Chemical mechanical polishing (CMP) is a process of global planarization that leverages the synergetic effect of chemical reactions and mechanical abrasion to facilitate wafer polishing.
CMP has become one of the cornerstone techniques in contemporary integrated circuit (IC) manufacturing processes, ranging from position lithography and patterning steps to controlling topography and maintaining appropriate wafer surface characteristics.
The importance and use of these applications have increased due to ongoing demands for reduced device sizes, and enhanced performance has driven the need for increasingly stringent requirements around semiconductor manufacturing.
Therefore, it is essential that new and evolving CMP technologies meet these requirements while accommodating new demands as they arise.
This article explores how Bruker’s TriboLab CMP rises to these challenges. This instrument offers reliable CMP quality control and optimization, as well as helping to optimize the evaluation of novel CMP technologies by both suppliers and end-users – both in series and in parallel.


Figure 1. The top graph shows pad wear rate in millimeters. Conditioning discs 8 and 9 show lower wear. The bottom graph shows friction variation with time, and conditioning discs 8 and 9 also showed longer stabilization time (in terms of COF). Image Credit: Bruker Nano Surfaces
Quality Control of CMP Processes
The large number of different components involved in owning CMP equipment result in high maintenance costs. In 2013, the value of the CMP market exceeded 2.5 billion dollars, with the consumables market exceeding the value of the systems market.
Much of this high cost of ownership is linked to the manufacturing process’s inefficiencies, for example, polish rate drift and excess downforce (Fz).
Bruker’s TriboLab CMP represents a reliable means of mitigating these issues thanks to its easy-to-use evaluation routines, including custom test creation capabilities and a series of pre-defined monitoring and quality control recipes.
CMP is employed alongside precise and accurate metrology measurements to manage product quality and consistency as part of CMP processes. Even the slightest variability in terms of the chemicals used or the process conditions can have a direct impact, prompting variations in processes and polish metrics.
These variations can cause issues such as selectivity, corrosion, defects and inadequate polish rates. These problems can be directly addressed on a smaller scale through the use of the TriboLab CMP, allowing these to be negated before the onset of significant detrimental effects with full-scale CMP usage.
One of TriboLab CMP’s key advantages lies in its small footprint. This compact benchtop CMP system has been designed and developed to offer mechanical testing and characterization, replicating full-scale polishing process conditions and typical consumables wear.
The instrument’s rotational motion is provided by pressurizing mechanisms on the wafer carrier.
Integrated sensors monitor and measure the vertical force (Fz), acoustic emissions and coefficient of friction (COF) throughout the experiments. These sensors can be employed as part of an end-point detection system, allowing the system to work with a range of specific test conditions.
When conducting polishing experiments on the TriboLab CMP, it is possible to cut round or square coupons from full-size wafers to fit inside the benchtop wafer holders. This feature affords users a significant reduction in wastage and costs, helping to ensure that R&D is as cost-effective and efficient as possible.
Pad conditioning impacts pad-wafer interactions, affecting the removal rate’s reproducibility.
Removal rate drift and ‘glazed’ pads can also have a negative impact on reproducibility, meaning that it is essential to condition the pad’s surface in-situ (during polishing) or ex-situ (in between polishing runs).
Conditioning the pad helps regenerate its surface while producing new pad asperities and removing any glazed areas.
Pad conditioners are tools specifically designed and tailored for each application, ensuring that the required roughness and porosity are consistently maintained throughout a pad’s lifetime.
Slurry transport and distribution will therefore be reliably maintained on the pad, with removal rate, polishing quality and planarity remaining steady, controlled and sustained throughout the pad’s lifetime.
Properly maintaining pads can help lower the overall cost of CMP equipment ownership. As the TriboLab CMP accommodates identical pad conditions to full-sized models, users are able to monitor these issues more efficiently.
The TriboLab CMP can be used to condition pads both in-situ and ex-situ, as well as for monitoring and measuring changes in COF, height, normal load and temperature over time. The faster that the COF stabilizes during conditioning, the more effective the conditioner is, and the longer the pad’s lifetime will be.
Figure 2 provides a practical example of CMP experiments conducted using a TriboLab CMP (taken from Yan Pan et al. 2010 J. Electrochem. Soc. 157 H1082).


Figure 2. The effect of sodium dodecyl sulfate (SDS) concentration on static dissolution rate and removal rate; polishing copper (top). COF variation with time for different SDS concentrations; polishing copper (bottom). Image Credit: Bruker Nano Surfaces
These experiments looked into the impact of slurry on copper polishing and explored and developed a physical model for the impact of sodium dodecyl sulfate (SDS) on polishing.
The study saw SDS surfactants added to the slurry at various concentrations. It also included hydrogen peroxide, glycine and silica particles.
The slurry needs to meet two requirements if it is to be suitable for copper CMP: any mechanically abraded copper oxide particles must dissolve in the slurry and be removed from the polishing interface.
In contrast, the surface oxidation and polishing rate encountering the pad should be higher than the removal rate of underlying copper.
The graph below shows that it was possible to achieve a high material removal rate with no surfactant, but many scratches and pits were left on the polished surfaces. These findings correspond to the highest COF, likely as a result of mechanical abrasion.
It was also noted that an increase in surfactant concentration led to a series of behaviors; for example, lower removal rates, followed by a slight increase in removal rate.
COF continued to decrease as more SDS was added, demonstrating a correlation between changes in the surface’s chemical properties. This resulted in surface variation and impacted the surface’s zeta potential, wettability, and ionic strength.
Increasing the SDS concentration to a total of 0.75 mM/l was also found to limit the number of scratches and corrosion throughout polishing – this ultimately resulted in a more effective CMP process.
This characterization test – and similar tests – are key to minimizing costs.
CMP Process Optimization
The high cost of ownership associated with CMP systems means the product must exhibit optimal function at all times. The TriboLab CMP can support CMP process optimization via user-friendly test programming and monitoring both in-situ and ex-situ.
Available software has made writing recipes straightforward, with each recipe able to include one or more sequences – each comprised of one or more steps.
These sequences can be run individually or in series, with all data channels saved into data files; for example, normal force, acoustic emission signals, frictional force (on the polishing head and conditioning discs), pad temperature and height.
Every parameter can be independently altered inside of each step (Figure 3), including load control on the conditioner or the wafer, as well as carriage position control.
Water and slurry feeds are programmable and can be automated, while pumps can be either switched on or off or set to operate at a specific flow rate. Finally, velocity, the direction of motion and lateral cycles can all be changed.
Monitoring the CMP progress in Bruker’s TriboLab CMP involves both in-situ monitoring and end point detection.
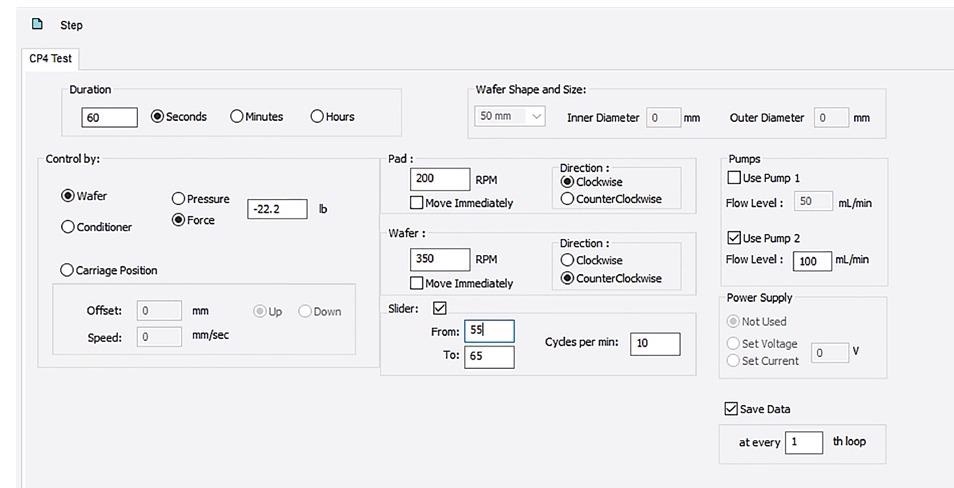
Figure 3. Demonstration of TriboLab CMP Software. Image Credit: Bruker Nano Surfaces
In-Situ Monitoring and End Point Detection
The industry currently utilizes an array of end point detection approaches, including electrical, thermal, acoustic, vibrational, frictional and optical methods.
Bruker’s TriboLab CMP has been designed to accommodate this trend, with a wide variety of end-point detections available to evaluate a number of polishing process endpoints.
Acoustic Emission (AE) has been integrated into the wafer chuck in order to facilitate the detection of a spectrum of COF frequencies generated during polishing. AE can also be employed in the detection of micro-scratches, layer contamination, elastic-plastic and sublayer deformation.
Pad temperature is also measured as part of endpoint detection testing. It is possible to analyze changes in the COF over time as part of endpoint detection, thanks to the TriboLab CMP’s ability to monitor pad wear by monitoring height.
Figure 4 displays data from a demonstration of benchtop CMP. This data demonstrates how parallel AE and COF measurements complement one another when looking to detect polishing endpoints.
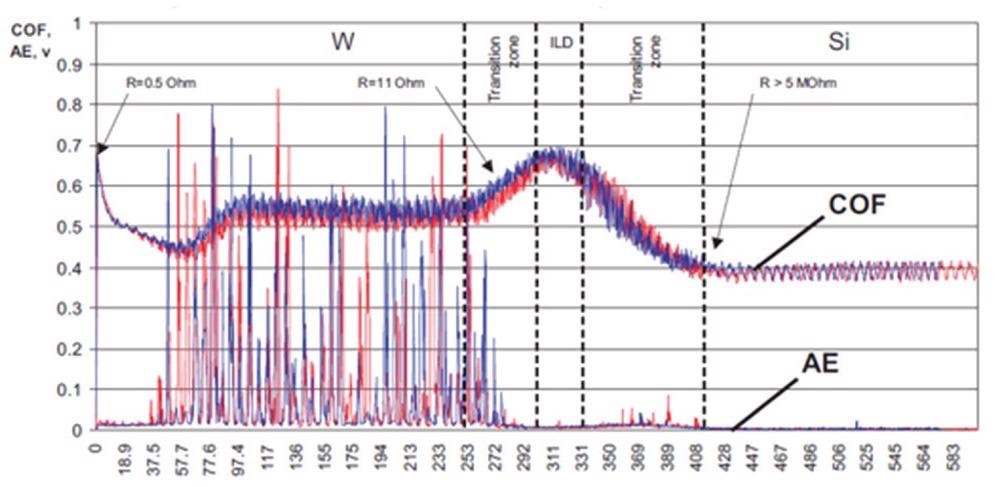
Figure 4. This graph demonstrates both the COF and AE as a product of time spent polishing. Image Credit: Bruker Nano Surfaces
Conclusion
The TriboLab CMP is able to address a diverse array of new and historical challenges in CMP use cases. The central problem addressed with Bruker’s TriboLab CMP is the significant amount of resources wasted through the use of inefficient CMP development processes.
The TriboLab CMP empowers CMP systems via efficient and cost-effective testing, quality control and process optimization.
These tests are applicable to both large-scale equipment and consumables and can be accomplished through a broad range of tribological measurements and user-friendly software, all housed in a compact footprint.
As demands for ever smaller devices with ever-increasing performance requirements continue, it is expected to become even more vital that CMP processes are efficient and effective.
Bruker’s TriboLab CMP ensures this effectiveness and efficiency in a single benchtop tool and is ideal for end-users and suppliers, in series or parallel.
Acknowledgments
Produced from materials originally authored by Kora Farokhzadeh, Ph.D. from Bruker Nano Surfaces and Metrology.
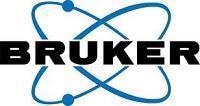
This information has been sourced, reviewed and adapted from materials provided by Bruker Nano Surfaces.
For more information on this source, please visit Bruker Nano Surfaces.