By virtue of its ability to efficiently store energy and then deliver it on demand, the lithium-ion battery has become the rechargeable battery of choice for the widest range of applications from mobile phones to electric vehicles (EVs). Lithium ions move from the negative electrode of the battery through a suitable electrolyte to the positive electrode to provide energy, and the reverse occurs during recharging.
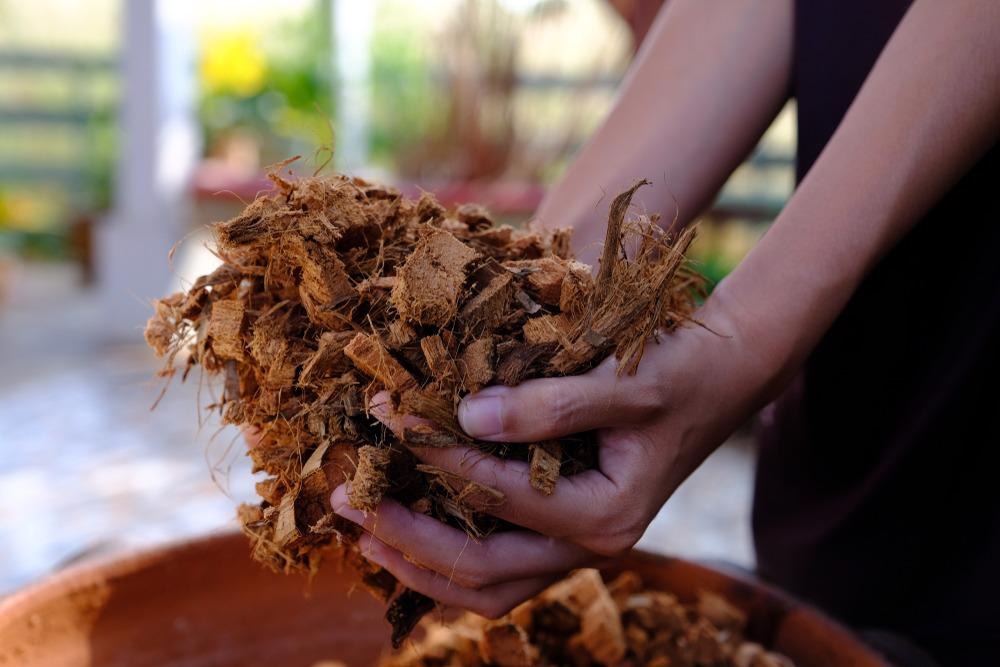
Image Credit: EVANATTOZA/Shutterstock.com
However, this high-performance energy storage solution carries the risk of fire and chemical hazard as the organic-carbonate-based solvents used to dissolve electrolytes, commonly lithium hexafluorophosphate (LiPF6), are highly volatile and flammable. In addition, LiPF6 is thermally unstable and its decomposition in an organic-solvent based electrolyte produces hydrogen fluoride that is toxic and corrosive.
There is potential for the hydrogen fluoride produced to react with the positive electrode to release transition metals and corrode the current collectors. Such reactions not only reduce battery performance but also carry the risk of water and soil pollution with the potential for harming and human health. Consequently, there is an ongoing desire to replace the large fluorine and flammable organic solvent content of lithium-ion batteries to improve the safety and performance of next-generation batteries.
This need has been highlighted with the recent adoption of lithium-ion battery technology to fuel electric cars, which are due to replace vehicles propelled by fossil fuels as part of the effort to reduce the transportation sector's carbon footprint. The surge in the production of lithium batteries and the vast increase in battery size needed to power electric vehicles has created an unprecedented increase in demand for the component chemicals. Since the increase in demand stems largely from strategies to protect the environment, it is desirable for the components to be sourced in a sustainable manner.
Recent research has reported the potential for obtaining electrolytes suitable for lithium-ion batteries from biomass and agricultural waste to reduce the depletion of natural resources. The electrolyte 2-furoic acid was produced from lignocellulosic biomass and used to form an ionic liquid suitable for use as the electrolyte in a lithium-ion battery. Ionic liquids are molten salts at room temperature that have high thermal stability and good ionic conductivity. Furthermore, they are not flammable, offering a safer substitute for the volatile organic-solvent-based electrolytes currently used in lithium-ion batteries.
The structure of the lithium salt and electrolytes produced were characterized by nuclear magnetic resonance (NMR) spectroscopic analysis using a Bruker Avance 400MHz spectrometer. NMR diffusion and relaxation measurements were obtained through pulsed gradient spin echo-NMR using a Bruker Avance III spectrometer. The attenuated total reflection Fourier transform infrared (ATR-FTIR) spectra of samples were recorded using a Bruker IFS 80v spectrometer equipped with a deuterated triglycine sulfate (DTGS) detector and diamond ATR accessory.
The data obtained confirmed that fluorine-free electrolyte manufactured in part from a sustainable source was thermally and electrochemically stable and provided effective battery function. This novel electrolyte production thus holds promise for helping to meet global emission targets and protect the environment through alternative cost-effective battery composition. This latest development will help address the challenges associated with the safety, recyclability, accessibility, affordability and service life of lithium-ion batteries.
Bruker’s unparalled technology portfolio is used at various positions within the Li-Ion Battery supply and value chains. This includes NMR and FTIR spectrometers for novel electrolyte fomulations as described here. But it also spans from investigating the phenomenon of metallic Li deposition at anode materials which is called Li-plating. The key technology used there is Electron Paramagnetic Resonance or EPR2. Solid-State Magic Angle Spinning (MAS) NMR spectroscopy is used to understand ion-mobility during the charging and dis-charging processes of batteries. Finally, sensitivity enhanced cryogenically cooled CP-MAS probes can be used to identify and quantify valuable trace elements in the black mass produced during battery recycling processes. Novel recycling processes assisted by means of magnetic resonance analysis will be vital in applying circular economy concepts to the battery industry.
References
- Khan IA, Gnezdilov OL, Filippov A, et al. Ion Transport and Electrochemical Properties of Fluorine-Free Lithium-Ion Battery Electrolytes Derived from Biomass. ACS Sustainable Chem. Eng. 2021. https://doi.org/10.1021/acssuschemeng.1c00939
- https://www.bruker.com/en/resources/library/application-notes-mr/using-epr-for-analysis-of-metallic-lithium-microstructure.html
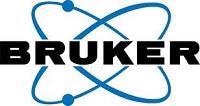
This information has been sourced, reviewed and adapted from materials provided by Bruker BioSpin - NMR, EPR and Imaging.
For more information on this source, please visit Bruker BioSpin - NMR, EPR and Imaging.