A recent study in the journal Polymers identifies means of regulating the shrinkage effect of UV curing to enable its use for precision devices.
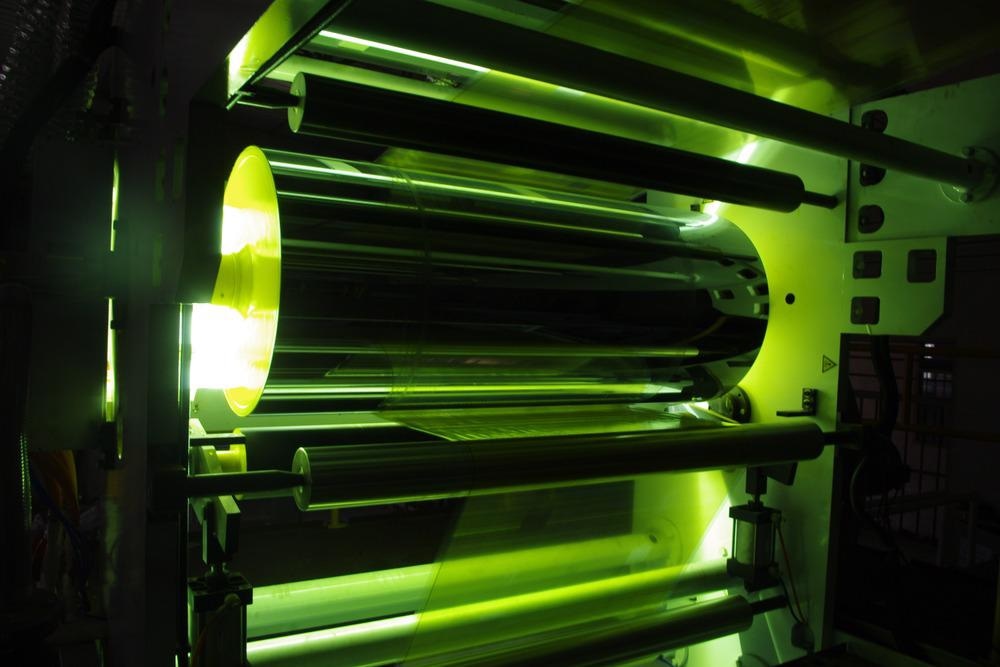
Image Credit: Narudol Mongkollapkit/Shutterstock.com
Background Information
The process of UV curing coating is primarily a surface treatment process for protection and enhanced lifetime. The UV curing could be termed as a drying process accompanied by the occurrence of polymerization. However, UV curing coatings are not preferred for precision instruments due to the shrinking of material resins.
This article is focused on the latest study on a novel technique substantially reducing the shrinkage in UV coatings. The advantage of UV curing is the reduced time as compared to traditional techniques. The strong forces developed due to polarization also increase the strength and result in a vast improvement in mechanical and chemical properties. The technology truly has revolutionized the future of UV curing.
Material Composition and Properties
Ultra Violet curing technology grew rapidly during the 1990s due to its various advantages over the classical methods.
The basic constituent elements in UV curing consist of acrylated urethane resins, acrylated oils, unsaturated polyesters, oligomers, diluents, photopolymerization initiators, and other additives for process optimization such as pigments and stabilizers, etc. Acrylated polyesters are manufactured with variable viscosity values and have a considerably low molecular weight.
Epoxies are useful as their properties offer a good cure rate. They are characterized by relatively higher skin irritancy and the high molecular weight of epoxy resins. Such properties allow them to have top-notch corrosion resistance properties. Urethanes are preferred because of their well-known good qualities such as toughness, stability, temperature, and chemical resistance along with a faster cure rate.
Industrial treatments are necessary to lower the viscosity of diluents for effective operations. This is done by the inclusion of monomers in a higher quantity. The selection is based upon essential properties such as financial constraints, volatility, solvation efficiency, and odor.
Photoinitiators are light sensible materials and enable the utilization of absorbed light for polymerization of the binder. The photoinitiator is critically selected keeping in mind the wavelength region of light and radiation properties. Hence, all materials are carefully selected after careful consideration regarding their properties and compatibility.
Industrial Usage and Limitations
UV curing technology has been implemented by various industries such as the printing industry, with screen and letterpress printing. The paper and ink industry utilizes it for increasing the lifetime of its products. The plastic manufacturing industry utilizes UV curing for special purposes such as plastic packaging.
UV rim coating improves production and packing effectiveness, which leads to higher profits. The distinct process properties of UV curing allow it to be utilized for almost any substrate such as composites, magnetic recording tapes, leather, vinyl, and even human teeth.
Even with such advantageous characteristics, UV curing has industrial application limitations. It involves acrylated polyesters usage and their utilization has a major disadvantage. Their low molecular weight leads to low reaction rates and an increase in surface inhibition. A few other limitations include the lower penetration of UV curing and high price along with the large volume of UV curing equipment.
However, recent equipment such as NETZSCH's Photo-DSC 204 F1 Phoenix has a suitable size and provides efficient UV curing. It is also operable from -100°C to 200°C and allows the user to select suitable light intensity, temperature, and exposure time. However, the major limitation is the shrinkage that occurs in precision devices by UV curing. The latest research by Mr. Y. Tao and his team has represented a successfully implemented anti-shrinkage UV curing model.
Latest Research
The latest study involves integrating hollow polyurethane acrylate (PUA) microspheres with the mixture of tripropylene glycol diacrylate (TPGDA) coatings. The PUA is mixed with various fractions of volume mixture with different diameters and thicknesses. An empirical formula relating various geometric parameters and shrinkage ratios is also developed.
The essential reagents include 2-hydroxy-2- methyl propiophenone (Photoinitiator 1173), 1,6-hexanediol diacrylate (HDDA), Polyvinyl alcohol (PVA), and PUA resin. Microfluidics technology was utilized for PUA microspheres manufacturing.
An amalgam of TPGDA coating and PUA mixture was created to adjust the shrinking ratio. Photoinitiator 1173 and TPGDA solution was created with weight ratios of 3% and 97%, respectively. The curing process results in polymerization causing resin phases to be solidified. Thin films of PUA material go through mechanical experiments; nanoindentation and in-situ tensile tests are performed for experimental results and validation.
The development of the anti-shrinkage model is done by TPGDA mixture with PUA spheres, with uniaxial tensile tests and finite element analysis (FEA) utilized initially for mechanical properties followed by the development of empirical formula.
Nanoindentation tests were done to accurately measure Youngs’ modulus of PUA films. The FEA analysis was conducted in Abaqus via an accurate RVE model development. For validation, a system without microspheres acts as the reference control group. The experimental results are first compared keeping in mind the standard system, and then with the empirical formula developed.
The study showed that results are comparable and resulted in the successful development of the anti-shrinkage model for UV curing.
Implications and Limitations
The modern study developed a model which prevented the shrinking of resins after UV curing.
This would enhance the mechanical properties of substances after the UV curing process which converted intermolecular forces into intramolecular forces.
The reduction in shrinkage results in a decrease in coating stress cracking, stresses, and warpage, hence increasing the efficiency of UV curing and increasing lifetime and mechanical properties of products related to various industries such as the paper industry, plastic industry, pipe repairs, composite industry, and vinyl industry.
Along with this a substantial reduction in shrinkage would allow the utilization of UV curing in the precision instruments industry resulting in a revolutionization in the manufacturing industry.
Although this is useful in every aspect, however, this process was done using only acrylated urethane microspheres. The calculations for other polymers would be quite different so would be the resulting properties.
In short, the problems due to UV shrinking in precision instruments was the sole reason for their restricted usage. However, this study along with several others focused on the purpose of reducing shrinkage has been very beneficial and productive.
The implementation of this research in various industries, especially precision instruments, would result in increased applications of UV curing throughout the world.
References
Marx, P., & Wiesbrock, F. (2021). Expanding Monomers as Anti-Shrinkage Additives. Polymers, 13(5), 806. Retrieved October 24, 2021. https://www.mdpi.com/2073-4360/13/5/806
Tao, Y., Sun, G., Wei, Y., Liu, R., & Zhao, J. (2021). An anti-shrinkage model of an ultraviolet-curing coating filled with hollow polyurethane acrylate microspheres. Mechanics of Materials, 163. doi:https://doi.org/10.1016/j.mechmat.2021.104091
Xu, J., Jiang, Y., Zhang, T., Dai, Y., Yang, D., Qiu, F., . . . Yang, P. (2018). Synthesis of UV-curing waterborne polyurethane-acrylate coating and its photopolymerization kinetics using FT-IR and photo-DSC methods. Progress in Organic Coatings, 10-18. https://www.researchgate.net/publication/327371815_Synthesis_of_UV-curing_waterborne_polyurethane-acrylate_coating_and_its_photopolymerization_kinetics_using_FT-IR_and_photo-DSC_methods
Disclaimer: The views expressed here are those of the author expressed in their private capacity and do not necessarily represent the views of AZoM.com Limited T/A AZoNetwork the owner and operator of this website. This disclaimer forms part of the Terms and conditions of use of this website.