AZoM speaks with Ozgun Kilic Afsar, a Ph.D. candidate at KTH Royal Institute of Technology, and a Research Affiliate at MIT Media Lab. Ozgun is currently working on the development of, OmniFiber. One of the contexts that Ozgun is currently researching is OmniFiber's potential to allow for intergenerational interactions in opera, such as two experts singing a duet across time and space.
Can you give our readers an overview process involved in the development of OmniFiber?
We have a multi-step fabrication process. In the initial stage, we try to work primarily with commercially available products and materials. The fiber's general construct involves elastomeric materials and composition to make a stretchable sensor and a tubular-braided, interlocking mesh layer.
Going layer-by-layer, we initially have a fluid channel where our working fluid medium runs through, this could be compressed air or a liquid. In our case, compressed air was used in most applications.
The elastomeric layer is a tubular elastomer, and this exists in several diameters. We wanted to miniaturize it to work as a composite fiber possible to structure using traditional textile manufacturing machinery for knitting or weaving multifunctional textiles. For the fiber to go into the knitting machine, certain surface properties are required as well as certain elasticity and flexibility, in order to have a seamless fabrication process.
Considering that we have both worked with commercially available tubing and extruded tubing in our premises, the smallest elastomeric tubing that we used so far has an outer diameter of 600 micron. We have recently purchased an extrusion head that will allow us to go even smaller.
On top of the elastomeric tubing, we devised a method to spray the resistive sensor layer to adhere to the elastomeric layer. So the only material that properly adheres to an elastomeric substrate is another elastomer. You cannot apply, for instance, a polymeric substrate or conductive layer on top of an elastomer unless you go through a lot of surface treatment to have strong adherence.
In our case, that adherence is crucial for high yields in our inflatable fibers. Therefore, we devise the method to make a low viscosity conductive solution using elastomers, a type of silicone, and conductive nanoparticles and mix them until they become sprayable before they cure.
After applying the sensor layers on the microtubule, we used an off-the-shelf tubular braid made of polyester or nylon filaments. These have diameters of less than half a millimeter, which is good because you want their size to be slightly less than that of the diameter of the elastomeric tubing.
As feeding the tubing inside the interlocked mesh requires a lot of manual labor, we are currently building a desktop micro-braiding machine. The plan is that as soon as the tubing is extruded and cured, we will have the braided layer with customizable parameters wrapping directly around it. This way, we can have the whole composite structure go through an automated fabrication process.
The next step is manually adding the pneumatic fittings, because you have to have good sealing on both ends for the sensors and the actuators to work correctly. We discuss this process in-depth in our paper. We devised a surface treatment and combination of rigid fittings and wiring to soft tubular substrates in order to achieve a robust end sealing.
This is the multistep fabrication process of a single fiber. With the automated fabrication machine that we are building, our aim is to have infinite lengths of this robotic fiber although we may not use the entire strand of robotic fiber when making a T-shirt with robotic functionalities. Still, we would like to be able to scale the fabrication for continuous manufacturing on industrial machines for which you might need kilometers of fibers on a spool. At this stage, we achieved 70 meters, but with our automated fabrication technique, we hope that this will increase quite significantly.
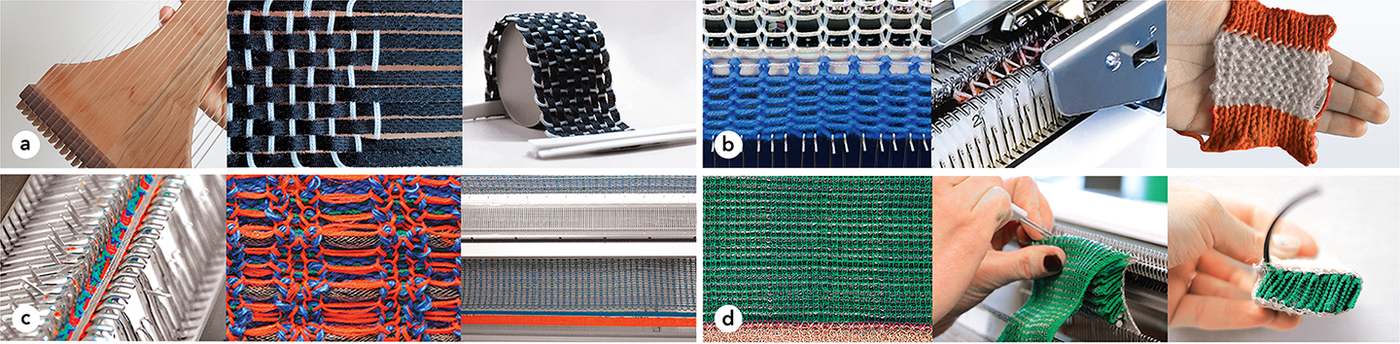
OmniFiber-based swatches with various fiber structuring techniques: (a) Woven (b) Plain knitted and rib knitted (c) Inlay-knitted (d) Weft-knitted quasi-spacer fabric with active OmniFiber spacer layer. Image Credit: Ozgun Kilic Afsar
What are some of the key features of OmniFiber?
OmniFiber is a type of artificial muscle fiber. We are building on previous research in artificial muscles as well as in pneumatically actuated soft robotics. OmniFiber is pneumatically actuated instead of using a thermal actuation or electrical actuation. Of course, we drive our circuit electrically, but only to control the on and off switches in the different nozzles that control each fiber. Otherwise, the main medium that we work with is compressed air.
We have tried other media, such as liquid metals, which could add another functionality to our fiber. We are also interested in working with supercritical fluids because, as you have longer strands of this fiber, a certain resistance will build up which will require much higher working pressures. To actuate the continuous fiber easily, you need the least surface resistance in the tubing core as possible. We believe that working with supercritical fluids will help us decrease the resistance and improve flow rates in return.
We wanted to work with pneumatics because pneumatics is the backbone of industry. And the reason for that is they have a high force-to-weight ratio.
I am interested in working with haptics and touch in terms of interaction and less with the visual shape-changing functionality of fiber. I want to create something that we can feel on our bodies, and for that, you require a certain force range. Suppose I wanted to simulate, for instance, a firm hug in a telepresence interaction setting, like sending out a hug message. To feel that hug through a sweater, T-shirt or jacket, 200 Newtons are required to generate a firm hug. For this, we found most of the existing artificial muscles quite insufficient in the force they provide or too slow in response speed, and we know pneumatics outperform its counterparts in that sense.
Furthermore, for a thermally actuated fiber or an electrically induced thermal actuation, you must constantly provide power to the system to keep an actuated state. So if we consider the hug example, say I want to hug you for 10 seconds, and if I use the thermally actuated mechanism, we would need to provide power to the circuit constantly. Whereas in a pneumatic system, it's just a matter of keeping the valve at its closed state. As long as you have good sealing in the interface, you can keep the actuated state without providing any extra power.
We are also interested in working with immediate feedback. I want to send an immediate haptic message, however to achieve that, thermal actuators have a long way to go because thermal actuation, or actuation based on large temperature variations, is inherently a slow process. There is another fiber mechanism that we're currently working on as a new type of artificial muscle, a thermoresponsive one, and still it takes tens of seconds to be able to achieve the stroke and force of actuation that we are able to achieve with OmniFiber in milliseconds.
Robotic fibers can make breath-monitoring garments
Can you give our readers an insight into the role of the fluid channel employed within the multi-layered fibers?
The fluid channel is a simple tubular-shape channel inside an elastomeric substrate. Currently, we work with a single channel, but extruding our own tubings will allow us to have multiple cores and geometries to run different functional fluids through them, which is again another thread that we pursue in this work.
For example, one of the channels could be used for running a conductive material to utilize the fiber as a sensor. A second channel can be used by the compressed air medium, which also makes it an actuator. This way, you would have the same properties that we do in OmniFiber, but everything is encapsulated in the tubular construct inside the channels, rather than having sensor traces applied onto the surface. Thinking ahead, encapsulating all layers in the elastomeric tubing may help us with washability, for instance.
We secure our sensor channels with another 30 micron-thin elastomeric layer; however, we haven't done washability tests yet. It’s a very important property to have if you want to commercialize a fiber one day, which we hope to.
The fluid channel is the part that contains the compressed air. It expands when you compress a larger volume of air than the tubing can take, and this is the mechanism that our fiber works with. You expand the inner channel with the compressed air until it cannot expand any more in the radial section and, while it's expanding in the radial section, the interlocked layer outside the tubing forces it to contract in length. This is similar to how human muscles work as well.
What benefits does OmniFiber have when compared to existing artificial muscle fibers?
OmniFiber is entirely skin-safe. With thermal actuators, you risk discomfort to the point of burning the skin if you have a malfunction or if there is overheating in a particular location along the thermally actuated fiber. We don't have such a risk unless we work with extreme pressures, which is hundreds of bars, that we will likely never need. Therefore, I feel comfortable saying our fiber is completely skin-safe.
The fact that it is knittable and the surface properties allow it to go into an industrial knitting machine is an advantage over, for instance, more metallic counterparts like shape-memory alloys.
Additionally, we don't need to train our actuators to have a two-way reversibility function, whereas, with shape-memory alloys or twisted and coiled polymeric actuators, you need to program the fibers through an arduous training process.
What are some of the benefits that OmniFiber can provide to singers and performers?
This is very close to home. The central vision and passion in this research is working closely with the human body and movement. Both singers and performers are amazing to collaborate with, because they're experts in controlling their bodies and in their somatic awareness.
I have been working with a professionally trained opera singer for more than a year. My Mom is also a soprano, so I have observed this since my childhood. I have been amazed by how they control their instruments, which are their bodies.
I wanted to understand the physiology of breathing in singing, specifically in the context of this work, because it's an invisible and intangible process. We can try to see what's happening in the laryngeal area, we can try to observe what's happening in the respiratory muscles, but it is not all so visible from the outside.
Working closely with experts helped me to understand this physiology better by actually trying it myself. We have been doing a lot of bodywork around making certain sounds and how my larynx works differently. Part of this process was becoming aware of these muscles in breathing and how I control the rhythm of the voice and sounds that I'm making by understanding it through my own body.
One of our aspirations is to help listeners understand singing physiology better. As for helping out singers, this is another path that I would like to take in my research. Working with experts helped me observe that they are already amazing at what they do.
It is fascinating finding out about their creative processes and get a hold of the tacit knowledge they have built over many years. Robotic technology and robotic wearables could help them become more creative or do something else that they wouldn't be able to do with their bodies without this technology.
I believe the only reason we would put a piece of technology onto the body of an already amazing performer or singer would be if it allowed them to do something more creative or different to change their practice, which is one of the aims.
I will also work with a group of dancers. I will observe how our devices could act as a haptic mediator between the choreographer and a dancer where the choreographer physically communicates the choreography to the dancer. That is one of the subsequent studies, which will likely take place a year from now.
My general area of interest is pedagogical contexts, so learning creative movement in a singing or dance practice, for novice learners to learn how to control their breathing or tensions in their muscles. In singing, for example, things are a lot more nuanced than just breathing low or breathing high. I aim to translate some of this metaphorical language that instructors use in vocal pedagogy into the language of the body through robotic wearables.
My close collaborator, the opera-singer, usually runs this example of "breathing into your back," which may not be so understandable in the early process of learning how to do a particular type of breathing. How about stimulating that specific part of your body with the robotic wearable kinesthetically, so it guides you to do that movement? So, in the pedagogy context, the acquisition of a specific motor skill or the transference of a particular motor skill from the expert to the trainee is of interest to us.
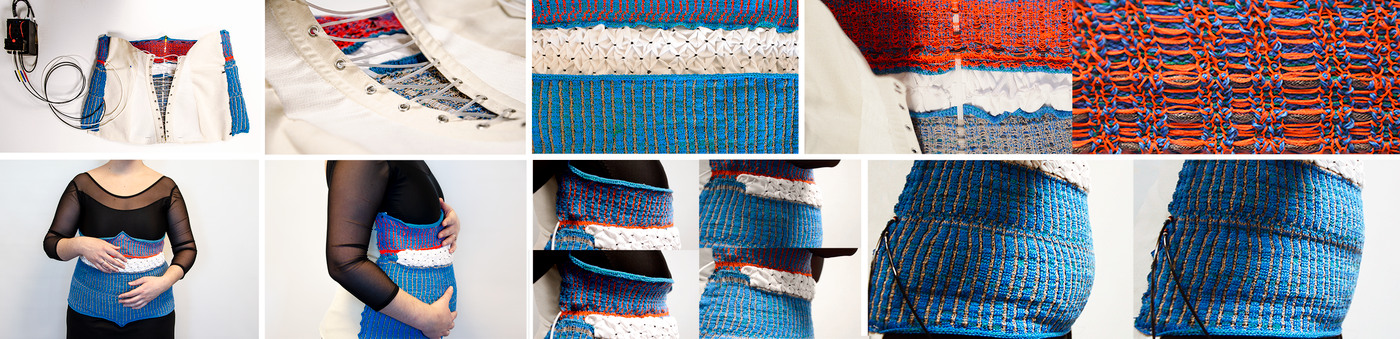
An upper body garment for breathing guidance during singing, peristaltically controlled by FlowIO. Image Credit: Ozgun Kilic Afsar
What were some of the testing procedures involved during the development of OmniFiber?
We have an in-depth discussion that involves the characterization of the sensor in our paper, including how much strain it allows and how much body deformation we can record through them. We also discuss the actuator’s mechanical characterization, as in force and strain outputs of a single fiber at different lengths and thicknesses.
Then we started looking into the textile mechanisms and how we could fabricate a mechanical swatch of textiles - each one with a different functionality - and how we can apply them into garments to create multimodal haptic feedback; compression or skin stretch, vibration, or push forces towards the body. At the fiber,, fabric and garment scale, all of these procedures were tested and detailed in our fabrication and implementation section.
In what ways can OmniFiber be employed to help athletes monitor performance?
I think this is quite interesting in the context of sports or weight training. There was some discussion around how you control your breathing when you're weightlifting, for instance, or optimized breathing patterns when you're a runner. Or even if you're not an athlete, for example, if you're meditating, another mode of breathing will help you get to a meditative state.
We approached the design of the garment, which is aimed to be an undergarment, from a modular wearable approach. For example, in certain types of activities, different types of breathing will be required. Modularity allows for the removal of some parts of the garment and the ability to use the required parts that stimulate the respiratory muscle groups of the choice of respiration type. In addition, you can program and reprogram a certain type of breathing pattern into the garment, to guide you in a specific way.
Earlier this year, UCLA carried out a study with opera singers and post long COVID patients, carrying out breathing exercises over video calls. That would be a fantastic opportunity for us to add a haptic mode of communication to that interaction.
In a medical setting, what are some of the potential uses of OmniFiber?
Wherever breathing is vital, I can see our technology being useful, but it’s certainly not limited to breathing guidance. Recently, many individuals with certain motor disabilities or relatives of individuals who require a rehabilitative device have reached out. The first aim and function of artificial muscles is to help those with motor impairments. When your natural muscles are not working properly, they can help carry out motor tasks.
We have, for instance, made a glove that could either help you have a firmer grasp around a cup or help you learn a piano. So before moving into the creative realm, I can definitely see how our technology can benefit people in their everyday lives.
It could also be applied to people who do a lot of physical work and get tired towards the end of the day, for instance, this could help them finalize their tasks with the support of the robotic system, without too much energy and workforce from their own muscles, to help them in the long run.
Our technology can be used to monitor and communicate between doctors and an outpatient who is recovering from a certain motor impairment. Patients can communicate their movements remotely to their doctor or physiotherapist without having to go to the hospital.
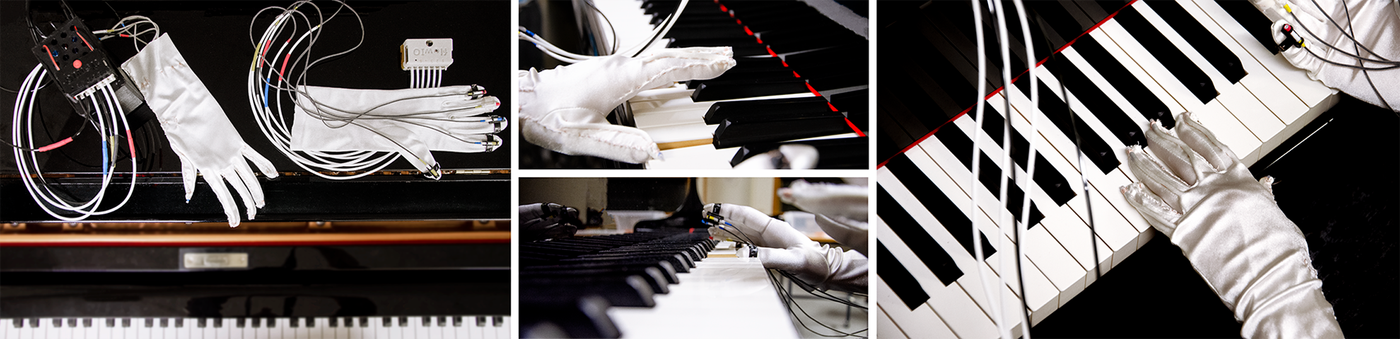
Piano skill gloves with (1) attachable/detachable fiber devices, (2) sewn in fiber devices. Image Credit: Ozgun Kilic Afsar
What are your predictions for the future of 'robotic' textiles?
I definitely see morphing textiles or shape-changing textiles with a sensing and an actuation component, which are simply transducers, making their way into society.
As researchers and inventors, we have a huge amount of responsibility for the ethics of such technology that is very close to our bodies. Part of my research is very focused on the politics of the body and the ethics of wearable technology. We have to think about these before these robotic fibers and fabrics become abundant and part of our everyday wear.
There is a research group at MIT at the forefront of Advanced Fibers, led by Professor Yoel Fink, working on computing fibers and fabrics. They embed the processing system inside a fiber, which, in effect, means we could have both the mechanical transducers like we have achieved, but also a system that could process and store this information within the textile without requiring any external memory or microprocessor.
I think robotic textiles will be very beneficial in monitoring our everyday activities, everyday changes in our body from very observable changes to in-body changes and things that we wouldn't otherwise observe.
If our garments can learn about our bodies and adapt to them in the long run, this could help both in the sustainability of our everyday wear and could change the whole fashion industry. However, until then there is a long road ahead in terms of how we can recycle such composite structures with all the embedded power lines. It will be a very different future in many ways, but I am excited to be a small part of that.
In terms of OmniFiber, are there any developments in the pipeline?
One is definitely scaling the manufacturing, we have a long way to go to make the fabrication process fully automated. Simultaneously, we will be working in different contexts: in the sports science context with both industrial and academic collaborators to build finalized designs for specific case scenarios other than our current breath regulation application.
As part of the fabrication process, we are looking into more miniaturized devices, working with different functional fluids for sensing as well as having control over the interlocking mechanism so we can embed different modes of actuation in a single strand of fiber.
What would obviously become a strong need, is a computational design tool that would support building and simulating these heterogeneous mechanisms in the first place. For example, if there's a textile or fashion-tech designer that is working with our material, they would like to see how things will behave before they implement their designs. So, a design and simulation tool is absolutely necessary as the behavior of the fiber when made into textiles is not so intuitive.
Finally, as part of the research project for my Ph.D., we are investigating energy harvesting from human movement to provide high pressure microfluidic actuation to our system. We are looking at having a small enough tanks that hold the compressed air as the energy source to activate your wearable device which is mostly produced by you and your everyday movement.
Where can readers find more information?
Project: https://www.media.mit.edu/projects/omnifiber-millifluidic-muscle-fibers/overview/
Profile: https://www.media.mit.edu/people/ozgun/overview/
Linkedin: https://www.linkedin.com/in/ozgun-kilic-afsar-47456a37/
About Ozgun Kilic Afsar
Ozgun Kilic Afsar is a Ph.D. candidate at KTH Royal Institute of Technology, and a Research Affiliate at MIT Media Lab. She completed her master's degree at the Royal College of Art in London. Her current research focuses on sensor integrated soft robotic fibers and textiles that correspond to the dexterity of human biomechanics.
Such active textile systems feature multimodal haptic feedback to kinesthetically support skill acquisition and transfer in creative movement practices. Her work has recently been featured as a cover story on MIT News. She is currently working on a robotic undergarment and researching its potential to allow for intergenerational interactions in the context of opera, such as two experts singing a duet across time and space. Her aim is to generate a tangible skills database to safeguard somatic skills in the form of haptic notations through soft robotic materials.
Disclaimer: The views expressed here are those of the interviewee and do not necessarily represent the views of AZoM.com Limited (T/A) AZoNetwork, the owner and operator of this website. This disclaimer forms part of the Terms and Conditions of use of this website.