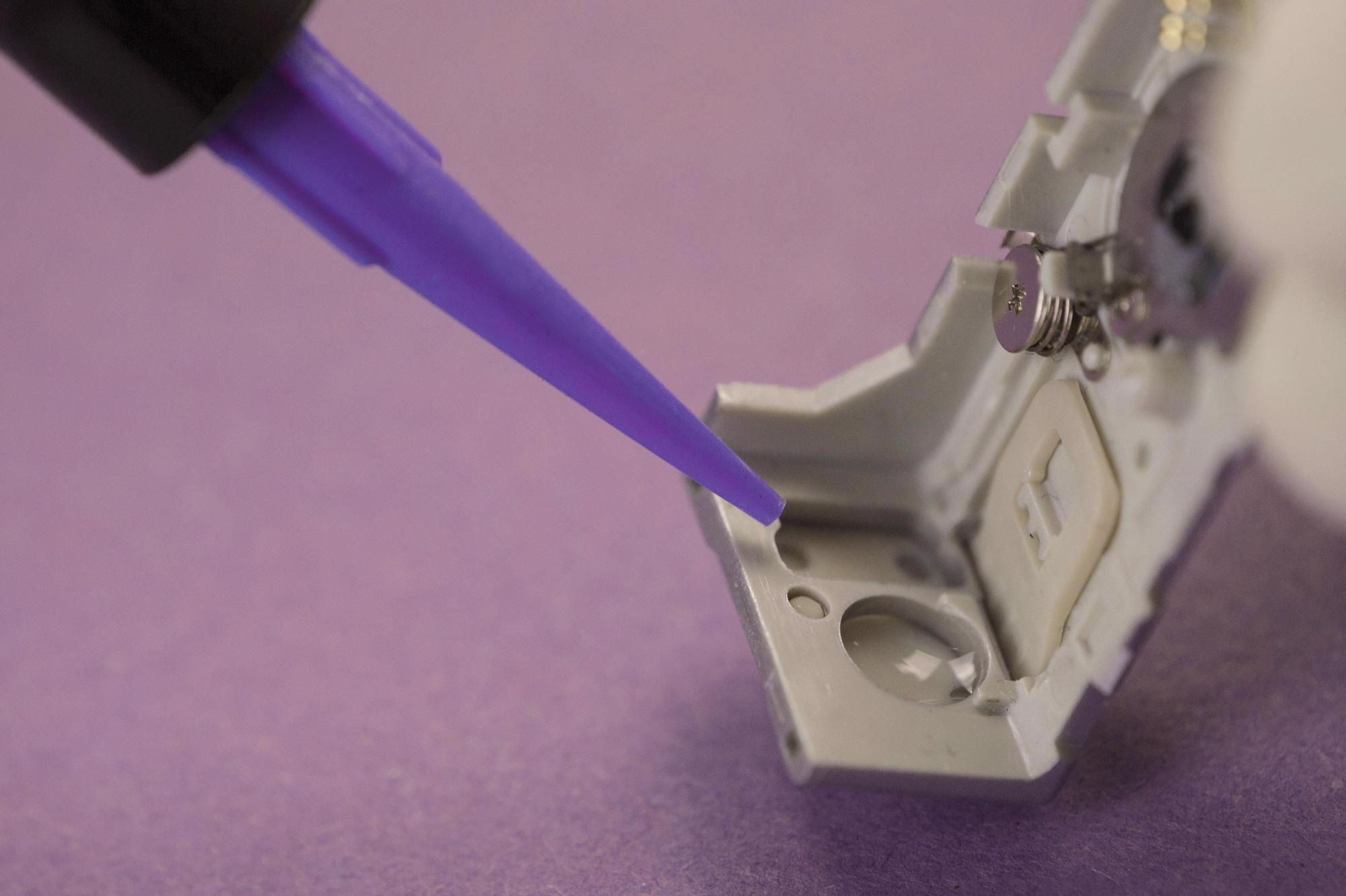
Image Credit: Master Bond Inc.
This novel approach is based on the recognition that UV curables will crosslink quickly and thoroughly upon exposure to light, but these will not cure in areas not exposed to light. The introduction of a dual cure mechanism allows those areas not exposed to light to be cured via the addition of heat.
The cure’s thermal part takes place at 80 °C – a user-friendly, achievable temperature ideal for working with plastics. Dual cure systems are an ideal option for the rapid fixturing of parts using the UV portion of the cure before finishing via heating.
This system exhibits lower viscosity while its UV portion features a cationic cure mechanism. As a nano-filled system, the UV22DC80-1Med boasts an extremely low shrinkage and outstanding dimensional stability.
It is not inhibited by oxygen and offers a number of advantageous properties following polymerization, bonding well to a diverse array of substrates, such as metals, glass, ceramics and the majority of plastics.
UV22DC80-1Med also offers very good chemical resistance and is able to withstand many acids, bases, solvents and fuels.
UV22DC80-1Med is a robust electrical insulator, able to endure demanding thermal cycling - its service temperature range is -60 °F to +350 °F.
Straight UV curing can be achieved for thicknesses of 0.01 to 0.02 inches in just seconds when utilizing UV light at 365 nm with 20 to 40 milliwatts/cm2 of energy. Higher energy outputs can be employed to achieve faster cures.
Any shaded areas not cured via UV can be cured via the application of 80 °C for 40 to 60 minutes. The application of post curing at 125 °C to 150 °C for 15 to 30 minutes can increase the glass transition temperature (Tg) from 90 °C (achieved by straight UV curing) to more than 125 °C.
This product is afforded a range of special properties via this robust combination of an 80 °C secondary cure and nano filler. Being able to initiate curing via UV light source and finalize this via the application of heat has made the UV22DC80-1Med a popular choice in a range of high-tech applications, including medical devices.
UV22DC80-1Med offers a range of distinct benefits, including:
- Single component system
- No mixing needed
- Dual cure - UV + heat (80 °C)
- Zero oxygen inhibition
- Robust physical strength properties
- Nano filled, abrasion-resistant, high dimensional stability
- Meets ISO 10993-5 and USP Class VI specifications
EP30Med - Two Component, Optically Clear, Low Viscosity Epoxy Resin
Master Bond’s EP30Med is an ideal choice of resin system for high-performance bonding, coating, sealing and encapsulating. It has been specifically formulated to readily cure at room temperature, though elevated temperatures will allow this to cure more quickly. Its key features include:
- Passes ISO 10993-5 for cytotoxicity
- Biocompatible as per USP Class VI testing
- Optically clear
- Endures 1,000 hours 85 °C/85% RH
- Meets certification for indirect contact with food
- Resistant to chemical sterilants
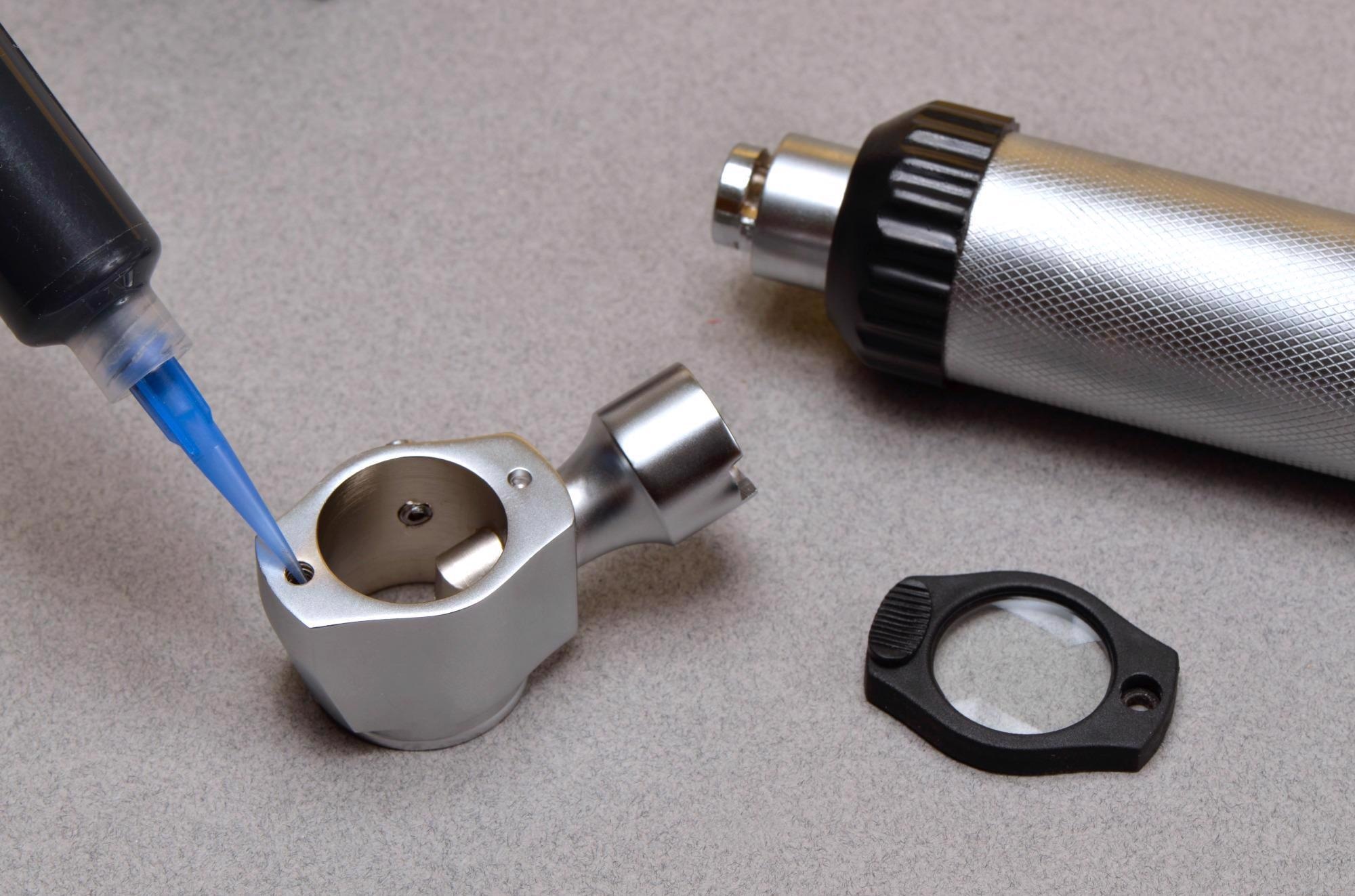
Image Credit: Master Bond Inc.
EP30Med has a 4:1 mix ratio by weight and does not contain any diluents or solvents. It produces rigid, high strength bonds which are highly resistant to water, oils, a number of organic solvents, cold sterilants, gamma radiation and ETO.
EP30Med is serviceable across a wide temperature range of -60 °F to +250 °F. It is suitable for bonding to an array of substrates, including glass, ceramics, metals, wood and a number of plastics.
EP30Med offers extremely low linear shrinkage upon cure, and once cured, this compound is an outstanding electrical insulator, making this system well suited to potted and encapsulating applications.
It also meets USP Class VI specifications – an essential requirement for use in medical devices – while meeting the FDA CFR 175.105 requirements for indirect food contact.
Adopting a cure schedule of overnight curing at room temperature, followed by 1 to 2 hours at 150 °F to 200 °F, will ensure optimal properties and biocompatibility.
EP30Med offers a range of distinct benefits, including:
- Convenient application - low viscosity means that only contact pressure is required for curing
- Easy mixing – 4:1 by weight
- Versatile cure schedules: room temperature curing or quicker elevated at curing temperatures
- High strength, rigid bonds form to a wide range of substrates
- Extremely low shrinkage
EP62-1LPSPMed White - Two Part, Very Low Viscosity Epoxy
Master Bond EP62-1LPSPMed White confidently passes ISO 10993-5 certifications while offering a forgiving mix ratio of 100:25 by weight. Its key features include:
- Passes ISO 10993-5 requirements
- Convenient handling
- Able to resist repeated sterilization
- Pigmented white
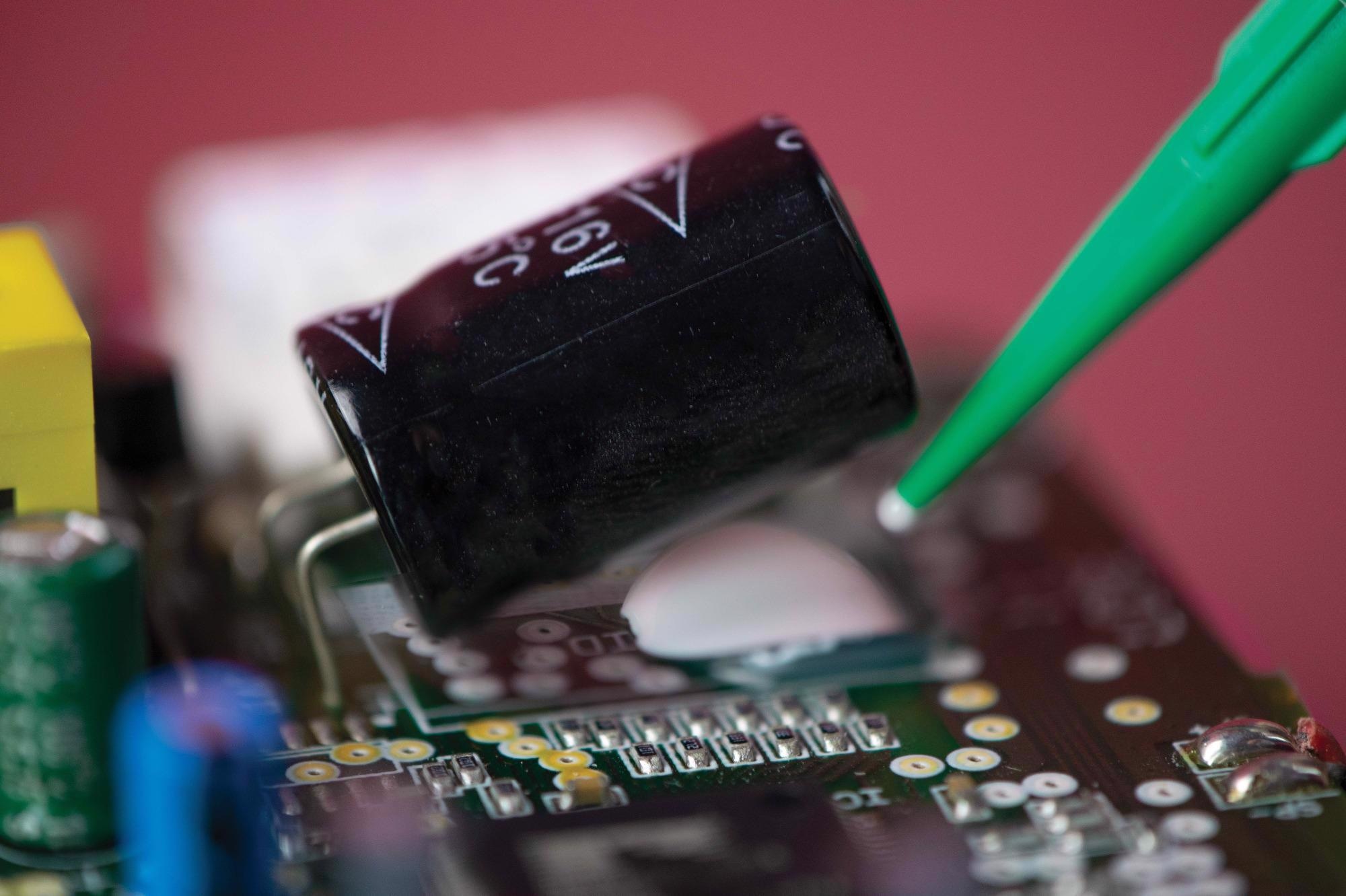
Image Credit: Master Bond Inc.
Its viscosity is low upon mixing, while its working life is 12 to 24 hours at room temperature. The most advisable cure schedule involves overnight curing at room temperature, followed by either 8 to 10 hours curing at 60 °C to 70 °C, 60 to 90 minutes at 80 °C to 100 °C or 30 to 60 minutes at 125 °C.
Using one of the aforementioned schedules followed by a post cure of 2 to 4 hours at 110 °C to 135 °C will ensure optimum properties. This epoxy features no diluents or solvents and offers low shrinkage upon curing.
The system is able to bond well to a wide range of substrates, including composites, glass, metals, rubber and many plastics.
EP62-1LPSPMed White is a robust electrical insulator while offering an array of attractive physical properties superior resistance to radiation, ETO, chemical sterilization and autoclaving.
The system can be used for both disposable and reusable medical devices, while its low viscosity makes it a viable option for small encapsulating and potting applications.
Its toughness allows the system to withstand thermal cycling, mechanical shock and vibration, while its temperature range extends from 4 K to +400 °F.
This compound is an excellent solution for medical devices which specifically require a white-colored, low viscosity, sterilization-resistant epoxy.
EP62-1LPSPMed White offers a range of distinct benefits, including:
- Forgiving 100:25 mix ratio by weight
- Ultra-low viscosity
- Extended working life
- Able to withstand autoclaving and chemical sterilants
- Wide temperature range
EP42HT-2Med - Two Component Epoxy
Master Bond’s Polymer System EP42HT-2Med features convenient handling and resistance to a range of repeated sterilization cycles. Its key features include:
- Convenient processing
- Passes ISO 10993-5 for cytotoxicity
- Withstands repeated sterilization, including autoclaving
- USP Class VI approved
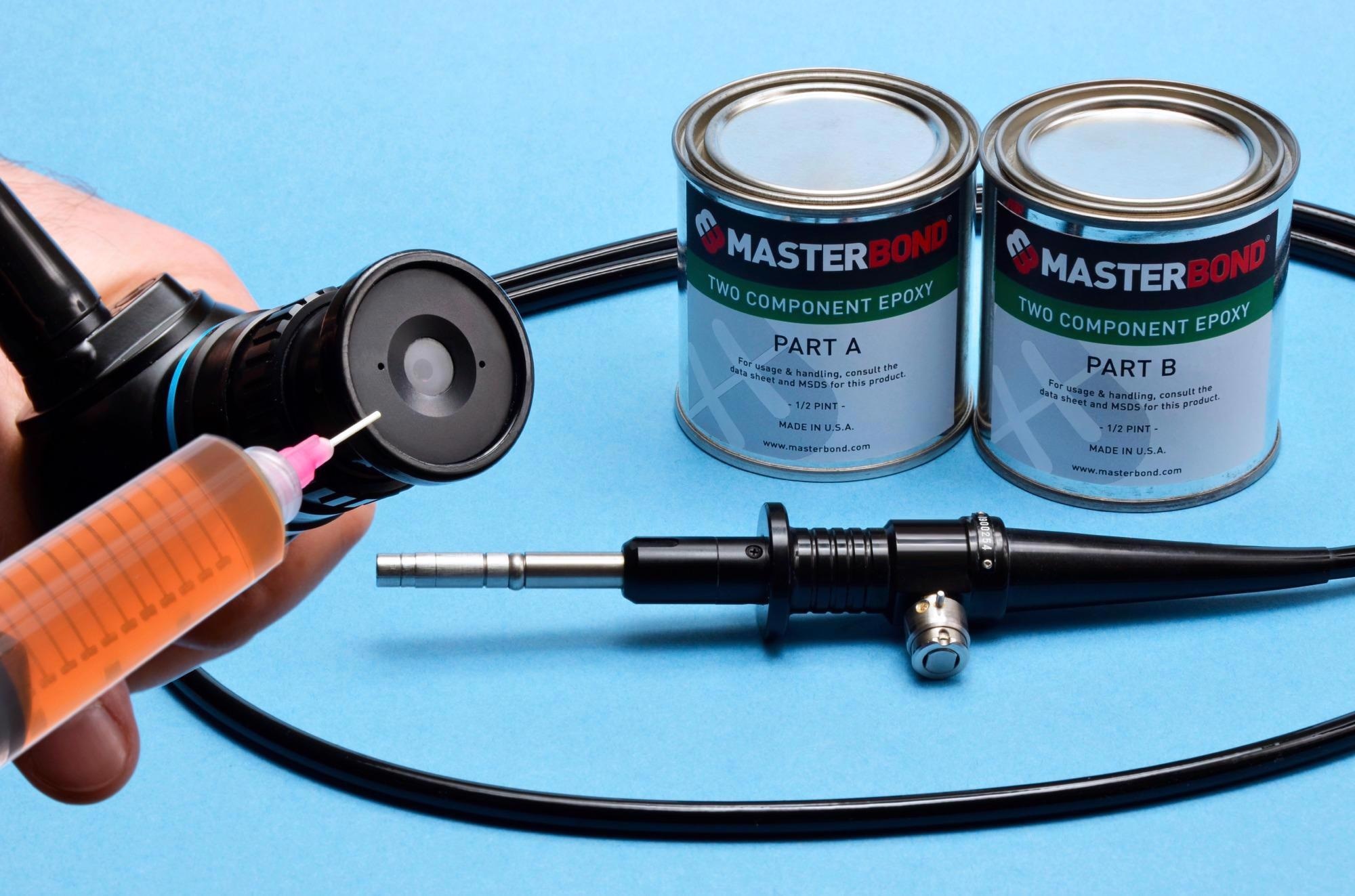
Image Credit: Master Bond Inc.
EP42HT-2Med’s 100:40 mix ratio by weight or 100:50 by volume ensures ease-of-use, while its good flow properties and moderate viscosity help ensure a long working life. This system contains no solvents and exhibits very low shrinkage upon curing.
The system has been designed to cure readily at ambient temperatures, but the addition of heat can speed this up. Cure schedule options are outlined in the chart below, but it is advisable to cure this overnight at room temperature, followed by 2 to 4 hours at 150 °F to 250 °F.
EP42HT-2Med offers excellent adhesive properties, bonding well to a diverse array of substrates, such as metals, glass, composites, ceramics, plastics and rubbers.
It boasts high resistance to acids, bases, solvents and a number of sterilants while offering excellent electrical and thermal insulation. Its lower exothermic properties make the system ideal for encapsulation applications up to 3 inches deep.
EP42HT-2Med offers a higher Tg and a service temperature range of -60 °F to 450 °F.
The color of Part A is clear while Part B is amber clear, allowing EP42HT-2Med to transmit light, making it the system of choice for medical device manufacturing. It is particularly useful for devices that receive repeated sterilization, such as endoscopes and surgical instruments.
EP42HT-2Med offers a range of distinct benefits, including:
- Multi-functional – suitable for bonding, sealing, potting or coating
- Convenient handling
- Good flow after mixing
- Highly resistant to ETO, radiation and chemicals
- Able to withstand repeated steam autoclaving
- Adheres to USP Class VI and ISO 10993-5 requirements
MB297Med - Single Component Ethyl Cyanoacrylate Type Adhesive
Master Bond MB297Med’s is a high strength, rapid curing, higher viscosity (2200-2400 cps) cyanoacrylate system primarily employed in the assembly of medical devices. Its key features include:
- Rapid fixture time
- Fast setting
- Meets USP Class VI specifications
- One component, no mix system
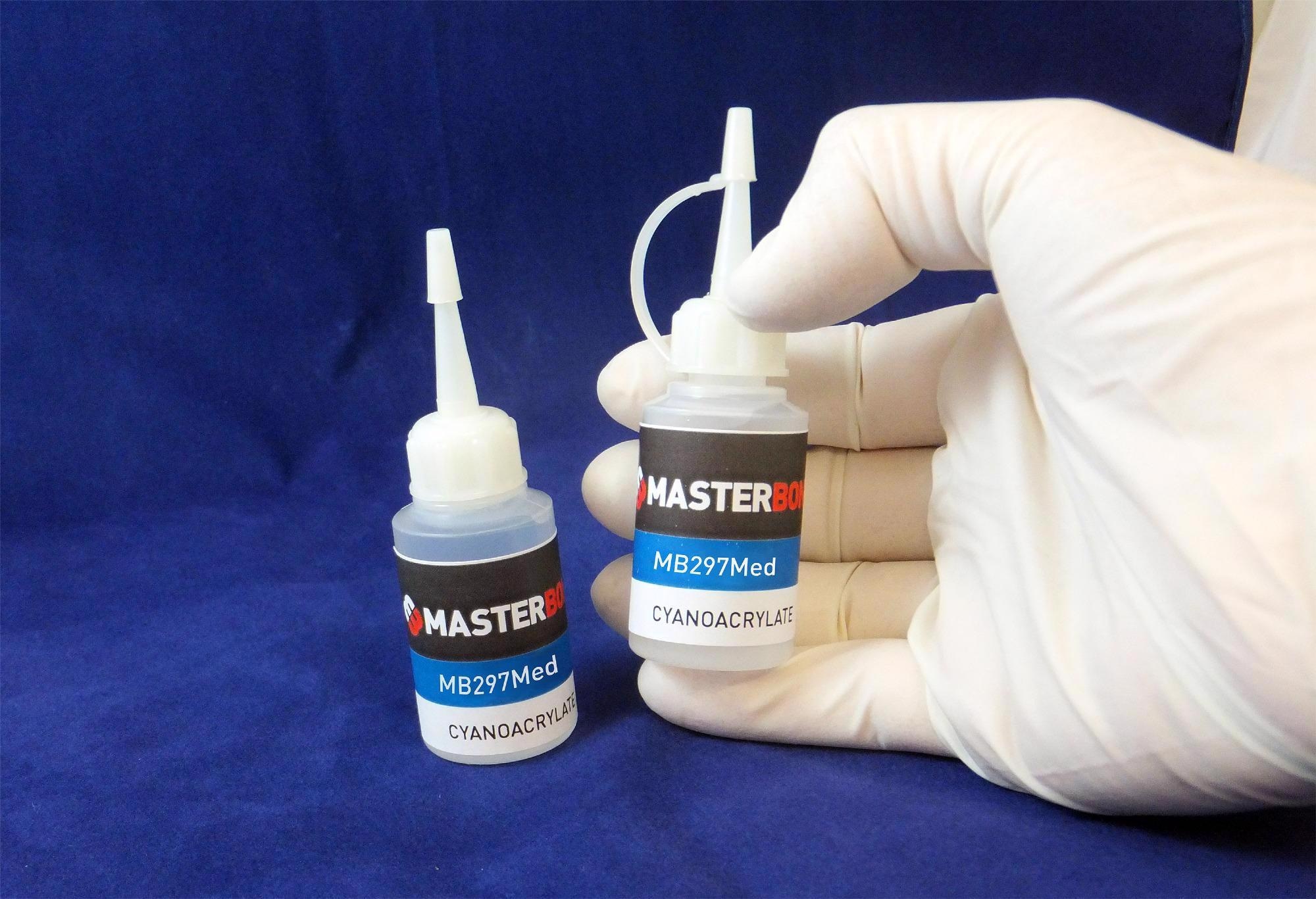
Image Credit: Master Bond Inc.
This type of system is typically referred to as superglue or an instant adhesive due to its capacity to cure very rapidly. The rate of cure is largely dependent upon the humidity, with higher humidity resulting in faster cures – 20 to 50 seconds for specific substrates and humidity levels.
Curing is normally extremely fast, meaning that only minimal contact pressure is required for bonding. It must be highlighted that this high-strength system does not require heating or mixing.
As the bond strength is extremely high in shear mode, MB297Med is able to bond well to a range of substrates – particularly metals, plastics and rubbers. This system’s service temperature range is -60 °F to +250 °F.
It should also be noted that MB297Med confidently meets USP Class VI specifications for biocompatibility, making it suitable for use in a number of medical applications, ranging from high-speed production to repair.
MB297Med offers excellent resistance to ETO and gamma sterilization processes. While many of its common applications involve disposable medical devices, it can also be employed in reusable devices under specific service conditions.
MB297Med offers a range of distinct benefits, including:
- No heating or mixing requirements
- Rapid curing at room temperature – typically within 1 minute
- Can typically be fixtured using contact pressure
- Bonds well to a wide range of substrates
- Excellent resistance to gamma sterilization and ETO
- Meets USP Class VI testing requirements
- Suitable for use with disposable and reusable medical devices
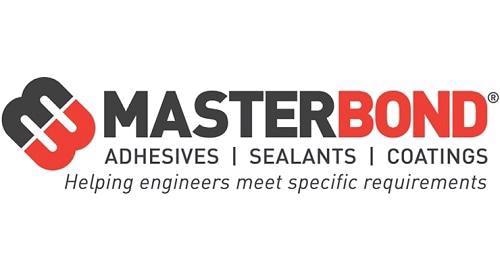
This information has been sourced, reviewed and adapted from materials provided by Master Bond Inc.
For more information on this source, please visit Master Bond Inc.