Research and development processes, design and analysis, material selection, and prototype testing techniques are an essential part of the global automotive industry. The vehicles have to operate under vacillating stresses as well as varying pressures and variable environmental conditions such as ambient temperature, extreme rain, etc.
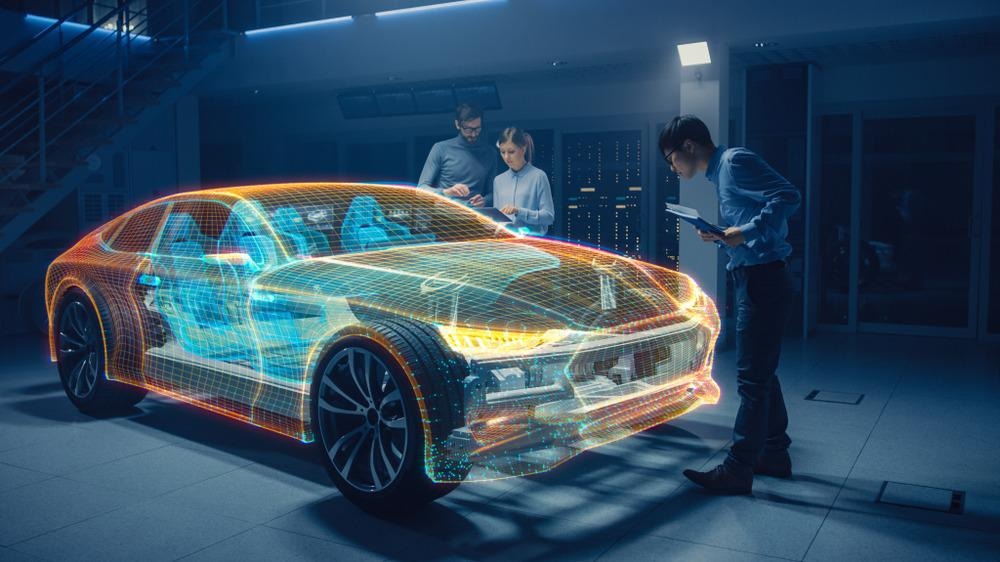
Image Credit: Gorodenkoff/Shutterstock.com
The automobile sector must ensure that its products can function in such a wide temperature range and with such fast temperature fluctuations without failing or experiencing material fatigue.
An automobile test bench, also known as a testing workbench, is a configuration used to validate the roadworthiness or soundness of an automotive design or model.
Automotive diagnostic processes are as varied as the test samples. Among several testing procedures, thermal simulations guarantee that materials stay (dimensionally) durable at high temperatures or swift temperature fluctuations, gaskets remain leak-free across a large dynamic range of temperature and pressure, and pumping systems perform effectively irrespective of medium-temperature and viscosity.
History of Temperature Control in the Automotive Industry
The 1929 Ford Model A was the first automobile to provide heat within the cabin as a factory-installed option. These new vehicle heaters delivered hot air from the powerplant into the car's interior, but the method had certain drawbacks, most notably a latency in heating up.
A crude kind of climate control was not available as a factory-installed option until the 1939 Packard. The "Weather Conditioner" was a $279 accessory that needed the Packard One-Eighty to be installed at a separate facility. Finally, Cadillac introduced Temperature Comfort Control, the world's first completely automated climate control system, in 1964. This was a pure analog system with three thermistors.
Materials and Methods
Temperature control is most commonly seen in test and inspection rigs, as well as material testing, in the automobile industry. To verify that all components of a car perform correctly and reliably throughout future usage, they are subjected to extraordinarily high-temperature changes. The temperature control test facility consists of temperature chambers with various sizes and available features.
Rapidly evolving temperature control systems are utilized in components and subassembly tests on a vehicle test bench, allowing for exact conditioning and quick temperature changes. Only perfect thermal management yields dependable and repeatable outcomes.
Thermal management systems give consistent temperatures or complicated temperature distribution to the workbench via liquid media, either explicitly or implicitly. Temperature monitoring systems, in addition to controlling the intermediate temperature, also allow for accurate regulation of circulation and static pressure.
Static tests are often done in a thermal control testing chamber following the ISO 12097-2, which includes testing of airbag modules.
Limitations of Temperature Control Testing
Although these tests are essential, certain limitations and complexities are associated with them. First and foremost, the cost and financial aspect is an essential one, as these processes are quite expensive owing to the costs of equipment and components.
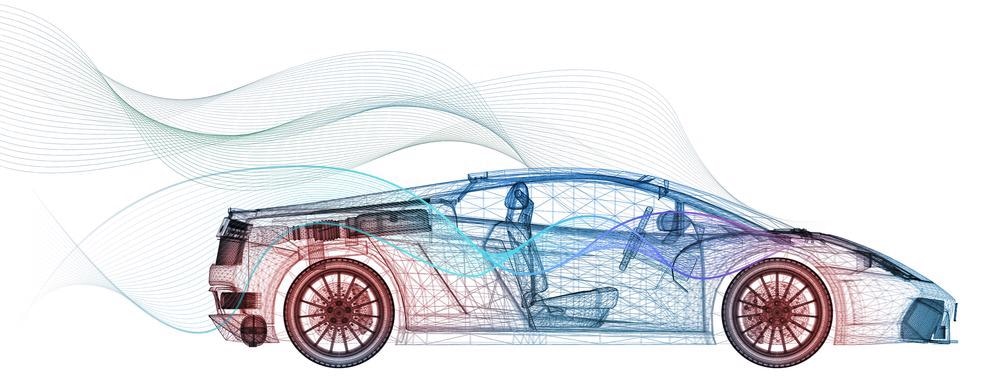
Image Credit: Italyan/Shutterstock.com
Along with this, quite a complex measurement circuit is needed, requiring an intricate design with a strong current source. In most cases, the presence of a bridge circuit is necessary that leads to increased costs. Sensitivity issues have also been observed in many cases, yet the necessity of this process cannot be negated. That is the core reason the automotive companies spend a hefty amount of money for this testing.
Research Findings
According to the latest research, thermal management systems are employed largely in two ways: to imitate exterior climatic conditions in a controlled room or to substitute internal networks, such as the engine's cooling cycle.
The latter enables the creation of real-world conditions on the testbed in which the test samples are sprayed with coolant following the operating procedures, such as in a car. The test specimens, on the other hand, can be specifically tempered and so, for example, pushed to their load limitations within the framework of safety testing.
Another major aspect is the development of active thermal management systems after control testing. In modern automotive products such as cars, water-cooled proton exchange membrane fuel cells (PEMFC) are incorporated.
A microcontroller, a coolant, air conditioners, a circulatory cooling system, and two temperature sensors comprise the thermal energy storage system of the PEMFC application on the automobile. The temperature is effectively controlled via the circulating water which effectively dissipates the heat out to maintain a standard temperature ensuring effective efficiency along with uninterrupted durable operation.
Limitations
The major limitations are the need for a separate workplace for effective testing. Along with this, the resulting control and management system is quite expensive and adds extra weight, which affects the overall performance efficiency of the product.
The integration of this novel technology may require design modifications which is a challenging task delaying the manufacturing of the product by a reimplementation of all steps including design, analysis, and testing.
Future Perspective
According to the latest Market Research Future (MRFR) study, the automotive temperature control system market is expected to develop at a 5.04 percent CAGR during the forecast period (2020-2027). Nowadays a lot of research is focused on the incorporation of semiconductors for these purposes.
The utilization of semiconductors is quite advantageous for thermal management systems owing to advantageous superior thermoelectric properties and affordable costs.
MEMS, IC sensors, and infrared temperature sensors are predicted to be emerging innovations as luxury automobiles become more common throughout the world and wiring harnesses get smaller. MEMS temperature sensors are widely employed in all major sophisticated applications for both electric and conventional automobiles.
In short, it wouldn’t be wrong to deduce that temperature management and control testing is a major technological breakthrough with substantial upscaling potential in the future.
References
Giampieri, A., Chin, J. L., Smallbone, A., & Roskilly, A. (2020). A review of the current automotive manufacturing practice from an energy perspective. Applied Energy. https://www.sciencedirect.com/science/article/pii/S0306261919317611
Julabo. (2021). Material and Component Tests. From Julabo: https://www.julabo.com/en-ushttps://www.julabo.com/en-us
Zhang, J., Wang, Y. X., He, H., & Wang, Y. (2020). Active Thermal Management for an Automotive Water-Cooled Proton Exchange Membrane Fuel Cell by Using Feedback Control. Vehicle Power and Propulsion Conference (pp. 1-5). Gijon, Spain: IEEE. https://www.semanticscholar.org/paper/Active-Thermal-Management-for-an-Automotive-Proton-Zhang-Wang/11078d5c8a0b3d9018119d02d861e7a5245f2b37
Zhou, F., Ren, Q., Yuan, S., Hong, S., Guo, W., Yu, J., & Qian, X. (2020). Temperature control strategy optimization for vehicle fuel cell stack under the real road condition. IEEE Chinese Automation Congress. https://ieeexplore.ieee.org/document/9326876
Disclaimer: The views expressed here are those of the author expressed in their private capacity and do not necessarily represent the views of AZoM.com Limited T/A AZoNetwork the owner and operator of this website. This disclaimer forms part of the Terms and conditions of use of this website.