Without a continual supply of semiconductor materials, a great number of technology sectors would experience manufacturing delays, supply shortages, or—in the extreme case—an abrupt termination of product. In this piece, it is examined why there is currently a shortage of chips, which companies this is having an impact upon, and what the circular economy might be able to lend to address the issue.
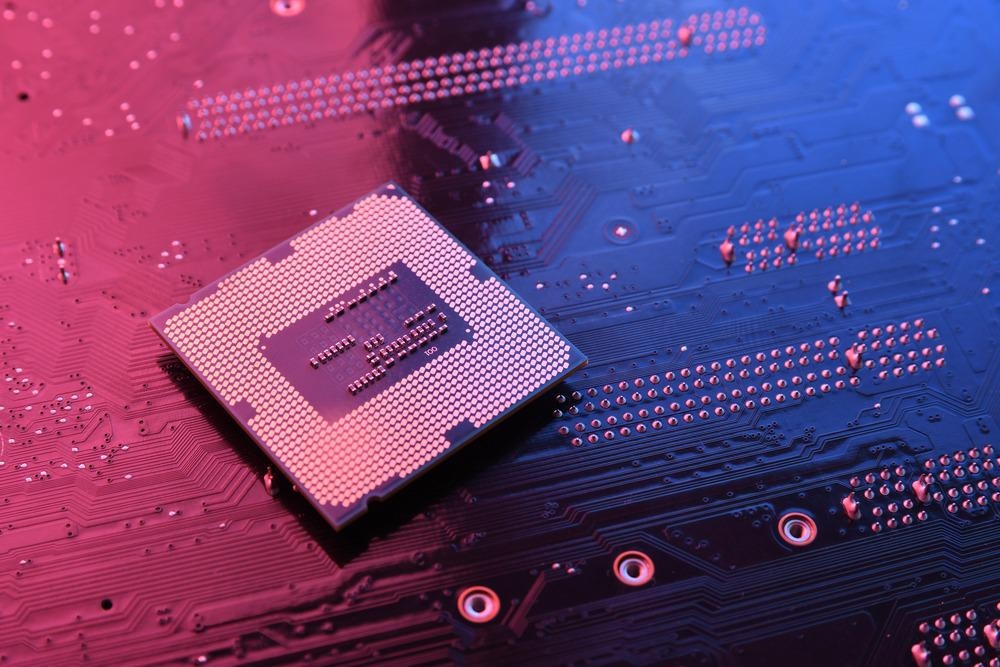
Image Credit: Zoomik/Shutterstock.com
Self-Isolation Meant Device Demand but Lack of Car Demand
Millions of products are reliant on computer chips, composed of semiconductors, for their complete functionality. Everything from digital products and white goods to smartphones and video games needs processing power. In the case of cars, advanced electronics are incorporated into state-of-the-art parking cameras and engine management systems.
Currently, there exists a massive chip shortage.
The dozens of microprocessors needed for each new car are leaving manufacturers with a sourcing problem as they vie with the consumer electronics markets to secure the supplies available, driving high industry demand in the process.
It is anticipated that the present situation, which has been escalating for a number of years, will continue deep into the new calendar year, as chip production resuming at total capacity will inevitably take time. A number of factors have contributed to the current semiconductor shortage.
The impact of the pandemic cannot be fully appreciated or quantified.
A sharp rise in device sales had been observed as people became confined, while a lack in the need for cars has forced car manufacturers to reduce orders. This in turn forced chipmakers to reorganize production.
Even before coronavirus, geo-political implications encumbered the chip industry; for example, the uncertainty created by the mounting tension between the US and China in their trade relations.
Indigenous US know-how became stymied for fear of supply to the Chinese military. Huawei, for example, responded to this by stockpiling before trade restrictions were implemented.
With their domination of chip manufacturing, Taiwan and South Korea are somewhat monopoly producers, accounting globally for 83% of processor chip production. Serving the biggest players, namely Apple and Samsung, as priority customers with enormous buying power means fewer products for others.
Also adding to demand is the rollout of 5G infrastructure. All in all, backlogs within the semiconductor industry may mean it will take two years to address the current situation.
Impact of the Shortage
As the car industry implements just-in-time delivery to obviate stockpiling parts, it has found itself at the mercy of the semiconductor material and chip supply.
It emerged that this industry was suffering prior to Christmas 2020.
With the current shortage, vehicle production has consequently either slowed or been suspended by a growing list of manufacturers, including Daimler, Toyota, Ford, and Volvo among others. Jaguar Land Rover has shut factories temporarily as a result of the shortage.
As perhaps the world’s biggest computer-chip manufacturer, Samsung cannot satisfy its customer orders while similar challenges are being felt by Qualcomm, the company responsible for the modems and processors integral to powering so many of the leading consumer gadgets on the market.
Circular Economy: Shifting from Disposal to Recycle
Many organizations believe implementing effective initiatives in a semiconductor circular economy is imperative to address the serious imbalance being experienced at present and to mitigate future global shortages.
However, there is a question as to whether this can be realized. Shifting from disposal to recycling resources is key.
Remanufacturing used system parts, qualified to the same standard as new parts, is a core initiative in the circular economy landscape preventing unnecessary waste.
Minimizing the use of new resources as much as possible, while maximizing value from materials, are also priorities when repurposing products across their life cycles. Extending their product lifetime as much as possible is a strong driver.
These strategies are cross-cutting and would appeal to a diverse range of companies.
With endeavors to create a greener society also part of their agenda, corporations are investing in recycling and reusing strategies where materials and products find a new lease of life.
In terms of materials, it has been estimated that 1 million smartphones contain the equivalent of 15 kg palladium, 34 kg gold, 350 kg silver, and 16,000 kg copper, while under normal circumstances ca. 3%–4% of the daily 250,000 silicon wafers placed into manufacturing are scrapped.
More extensive reclamation of these elements could be attractive if the cost, release of toxic pollutants, and gathering of waste from doing so could all be reduced. Gallium arsenide and expensive rare earth element (REE) materials extensively used in semiconductor production require an escalation in their recovery from processing.
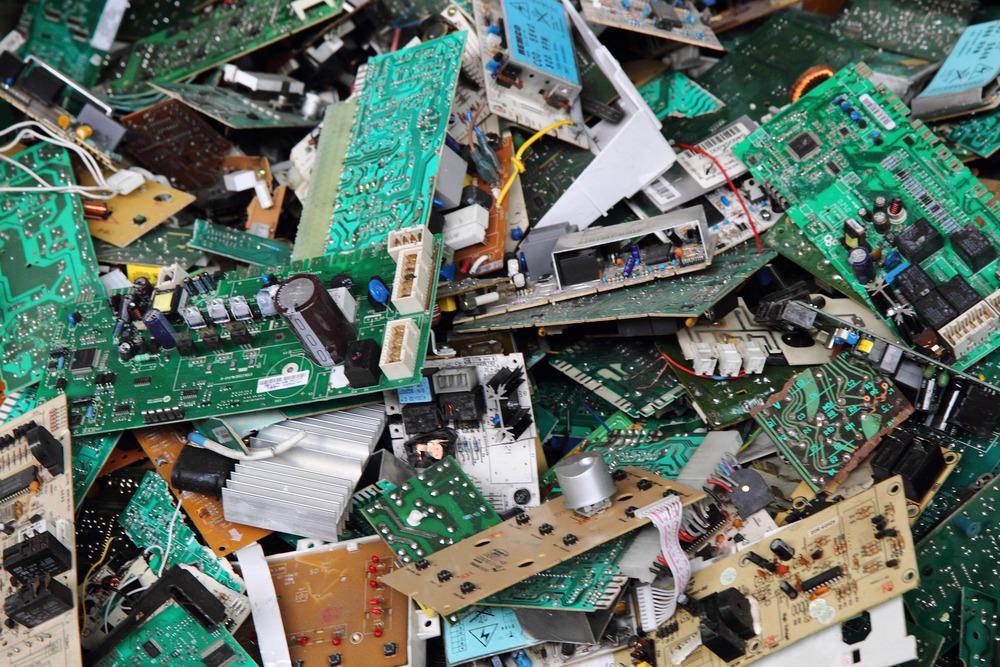
Image Credit: Jirik V/Shutterstock.com
In terms of product recycling, companies such as ASML and Nikon are generating best practices at embedding circular economy approaches with reach and depth that will foster future success and competitiveness of the semiconductor industry.
For example, ASML’s Return4Reuse program seeks to reuse old equipment by producing less sophisticated chips, while ensuring progressively sustainable use of materials across processes and the value chain via refurbished products.
They state that, in 2020, they reused nearly 4 million kg of materials, preventing these from ending up as waste.
Long-Term Environmental Vision Required
Nikon, which also manufactures critical semiconductor lithography systems, engages proactively in the 3Rs of reducing, recycling, and reusing.
Fundamental to its approach to realize a model for a resource-circulating society in its long-term environmental vision is repurchasing and undertaking part and component restoration.
This is an effective means of reducing waste. Energy-saving initiatives such as on-site projection lens replacement, for example, have also been adopted while updating the software rather than the hardware results in the lithography system longevity at the customer's facilities.
To open up the possibility of a sustainable future, the potential of material shortages needs greater exploration, while success will likely be driven by a circular economy agenda within the semiconductor materials industry.
References and Further Reading
Nikon (2021). Reusing semiconductor lithography systems to reduce waste [Online]. Available at: https://www.nikon.com/about/sustainability/highlight/1902_reuse/ (Accessed on 17 September 2021)
ASML (2021). Circular economy Minimizing waste, maximizing resource [Online]. Available at: https://www.asml.com/en/company/sustainability/circular-economy (Accessed on 17 September 2021)
Chizaryfard A. et. al. (2021). The transformation to a circular economy: framing an evolutionary view. Journal of Evolutionary Economics 31 475 https://doi.org/10.1007/s00191-020-00709-0
Disclaimer: The views expressed here are those of the author expressed in their private capacity and do not necessarily represent the views of AZoM.com Limited T/A AZoNetwork the owner and operator of this website. This disclaimer forms part of the Terms and conditions of use of this website.