Silicon carbide is a semiconductor that consists of silicon and carbon, and is the third hardest material in the world; the use of this advanced material via 3D printing for applications such as aerospace will be discussed further in this article.
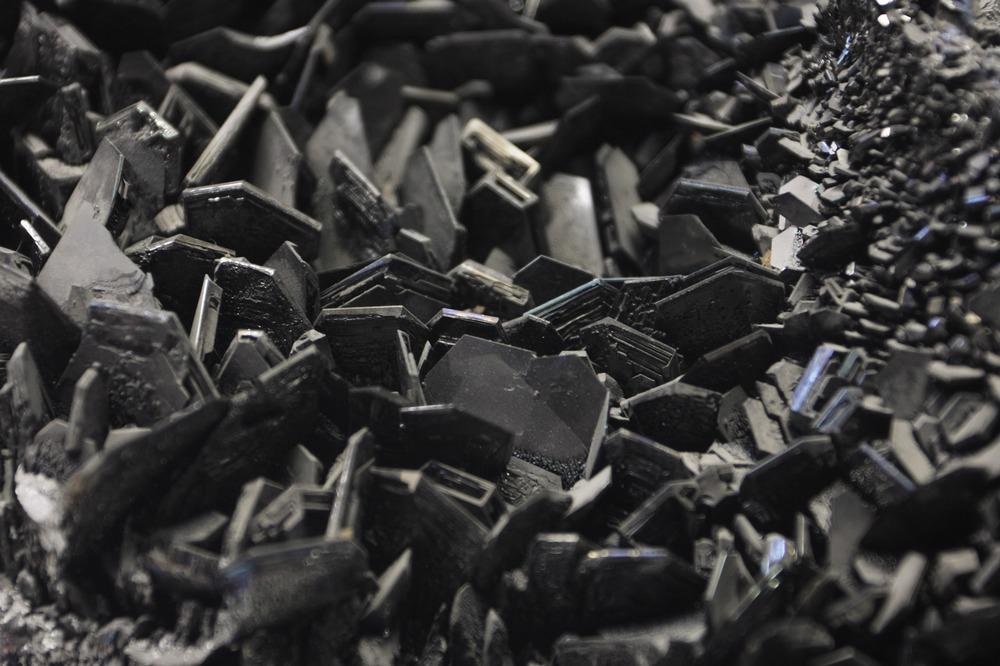
Image Credit: Zoltan Major/Shutterstock.com
The demand for composite materials has risen in recent years with their advantages being recognized more than conventional materials. Carbon fiber materials, which can be used in civil aviation, are 20% lighter than aluminum and have of benefits such as non-corrosion or fatigue, as well as requiring less maintenance.
Passenger aircrafts were previously mainly made from metals such as steel and aluminum, however in the aim of reducing the weight of these materials, other materials gained popularity, including carbon fiber composites.
Silicon carbide, which is otherwise known as carborundum, is a compound which was first discovered by Edward Acheson in 1891; this semiconducting material has gained traction for use in semiconductor devices within various industries. It is seen as an important industrial ceramic material which can be used for structural purposes.
Silicon Carbide Versus Silicon for Electric Vehicles and Electronics
This ceramic material has a unique set of physical and chemical properties that increases its desirability as a manufacturing material, with high hardness and mechanical stability which can withstand high temperatures.
Other advantages such as good thermal conductivity, low coefficient of thermal expansion, as well as high resistance to corrosion and oxidation, illustrate how this advanced material may revolutionize many industries including aerospace.
As astronomical telescopes were advancing and were becoming larger, a new issue was arising: the reduction of mirror weight. This led to the requirements for a new material.
3D printed silicon carbide, which was lighter than metal or glass, was the perfect solution. This material has the ability to be optically polished, which enhanced its suitability for use as a highly effective and lightweight mirror.
Additionally, with its mechanical stability able to withstand various extreme temperatures, it would be an effective material for the low temperatures within space, which can include up to -240 degrees Celsius.
Airbus Defense and Space
Airbus Defense and Space (Airbus DS), having realized the potential of silicon carbide, have collaborated with Mersen, a French ceramic material specialist, in order to create the company Boostec. This partnership aimed to produce high-performing silicon carbide materials with smaller dimensions, such as approximately 3 meters, which would not weigh as much as traditional materials.
Emmanuel Sein, from Airbus DS, explained the significance of this, stating, “The primary mirror is the largest single space telescope mirror in the world, 3.5 meters in diameter and weighing approximately 300 kg. If it had been built with standard optical materials instead of advanced aerospace materials, the mass would have been three tones.”
Airbus DS have previously been successful in creating a highly precise silicon carbide camera for the Rosetta mission and also built the Herschel Space Observatory for the European Space Agency in 2009.
3D Printing for Space
The ambitious objectives of Airbus DS have illustrated its pioneering leadership in aerospace innovation, with the primary goal being to mass produce parts which could transform space engineering through refining 3D printing.
The collaboration of Airbus DS in the European AMAZE project may lead to many innovative advancements in bringing 3D printed parts into space and transforming this industry for a more developed future.
The first 3D printed part which was used in space consisted of a high-strength titanium alloy bracket that was utilized on-board of the Atlantic Bird 7 telecoms satellite; this novel creation was headed by no other than Airbus DS in 2011.
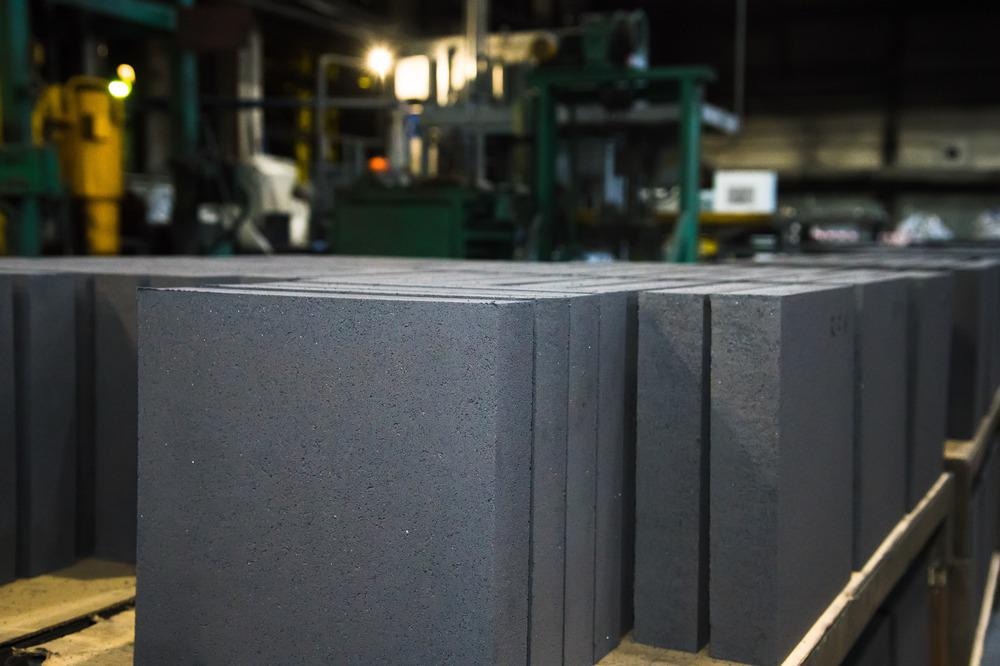
Industrial enterprise for the production of silicon carbide and abrasive materials. Image Credit: SGr/Shutterstock.com
Continuing this pioneering work, Airbus DS was also responsible for the production of the first space-qualified aluminum 3D printed part for the Eurostar E3000 satellite. This innovative component was a high-performing competitor which weighed 35% less than the original part and scored 40% higher in stiffness.
This component was unable to be manufactured using conventional methods, which signifies how 3D printing has provided the potential towards a more advanced manufacturing method; this could enable the production of higher precision and better performing components for aerospace use.
Additionally, this could transform the space material industry, with 3D printed silicon carbide replacing less functional and heavy materials which would in comparison seem outdatedly inefficient compared to its innovative, lighter, and more effective counterpart.
Limitations of 3D Printing for Space
While the potential of 3D printing is limitless for a wide range of applications, a challenge of creating large-scale component space materials using this manufacturing method has not yet been overcome.
Telecommunications Satellites R&D Manager Alan Cox explained, “We must first be able to prove the repeatability of 3D processes and our ability to consistently produce high-quality, affordable components.”
This repeatability and consistency in producing high-quality components is an obstacle which, with time and commitment, can lead to the revolutionary turning point of 3D printing large-scale space materials.
With the AMAZE project, led by the European Space Agency, which consists of 28 collaborating partners including Airbus DS, the goal of refining 3D printing for the mass production of space materials may be quite achievable.
This would truly enable mass 3D printed space materials to become a promisingly tangible reality.
Further Reading and References
Airbus. (2021). Advancing aerospace materials. [online] Available at: <https://www.airbus.com/newsroom/news/en/2016/10/composites-silicon-carbide.html> [Accessed 17 October 2021].
BYJUS. (2021). Silicon Carbide - Structure, Properties, and Uses of SiC. [online] Available at: <https://byjus.com/chemistry/silicon-carbide/> [Accessed 17 October 2021].
Mukasyan, A., (2017). Silicon Carbide. Concise Encyclopedia of Self-Propagating High-Temperature Synthesis, pp.336-338. DOI: https://doi.org/10.1016/B978-0-12-804173-4.00133-2
Disclaimer: The views expressed here are those of the author expressed in their private capacity and do not necessarily represent the views of AZoM.com Limited T/A AZoNetwork the owner and operator of this website. This disclaimer forms part of the Terms and conditions of use of this website.