Laser surface engineering methods apply precise laser energy to metal surfaces to increase hardness and wear resistance. A recent study published in Metals found that combining laser surface engineering techniques with nitriding created superior wear resistance for AISI P21 steel used for plastic molds.
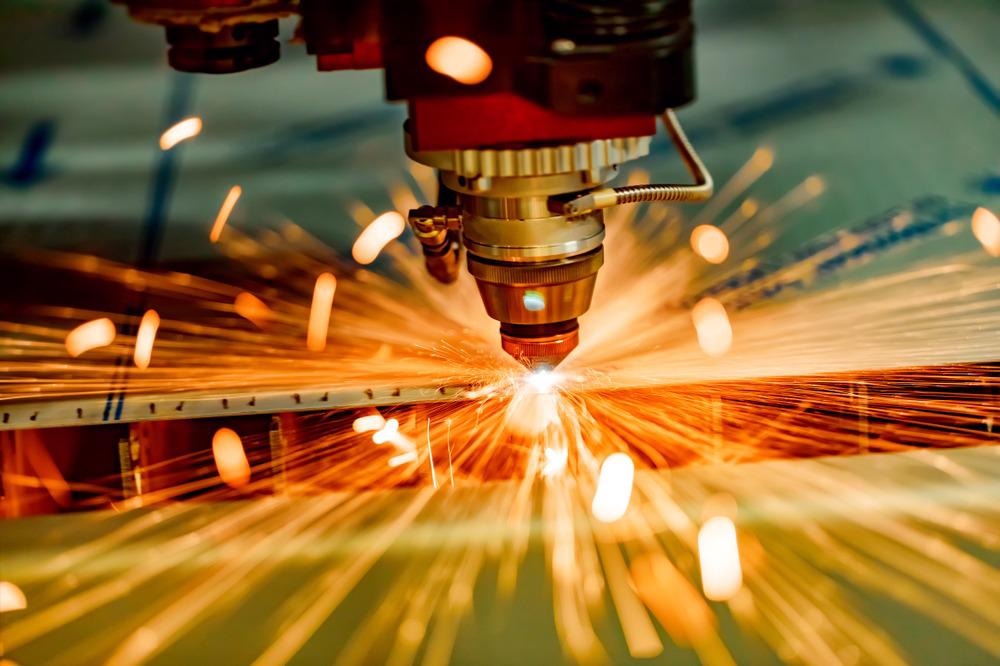
Image Credit: Andrey Armyagov/Shutterstock.com
Hardened P21 Steel for Plastic Molds
AISI P21 steel has good mechanical properties with excellent machinability and is, therefore, a commonly used material for plastic injection molds. Plastic injection molds are required to be used millions of times over in mass production for plastic items.
This extremely high wear requirement means that molds are often damaged by wear, corrosion, and fatigue during the plastic injection molding process. Damaged molds must be replaced to ensure satisfactory quality in the production process, incurring increased production costs for manufacturers.
Surface treatments prevent molds from becoming damaged, improving their lifespan and providing a long-term return on the treatment investment.
Despite this, there has been scant research on the surface treatments and their influence on P21’s microstructure, mechanical properties, or functional properties. The study, led by researchers at Inha University, Korea, and the Korea Institute of Machinery and Materials provides new evidence for surface treatments on P21.
Laser Heat Treatment
Lasers have been widely used in surface treatment applications due to their high precision, high speed, and selectivity. Lasers are a highly versatile tool with novel properties, leading to increasing adoption in industrial metal treatment operations.
During laser treatment, materials can cool very quickly compared to other surface engineering techniques. This means that laser treatments can be applied to a range of materials, even glass.
Laser hardening methods are commonly used for steel and cast iron materials. Controlled, localized heating preserves the metallurgical properties of the base material while creating a hardened surface to increase wear resistance.
Laser surface engineering typically creates a hardened layer up to around 0.2 to 2.0 mm into the material, while the shape of the hardened area can be controlled with beam shaping optics.
Products used for laser heat treatment can also be used for heat-assisted roll-forming, heat-assisted stamping of ultra-high-strength steels, thermal-assisted bending processing of high-strength steels, and other surface structuring applications as well.
Laser Nitriding
Nitriding is a heat treatment technique that works by diffusing nitrogen into the metal’s subsurface to obtain a hardened surface. Nitriding is typically carried out with a plasma arc and is widely applied in manufacturing. Gears, die-cast tools, camshafts, crankshafts, molds, and other metal parts that need to have extremely high wear resistance all benefit from plasma nitriding.
Laser nitriding was first proposed in the early 1980s and has been a focus of research since then. Laser nitriding has the potential to be a much more precise process than plasma nitriding and therefore may be suitable for more selective surface engineering applications.
Further Reading: The Significance of Laser Surface Functionalization
Usually, the part to be treated is placed in a nitrogen chamber for laser nitriding to take place. A high-intensity laser is employed, for example, an excimer-, CO2-, or Nd-doped yttrium aluminum garnet. The laser beam is directed to the target area, where it produces nitrogen plasma and melts a small volume of the surface. Then, precursor nitrogen diffuses into the melted area of the surface.
The technique limits treatment to a few square millimeters for just a few shots; the sample is moved and retreated to create a uniformly treated surface. This means that the material is only exposed to the laser for short periods of time, and heating can be highly localized. As a result, laser nitriding works with heat-sensitive materials.
Testing Laser Treatments for P21 Steel Molds
Both traditional laser heat treatment and laser nitriding were applied to AISI P21 steel components for plastic mold injection machines. For both techniques, the team used a high-power diode laser in order to create a high durability plastic injection mold from P21 steel.
After applying the treatments, the team used transmission electron microscopy (TEM) and electron energy loss spectroscopy (EELS) analyses to determine how the samples’ microstructures evolved during treatment.
They compared measurements of the samples’ microhardness taken before and after treatments, and also performed a pin-on-disk tribotest on the base metal, laser heat-treated P21, and laser nitrided P21. This latter experiment was used to investigate the correlation between laser treatments and wear behaviors.
TEM and EELS analysis showed that nitrogen (N) diffused into the melted P21 steel, while aluminum (Al) in the alloy also diffused toward N. This was attributed to a relatively strong chemical affinity between N and Al compared to iron (Fe), steel’s other main component. This resulted in the formation of a number of aluminum-nitrogen (AlN) precipitates forming within the nitrided samples’ subsurfaces.
Microhardness measurements showed that P21 steel’s surface hardness increased from 409 HV to 536 HV after laser nitriding, while there was no hardness increase for other laser heat treatment methods used on P21 in the study. Wear resistance was also increased in the laser nitrided P21, while the base material and other heat-treated samples showed no increase in wear resistance.
The efficacy of laser nitriding for P21 steel was attributed to the development of hard AlN precipitates in laser nitrided P21’s subsurface.
References and Further Reading
Lee, K-H., et al. (2016). Microstructure and Hardness of Surface Melting Hardened Zone of Mold Steel, SM45C using Yb:YAG Disk Laser. Journal of Welding and Joining. Available at: https://doi.org/10.5781/JWJ.2016.34.1.75.
Meka, S.R., et al. (2016). Generating duplex microstructures by nitriding; nitriding of iron based Fe–Mn alloy. Materials Science and Technology. Available at: https://doi.org/10.1179/1743284715Y.0000000098.
Shin, W-S., et al. (2020). Effect of Laser Heat-Treatment and Laser Nitriding on the Microstructural Evolutions and Wear Behaviors of AISI P21 Mold Steel. Metals. Available at: https://doi.org/10.3390/met10111487.
Sim, A. et al. (2019). Effect of laser-assisted nitriding with a high-power diode laser on surface hardening of aluminum-containing martensitic steel. Optics and Laser Technology. Available at: https://doi.org/10.1016/j.optlastec.2019.03.040.
Disclaimer: The views expressed here are those of the author expressed in their private capacity and do not necessarily represent the views of AZoM.com Limited T/A AZoNetwork the owner and operator of this website. This disclaimer forms part of the Terms and conditions of use of this website.