Steel wire is used in demanding, safety-critical applications. This article details the development of OES technology to ensure tough wire specifications are met.
At first glance, steel wire appears to be ordinary, and several of its applications are also rather ordinary, such as springs, chain-link fencing and the basic nail. However, upon closer inspection, steel wire is anything but mundane.
Steel wire is mainly used for demanding, safety-critical aerospace and automotive applications, such as valves in engines or within headrests.
A more common application is reinforcement in car tires. The wire must measure up to a precise specification; selected for its strength while supporting tire specification in relation to driving performance and fuel economy.
Evaluating and confirming the material properties and composition of the wire is a crucial part of the production process.
Steel Wire Production
It’s useful to put the process into context by taking a look at how steel wire is made:
Rolling
Recycled scrap is smelted to create a square billet, which is then rolled in a blooming mill to lessen the cross section. Rolling continues within an intermediate mill until the steel wire achieves the specified size. For tires, this is generally 5.5 mm in diameter. The wire is cooled before moving on to the next phase of production.
Treatment
The next production stage introduces various treatments, such as annealing and pickling.
Annealing is the heating and cooling of the wire in line with a particular temperature vs. time profile. This alters the physical characteristics of the wire, predominantly by increasing ductility and reducing hardness; a crucial step as the wire will be subjected to further processes, including shaping and/or machining.
Pickling involves a chemical treatment where undesired surface oxide is eliminated by dissolution in acid. These treatments depend on the specification for the final application.
Analysis
Eventually, the wire is tested to verify that its performance meets expectations and reaches the specified criteria prior to distribution. From each steel wire ring, a section is cut off and sent to the lab for testing.
Usually, tests are performed to check the surface quality, size and shape, tensile strength, decarburization and chemical composition. Chemical composition has a significant bearing on the wire’s overall performance.
Why OES Spark Analysis?
Establishing the chemical composition provides the basic steel grade and key information relating to other elements that are present and may affect the performance of the wire over its lifetime.
For instance, in the analysis of wire developed for use in tires, it would need to demonstrate that it is indeed high carbon steel and confirm the exact amounts of other elements, such as silicon, phosphorus, manganese and sulfur. Not all analysis methods can pick up these elements at extremely low levels; therefore, OES is the industry standard.
OES can measure a vast range of elements and concentrations. It delivers exceptional accuracy when measuring low levels of tramp and trace elements and is very good at providing reliable stainless-steel L-grade information.
OES is the only technology that can analyze the nitrogen content in duplex and austenitic stainless steels.
On a practical level, OES is rapid and advanced equipment is simple to use and comparatively inexpensive to operate. Sample preparation is straightforward, and a number of components can be tested, including bolts, tubes, wires and plates.
How Does OES Work?
OES is a spectral analysis technology, which means that it works by identifying the specific spectrum radiation a material emits when that material is exposed to an application of energy. The resulting spectrum determines what material is present.
By heating a small area of the sample, vaporization of the material occurs. This influences the atoms of the material, which then emit light of particular wavelengths. Each element emits a specific pattern of radiation, and the instrument’s detection technology can ‘read’ the spectrum to determine which elements are present.
In a real-world metallic sample, each element has an intricate spectrum of numerous wavelengths of light, giving rise to an immensely complicated set of emitted spectra. There are three key components of the optical emission spectrometer that function to supply accurate results:
- Spark generator that contains an electrode linked to a high-voltage source within an argon atmosphere. Application of the spark stand to the metal sample generates a high-voltage electrical discharge that vaporizes the metal.
- Optical system in which the spectrometer is housed. The light that the atoms emit from within the sample is split up into singular wavelengths (using a diffraction grating), permeating the detector. This detector evaluates the intensity of light for each wavelength.
- Instrument software translates the thousands of signals from the detector to determine which elements are present in the tested sample. Further equivalence testing of detection limits with calibrated reference levels enables the software to identify how much of each element is present.
Now a general understanding of how OES and the components in the instrument work have been established, the discussion can focus on the challenges of the technique for steel wire analysis and how advances in OES technology are helping move past any obstacles.
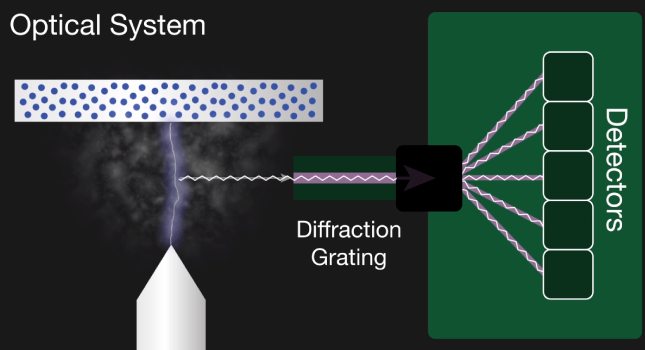
Image Credit: Hitachi High-Tech Analytical Science
Why is OES Wire Analysis so Tricky?
The problem with getting accurate OES readings from steel wire is relatively simple: the spark gap opening is larger than the steel wire.
In the perfect measurement scenario, the opening at the end of the spark stand in which the spark electrode is housed would be completely covered by the surface of the metal to be measured. This makes sure that air does not pass into the argon-filled spark stand chamber.
There are two main reasons that air should not be present in the chamber:
- Oxidation of the metal surface occurs as soon as it is vaporized, which means the oxide would be analyzed rather than the basic metal.
- Some of the most crucial elements for wire analysis, such as phosphorous, carbon, sulfur and boron, emit light in the UV range. Air absorbs UV light, so if air enters the spark chamber, any UV radiation emitted from the sample is re-absorbed before it has a chance to be detected by the instrument, and analysis will fail to identify these elements or display concentrations that are extremely low. This will either cause the rejection of perfectly good wire or, even worse, allow wire to pass that doesn’t meet the spec.
Getting Accurate OES Results for Thin Steel Wire
Advanced OES instruments such as the FOUNDRY-MASTER Smart and the OE series from Hitachi High-Tech are conquering this issue with thin wire analysis in two ways.
Firstly, the spark chamber opening is reduced using special adaptors that fit the exact diameter of the wire. This improves the method, but it’s still difficult to place the small analyzer head in the exact place on the wire. The fact that the wire is round increases the difficulty in achieving a perfect, even seal between the spark head and the wire surface.
So, the second measure involves preventing ingress of air into the spark chamber, even if the spark head is exposed to the atmosphere. This is accomplished utilizing specialized laminar flow technology that facilitates a smooth flow of argon around the electrode, which protects the plasma from the negative effects of in-streaming air passing into the spark stand chamber.
This makes analyzing wire, even down to 5.5 mm tire specifications, a relatively simple exercise. Firstly, a piece of wire from a new batch is extracted from the annealed ring, and the surface is primed to ensure a clean, non-contaminated surface ready for analysis.
The appropriate adaptor for the wire diameter is placed on the spark head, and the wire is fixed in place onto the adaptor. To ensure accuracy, the equivalent program for the right wire diameter must also be selected on the instrument’s software. If the analysis fits within the tolerances of the specification, the other rings of the batch can then be analyzed.
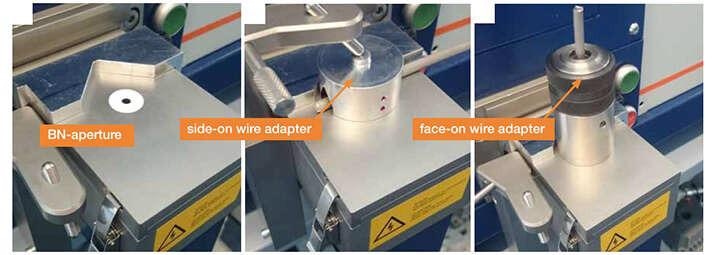
Image Credit: Hitachi High-Tech Analytical Science
100% Quality Control
OES is the superior method for analyzing steel wires that are bound for use in safety-critical applications. With the appropriate measurement methods and application of the right spark technology, the challenge of thin wire measurements can be circumvented, and accurate results for each ring of steel wire distributed can be achieved.
Contact Hitachi for a demonstration to discover how the OE series could help users attain the accurate analysis of wires.
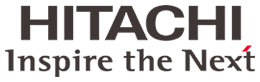
This information has been sourced, reviewed and adapted from materials provided by Hitachi High-Tech Analytical Science.
For more information on this source, please visit Hitachi High-Tech Analytical Science.